As industries like food, packaging, and pharmaceuticals continue to experience rapid growth, the automation provided by vibratory feeding and conveying will inevitably play an increasingly critical role within this processing environment — ultimately leading to greater economies of scale.
How Vibratory Feeding & Conveying Works
Conveyors are typically used to move products from one point to another in a given process. For example, conveyors can be used to transport raw materials – such as bulk nuts – from a rail car to a storage tank, and then finally into a processing plant. In most process applications, material must first be fed into a feeder and then conveyed repeatedly throughout the plant.
To ensure a more accurate measurement of bulk materials, vibratory feeders are strategically positioned throughout a plant. These feeders are designed to deliver a controlled flow of materials into downstream processing equipment. They are particularly effective in handling a diverse range of bulk materials, such as powders, granular substances, sticky materials, and large, cumbersome items.
When the product exits the storage tank, it passes through a feeder that is specifically designed to regulate the flow into the processing stage. These feeders play a crucial role in controlling the flow rate and may require frequent starting and stopping. State-of-the-art units excel in their ability to adjust the feeding rate to meet these demands effectively.
Material on a vibratory feeder is propelled upward and forward, causing it to descend further down the tray. The tray’s deflection or stroke–combined with the frequency of the vibration–determines the speed at which the material will convey. Another important factor to consider is the angle of deflection, as it determines the height at which the product is thrown in relation to its horizontal movement.
The illustration above depicts the movement cycle of an individual particle as it advances along a vibratory feeder or conveyor tray. When a vibratory feeder operates on
a 60-cycle power supply, this particle movement cycle repeats a total of 3,600 times per minute. Conversely, with a 50-cycle power supply, the cycle repeats 3,000 times per minute. In the case of a high-deflection (HD model) electromagnetic feeder operating at 30 Hz, the material flow cycle repeats 1,800 times per minute.
To control the feed rate, adjustments to the tray’s movement or deflection are made while the number of strokes remains consistent with the power supply frequency. This means that the stroke length can be modified from 0% to 100% by altering the voltage input, allowing for both increased and decreased feed rates. With a mechanically driven feeder or conveyor, the movement cycle repeats between 75 and 90 times per minute.
The design of each vibratory feeder and conveyor is tailored to meet specific requirements, such as the desired amplitude, frequency, and angles of deflection, which are necessary to move different materials at precise rates. Various factors come into play when determining this design, including the type of material being processed, the desired flow rate, the environmental conditions, the need for process start and stop cycles, the operating cost of the equipment, and the likelihood of repair. Therefore, selecting the appropriate feeder or conveyor for the specific processing application is vital to achieve optimal efficiency.
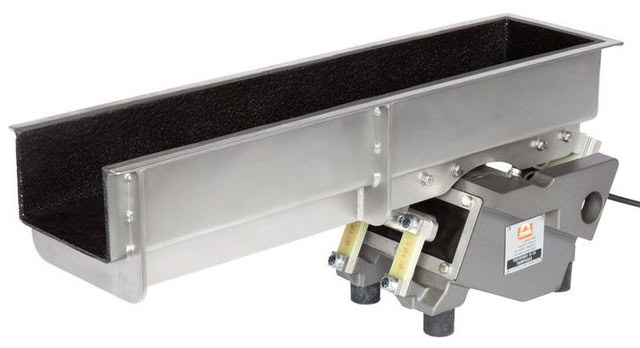
Material & Process Considerations for Vibratory Equipment
While many factors impact the selection process, the material being processed is the most important element to consider when selecting vibratory equipment. From high-frequency to high-deflection models, many types of vibratory feeders and conveyors can be customized to improve the flow rate of materials. Choosing vibratory equipment tailored to specific application requirements ensures an effective feeder solution and an extended and trouble-free service lifespan.
1. Material Size
One of the first and most important variables to consider when selecting equipment for vibratory feeding and conveying is the size of the material that will be processed. These size variations include fine, mid-size, and coarse materials.
