Their largest plant in Piscataway, New Jersey operates 23 blown film extrusion lines and produces some 115 million pounds (52 million kg) yearly of 15 different polyethylene, or PE resins. These are compounded to meet customer requirements for density, gauge, surface characteristics, color, food contact, shrinkage, printing, UV resistance, anti-fog, flame retardancy and other properties.
Under the leadership of corporate project manager Ed Komoroski, AAP increased the system’s capacity and reliability over the past decade, doubling the number of silos and adding multiple conveying lines. Before he joined the company, material was conveyed pneumatically from rail cars into the plant through flexible hose, and then through pneumatic piping and sweep elbows to holding bins and extruders.
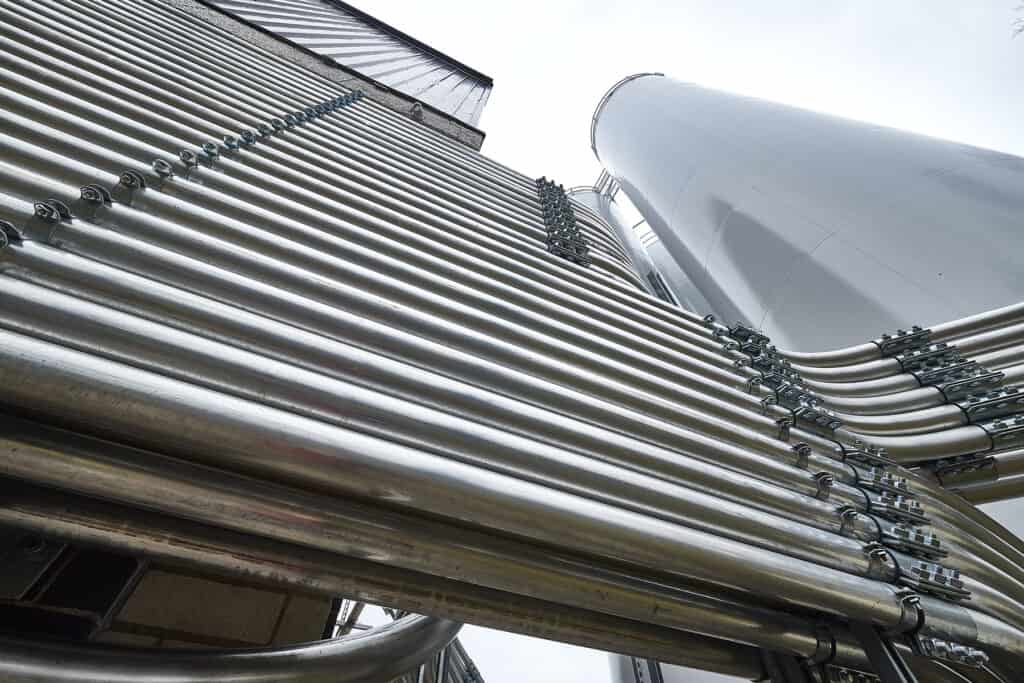
The high volume conveying, together with PE’s relatively low melt temperature of 248 to 266°F (120 to 130°C), created a problem with streamers (also known as angel hair and snake skins).
The heat generated by the PE impacting sweep elbows melted the product inside the conveying lines, forming streamers that jammed downstream equipment. This led to production tie-ups and demurrage charges while rail cars waited to be unloaded.
Upping transfer capacity, efficiency
At the heart of AAP’s vastly revised process is a series of plant-wide pneumatic vacuum conveying systems with over 108 bends and 128 separate lines. The lines transfer PE pellets from rail cars to eight exterior silos, then to interior holding bins, and ultimately to mixers on an upper level and extrusion lines below.
To avert PE degradation and production delays, Komoroski turned to HammerTek and the company’s 90-degree Smart Elbow® deflection elbows.
