From Granules to Powders: Tackling Segregation in Industrial Processes
Segregation remains a persistent issue in powder technology, often manifesting during transport, storage, or mixing. One of the primary drivers of segregation is the variation in physical properties, such as particle size and density. For example, smaller particles may settle at the bottom of a container, while larger particles rise to the top—a phenomenon commonly referred to as the Brazil Nut Effect.
Additionally, differences in flowability can result in rolling segregation, where smoother particles travel further on inclined surfaces compared to their rougher counterparts. These phenomena highlight the complexity of achieving consistent powder mixtures.
To mitigate segregation, engineers often turn to environmental and design controls. Managing factors like vibration, airflows, and humidity during storage and transport can reduce particle movement. Specialized equipment, such as flow equalizers and anti-segregation devices, can further help control trajectory and minimize stratification. Equipment geometry also plays a role, with optimized hoppers and chutes reducing separation tendencies during discharge.
Particle Size Reduction: The Science of Milling
Effective powder processing begins with controlling particle size. Achieving finer particles through milling processes increases surface area, improves dissolution rates, and enhances reactivity. Milling methods such as hammer, ball, jet, and cryogenic milling are widely employed, each offering unique benefits and limitations.
Jet milling is particularly notable for its ability to process heat-sensitive materials without generating significant heat. By using high-velocity air streams to cause particle collisions, it achieves particle sizes within the sub-micron range. This method, while energy-intensive, is ideal for applications requiring narrow particle size distributions, such as in pharmaceuticals and polymers.
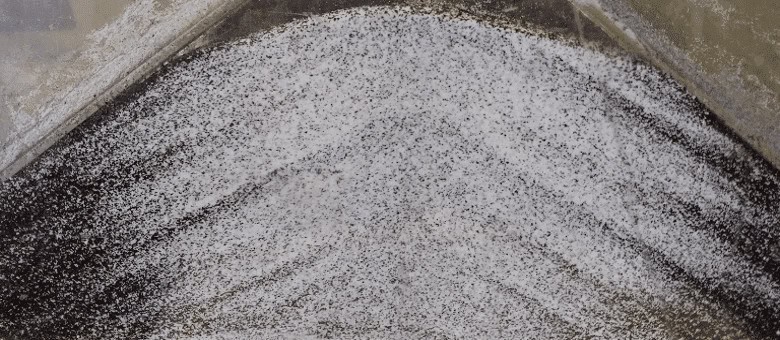
On the other hand, cryogenic milling addresses the issue of heat sensitivity by cooling materials with liquid nitrogen prior to grinding. This prevents thermal degradation and makes brittle materials like elastomers and thermoplastics easier to grind. Although cryogenic milling is costly and requires specialized handling, its benefits often outweigh its challenges, especially for niche applications.
Hammer and ball milling, in contrast, are more traditional approaches. Hammer milling involves high-speed rotating hammers that break materials into smaller fragments. While effective, it often generates heat and dust, making it less suitable for materials sensitive to thermal damage. Ball milling, which relies on rotating drums and grinding media, can achieve finer particles but is similarly limited by heat generation and longer processing times.
Granulation: Enhancing Powder Properties Through Enlargement
Granulation offers a complementary approach to milling by transforming fine powders into larger, cohesive granules. This process is essential for improving flow properties, reducing dust emissions, and enhancing material handling. Granules also exhibit better stability, making them suitable for transport and storage.
Wet granulation remains a popular method, particularly in the pharmaceutical industry. By using liquid binders, this technique ensures uniformity and compressibility, facilitating downstream processing. However, the energy-intensive drying stage poses challenges, especially for heat-sensitive materials. Conversely, dry granulation eliminates the need for liquids, compacting powders into briquettes or ribbons. While energy-efficient, this method may result in less uniform granules compared to wet granulation.
Fluidized bed granulation represents a more advanced technique, offering superior control over granule size and distribution. Particles are suspended in an upward airflow while a binder solution is sprayed, facilitating simultaneous granulation and drying. This precision makes it ideal for applications requiring high consistency and quality.
Analytical Techniques for Powder Behavior and Segregation Control
Understanding powder behavior is pivotal for mitigating segregation and ensuring uniformity. Advanced analytical tools provide insights into particle interactions and distribution, enabling engineers to optimize processes.
Other interesting articles:
Mastering Powder Flow and Compaction for Industrial Applications
Exploring Viscosity in Powder Handling Technology
Viscosity Dynamics in Powder Technology: A Guide for Process Engineers
Characteristics and Significance of Nano-Dust: Insights for Powder Processing Professionals
Powder Compaction: Advancing Precision in Industrial Engineering
Powder Particle Engineering: Revolutionizing Material Design and Manufacturing
Near-infrared (NIR) spectroscopy offers non-destructive, real-time analysis of chemical composition, making it invaluable for blending active pharmaceutical ingredients (APIs) with excipients. X-ray tomography complements this by producing three-dimensional images of particle distribution, aiding in the assessment of granule packing and porosity. Laser diffraction, another critical technique, measures particle size distribution, helping identify segregation risks and refine processing conditions.
Discrete element modeling (DEM) has emerged as a powerful simulation tool, predicting particle behavior under varying conditions such as mixing, conveying, and storage. By visualizing how particles move and interact, DEM helps engineers design equipment and processes that minimize segregation. Statistical sampling methods further validate mixture homogeneity, ensuring consistent product quality.
Real-World Applications: Industry Insights
Effective particle size control and segregation management are vital across diverse industries. In pharmaceuticals, maintaining uniform API distribution ensures accurate dosing and therapeutic efficacy. Food processing benefits from consistent flavor and texture, achieved through controlled granulation and blending. Additive manufacturing, metallurgy, and construction also rely on homogeneous mixtures for structural integrity and material performance.
Energy storage is another field where particle uniformity is crucial. Consistent particle size distribution in battery materials ensures reliable performance and longevity, highlighting the cross-industry importance of advanced powder processing techniques.
Sustainability and Future Trends
As industries prioritize sustainability, energy-efficient equipment and eco-friendly practices are becoming integral to powder processing. Jet and cryogenic milling, while effective, face scrutiny due to their high energy demands. Innovations in equipment design and process optimization aim to reduce these environmental impacts. Furthermore, the integration of real-time monitoring systems and AI-driven analytics is set to revolutionize the field, enabling smarter, more sustainable manufacturing processes.
Conclusion
The science of powder processing underscores the importance of particle size control and segregation management in modern manufacturing. By leveraging advanced milling and granulation techniques, coupled with cutting-edge analytical tools, industries can overcome challenges and achieve consistent, high-quality products. As technology evolves, the focus on sustainability and precision will continue to drive innovation, ensuring powder processing remains a cornerstone of industrial success.