Pneumatic conveying lines transfer materials between bulk handling trucks, eight silos, and batch-weighing and blending operations. Six of the silos hold cement, limestone, and plaster. “Those materials are not very abrasive…they’re like flour,” says Mike Deppa, senior project engineer. The other two silos hold sand. “Sand products are our biggest challenge. Moving at 60 mph (95.5 km/h) through the pipe, it just wears them out.”
To distribute the internal wear and prolong the service life of each sand line, horizontal straight sections are rotated 90 degrees every two weeks. “By the time we replace them, they’re like a tin can,” Deppa says. “We try to get every bit out of them ― they’re expensive.”
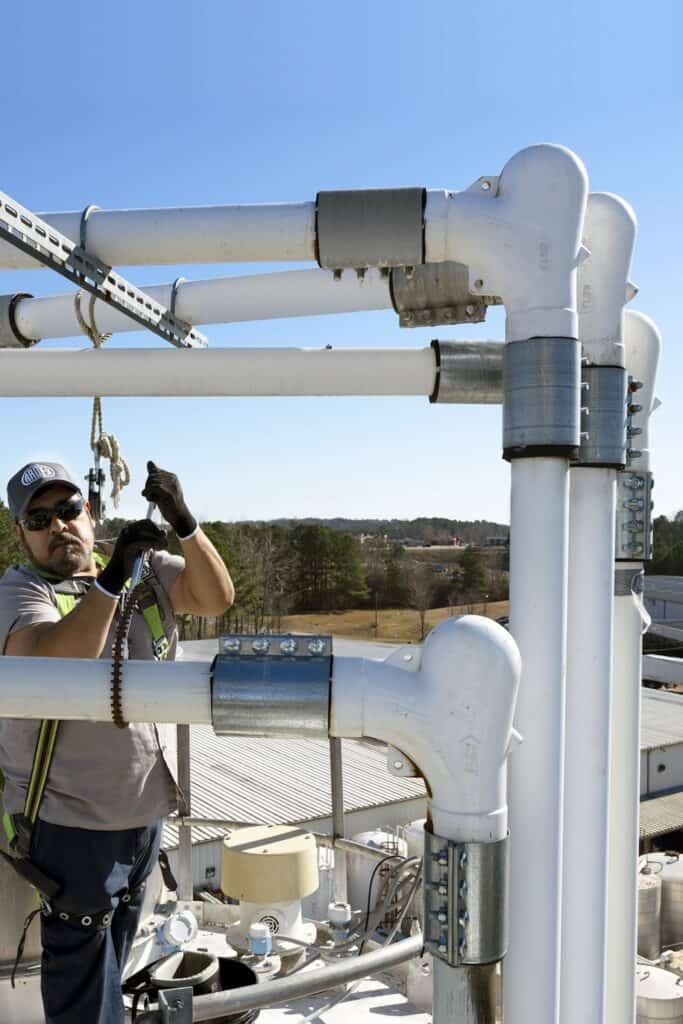
Wear presents more problems at the elbows, where the pipelines change direction. “With elbows, there’s not much we can do as far as preventive maintenance. We usually just keep running until a hole develops.”
Replacement deflection elbow lasts 12 to 24 times longer
Operating in dilute and dense phase, the pneumatic conveying system from each silo’s discharge originally included a European cast iron deflection elbow and a sweep elbow made of plastic with a rubber insert. While the elbows worked well in many areas, they didn’t last long when sand was involved. “The sand eats through the rubber hoses like crazy,” Deppa says. “The cast iron ones would last maybe a month in some cases.”
To extend elbow service life at the high-wear areas of the pipelines handling sand, Deppa installed Smart Elbow® deflection elbows from HammerTek Corp.
They feature a spherical vortex chamber protruding from the inlet leg. As material enters, a portion of it is diverted into the vortex chamber where it forms a loosely packed mass that slowly rotates in the direction of flow and deflects incoming particles around the bend. Because some sand particles continuously leave the chamber as new particles enter, the rotating ball of material is continuously replenished, and self-evacuating at the conclusion of a cycle.