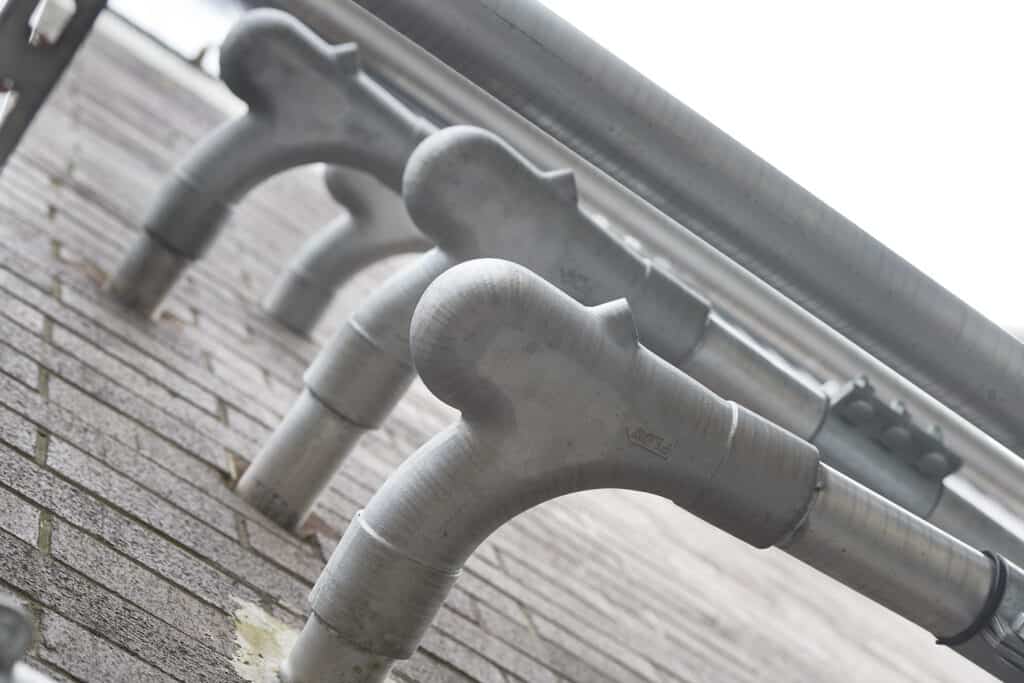
The elbows feature a bulb-like protrusion that extends beyond the 90 degree pathway, creating a ball of material suspended in air that rotates in the same direction as the airstream that powers it. This causes incoming pellets to be deflected around the bend without impacting and heating the elbow wall, thereby preventing elbow wear, material degradation, melting and plugging.
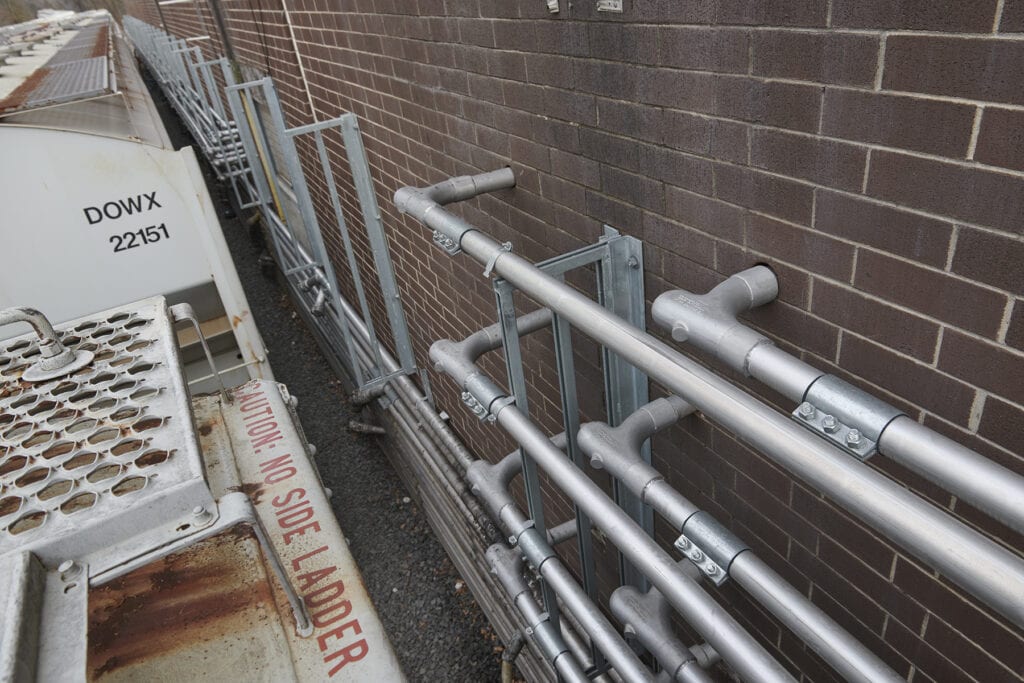
