Commonly overlooked at the design stage, or the first item to be axed when budgets get tight, vacuum conveying is typically installed retrospectively, perhaps prompted by an operator injury or containment breach. It is often shoe-horned into tight spaces (both height and footprint), with signal lines and hoses following tortuous routes around existing equipment – and giving these versatile and much misaligned systems a bad reputation.
The truth about vacuum conveying is quite the opposite, and a well-designed system can enhance a process, increasing throughput and efficiency, eliminating the risk of operator injury and exposure, and ensuring product containment – while being kept tidy and compact.
The Problem
The typical integrated pharmaceutical granulation suite is perhaps the best example of these principles being optimally applied. These suites vary across the industry, dependant on factors such as batch size, the nature of the product, binder type etc., but will typically comprise a number of distinct processes turning raw material into granule, for onward processing – perhaps into tablet or capsule form.
The raw material is first loaded into a high-shear mixer / granulator. This may include active, excipients and a binder, all of which need to be introduced into the mixer bowl, which is generally raised off the suite floor on a podium, and accessed by steps. Once mixed and granulated, the wet granulate is passed through a mill to remove oversize lumps, and into a fluid bed dryer where it is dried in a bed of moisture-controlled air. The dried granule is then passed through a second mill to remove agglomerates formed in the drying process, and then into bins or IBCs for onward movement to tabletting etc.
The movement of the wet mass from high-shear mixer, through the wet mill, and into the dryer bowl is most commonly achieved under gravity (the reason for raising the mixer on a podium), but it is the initial loading and final unloading where vacuum transfer is relevant.
