Polimak designs storage systems with varying sizes, capacities, and configurations. Depending on the customer’s needs, we manufacture storage silos ranging from low to high capacities to ensure maximum efficiency and minimum costs.
The following features are taken into consideration when determining the design of storage silos:
- Properties of bulk material: bulk density, particle size, angle of repose, flowability, moisture, corrosivity, minimum ignition temperature,
- Silo geometry: width, height, cone angle, outlet size,
- Volume of storage,
- Silo filling capacity,
- Silo discharge capacity,
- Surface roughness,
- Connected equipment,
- Wind loads,
- Seismic loads,
- Static load and dynamic load,
- Access and inspection points,
- Environmental considerations,
- Operational flexibility.
Bridging (also known as arching) and ratholing are common problems in silo design and operation, especially when the flow of stored material is not sufficiently considered in the silo design.
Bridging/Arching: It is characterized by an arch-shaped formation at the outlet of the hopper, which obstructs the flow of material. In the case of coarse-grained bulk solids, bridging occurs due to the interlocking of particles, whereas for fine-grained materials, arching happens due to adhesion between the particles.
Ratholing: It refers to the funnel-shaped formation inside the container, where the bulk material flows only through the channel directly above the outlet. The main cause of ratholing is the inherent strength of the material itself.
A common way to solve this problem is by installing a bin activator in the storage system (which will be discussed in the Silo Equipment Section).
Filling of storage silos should be carried out carefully to prevent potential risks. Some of the most common risks during this process are as follows:
- Silo overpressure
- Silo underpressure
- Silo overfilling
- Explosion risk from combustable dusts
- Adverse weather conditions
To handle bulk material while avoiding the hazards listed above, it is essential to use a silo control system (which will be discussed below).
Polimak delivers turnkey bulk storage silos and their production includes the following steps:
– Feasibility analysis
– Concept design
– Initial design in 2D / 3D
– FEA (Finite element analysis) of the silo for structural safety
– Cabling, instrumentation, and piping design
– Detailed design in 2D / 3D
– Fabrication
– Installation
– Commissioning
Through this detailed design process, from feasibility to commissioning, the aim is to avoid the problems discussed above.
Silo Equipment
Polimak offers a wide range of equipment for functions such as constant monitoring, ensuring silo safety, collecting dust, and ensuring smooth flow.
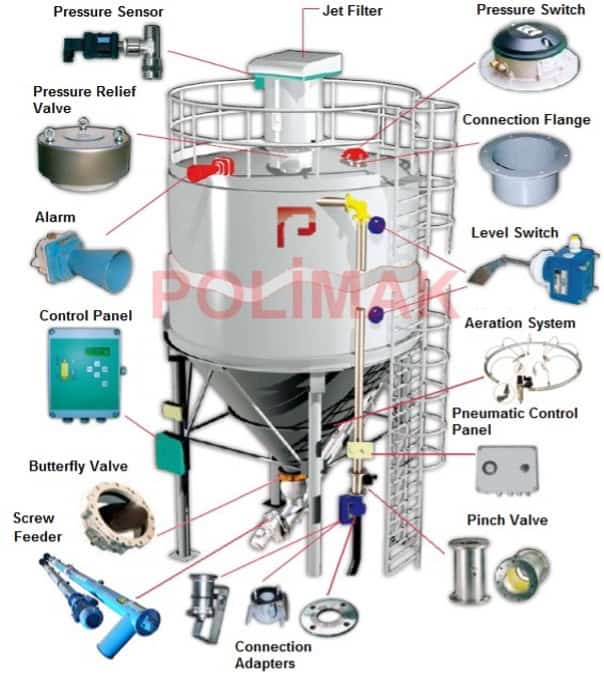
i) Silo Jet Filter: It is used to collect dust emissions, ensuring reliable silo filling. To maintain proper filling, air within the storage unit must be discharged, and any dust formations should be filtered. Silo jet filters perform these two essential functions and are commonly used in the handling of materials such as cement, ash, plastics, and minerals within pneumatic conveying systems.
ii) Silo Level Switch/Silo Level Sensor: It serves to monitor and control the product level within the silo. These sensors are equipped with rotating paddles. When the product level reaches the sensor, the paddles stop rotating and send a signal to the operator, ensuring accurate monitoring
iii) Pressure Relief Valve: An essential piece of equipment for ensuring silo safety. During the loading process, pressure buildup within the silo remains a potential risk. The silo pressure should not exceed critical levels. In such cases, the relief valve vents the silo, reducing the pressure to a safe level.
iv) Silo Pressure Sensor: They continuously monitor the air pressure level inside the silo and transmit this information to the automation system.
v) Aeration Pads/Air Jets: They help enhance the flow of bulk material within the silo. Installed near the hopper outlet, they fluidize the material using pressurized air.
vi) Silo Discharge Butterfly Valve: Consisting of a rotating disc within a circular hollow body, these valves are used to control the discharge of bulk materials.
vii) Silo Discharge Screw Conveyor: It consists of a rotating screw inside a tube or trough, which moves the material toward the discharge point and transports the material from the silo.
vii) Rotary Valve: Installed below the silo, rotary valves are used to transfer bulk material to screw feeders, conveyors, and other equipment.
viii) Pinch Valve: The pressurized air within the valve closes off the flow of bulk material. When the valve is open, there is no obstruction to the flow.
ix) Bin Activator: Also known as vibrating bin discharger, it is especially needed for hard-to-flow bulk materials. By generating vibration movements, they fluidize the material, facilitating the discharge process.
Silo Control System
Generally, silo control systems are employed during the loading of a silo with a pneumatic conveying system. This mechanism allows the operator to control the product level and pressure level in the silo, as well as the jet filter, inlet, and discharge valves.
It is essential to use PLC-based monitoring systems to ensure the safety of the production plant, silo, and workers. This system provides comprehensive protection by monitoring storage silos, as well as the connected upstream and downstream units. Thanks to the sensors mentioned above, common silo problems such as overfilling, overpressurization, and underpressurization are prevented.
Polimak provides a diverse set of silo filling control systems:

