This is made possible through a unique multi-oil/multi-process approach and personalized services. The core of AAK Rotterdam’s operations lies in the refinement of vegetable oils. Within this process, the shelf life of freshly pressed oils is extended by removing color, odor, and flavor components. At this facility of AAK, oils are produced to the highest food safety standards, mainly for customers in the baby food industry. AAK Rotterdam specializes in supplying these refined oils as raw materials to various manufacturers.
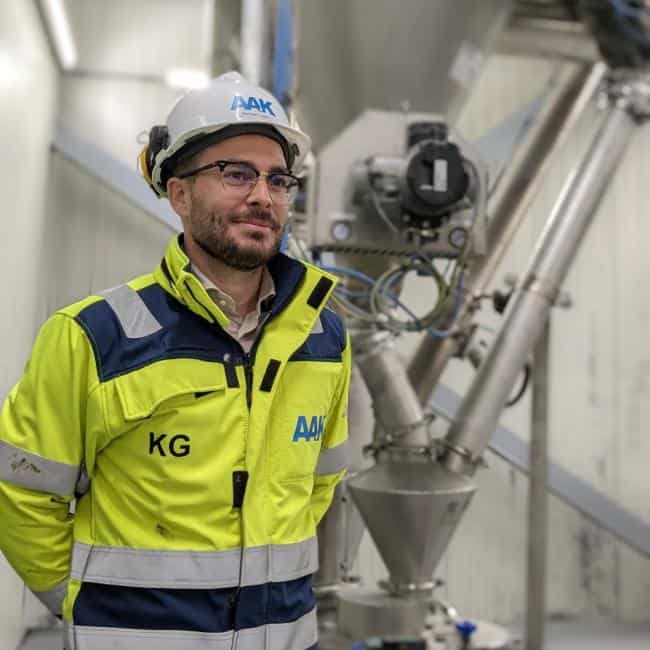
A precise process requires accurate powder dosing
The food industry adheres to strict hygiene and product composition standards. When it comes to food products for children, these standards are even more rigorous. Therefore, AAK’s production facilities are subject to stringent quality controls and are certified according to international standards. The plant-based oil is purified using heat and other methods. Part of the oil filtering process involves powders. These adhere to a stainless-steel mesh, retaining unwanted substances from the oil.
Previously, the powder addition was done with a dosing screw. The amount of product to be added was determined based on the rotational speed, and the screw was calibrated once a week. This method had two main drawbacks: dust emission and the risk of insufficient powder addition. The latter often led to downtime, as typically once a month a batch had to be rerun to ensure the right quality. Seeking to improve powder dosing, AAK sought a new solution.
Custom solutions and a clear vision of the outcome
Kenneth Gijzen, Maintenance & Engineering Manager at AAK Rotterdam, states: “We needed a custom solution that had to fit precisely in our line, offering accuracy and reduced dust emission. Our Big Bag Unloading Stations are in a fixed place, and the endpoint is also set. The space in between was all we had to work with. We requested quotes from several organizations and ultimately chose Dinnissen due to their detailed 3D sketches demonstrating their ability to assist.”
A gain-in-weight powder dosing installation
The dosing screw has been replaced by a Dinnissen installation. One floor above the liquid tank, three different powders are added to the process. These powders are delivered from one of two Big Bag Discharging Stations or a bag dump cabinet to dosing hoppers on load cells. The dosing is done through a vibrating butterfly valve. The signal from the load cells enables the valve to allow the desired quantity and close once enough powder is dosed. Kenneth notes the benefits: “Initially, we would overdose for safety to ensure enough powder was added to the process. Now, we can dose much more precisely, saving product and ensuring optimal process addition.”
