With various names, like big bag unloaders, FIBC dischargers/unloaders, and super sack unloaders/dischargers, big bag discharge systems are one of the most sought-after products of POLİMAK. Our product ensures a clean working environment, eliminates dust emission and enables a simple, secure handling of bigbags.
The type of bulk material to be discharged can vary from freely flowing granules to poorly flowing sticky fine powders. Also, the size of big bag and the type of downstream equipment need to be considered while designing the system. POLİMAK Big Bag Discharge Systems are designed by taking all these criteria into account.
Big Bag Discharge Mechanisms
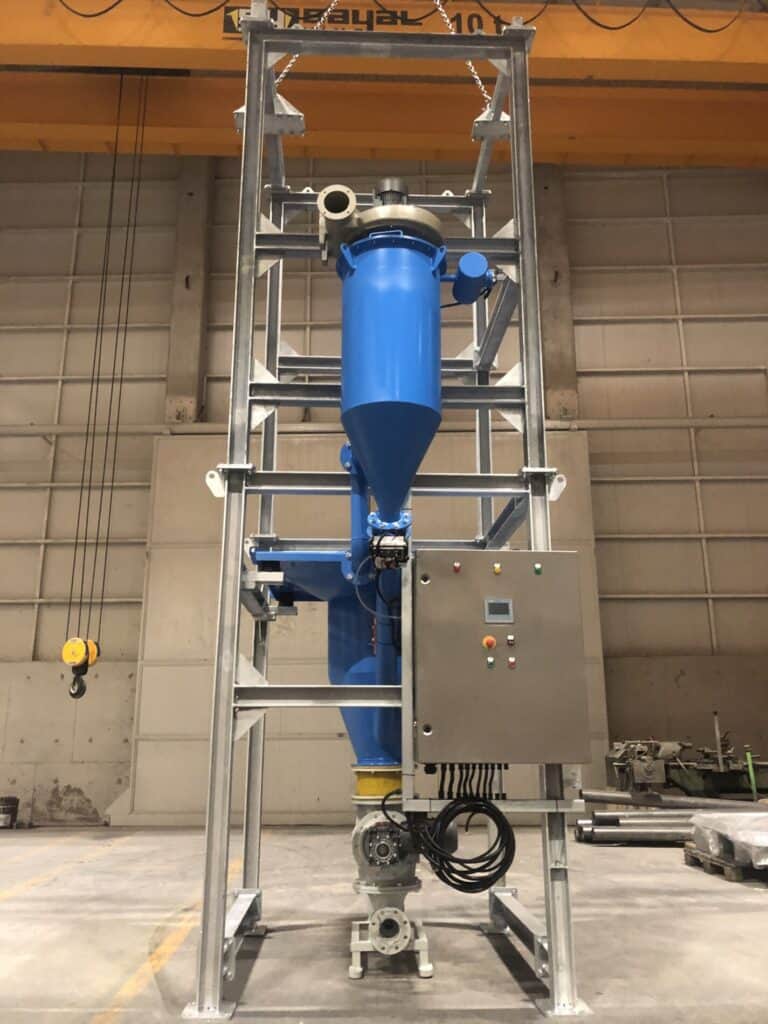
Discharging big bags into storage silos, production lines or other systems can be done in different ways, with pneumatic and mechanical conveying being the most commonly used methods.
Pneumatic conveying systems are ideal for long-distance transport of bulk materials. There are two main types of pneumatic conveying systems based on velocity and pressure: i) dilute (lean) phase, ii) dense phase. Dilute phase conveying systems are mainly suitable for non-abrasive, hard-to-break materials with low bulk density. It conveys materials at low pressure and high velocity. Dense phase, on the other hand, is ideal for abrasive, fragile and friable materials. The transfer takes place at low velocity and high pressure differential. Blowers, fans and compressors are used to move the material through the pipeline.
In mechanical conveying systems, distance and height are crucial factors in selecting the appropriate method. For short distances or movement along a single axis, screw feeders are the preferred solution. However, for taller structures like high silos, different conveyors, such as bucket elevators, are required.
For unloading heavy materials from big bags, the big bag discharge system can be installed at the top of the silo, with a control valve to ensure smooth discharge. Compared to other systems, this system, which operates with gravity, provides a simple solution.
Various methods of handling big bags
Based on the customer’s needs, our models come with different components:
- Based on the system’s height and the customer’s requirements, the big bag discharge system can be designed without an upper frame. The big bag is then brought by forklift or overhead crane and installed into the system.
- If there is an upper frame, big bang hanging units can be installed. A lifting cross can be added to the system and then by attaching it to big bag handles, the big bag can be put on upper frame and be discharged efficiently.
- A monorail or electrical hoist moving horizontally can be installed on the upper frame, enabling the lifting of big bags from ground to the discharge system.
Accessories
- Big bag discharge, dosing, weighing and batching systems: Bulk material in powder or granular form can be moved from big bag discharge units to weighing and batching systems. During the process of dosing and batching the hopper should remain full. Our big bag discharge systems are designed to monitor the level of product in the hopper, ensuring a constant level is maintained. Either pneumatic or mechanical conveying can be chosen, based on the distance and requested dosing rate.
- Dust collector: Dust formation is unavoidable during the handling of FIBC. To minimize dust formation, installing a dust collector with a built-in fan is recommended. In this process the collected dust is redirected to the big bag discharge unit, ensuring no product waste. On the other hand, the reverse pulse jet system purifies the air within the system.
- Big Bag Massaging System: When the material to be handled tends to get compacted easily, we recommend using POLİMAK’s Pneumatic Big Bag Massaging System. This system facilitates the flow of especially compacted bulk material by applying force from the outside.
- Lump breaker: Due to moisture or high cohesion, clumps may form, hindering the material’s flowability. To ensure the smooth passage of bulk material from the big bag discharge system to the downstream, these lump formations must be broken. Our lump breakers installed at the outlet of the discharge system effectively resolve this problem.
- Screening system: Placed at the outlet of the system, it prevents the passage of material with unwanted particle sizes. POLİMAK screening systems come with different sizes, depending on the customer’s need. Among the various options available, vibrating screens are the most common type used in bulk material handling.
- Big bag cutting knives: In the case of high volumes these blades can be installed in the middle of the platform. In applications that require high throughput, using cutting knives is recommended to ensure a faster handling of the big bags.
- POLİMAK’s extensive inventory of valves, including rotary valves, slidegate valves, iris valves, and butterfly valves, enable controlled and smooth product discharge.
- Magnetic separator: Installed at the outlet of the system, it collects unwanted metallic particles and substantially reduces the risk of contamination from them.
- ATEX-certified equipments prevent overheating, unwanted leakage and combustion.
The Advantage of Working with POLİMAK’s Big Bag Discharge Systems
Considering the variety of these options, POLİMAK’s Big Bag Discharge Systems are ready for use in a wide variety of applications, particularly in food, chemicals, mining, plastics and cement industries. POLİMAK’s over 40 years of expertise and know-how provide high quality, problem-free, safe and cost-effective solutions for big bag discharge mechanisms. By incorporating the various accessories mentioned, we provide tailored, industry-specific solutions to meet the unique demands of each sector.