Pre-testing in the TBMA test room showed that these products can be easily processed with vacuum conveying. Also, a smart solution was invented to prevent cross-contamination.
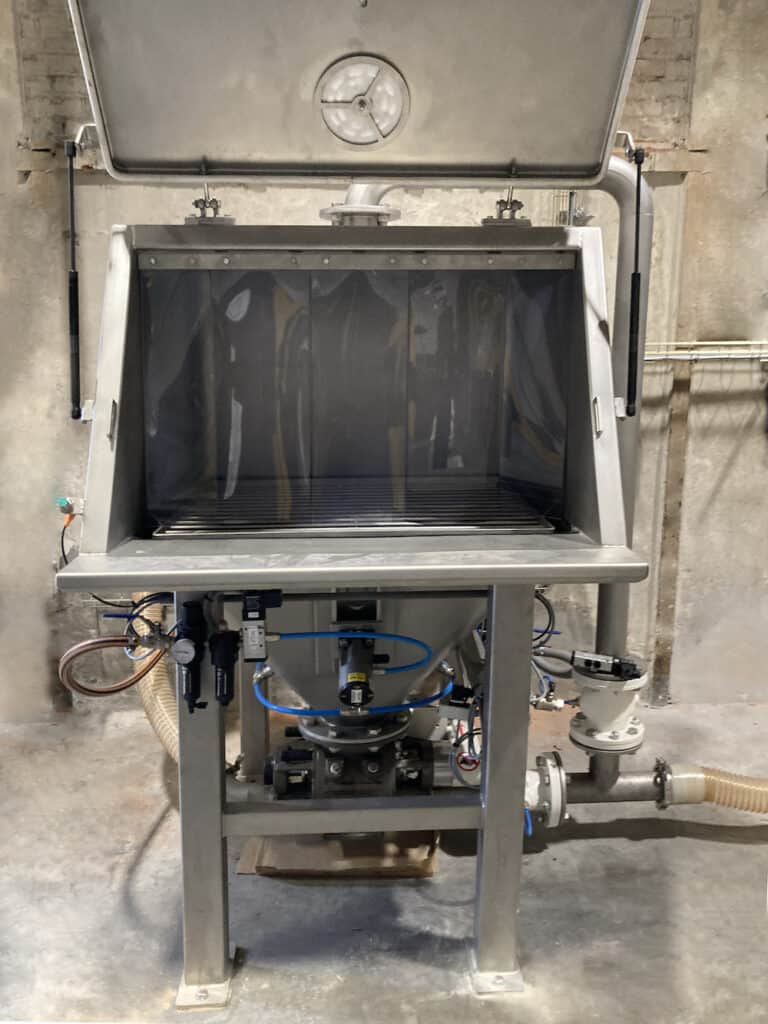
Campine in Beerse (Belgium) recycles industrial waste streams to make new raw materials. The company dismantles lead-based car batteries and is engaged in the recovery of metals. They also produce high-quality antimony trioxide as flame retardant synergist, raw material for pigments or catalyst for PET production. This makes the company a prominent player in the circular economy. Specifically for the plastic market, Campine produces masterbatches in which powdered additives are mixed in a carrier polymer. In this way, they relieve their customers when it comes to safe processing of dusty and ATEX-sensitive powders.
Alternative
To optimise their production process, Campine sought an alternative to pouring bags of additives directly into a gravimetric feeder. This refilling was a dusty and non-ergonomic affair, all the more so because the bags had to be raised to a higher working level. The stickiness of some products did create a challenge. Also, it had to be taken into account that the feeder is being used for many different products, and that cross-contamination should be excluded as far as possible.
Bag dumping cabinet
TBMA proposed installing a bag dumping cabinet with a blow-through rotary valve underneath and then a double conveying line with a Piab vacuum conveyor at the end point. The Piab unit takes care of the dust extraction of the cabinet and then the vacuum conveying of the product from the cabinet via the blow-through rotary valve and the conveying line to the feeder. The dust extraction eliminates the need for a separately constructed or external filter, which is a significant saving. An additional disadvantage of an external filter is that the collected product must be regarded as waste.