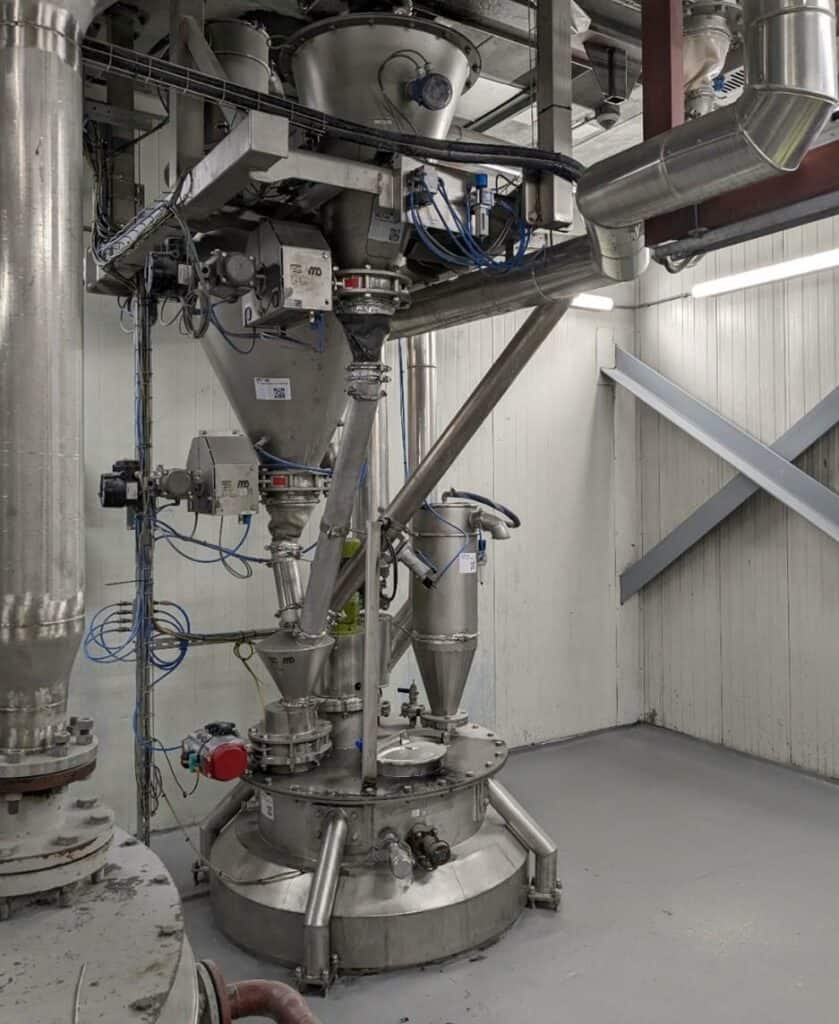
A more hygienic, efficient, and cost-effective process
According to Kenneth, the new line has brought several advantages: “Firstly, reduced dust emission makes the process more hygienic and healthier for our employees. Additionally, the elimination of overdosing is economically beneficial. A third advantage is a significant reduction in downtime. Where batches had to be reprocessed because an insufficient amount of powder was added, we are now assured of accurate dosing. Also, weekly calibrations are no longer necessary. Finally, we are guaranteed consistent product quality.”
A reliable collaboration
Dinnissen’s proposal wasn’t the cheapest, but AAK Rotterdam chose them anyway. “What really makes Dinnissen unique, is the preliminary work,” Kenneth states. “You can literally count every bolt and nut in the drawing. This eliminates any doubt about how something is intended. I had not personally worked with Dinnissen before, but the recommendations from the associated engineering firm and Dinnissen’s detailed documentation in the preliminary phase were decisive in our choice for Dinnissen. Now, after three years of production, the installation is still running smoothly. In hindsight, we could have communicated more clearly about deadlines and delivery times, as it was sometimes unclear when to expect certain things. On the other hand, everything was handled with the utmost care. Dinnissen always finds an appropriate solution to your problem.”
After the delivery of the dosing solution, a new challenge was already on the horizon. The collaboration between AAK and Dinnissen will continue to yield great solutions in the future. AAK is committed to Making Better Happen™, and Dinnissen is more than willing to contribute to this goal.