Simplifying the processing of difficult to handle powders is often made easier with agitated screw feeder systems. By combining the roles of hopper and screw feeder, the Agitated screw feeder eliminates the discharge issues often experienced at the interface between the hopper discharge point and the screw feeder when handing poorly flowing powders.
Agitating powders prevent ratholing, arching, and other hopper flow issues by using rotating blades to constantly agitate the fine cohesive powder or filter cake. By integrating the feeder within the hopper it is also easier to ensure consistent feed rates, whether the material is required to be discharged quickly or the subsequent process needs a slow and stable feed. Typically, Ajax’s agitated screw feeders are individually designed to suit each customer’s specific applications – whether that’s different batch holding capacities, discharge rate needs, or variability inflow condition of the material to be handled.

An Ajax agitated screw feeder fabricated in Alloy 22 for its extreme corrosion resistance.
For Thomas Swan, a leading manufacturer of performance and specialty chemicals, Ajax Equipment has supplied a large capacity ATEX rated agitated screw feeder for handling an active ingredient used in the production of personal healthcare products.
The large stainless-steel agitated screw feeder combines a large holding volume vessel with a twin-bladed agitator, which features a special profile to help maintain material flow condition, agitate the batch, and sweep it towards the integral Lynflow ribbon flighted screw feeder offset below.
The agitated screw feeder processes up to two batches of material from a centrifuge over an extended period, ensuring the powder is in the correct condition before quickly and effectively discharging it into a downstream dryer.
Commenting, Andrew McNally, Senior Engineering Manager at Thomas Swan, said, “The Ajax agitated screw feeder was installed as part of a significant plant upgrade project. This is an impressive piece of equipment and performs exactly as designed. When it came to selecting equipment for handling this non-free-flowing solid, Ajax was my go-to. Ajax has provided me with similar solids handling equipment previously and the equipment they provide is well designed, robust and most importantly always ensures the material flows.”
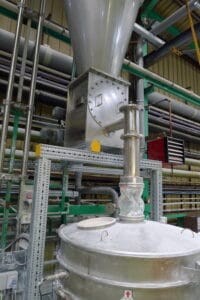
As the production process can not be stopped immediately, Ajax’s agitated screw feeder holds and maintains the material whilst the filter is changed.
In another project, Ajax has recently supplied two stainless steel agitated screw feeders designed to handle batches of 6T of centrifuge product within a barrel-shaped hopper section which provide exceptionally good containment of the chemical powder.
Previously Ajax produced a similarly sized agitated screw feeder for the same chemical manufacturer in Alloy 22, an extremely corrosion-resistant high nickel alloy for, particularly demanding process conditions.
For all three of these large, agitated screw feeders powder testing was a key part of the design process in assessing the extent of the agitator, the screw feeder form below – in this case, ribbon flights were used to avoid clogging with the adhesive powder – and to help specify the correct drive power required for the agitator and screw.
Another advantage of integrating an agitated feeder into chemical processing is where it is necessary to hold-up a product on a more infrequent basis, for a filter change for example. For a specialist manufacturer of inorganic specialty chemicals processing a highly hygroscopic powder, an agitated screw feeder was used to collect powder from a vertical elevator while a filter was changed. Using an agitated screw feeder in this way kept the powder in a good flowing condition until processing could be resumed.
Agitated screw feeders provide a flexible solution to many powder processing facilities. By ensuring material condition is maintained until required, offering storage that ranges from a few kilograms to several tonnes as well as regulating feed – even down to relatively low rates – agitated screw feeders not only remove potential issues but bring considerable benefits to chemical processing.