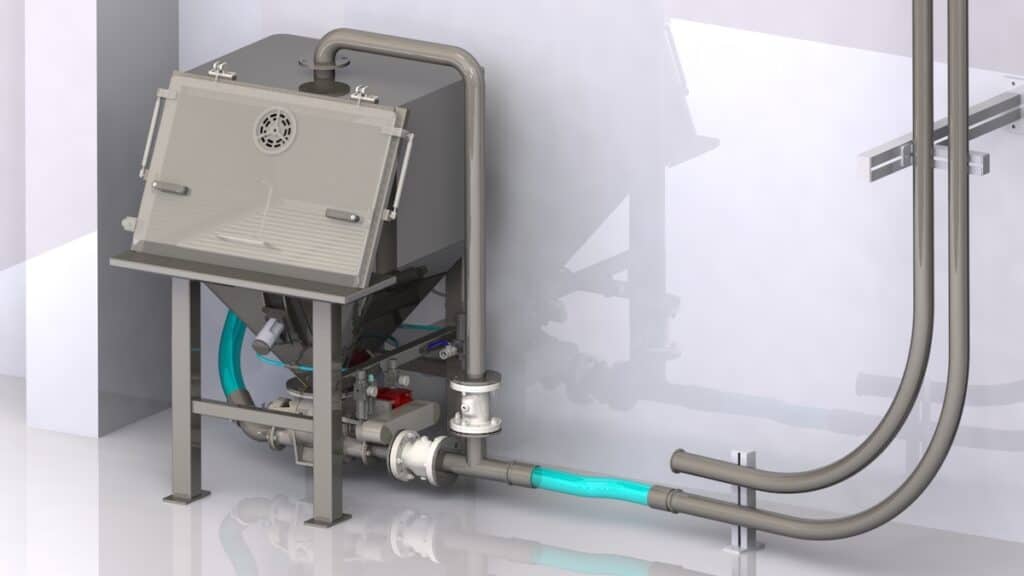
Dust extraction
During the emptying of the bags, the dust extraction works, but the product is not yet conveyed from the cabinet. The cabinet’s window is equipped with vertical plastic strips. These ensure that the released substance does not come out and the window is closed as much as possible during emptying of the bags. As a result, less dust extraction is required. The Piab creates a vacuum in the cabinet: an air flow is created inwards, which means that any dust is sucked in. The dust is brought into the conveying line via the top of the cabinet and taken with the next refill of the feeder, so that nothing is lost.
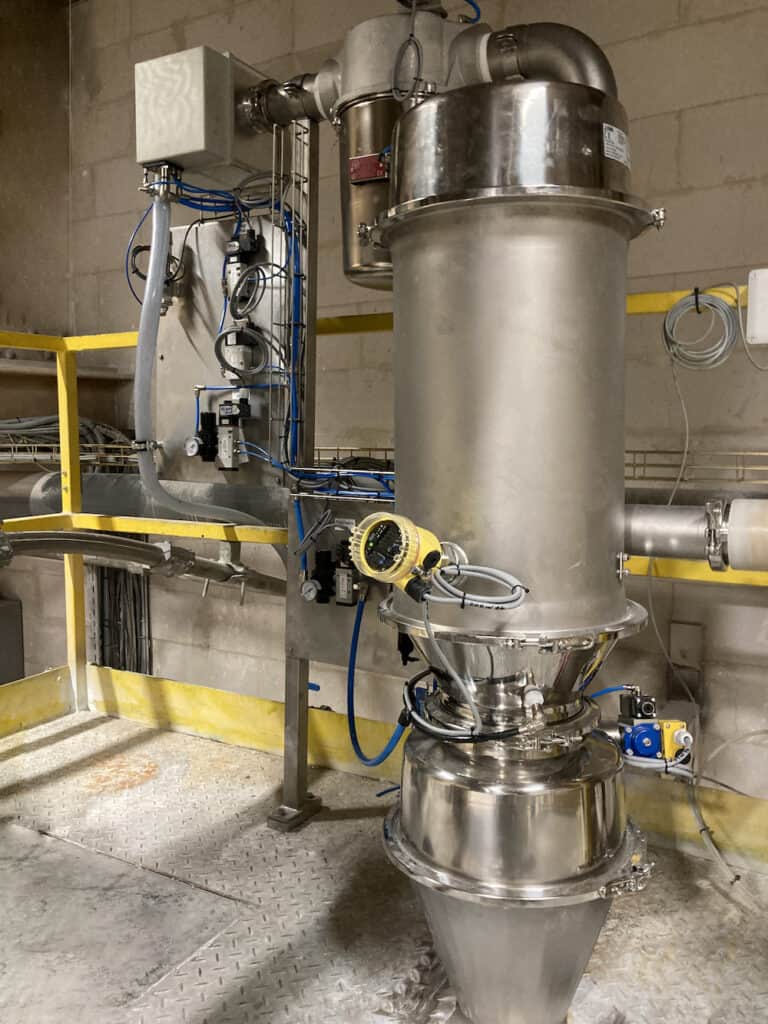
Vacuum conveying
After filling the cabinet, the dust extraction is closed and a valve in the conveying line under the blow-through rotary valve is opened. The Piab now generates a vacuum under the rotary valve and consequently, the product that falls from the rotor sockets into the conveying line is sucked into the feeder. The correct amount of product for the refill is set up above the feeder, so that it can be refilled quickly upon product request.
