As these materials are processed from raw to granular form, and then distributed to industrial processes, the materials must be repeatedly moved and stored.
Pneumatic conveying is often the preferred best-practice method for moving these materials. Pneumatic conveying systems ensure that dust is contained, allow flexible transports of the minerals to multiple locations and ensure that the transport system is largely comprised of simple pipes that require little cost or maintenance. A well designed pneumatic conveying system can provide years of service with low cost of ownership. However, with abrasive minerals, several design considerations must be made to protect against erosion at key locations in the process flow. If such considerations are not made, the equipment life-cycle can be shortened from years to days.
Cyclonaire has been conveying abrasive materials from day one of our 45+-year history. Cyclonaire was founded on a patented railcar unloader, specifically designed for handling abrasive minerals. Most mineral products are eventually shipped from mine or mill to end-use customers in large quantities, often by rail, which quickly exposed Cyclonaire to the full range of abrasive materials as our client list expanded. More than four decades of working in this environment has led to the development and incorporation of many best-practice techniques.
Many of these techniques are very simple and low cost to implement. Others are more involved and expensive. The goal of this article is to introduce the types of solutions available and the concepts behind them to ensure that the most appropriate selection is incorporated; more extreme situations are considered as well.
How Abrasive Is It?
One of the challenges when handling abrasive minerals is to identify “how abrasive is it”? This will often drive decisions about the degree of design fortification. There are four physical characteristics that contribute to the abrasiveness of the material:
- 1.Particle Hardness
- 2.Particle Shape
- 3.Bulk-Material Density
- 4.Particle Size
Factors can be applied to each of these parameters and multiplied to determine an overall abrasive index of one material as compared to another. This can help to objectively describe why Talc (Moh’s hardness of 1, low density, small particle shape) is much less abrasive than Silica Sand (Moh’s hardness of 6-7, higher density, larger and sharper particle shape). Because such a range of abrasiveness can be encountered, the effect on the material handling equipment will vary significantly as well. Accordingly, if careful consideration is not taken when selecting/designing the equipment, what might be a highly successful installation for one material might be considered a catastrophic-failure for another.
Another very important concept to understand is that abrasive wear has been shown to be proportional to the conveying velocity raised to the X power, where X varies between three and five. To put that in perspective, increasing the velocity 10 percent can increase wear by up to 70 percent. Understating this phenomenon is the key to most of the effective design solutions for abrasive minerals – identifying localized velocities and reducing them wherever possible.
Main Transport Velocity
First, it is important to consider the main transport velocity. Pneumatic conveying systems can be designed across a wide range of flow types. At the far extremes are:
- Dense Phase uses lower air velocities, and at the extreme end of the spectrum, relies entirely on differential pressure rather than velocity to extrude slugs of minerals through the pipe. Velocities typically range from 100-4,000 ft/min for these system types. (think: toothpaste out of tube)
- Dilute Phase uses high air velocities to carry each individual particle suspended in the airstream. Velocities typically range from 4,000-9,000 ft/min for these system types. (think: sandblaster)
Summary
As this discussion has made apparent, the devil is in the details when designing for abrasive mineral transfer, and striking the balance between under-designing or over-designing can be the most difficult challenge when specifying a pneumatic conveying system for abrasive minerals.
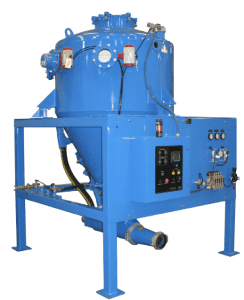
Under-designing, or simply failing to consider abrasion protection, can result in high abrasive wear resulting in material leaks, high repair costs, and frequent downtime.
Over-designing can inflate capital costs which might make such projects cost-prohibitive. This is why it is important to fully consider:
- How abrasive is my mineral?
- How can velocity be appropriately selected for the abrasive service?
- How can local velocity concentrations or high contact components be effectively fortified/protected?
- What will be the full life-cycle cost of operation of this system?
Working with a partner who understands these issues and helps you to select the right level of system fortification is important. At Cyclonaire, this consultative and collaborative approach is our standard business practice.