The Austrian machinery supplier will be showing its solutions for the sustainable use of plastic packaging at interpack 2023.
“Closed loops for plastic packaging are not only a prerequisite for counteracting environmental pollution and constantly growing mountains of rubbish, but also to conserve resources,” emphasized Angelika Huemer, Managing Partner of Starlinger & Co Ges.m.b.H. “Wherever such loops can be implemented in a sensible way, it should be done as quickly as possible. At Starlinger, we have been working on solutions to close the loop for woven plastic packaging for a number of years. Our concepts of using recycled PET or polypropylene in the manufacture of big bags and small woven bags are well received by the pioneers in the industry, and we will continue to work on them.”
Big bags become big bags again
A pioneering project in this regard will soon be underway: Using Starlinger technology, big bag manufacturer LC Packaging, PET recycler PRT – a member of ALPLA Group, and Croatian recycler Velebit will jointly implement a closed loop for big bags made of polypropylene (PP) in autumn 2023. The big bags, which PRT uses for both the transport and storage of the input materials and the rPET granules produced from them, are recycled into rPP pellets by Velebit on a Starlinger recycling plant. LC Packaging mixes the recycled pellets with virgin material and produces tape fabric which is converted to rPP big bags. The finished big bags are then supplied again to PRT.
Closed packaging cycles in the industrial sector
In order to make polypropylene big bags, the most commonly used material for this type of packaging, more sustainable, Starlinger provides a pioneering solution for the packaging industry by processing recycled PP – also from post-consumer waste – on its production lines. “Starlinger customers are already producing big bags with recycled polypropylene. If the quality of the recycled material is good, high proportions of recycled content in this type of heavy-duty packaging, which has to fulfil special requirements, are no problem,” said Huemer.
With the technology for manufacturing big bags from PET as an alternative to polypropylene, Starlinger is able to offer manufacturers in this packaging segment a solution for a completely closed packaging cycle. Properly recycled, rPET achieves properties like virgin resin and can be used up to 100% for the production of high-quality packaging – see bottle-to-bottle recycling. With Starlinger systems, it is now also possible to produce big bags from 100% recycled PET.
From plastic packaging to high-quality recyclate
Starlinger not only offers production equipment for woven plastic packaging, but also systems for the recycling and refining of plastics, which are also used in the closed-loop solutions mentioned above. Starlinger recycling technology and Starlinger viscotec play a leading role in the industry with technologies for the production of food-grade PET and HDPE recyclates as well as thermoforming films made of rPET.
With the new recoSTAR PET art PET recycling system, Starlinger recycling technology offers an energy-saving and low-maintenance machine concept that produces food-grade rPET of the highest quality and at the same time reduces production costs by around 21%. In the field of post-consumer recycling, Starlinger’s odor reduction technology helps ensure that packaging of consumer goods such as detergent and shampoo bottles can be recycled and reused in the same application, thus avoiding “downcycling”.
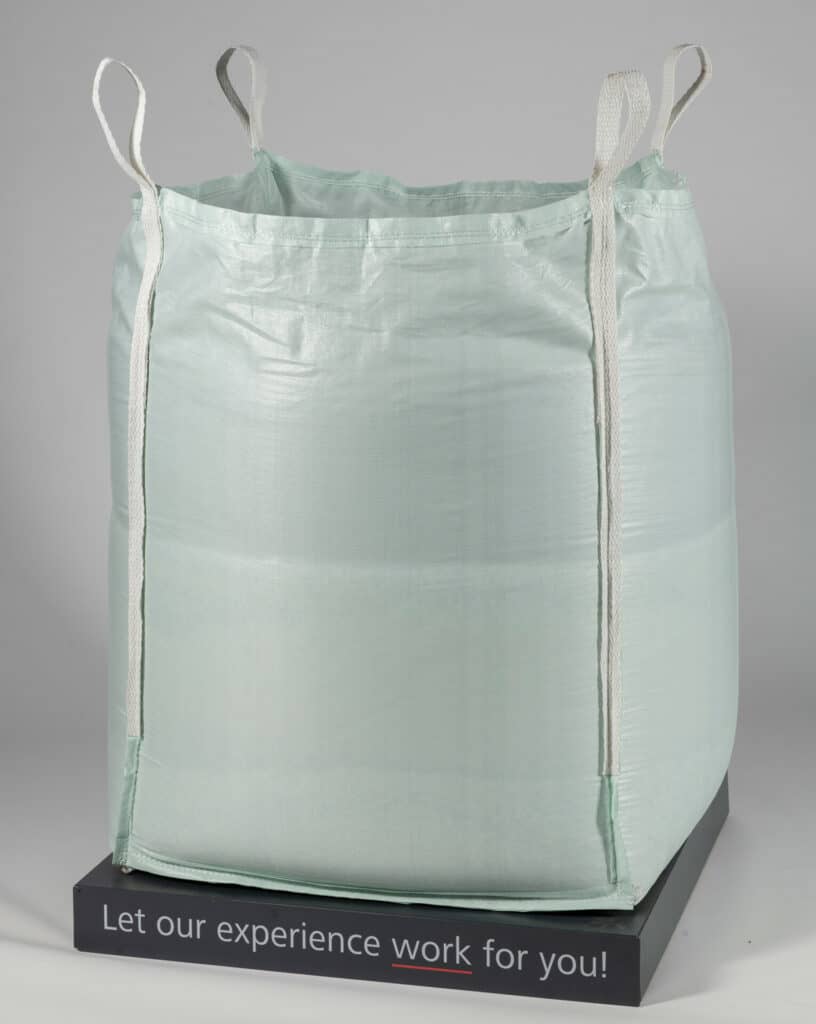
With the viscoZERO melt-phase decontamination reactor, Starlinger viscotec has developed a versatile system that produces recycled PS, PP, PE or HDPE suitable for food packaging applications and increases the intrinsic viscosity of PET. Unwanted odors are also effectively removed during the decontamination process. The line processes production waste from fiber and textiles production, skeleton waste, strappings, or post-consumer plastic flakes.
New sack conversion line and other highlights at the trade fair
The new Starlinger sack conversion line multiKON KXservo can be seen in operation at the booth and will produce IC*STAR sacks developed by Starlinger. In the IC*STAR production process, the cut sacks run through a welding device in which a coated sealing strip is welded onto the bottom of the sack in a continuous process using hot air in order to close it. IC*STAR sacks are characterized by material saving production, excellent protection of the product, and high strength combined with low packaging weight.
The production software provider GRAFiT will also be at the Starlinger stand during interpack. The Starlinger subsidiary offers software systems for the control and monitoring of production lines as well as product tracing which are installed also on Starlinger production lines, among others. Based on reliable information from the production line, the software provides a clear overview of all processes, enabling an objective analysis of the production process.
The Austrian platform “Packaging with a Future” will also be present at the Starlinger booth and provide information on circularity in the packaging industry.