Teflon coating
To demonstrate in advance that this system works, extensive tests have been carried out in the TBMA test room with various Campine products. The Piab unit proved to be perfectly compliant, although initially a number of products stuck a bit and product changes required more cleaning work than desired. The bag dumping cabinet and the Piab unit are therefore internally provided with a teflon coating to prevent the product from sticking. The TBMA HGR150 rotary valve is easy detachable and therefore easy to inspect and clean. The same goes for the Piab unit. All components are suitable for ATEX zone 21 internally and zone 22 externally.
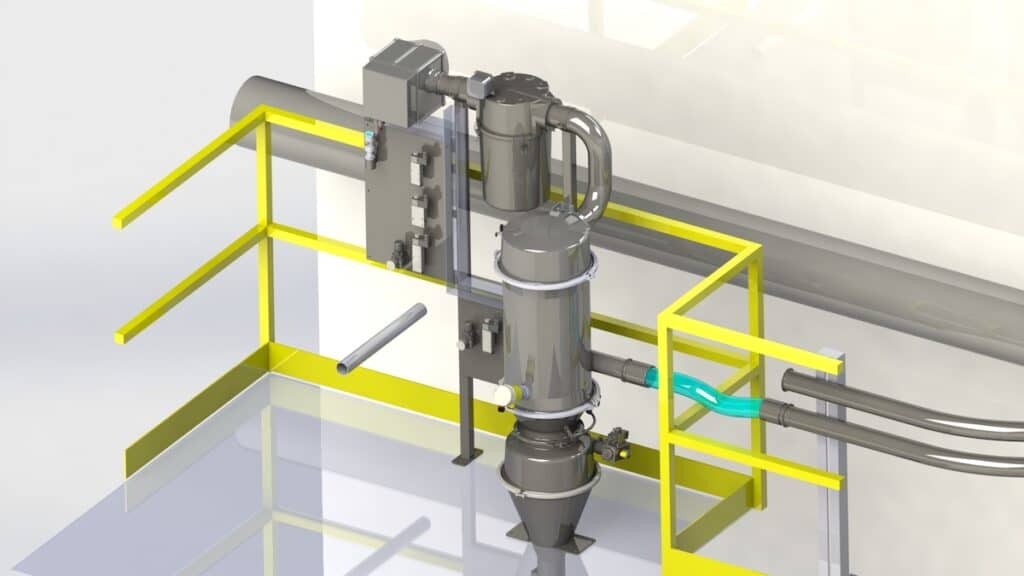
Extra line
The fact that pipes are the most difficult to clean does not pose any major problems for most products because hardly any rests remain. However, Campine also processes one product that should definitely not come into contact with others. Therefore, a separate conveying line is provided, exclusively for this product. In case of this specific product change, the filter plate in the Piab must be also changed. A simple operation, that can be performed quickly and easily by one operator.
New order
Campine recently placed an order for the same system for supplying product to another feeder at the same location. This system is expanded with a bigbag unloading installation. The Piab vacuum conveyor will also be used for dust extraction on the discharge hopper.
Wouter Van den Broeck, project maintenance engineer at Campine: “TBMA’s system is smart, safe and economical. The tests beforehand convinced us of the proper functioning of vacuum conveying. Thanks to the coatings, there is hardly any sticking. We are very satisfied with the installation and cooperation with TBMA. Reason enough to order the same system for one of our other feeders.”