Pneumatic conveying systems convey solids varying in size from fine powder to mm-sized granules depending on the diameter of the pipeline. The transport (conveying) is done by the particles being suspended in a stream of air in a horizontal, inclined or vertical pipeline ranging from a few meters to several hundred meters in length. The system is isolated from the environment therefore there is no spillage or contamination, unless damage occurs from inside the pipeline due to erosion or external force, making it a preferable mode of transportation.
The pneumatic conveying systems movement source supplies positive or negative compressed air, the material flows from a feeding hopper, by means of the conveying pipeline, to its destination (the (receiver). The receiver separates the conveyed material from the carrier medium.
The range of materials that can be conveyed by pneumatic conveying is based on the physical property of the material. The particle size, density, hardness, resistance to damage, and cohesive properties are key factors in determining whether a material is suitable for this conveying method type. Generally, cohesive and sticky materials are not suitable for a pneumatic conveying process because they can easily create pipeline blockage.
Furthermore, the pneumatic conveying system is the simplest method for efficiently conveying powders, granules, and pellets through pipelines in dry form. Pneumatic conveying systems are used in many industries to convey materials such as laboratory specimens, oil & gas, pulverized coal, sand, loading of cement to ships, food grains, sugar, milk powder, etc., and which have been around and used for several decades.
Acceleration and the velocity
Particle velocity during pneumatic conveying is the velocity at which a particle travels longitudinally along the pipeline. In the context of particle attrition by impact, it has been repeatedly demonstrated that impact velocity is by far the most influential factor in erosion and attrition which we will show later on.
Therefore, it is essential to understand the operating parameters that affect the particle velocity within the pipeline. In past research, Delft Solids Solutions had a client who had issues with material degradation during pneumatic transport whereby velocity played a key role, lowering or increasing velocity can have both a positive or negative effects on material abrasion and possible degradation. Depending on the material being transported and to minimize the particle attrition, the initial onsite testing of superficial air velocity is usually in the range of 10 to 50 m/s, which is generally close to the slip velocity (particle velocity).
However, the correlation between attrition and erosion of the pipeline is another factor to consider. Aside from particle attrition, erosion also occurs when the particles rush past the pipeline walls and impact bends during conveying. This is where pneumatic conveying system design comes into play. The multiple bends and one or more material entry points to transport material around a production facility play a crucial role in efficiency, sustainability, and product quality by trying to minimize particle attrition and pipeline wall erosion. The more bends, the more complicated the design of the pneumatic transport systems, which may increase particle impact zones along with the system. Hence while designing a transport system, it is best to use as few bends as possible. Bends increase the pressure drop in a line and are also the areas in which most of the serious erosion and particle attrition are caused.
Erosion
Erosion in pneumatic conveying pipelines is more prominent at bends due to the conveyed particle impact velocity, the angle of the bend, the particle hardness and abrasiveness, and the volume of the particles being loaded into the system. Due to repeated collisions of abrasive particles, cutting into the walls and primarily at bends, it is important to design a pneumatic conveying system with only essential bends.
Conveying of food substances such as milk powder, grains, sugars, etc. could be prone to degradation due to attrition and contamination with eroded pneumatic conveying pipe particulates which may cause health and quality issues. Therefore, it is important to find ways to minimize erosion of pneumatic conveying system pipes. The pipeline geometry plays a role, such as the internal diameter, internal finishing of the pipe quality, the pipe material, coupling alignment, length of the straight sections, and the long or short angles of the bends are crucial in minimizing particle damage and pipeline abrasion including maintaining particle quality and structure as much as possible.
Another aspect is the abrasive character of the particle being transported, for example, sugar will have different abrasive properties compared to milk powder.
It is clear to assume that the surface erosion and particulate attrition are both the results of the same contact event since both are in contact and interact during transport. Furthermore, the abrasive phenomenon responsible for material removal varies significantly between the two surface materials with both having unique abrasion characteristics whereby the hardness of the particles being transported and that of the surface material play a fundamental role in determining e.g. the fracture toughness and the material of the pipe walls resulting in either damage to the particle or the wall or both.
