This requires process analytical technology (PAT) to monitor critical process parameters (CPP) in real-time and report critical quality attributes (CQA) of the product. These factors are then utilized by formulation or process scientists to make informed, traceable, data-driven decisions or can be used to automate control for robustness and reliable process performance.
This study investigates the effect that changing CPP has on CQA (particle size and moisture content) during a fluid bed granulation (FBG) process. Throughout each step, batch changes were made to CPP to examine their effect on the particle size and moisture content. As process parameters were changed, a response can be seen in the particle size and moisture content profile for each batch. Comparisons were also made between in-line and off-line particle size distribution measurement methods for end-product material.
Granulation in pharmaceutical solid dosage manufacturing is used to prevent segregation of the components, improve the flow, and compaction properties of powders. Over-drying can cause attrition where granules fracture to create fines. Under-drying can lead to a sticky product that clings to surfaces such as tablet punches. Excess moisture also has impacts on product stability and shelf life. For these reasons, the moisture content is a CQA. Particle size distribution (PSD) impacts flowability, compressibility and dissolution of drug products and is also a CQA.
Traditionally to determine particle size or moisture content, samples are withdrawn from the process and analyzed off-line in a lab for particle size and moisture content. Moisture content is typically measured via a loss on drying (LOD) method. For particle size measurement of wet processes, the normally only-end product is measured to determine when to stop granulating. This is often done with sieve analysis or other at-line methods. This off/at-line analysis is slow, costly and all too late to modify a batch.
For an FBG process, a number of factors impact not only the end-point particle size but also the preceding particle size growth profile over time. To optimize the process, it is desired that the particle size growth profile over time is monitored and controlled. This will reduce batch-to-batch variation and enable the producer to reach the quality target product profile (QTPP). Real-time, in-line measurement of particle size and moisture during process development affords the ability to adjust CPPs of an FBG process and establish a more robust and reliable process.
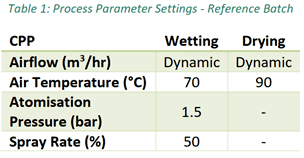
This study utilizes Eyecon2, which is a direct-imaging, real-time particle size analyzer, with a proven ability to monitor and track particle growth within an FBG process.
The study also utilizes Multieye2, a non-product contact, near-infrared spectrometer to monitor moisture content in real-time.
These technologies have proven to be an integral component in process development studies and have enabled pharmaceutical manufacturers to gain far greater detail to understand their manufacturing processes. In a dynamic pharmaceutical manufacturing process, this level of process knowledge and understanding is not achievable through sampling and off-line analysis.
The experimental plan of this study determines the effects of changing CPP on the particle size profile and moisture content during an FBG process using an Eyecon2 and Multieye2 in-line, and a Mastersizer 2000 off-line. To achieve this, the CPP of inlet air temperature, atomization pressure and spray rate was set for an optimal, uninterrupted process to create a baseline reference batch per Table 1. Further batches were executed with varying inputs of inlet air temperature, atomization pressure and spray rate to understand the effect and relationship between CCP and the CQA.
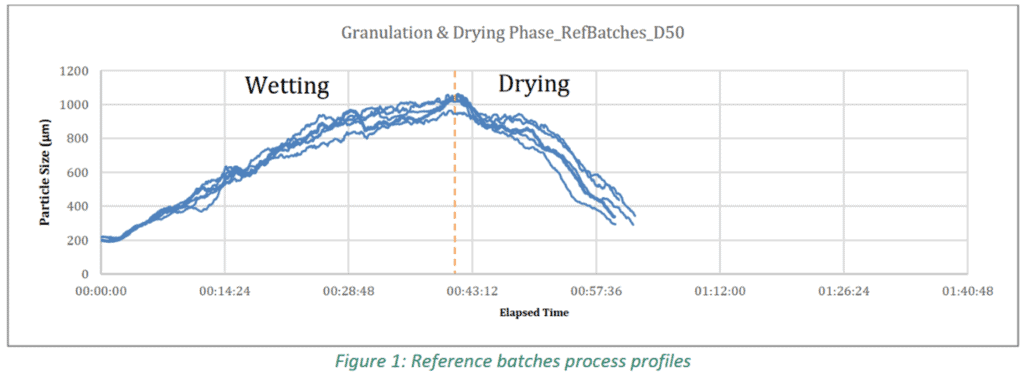
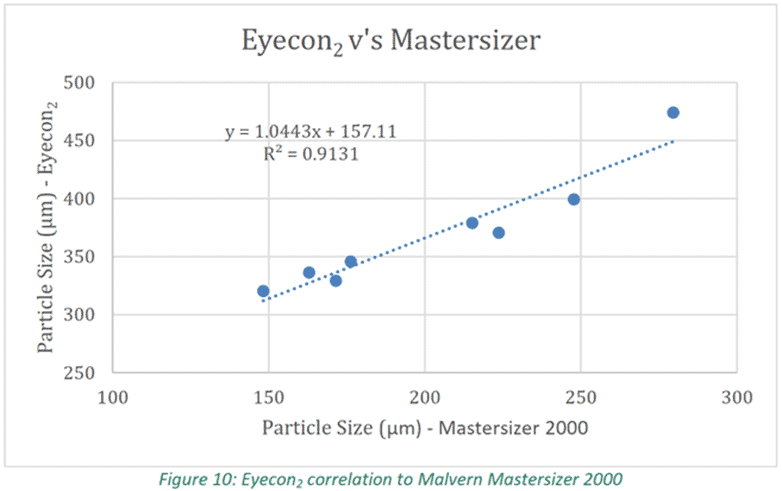
The results of the study show the effect inlet air temperature, spray rate and airflow rate have on particle size and moisture content. All three parameters also influenced the growth profile over time. It was clear that changes to one of these parameters during processing had a corresponding impact on the particle size and/or moisture content of the in-process material as seen in Figure1. As per Figure 10, it was shown that in-line Eyecon2 data correlated strongly with Mastersizer 2000 off-line lab analysis data, enabling for reliable decisions to be made, in real-time, on the process based on in-line PSD data.
The study demonstrates the benefit of monitoring and controlling particle size and moisture content by varying the process parameters of inlet air temperature, airflow rate and spray rate.