The Fundamentals of Fertilizer Processing
Fertilizer production starts with the procurement of raw materials, such as nitrogen, phosphorus, potassium, and secondary or micronutrients. These are processed to create nutrient-rich fertilizers in forms suitable for agricultural use. Granulation has emerged as the most popular method of fertilizer production, as granules offer consistent nutrient release, reduced dust formation, and ease of application using modern agricultural equipment.
The process typically begins with chemical reactions to produce key fertilizer compounds. For example, ammonia synthesis through the Haber-Bosch process forms the basis for nitrogen-based fertilizers, while phosphate rock undergoes treatment with sulfuric or phosphoric acid to create water-soluble phosphates. These materials are then blended, granulated, dried, and screened to produce fertilizers that meet specific agronomic needs.
Granulation techniques vary but often involve the use of rotating drums or disc pelletizers to form granules of uniform size. The granules are then dried to reduce moisture content, coated to improve storage stability, and cooled before being packaged for distribution.
Innovations Transforming Fertilizer Processing
Technological advancements have revolutionized fertilizer production, improving efficiency, reducing waste, and enhancing product quality. Among the most impactful innovations is the integration of digital tools for process optimization.
Real-time monitoring systems now provide granular data on temperature, moisture levels, particle size, and chemical composition during production. This data is analyzed using artificial intelligence (AI) algorithms to optimize operational parameters, improve consistency, and reduce downtime caused by equipment failures. These digital solutions ensure that granules meet the precise specifications required for modern agricultural practices.
In the realm of granulation, advancements in drum granulators and fluid bed technology have significantly improved efficiency. Modern granulators offer precise control over size distribution, ensuring that granules are uniform and suitable for mechanical application. Fluidized bed systems, meanwhile, enhance coating processes, allowing for controlled-release fertilizers that reduce nutrient losses and improve environmental outcomes.
Sustainability has also driven innovation in fertilizer processing. Closed-loop systems capture and reuse emissions such as ammonia, minimizing environmental impact and reducing raw material waste. Additionally, advancements in by-product recovery, such as extracting gypsum from phosphate processing or reusing carbon dioxide in urea production, are contributing to a circular economy.
Safety Protocols in Fertilizer Manufacturing
Safety is paramount in fertilizer production, particularly given the chemical reactions and materials involved. The risks associated with handling reactive chemicals such as ammonia and ammonium nitrate necessitate stringent safety measures.
Explosion risks are a major concern, especially in facilities producing nitrogen-based fertilizers. Ammonium nitrate, a key component in many fertilizers, is highly reactive and has been implicated in catastrophic industrial accidents. To mitigate this, production facilities adhere to strict safety protocols, including temperature monitoring, controlled mixing processes, and the separation of reactive substances. Specialized coatings can also stabilize ammonium nitrate granules, reducing their volatility.
Dust explosion hazards are equally critical, especially during granulation, drying, and conveying stages. Granulated fertilizers produce less dust than powders, but fine particles can still accumulate in equipment or airborne clouds, posing significant risks. Advanced dust collection systems, including cyclones and baghouse filters, capture particles before they pose a danger, while explosion venting systems ensure that any incidents are safely contained.
Corrosion and material degradation are additional safety concerns in fertilizer plants. The highly acidic and reactive nature of certain chemicals used in production can damage equipment over time, leading to potential failures. Regular inspections, the use of corrosion-resistant materials, and automated cleaning systems help mitigate these risks.
Challenges in Fertilizer Processing
The fertilizer industry faces numerous challenges, from managing raw material variability to balancing environmental and economic pressures.
One of the primary hurdles is the variability in raw material quality. For example, phosphate rock varies in purity depending on its source, affecting the efficiency of chemical reactions and the quality of the final product. Advanced analytical tools are increasingly being used to assess raw material composition in real-time, allowing for adjustments to processing parameters and blending ratios.
Energy consumption is another critical challenge. Fertilizer production, particularly nitrogen-based fertilizers, is energy-intensive. The Haber-Bosch process alone consumes substantial amounts of energy and contributes significantly to greenhouse gas emissions. Manufacturers are exploring alternatives such as green ammonia production, which uses renewable energy sources to synthesize ammonia, significantly reducing the carbon footprint of fertilizer production.
Environmental sustainability is a growing concern. Fertilizer manufacturing produces emissions such as nitrogen oxides (NOx) and ammonia, which can contribute to air and water pollution. Wastewater containing phosphates and nitrates poses a threat to aquatic ecosystems, causing eutrophication. Advanced scrubber systems, closed-loop water management, and innovative treatment methods are helping manufacturers minimize their environmental impact.
Storage and transportation also present challenges. Granulated fertilizers are hygroscopic, meaning they absorb moisture from the air. This can lead to clumping, nutrient degradation, and reduced usability. Manufacturers are investing in advanced coatings and packaging solutions to improve moisture resistance and maintain product quality during storage and transport.