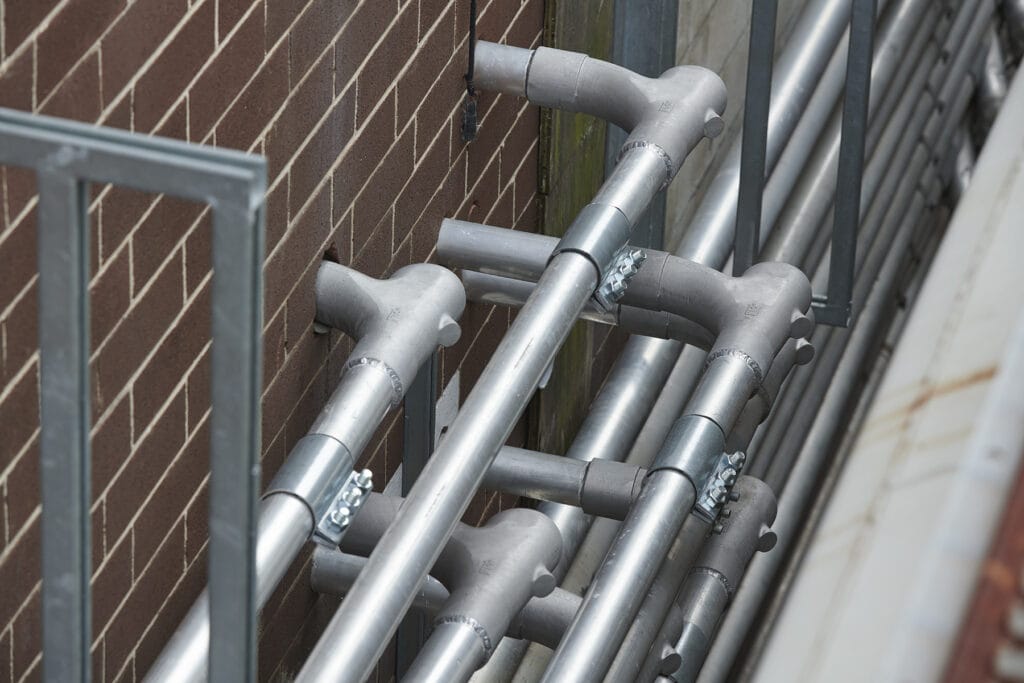
The elbows’ short-radius design allowed installation between the rail car siding and the building, and from silos through an exterior wall into the plant at 90 degrees.
AAP has installed over 100 of the deflection elbows. Komoroski explains that AAP no longer experiences the maintenance issues caused by streamers, improving production, and notes that Smart Elbow units will be specified on all new vacuum lines added to meet increased demand.