Delft Solids Solutions examines erosion case
In the researched case study, the aforementioned erosion phenomenon in a pipeline was evident and shown with SEM-EDX equipment. In that study, a material containing Ca, CI, C, and O was being conveyed at 8 m/s.
The tests showed that nearly all bends in the pneumatic test rig had been affected and erosion of the pipe walls was evident.
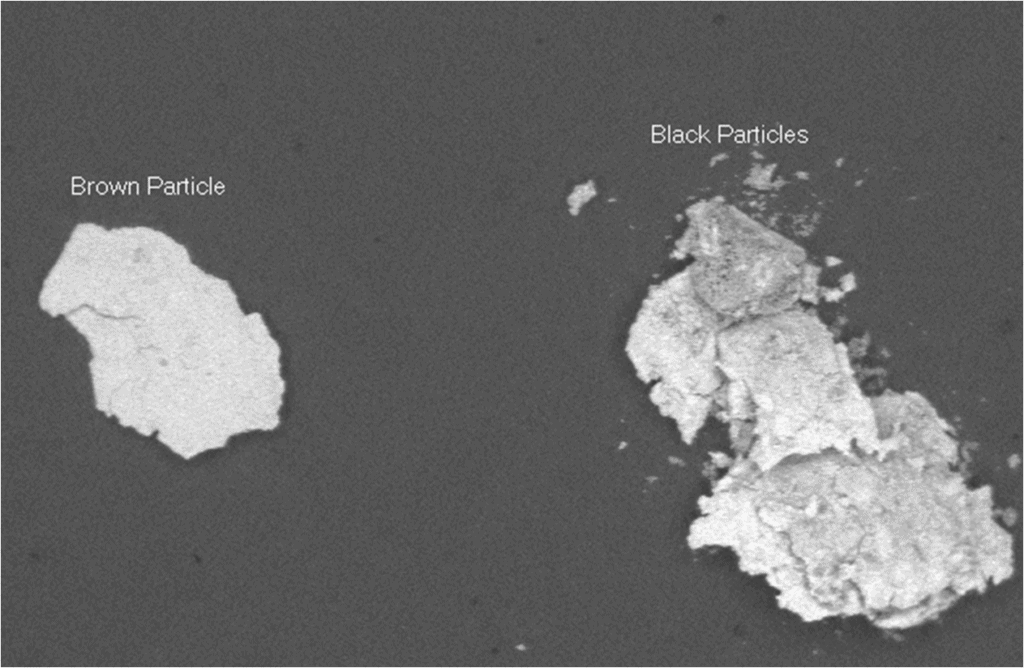
The black, darker particles as seen in the image below are the erodent wall particles containing the heavy metals Zn and Fe. These contaminates were found throughout the transported material.
It is safe to say that contaminants will have an adverse effect on product quality and safety. That is why regular sample testing in industrial plants is done to adhere to standards so that contaminants are minimized by finding solutions in the conveying process.
Either by switching conveying methods or altering the particle velocity and altering bend angles in the pipeline to reduce particle impact and abrasion, which correlates with pipeline wall erosion.
Research, development, and testing are paramount in the continuous advancement of particle science and technology.
Delft Solids Solutions dedicates its time and resources to testing, offering solutions to problems encountered, and designing more efficient processing methods in the particle processing industries.
With many years of research and field experience, our people at Delft Solids Solutions are working on the sustainability of existing projects and technological advancement in our field.
Particle Transport and Storage day
For the first time Delft Solids Solutions in close collaboration with partners; ESI Eurosilo, Innofour, TUDelft, AZO, Volkmann, will organize the Transport and Storage day on Tuesday, June the 14th 2022.
During the seminar we will offer a wide array of content, handling different themes associated with transport and storage of powders and granules. Offering overview lectures applicable to all industries ranging from food, feed, pharmaceutical, and cosmetics to chemicals.
Practical information
Date: Tuesday, June 14th, 2022
Location: Fletcher Hotel Wings, Rotterdam The Hague Airport Hotel & Conference Centre, Rotterdam Airportplein 55, 3045 AP Rotterdam, The Netherlands
Arrival time: 8:45 you will be offered coffee/tea on arrival
Investment: € 450,- (excl. VAT)