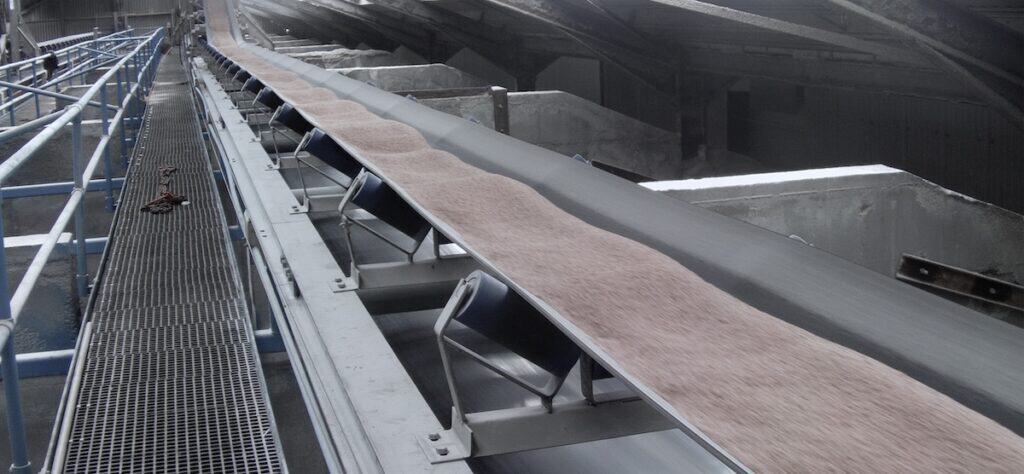
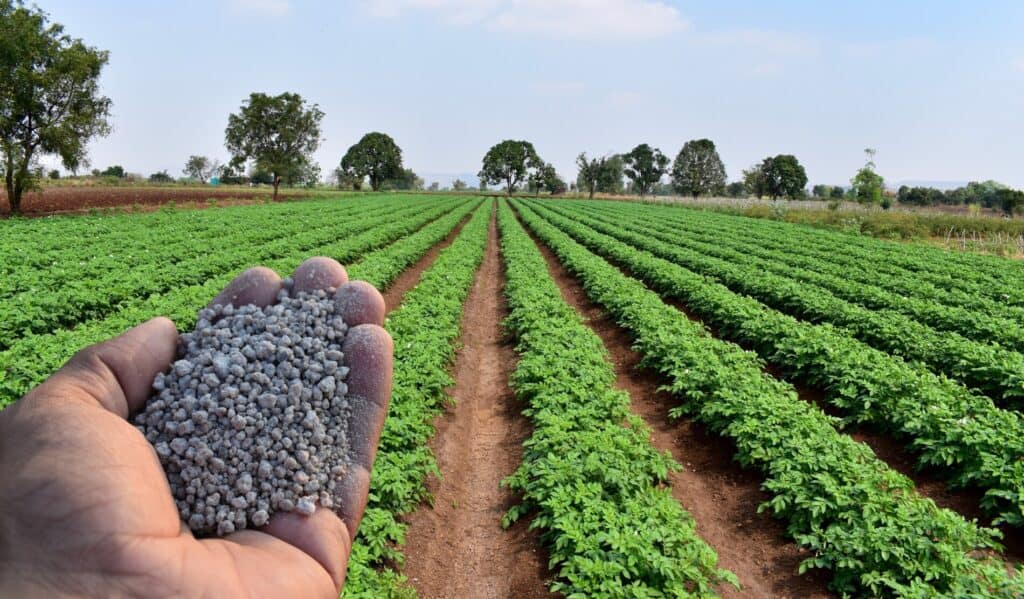
The Role of Sustainability in Fertilizer Processing
Sustainability is driving a fundamental shift in fertilizer processing. Beyond the adoption of green ammonia and by-product recovery systems, manufacturers are exploring alternative raw materials to reduce reliance on finite resources. For example, recycling agricultural and industrial waste into nutrient-rich fertilizers is gaining traction.
Controlled-release fertilizers are another key innovation. These products are coated with biodegradable materials that slowly release nutrients over time, reducing leaching and runoff while maximizing nutrient efficiency. Such advancements align with the global push for precision agriculture, where fertilizers are applied more efficiently to minimize environmental impact and optimize crop yields.
The role of digital tools in sustainability cannot be overstated. IoT-enabled sensors provide real-time data on resource use and emissions, allowing manufacturers to identify inefficiencies and implement corrective measures. These tools are vital for meeting increasingly stringent environmental regulations and achieving sustainability goals.
Conclusion
Fertilizer processing is a cornerstone of modern agriculture, enabling the production of high-quality nutrients that sustain global food systems. While granulated fertilizers dominate the industry due to their superior handling and application properties, the processes involved in their production are both complex and demanding.
Innovations in granulation, digital monitoring, and sustainability are transforming the industry, ensuring greater efficiency and reduced environmental impact. At the same time, stringent safety measures are essential to manage the risks associated with chemical reactions and material handling.
Despite the challenges of raw material variability, energy consumption, and environmental sustainability, the future of fertilizer processing is bright. With continued investment in technology, safety, and green initiatives, the industry is well-positioned to meet the demands of a growing population while minimizing its environmental footprint.
Find fertilizer processing equipment: https://bulkinside.com/equipment-guide/