i) Silo Filling Control System For Bulk Truck Filled Silos:
Silos filled by bulk trucks or road tankers need to be monitored by a PLC-based system to ensure safe, reliable, and efficient loading. The components connected to the monitoring system include the silo jet filter, pinch valve, and level and pressure sensors. For safe loading, the control system monitors the power supplied to the bulk truck, product level, and silo pressure.

ii) Silo Filling Control System For Silos Filled By Pneumatic Conveying Systems:
To reduce unnecessary costs and complexity, the industrial plant uses its own control system, such as SCADA or DCS, for the pneumatic filling of silos. In this configuration, it is preferable to install a local control panel to monitor silo functions. By connecting to SCADA and DCS units, several signals (start/stop, product level, alarm, pressure) can be transmitted between the units, enabling a simple, safe, and reliable loading process.

iii) Silo Filling Control System For Silos Filled By Mechanical Conveyors:
Silo filling by mechanical conveyors, such as bucket elevators and screw conveyors, requires a simpler configuration because there is no pressure buildup in the silo. In this configuration as well, a local control panel connected to SCADA and DCS units sends start, stop, level, and alarm signals, providing a safe and efficient loading process.
With over 40 years of technical expertise and know-how, POLİMAK delivers high-quality, reliable, safe, and cost-effective solutions for storage silos. Drawing on our broad spectrum of storage equipment outlined above, we offer specialized solutions for dry bulk material storage in different industries. Our ultimate goal is to continue producing tailor-made solutions for dry bulk material handling processes, ensuring optimal efficiency, reliability, and adherence to sustainability standards in storage.
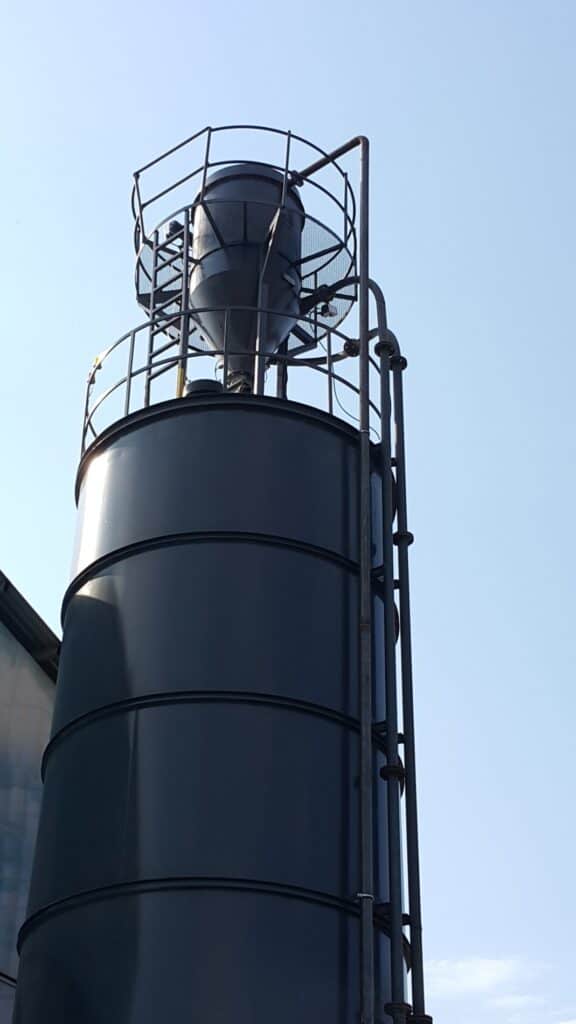