The new Seeflex 040E Corner Connector is a flexible connector made from BFM®’s strong Seeflex 040E material, a clear, ether-based thermoplastic polyurethane alloy. The uniquely shaped snap-fit connector features a tapered infeed end, 110º angled ‘corner’ bend and straight drain output end.
It is designed to redirect the CIP wash fluid out of the process equipment at the end of the CIP cycle, helping to ensure the rest of the plant stays dry and product is free from chemicals used in the cleaning process.
Reduces volume of expensive steel pipework
BFM®’s CEO, Blair McPheat, says the product was designed in response to requests from systems integrators who were designing new process lines and wanted a more cost-effective way to drain Clean-In-Place (CIP) wash water.
“They were already using our connectors for a number of processes and were aware that they sealed perfectly during the CIP wash process,” said McPheat. “We knew there must be a way we could extend the usability of the BFM® connector snap-fit concept to also replace much of the expensive stainless steel involved in typical tun dish-type drainage arrangements.”
The conduit between your equipment and drain
That’s when the idea came about for a ‘corner’ shaped connector that incorporated a tapered inlet end, bending around to a narrower, straight drainage end.
BFM® fitting spigots of corresponding diameters are welded to the process pipe that serves as the wash water egress point, and to the pipe where the water will be drained into. The Corner Connector is simply then snap-fitted into those spigots to become the conduit between the equipment and the drainpipe.
The Seeflex 040E Corner Connectors are all custom-made to the specific installation requirements, with the inlet and outlet diameters, and connector lengths being variable (within certain manufacturing limits).
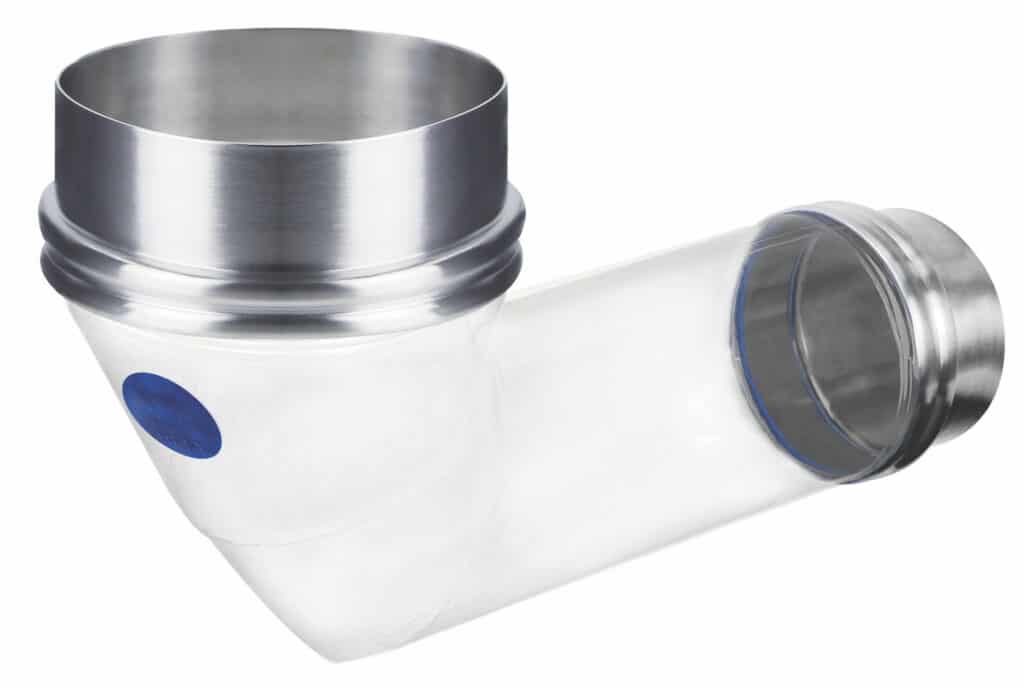
Simplifies CIP changeover processes
Operators find the simple snap-fit of the BFM® fitting system makes product changeovers a breeze compared to clamped systems. The same applies to Clean in Place processes where connectors need to be removed and refitted. That can be a time-consuming task if you have traditional clamped connectors.
“That’s another reason we’re confident having a snap-in BFM® connector that can replace these expensive tun dish swivel installations will appeal to many companies – as well as the big savings on the stainless-steel pipework of course!” said McPheat.
Corner Connector can replace corrugated transitions
A further potential application for the uniquely shaped flexible Corner Connector is under vibratory machines like sifters and sieves to connect directly to another process on a lower level.
“The angle of the corner lets you have visible product flow between two pieces of machinery at differing output/input levels. It’s a much more hygienic option than corrugated/bellows type connectors between machines – there are no crevices for product to build-up” said McPheat.
The Seeflex 040E material the Corner Connector is made from complies with FDA, USDA & EU regulations.