The process of loading the dry ingredients for a large production batch into a mixer / granulator by hand involves an operator manhandling drums of weighed product up podium steps, and tipping it into the opened lid. This not only exposes the operator to the product (often requiring gloves and mask to prevent contact, inhalation, exposure to eyes etc.), but can often lead to injuries on the steps, manual handling issues, minor batch losses, and airborne dust. It can also be a slow process, and is prone to errors in matching the recipe.
Once dried, the dryer bowl can be removed, breaking the containment seal, and the granule manually removed by scoop. It is tipped into the dry mill, then feeding into the bin below under gravity – all very labour intensive and time consuming. Due to the ergonomics of this process for the operator, the dispensing height of the dry mill dictates the use of a relatively small destination bin beneath it – and this then often needs to be transferred into a larger vessel / IBC for onward movement, introducing yet another step, and increasing batch losses and operator exposure during this additional transfer.
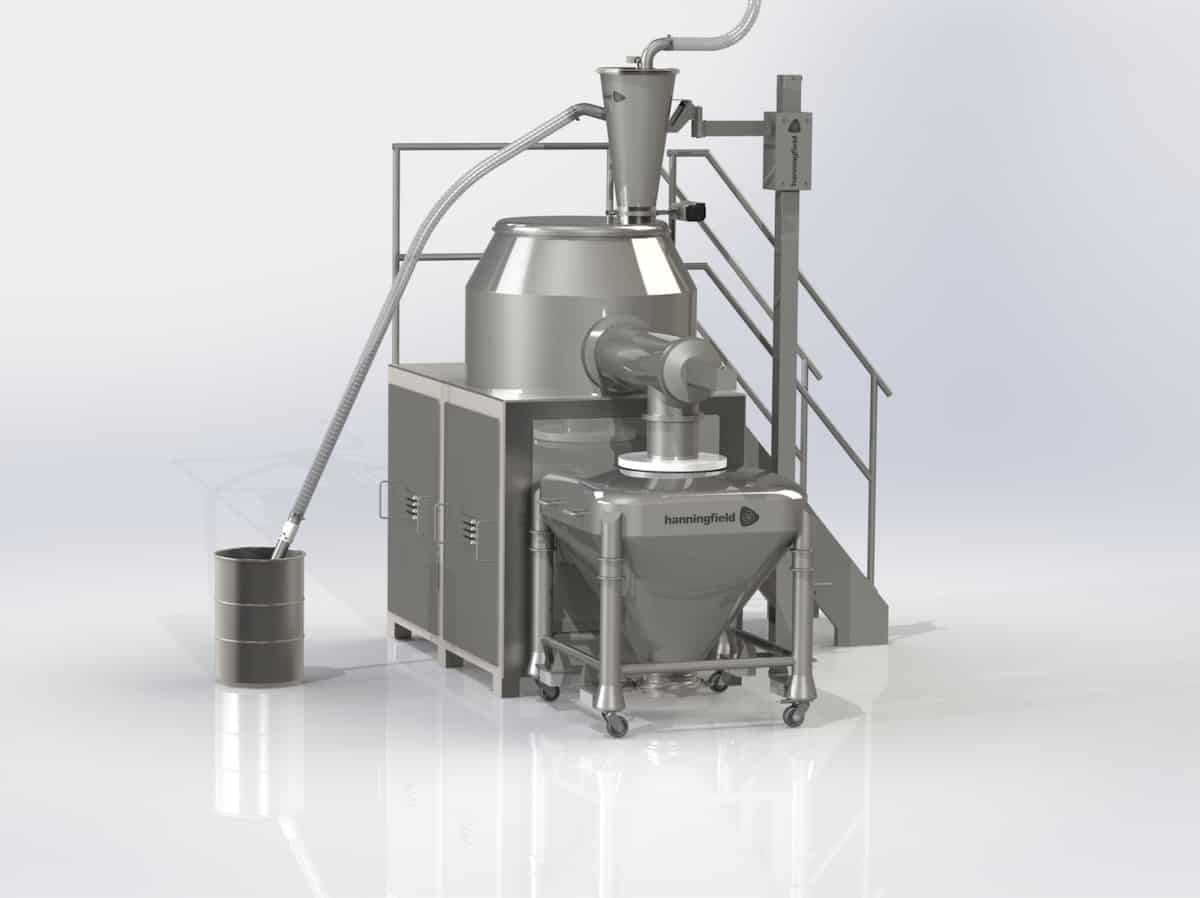
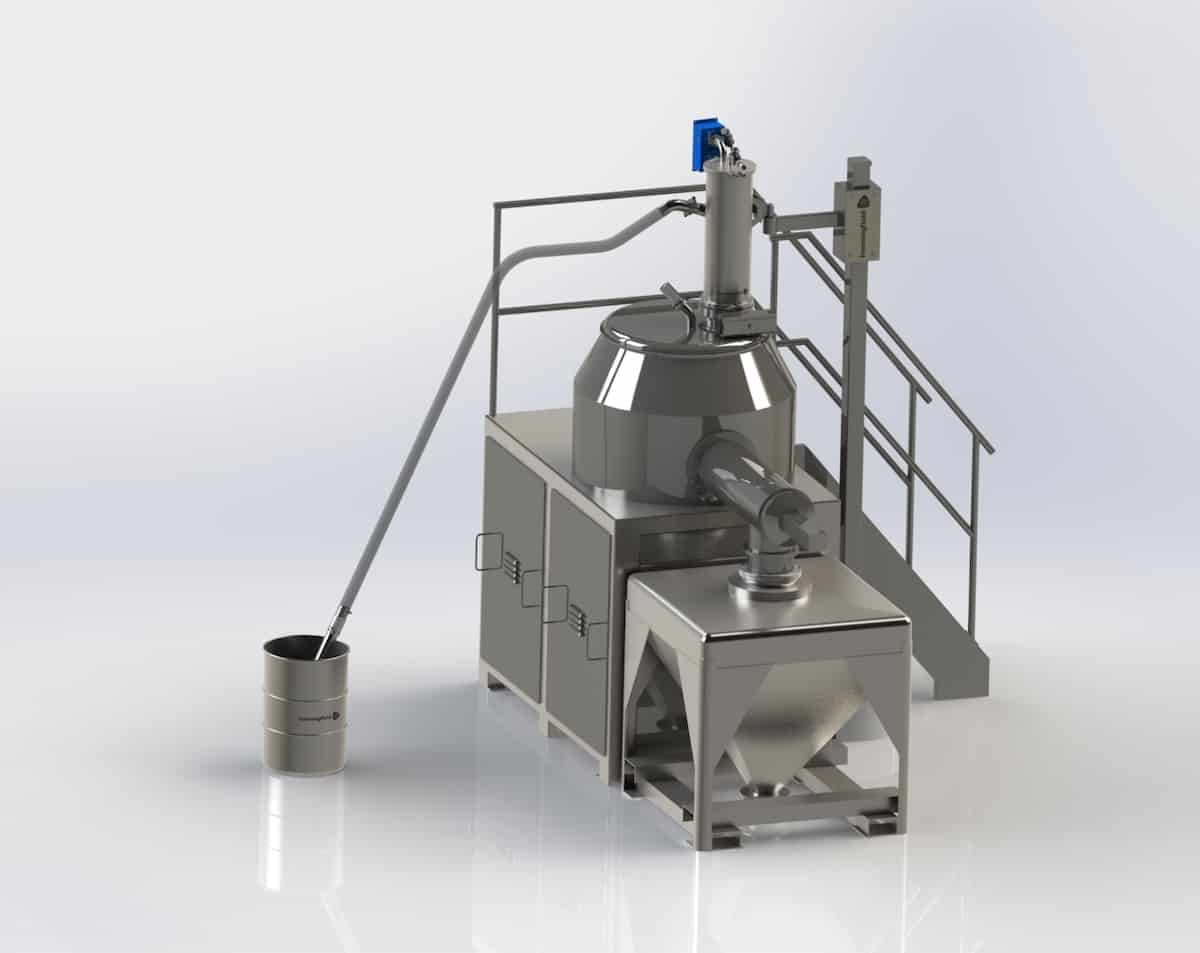
The Solution
The solution at both stages is simple – transfer the product under vacuum. The operator can tip the bag / drum of product directly into a sack-tip station at floor level, or can plunge a vacuum lance (akin to a domestic vacuum cleaner nozzle) into the bag or drum, eliminating the need to climb the podium steps. For more hazardous products, there are other means of unloading the supply containers without breaking the seal. The vacuum transfer system pulls the raw materials from this station or lance up to a hopper over the high-shear granulator, and drops it into the bowl in a contained manner. The sack-tip station may be supplied with a hood and/or curtain with dust extraction, to ensure there is no airborne dust in the room and negates the risk of operator exposure. Loading is fast and efficient from the point of unloading the supply drum / sack, and a large batch can be loaded into the granulator in a matter of minutes, for the wet granulation process to commence.
