Containment of manufacturing processes and material handling should be viewed not only based on personnel and plant protection from toxic dust migration, but also on the potential deflagration of drug substances and materials. Containment therefore should be thought of as a comprehensive approach for protection from all these hazards.
From both an EH&S and process equipment manufacturers’ perspective, the starting point in developing containment strategies focuses on material characteristics. There must be a scientific basis in determining the relative toxicity of a substance based on its exposure to the human body both on an intermittent and long-term basis. Epidemiology studies in both humans and animals generally determine the acceptable exposure level of toxic substances or commonly known as OEL or Operator Exposure Levels.
NIOSH National Institute for Occupational Safety and Health has developed an OEL banding process that provides a reliable approximation of a safe exposure level for potentially hazardous chemical substances. This is referred to as an OEB or Operator Exposure Band. Assignment of an OEL Band is where expert judgment comes into play based on comprehensive epidemiological knowledge.

Besides NIOSH, others have developed similar but different banding systems along with suggested OEL levels and methods of containment.
As drug substances become more potent and more active with smaller particle sizes, new banding systems have been developed to accommodate the newest high potency active pharmaceutical ingredients and intermediates. The chart below reflects banding to below 1 nanogram per cubic meter dust concentration.

Because of potential inconsistency in banding from one standard to another and many other reasons, the development of a dust containment strategy, process, and material handling solutions should be by means of a collaboration with all parties involved. This would include team members from the end-user such as but not limited to EHS’s representation, facilities management, process, equipment engineering as well as chemical operators.
Other parties such as engineering and architectural firms bring their own set of talents and expertise into the mix. In most cases, the A&E firms have the essential role of defining the scope of supply and operating performance standards of the process and containment equipment. Collaboration between the containment vendor and process equipment manufacture is equally important. Depending on the OEB/OEL, a containment solution can consist of primary, secondary, and sometimes tertiary measures. Industrial hygienists and specialty containment and testing consulting firms often play a significant role in characterizing the substance to be contained and may offer advice regarding containment measures and strategies.
Kilo-Size Batch Containment
Containment methods of conical mills very much depend on the size of the mill as well as the assignment of the OEL band. For mildly hazardous powders, and processing small scale kilo size batches, one may consider containment of the conical mill’s inlet and discharge. These arrangements are often referred to as “bottle to bottle” or “bag to bag”. These containment strategies are typically backed up with static PPE methods such as gowning, face, ear, and eye-protecting as well as a NIOSH rated respirator typically prescribed by an EH&S representative and/or company policy. Even for mildly hazardous materials, a smaller milling process may take place in a vent hood or laminar downflow booth.

In the left example, process material pre-charged in the upper container is isolated from the mill inlet by means of a butterfly valve. Once the mill is started the valve can be opened. Similarly, an isolation valve on the mill discharge remains open during the milling process. Once the batch is complete, the valve can be closed thus sealing the lower container.
Standard tri-clamp connections ensure fast deployment and easy docking of the containers.
Again, in the context of mildly hazardous powders, plastic charge bags, and plastic charge bottles have gained in popularity for single-use applications. Charge bags can be used in conjunction with or without isolation valves. They easily adapt to the conical mill inlet and discharge.
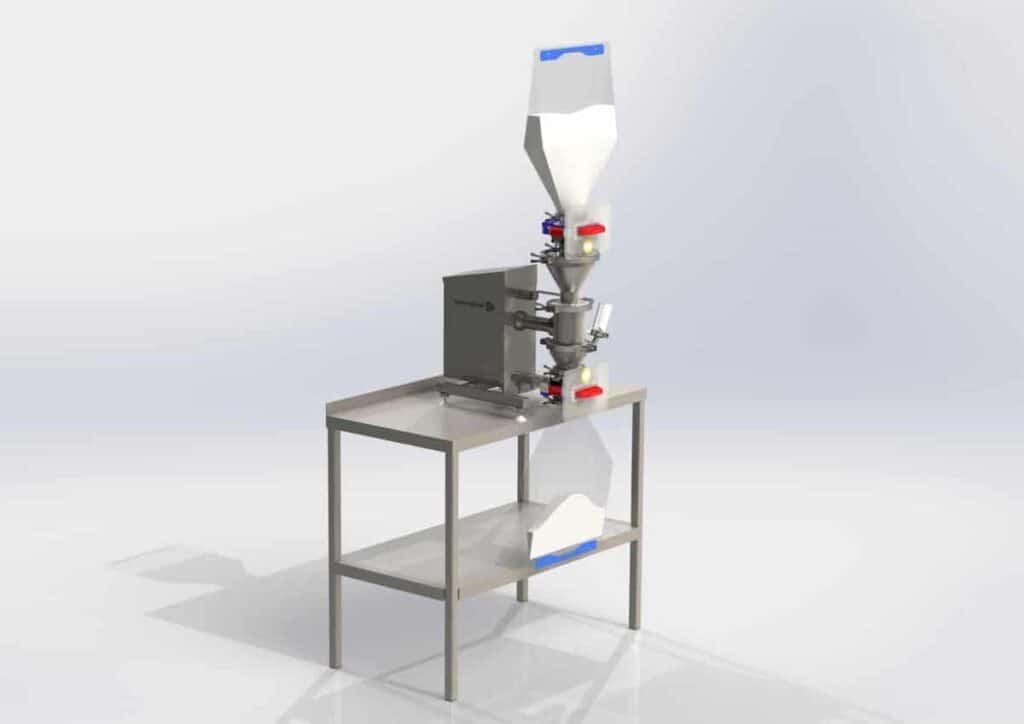
In an all solid “container to container” milling application, the displacement of air from the discharge container as it fills may require venting. This happens when the air or gas in the lower container cannot percolate upward through the mill and through the bed of powder contained in the upper feed container. When using plastic charge and collection bags, the bags can be manipulated to force air or gas from the collection to the feed bag. This avoids the use of vents and vent filters.
Beyond OEB 2, containment of the milling process becomes more stringent. Soft goods (plastic) single-use and rigid permanent isolators are called for. Both designs have their advantages and disadvantages. In general, rigid isolators are application-specific and ergonomically designed for specific processes. However, single-use plastic isolators can be custom-fabricated to accommodate specific containment requirements. Moreover, the range of application can be further extended by incorporating a rigid stainless steel frame, one or more rigid walls, and forced ventilation.