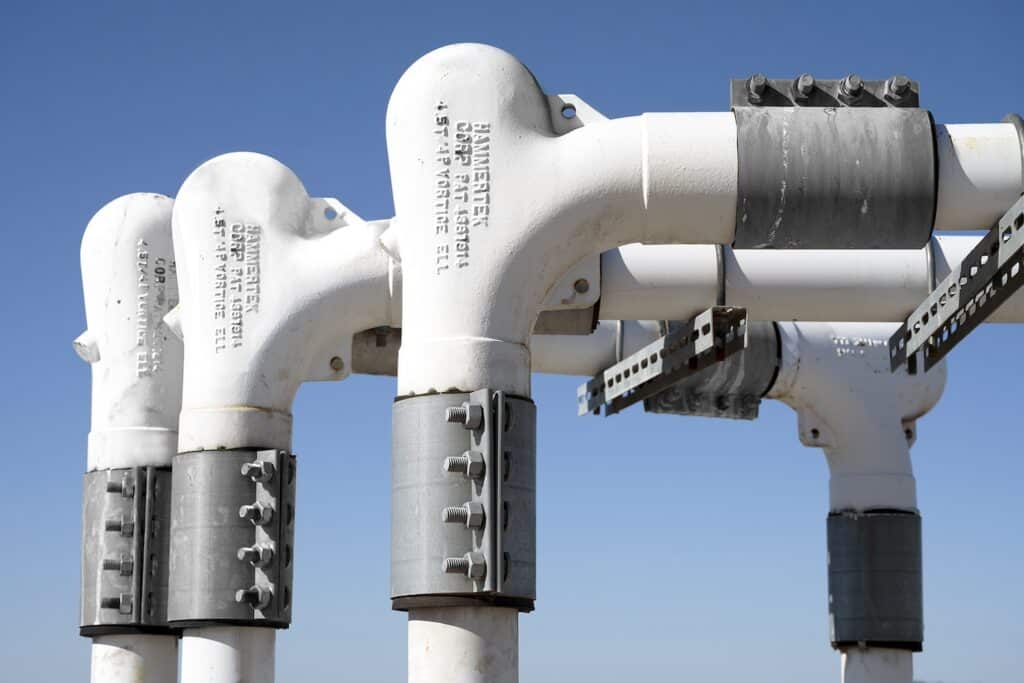
“The HammerTek deflection elbows make a big difference,” Deppa says. “Everywhere we’ve used them, it’s been far superior.” At one particularly difficult location where an original deflection elbow lasted a month, the Smart Elbow replacement has lasted a year. “Others have been running for a couple years without any issue,” he adds.
Comparing costs of elbow-related repairs and system downtime
The Smart Elbow bends cost more than the rubber hose elbows, but the longer service they provide justifies the price, Deppa says. “On our main line, we would wear through a rubber hose elbow in three months. We installed the HammerTek elbow and haven’t changed it yet in four years.” That has eliminated many blowouts and a source of unscheduled downtime.
“We went with the HammerTek elbows because our silos were manufactured with them on the fill side,” Deppa says. “It was a brand that we had seen installed and knew it worked.”
The first Smart Elbow bends Ardex installed were made of basic cast iron. The company has since switched to elbows made with HammerTek’s HammerLoy™, a more abrasion-resistant alloy. “We had good results with the cast iron elbow, but we’re even happier with the HammerLoy ones. It’s like a night-and-day difference.”

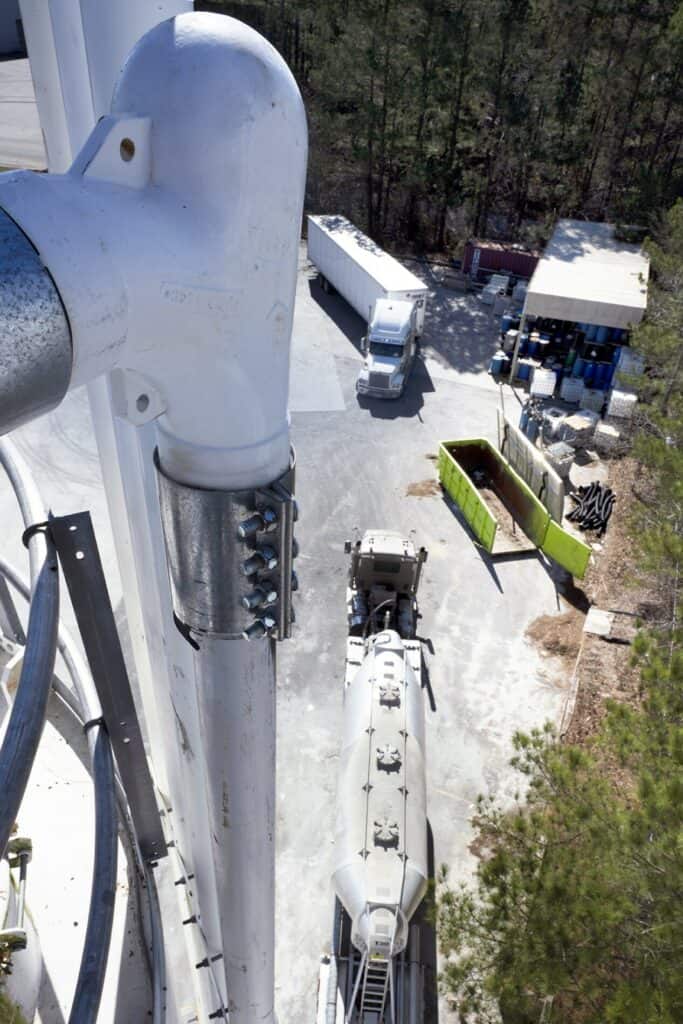