Once dried, instead of separating the bowl from the dryer body and exposing the product, a vacuum conveying system is connected to the discharge valve just above the plate. The bed is fluidised and the vacuum turned on. Dried product is raised as a fluid bed, and flows out of the discharge port, drawn by the vacuum. Again, the unloading of large batches can be achieved in minutes, far quicker than by manual unloading.
The vacuum system may also be sized to incorporate a dry mill (to remove agglomerates formed in the drying process) as part of the transfer. This vacuum swept milling is again faster than milling under gravity and is done so in a totally contained manner. The milled product is drawn into a transfer hopper and deposited into the destination vessel (drum, IBC etc.). The operator has had no involvement in this process other than making and breaking the transfer hose connections before and after, and operating the vacuum conveying system.
Conclusion
As with any piece of equipment, there will be exceptions, vacuum transfer will not lend itself to all applications, but in the majority of cases it will be of huge benefit to the process. If lateral movement is required between operations for dry material, then vacuum conveying should always be a serious consideration. Dry product (powder, granule, flake, chips, even tablets) can be transferred safely under vacuum, without the risk of injury, in a contained manner, eliminating airborne dust and operator exposure. Add to this the fact that the inclusion of a pneumatic conveying system can speed up product transfer considerably, increasing efficiency and reducing batch process times – and you would have to ask why would you not include such a beneficial piece of equipment?