“All the materials our clients work with are abrasive and, over time, any type of elbow will degrade if it isn’t specifically designed to handle them,” says Marcus Bollman, project engineer. “For us, the two options are the HammerTek deflection elbow or our own wear-back elbow.”
Chemco’s own elbow is a standard rolled 90-degree pipe with rolled steel welded to the back. The HammerTek design has a bulb-like protrusion where a loose ball of material rotates in the same direction as the airstream that powers it, deflecting material around the bend without impacting or wearing the elbow wall, preventing blow-outs. Material comprising the ball gradually self-renews as it continuously filters out of the chamber as new material enters.
“Long-term wear resistance is critical,” Bollman says, “because once the elbows are installed, they can be difficult to access…plus the downtime and the cost of a new elbow add up.”
Chemco’s 120,000 sq ft (11,150 m2) facility custom designs and builds 30-40 bulk storage and feeding systems per year, with silos ranging from 8 to 38 ft (2.4 to 12 m) in diameter.
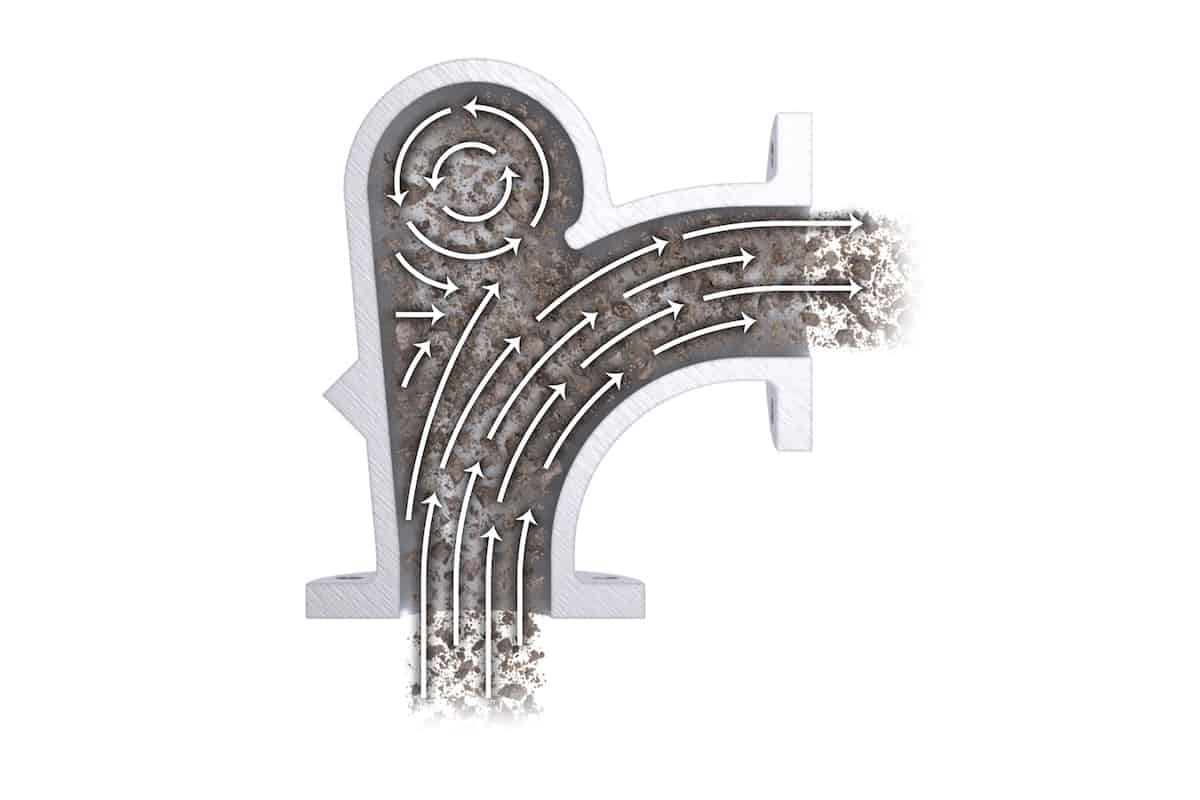
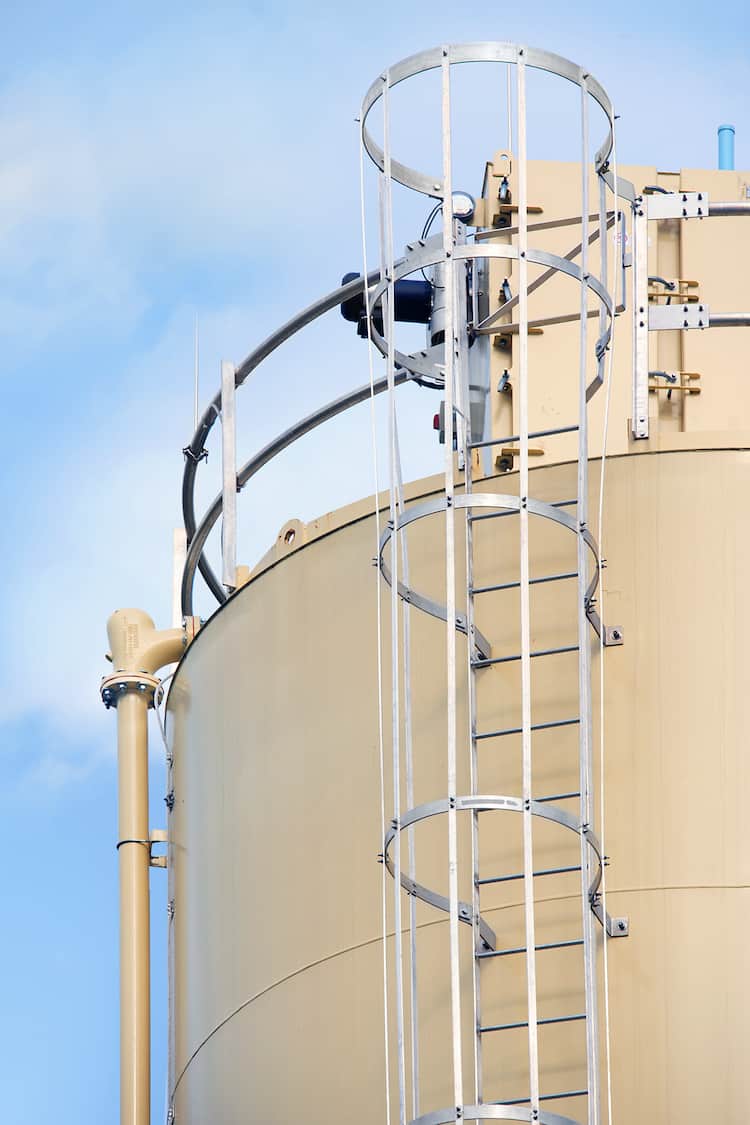