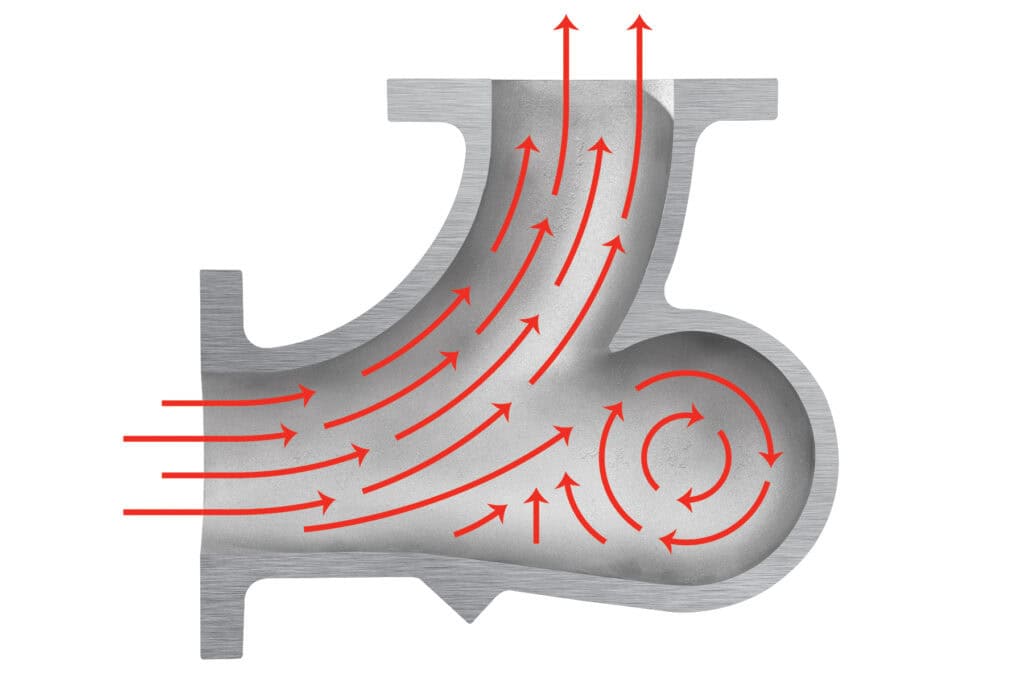
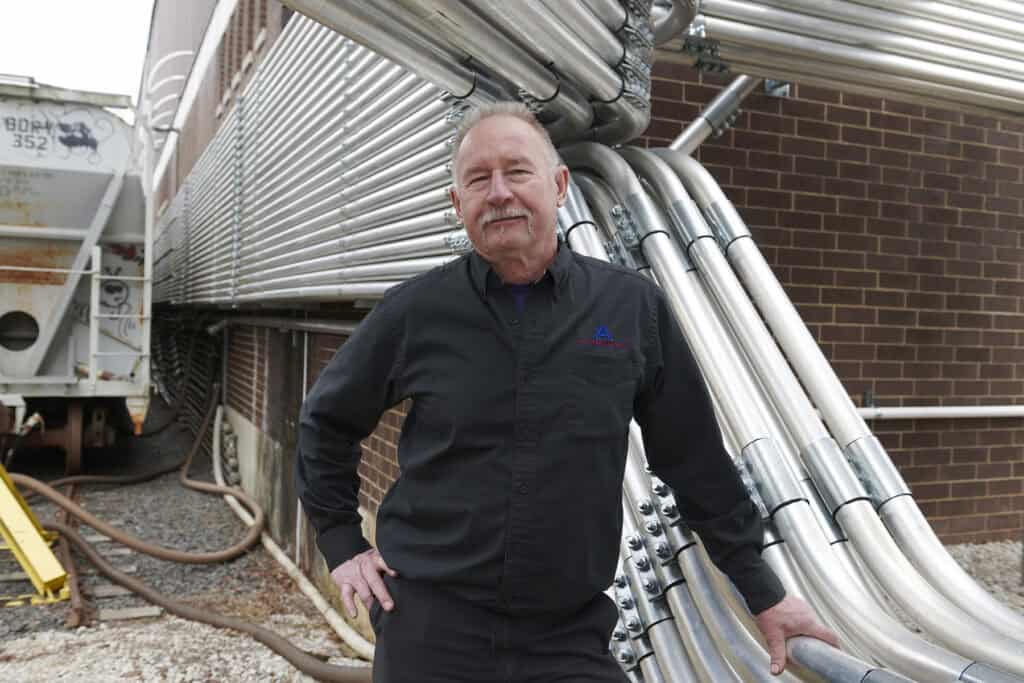