In the left example, a Hanningfield Uni-Mill M05-U is attached to the isolator rear wall. The complete milling head can be disconnected inside the isolator and bagged. Removal is through an RTP port built into the isolator. The design of the underdriven Uni-Mill allows for the easy separation of the functional milling head from the utility, motor, and electric/electronic components.
Isolators for a higher level of containment most often are under negative pressure. This ensures an ingress of air thus keeping migrant dust inside the isolator and captured in a ULPA or other appropriate filtration system. As a backup to containment, PPE including standard respirators or powered respirators (PAPR) often is prescribed.
Larger Scale Contained Powder Milling Systems
When powder milling and validation screening processes are unpractical to contain in an isolator due to the large batch size, other containment strategies must be considered.
Depending on the EH&S mandates, for lower mildly hazardous bands, one containment strategy involves the use of silicone caps and penetrations.
Vacuum can also be employed as a method for general dust containment for non-hazardous or minimally hazardous containment along with operator PPE for certain applications. Integration of unit processes while containing dust creates efficiencies while offering varying degrees of dust containment.

For stricter containment requirements, a flex-pack to the flex-pack arrangement may be considered. There are advantages and disadvantages to this system. A primary advantage is the overall cost. The flex-pack in some contained applications eliminates the need for split butterfly high containment valves. However, downstream, and subsequent processes must be able to accommodate this type of packaging.
Flex-packs attach to the mill inlet and discharge by means of special stainless steel ring adapters and band sealing tool. The integrity of the seals requires operator training and special crimping methods and tools.
A more conventional approach to a contained milling system is a rigid bin to bin system. For higher containment requirements split butterfly valves are used to isolate the Uni-Mill from the upper and lower feed bins.
Venting and contained sampling can also be incorporated into the design of a bin to bin system.
Breaking Containment Post-Processing
The integrity of the split butterfly valves is crucial to maintaining the prescribed OEL levels of the milling system. For the most stringent requirements, vacuum aspiration applied between the active and passive valve sections is needed when separating the valve sections. As the number of valve cycles increase, wear on the valve seats occur. For this reason, periodic maintenance is incredibly important.
Airborne dust within the containment zone is another matter that needs to be addressed as part of a total containment plan and execution. Spray balls and nozzles generally are employed to wet all the internal surfaces of the empty feed container and milling chamber before breaking containment. Proper washing device positioning is needed to wet out all surfaces. Of course, the mill must have proper provisions to be wet in place (WIP).
Summary
Comprehensive Containment Strategy: Size reduction by its very nature creates dust. Containment of toxic substances and protection from operator exposure requires a comprehensive protection plan and a well-thought-out execution strategy.
Classifying HPAPIs: High Potency Active Pharmaceutical Ingredients (HPAPIs) and other hazardous substances must be identified and classified in accordance with the most recent containment guidelines. This is the key to further action.
Increasingly Potent APIs: APIs are becoming more potent requiring higher level of containment and lower operator exposure.
Contained Milling: Whether dealing with large or small batch sizes, conical milling operations can be effectively contained for all OEB levels through primary, secondary, and tertiary containment strategies.
Collaboration is Key: The best and most effective contained milling strategy results from a collaboration between many stakeholders. Ergonomics and operator input should never be overlooked.