This is only true to a limited extent and in some cases is misleading for two reasons. Fist, the oft-quoted ‘First in; First out’ flow pattern does not apply to the material held in the converging section of a mass flow hopper because of the cross-sectional velocity gradient when discharging. The material in the center exists swifter than that at the sides, so discharging the peripheral material later than material held in the center. As segregation from a single point fill is usually radial, this means that as the bin initially discharges and finally empties there will be an imbalance of segregated fraction.
The second reason for the fallacy is that when ‘First in; First out’ does apply, it reproduces the selective segregation of lateral segregation, as may be generated in the material in a fluidized fluid condition. Combined with the above phenomena and operational variations in filling and emptying partially full bins, the consequences can be quite complex.
To address the situation, it is necessary to understand the form of segregation that is taking place. (1). Usually, this can be demonstrated by a simple ‘poured repose’ test by forming a small pile within a transparent vessel or between two closely-spaced plates and comparing samples from the top periphery and material in the top center of the pile. Alternately, if no pile is formed, samples from the surface and lower regions should be compared.
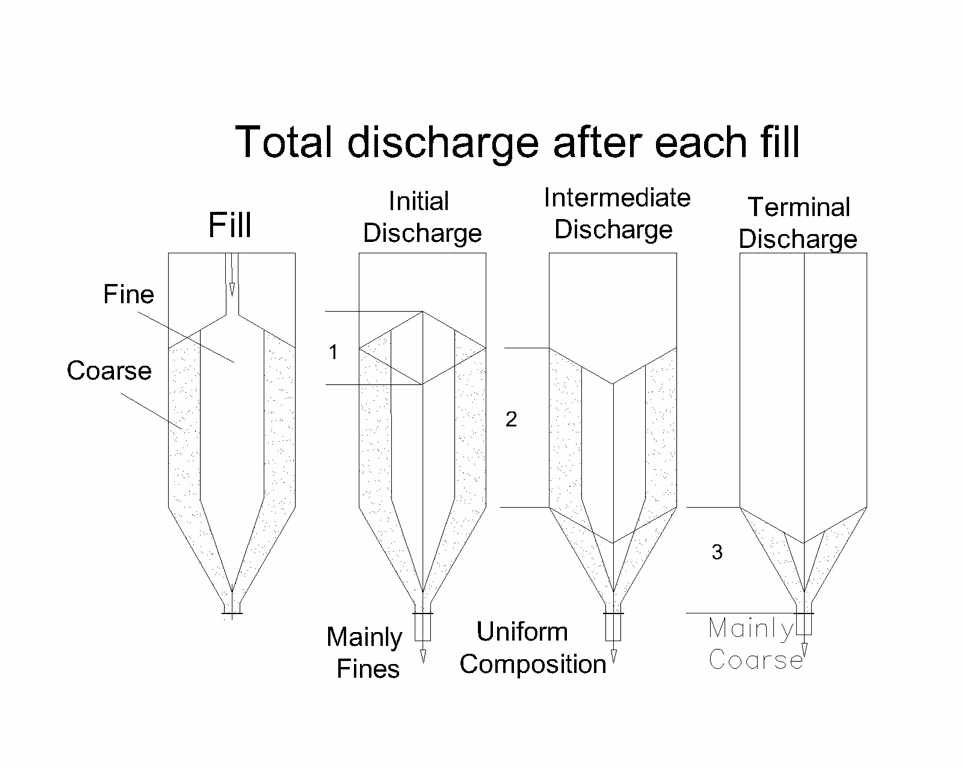
A ‘bullet’ type hopper insert, (2), can be used to reduce the effects of racial segregation in a mass flow hopper. This takes the form of an inverted cone supported on ribs from the converging hopper wall to form an annular flow channel that extracts an equal amount from the center and peripheral regions. The slope of the conical surface can be 150 less than that required for a mass flow converging surface. The diameter of the insert rim to be 0.707.D – 0.55.Wc where D = the hopper diameter and Wc = the critical arching diameter of a circular hopper outlet.
Lateral segregation is more difficult to correct, except for repetitive fixed batches. If the hopper is to receive consistent amounts then compensation for lateral segregation can be arranged by installing a central cylinder stretching from below the inlet to above the outlet, which will hold half of the incoming volume. When this cylinder fills, the overflow spills into the outer region of the hopper. The discharge then draws equally from the inner and the outer regions, to remix on discharge. Some ‘tuning’ may be needed for optimum results so adjustment facilities are useful.
The only way to compensate for irregular segregation due to filling and emptying variations or product differences is to install a ‘tributary’ form of collection from the contents of the hopper so that the discharge is a mix from many locations. This requires specialized design appropriate to the geometry of the installation and is best left to specialists.