- Fine Material: Because they tend to fluidize and flush, fine materials ranging from -50 mesh to -400 mesh do not feed well on traditional high-frequency electromagnetic feeders. The most effective way to handle these materials is to use a lower frequency, high-deflection electromagnetic feeder for low-mid range capacities or a mechanical feeder for higher capacities.
Tray Capacity | Feeder Type | Operation Range |
Low-Mid | High-Deflection Electromagnetic Feeder | 3/16” (4.76 mm) amplitude x 30 Hz |
High | Mechanical Feeder | 1/4” to 7/16” (6.35 to 11.11 mm) amplitude x 20 Hz |
- Mid-Size Material: Materials ranging from +50 mesh to 2-3” (50.8-76.2 mm) in size tend to feed very well on both traditional electromagnetic feeders (.045 to .070”, or 1.143 to 1.77 mm, amplitude x 50 or 60 Hz) and mechanical feeders. An electromagnetic feeder will offer the most precise control, while a mechanical feeder or high-deflection electromagnetic feeder will provide the greatest capacity.
- Course Material: Coarser materials that fall in the +3” to 12” (75-305 mm) size range can be handled on electromagnetic and mechanical feeders. The best feed rate control is with electromagnetic feeders and the highest capacities may be achieved with mechanical feeders.
2. Material Drag
The drag of certain materials—such as gummy candies and vitamins—and their tackiness can cause significant feeding challenges, particularly with the use of high-frequency or traditional electromagnetic feeders. This is because these materials have a high coefficient of friction, which increases surface tension and may result in material buildup on the tray surface or reduced feed velocities. In certain situations, high-deflection feeders and specially textured tray surfaces or liner materials can be used to help minimize this issue.
3. Material Flexibility
Materials that are more rigid or solid tend to feed more effectively on an electromagnetic feeder as compared to other vibratory equipment. As the flexibility or leafiness of a material increases, such as with parsley flakes, it becomes harder to feed. In this case, a high-deflection electromagnetic or mechanical feeder will be the ideal choice.
4. Bulk Density of a Material
The overall weight or bulk density of a material has a significant impact on its feeding characteristics. Lighter materials (less than 10 lbs. or 4.53 kg/cubic feet), and especially fine materials (-50 mesh), do not contain as much mass and, therefore, feed at a much slower rate. Because of this, the most effective equipment for lightweight materials, like cereal and powdery spices, are high-deflection electromagnetic and mechanical feeders.
5. Material Durability
More fragile materials, such as glass fibers and finished friable food products, will be more successfully fed and conveyed using a high-deflection vibratory unit. These types of feeders produce substantially less “G force” than typical (50-60 Hz) electromagnetic feeders by using greater amplitude while reducing the frequency—allowing for gentler handling.
6. Feeder Head Loading
Certain vibratory feeders are capable of handling a higher head load—which is the amount of material weight that rests on a feeder—compared to other vibratory units. If a vibratory feeder is used under a hopper, such as in the case of a small A, C, or HD-C model feeder, it must be able to start and operate at full amplitude with the head load.
7. Cycling or Continuous Operation
Certain vibratory feeders are capable of being cycled—stopped and started—more often than others. Electromagnetic feeders, especially high-speed models for food packaging applications, are particularly ideal for frequent on/off cycling up to 60 times per minute. Because their design lacks the belts, bearings, or other moving components that typically wear out, these feeders do not put stress on a belt or clutch when being cycled.
8. Type & Length of Service
Another important consideration is the type and length of service. For instance, does the vibratory equipment need to operate for an extended period without maintenance, or is it more of a short-term application? Although there may be a higher initial investment for a large electromagnetic feeder, it is a highly efficient piece of equipment that does not require regular maintenance and may operate for years with minimal to no attention, making it less costly over its service life.
Technological advancements and an increasing shift toward automation have made vibratory feeders and conveyors more applicable than ever across nearly all industries. From their sanitary construction and ease of cleaning to the low-maintenance design, these units are an ideal choice for facilities where greater product purity, energy savings, and streamlined operations are desired.