The storage of these products in silos forms no exception to this practice. Many silos are constructed out of concrete or mild steel. These materials are known to release impurities over time, especially with highly abrasive product and/or high transportation speeds. For this reason, a food-grade approved coating is often applied to manage this contamination risk.
However, this practice causes additional risks regarding explosion safety. These are discussed here, together with possible preventive or protective measures.
Propagating brush discharges
The main issue regarding the application of a coating, is the phenomenon of a propagating brush discharge. This type of discharge is created when a relatively thin layer of non-conductive material is applied onto a grounded conductor. When this thin layer gets charged to a sufficiently high level, an electrical breakdown will take place from the surface of this coating towards the earthed conductor, in order to release this high charge. The resulting propagating brush discharge has an energy content as high as 1000 mJ or even more, and is therefore capable to ignite most dusts clouds with a concentration above their lower explosion limit (LEL). For this reason, flexible hoses with metal reinforcement are already widely known to form a potential ignition source when not made out of so-called antistatic material. But does this also apply for silos, since the product speed is much lower, and the degree of charging is obviously much less?
IEC/TS 60079-32-1:2013+A1:2017
This current technical standard regarding equipment, product and process properties necessary to avoid electrostatic discharges, specifically warns for this practice (application of a non-conductive coating) in all type of “conductive, earthed containers”. This therefore includes metal silos. It states that such coating can give rise to propagating brush discharges, and should therefore be avoided.
The underlying thought is as follows: when material is discharged in the silo, there is charge compression taking place in the bulk material. This may generate a high electrostatic field, which is also the origin of cone discharges.
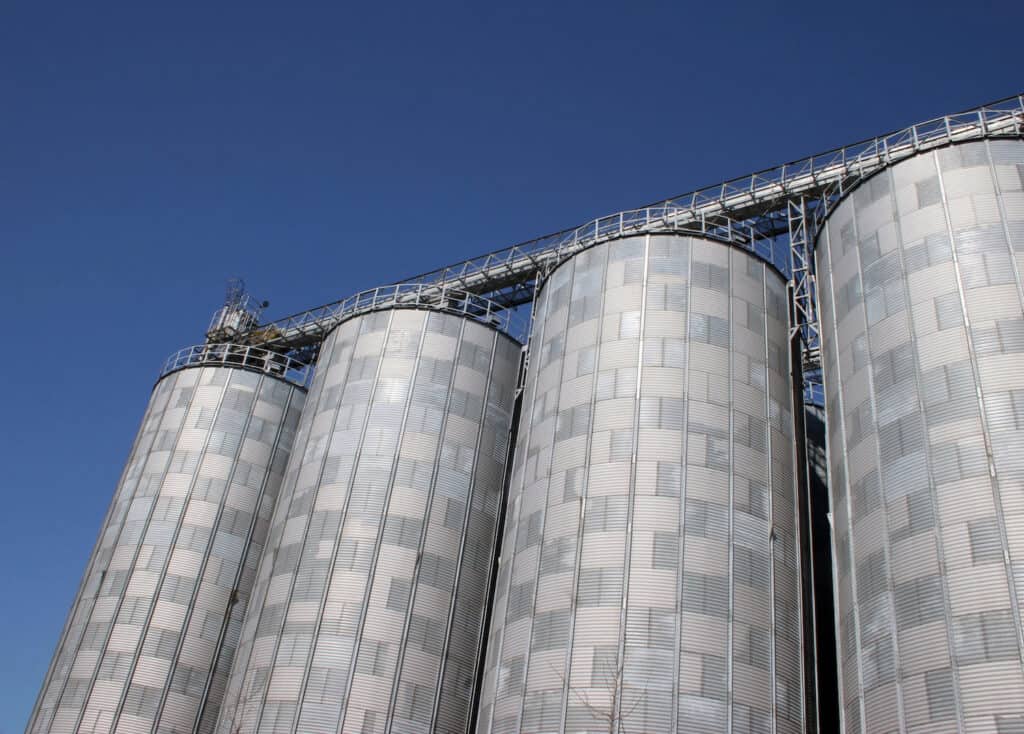
However, before these cone discharges arise, other small discharges (corona and brush discharges) begin to arise on the charged bulk. These discharges are known to contain insufficient energy to ignite a dust cloud, but the corresponding counter-charges are directed along the electric field lines to the earthed silo outer wall, and form a high surface charge density on the insulating coating. This might finally lead to a propagating brush discharge. Therefore, internal coating of a metal silo with a non-conductive coating, should always be carried out with great caution.
How to manage this risk?
IEC/TS 60079-32-1:2013 does provide guidance on how to safely exclude this specific risk in case the coating is unavoidable.
One option is to apply a very thick layer of coating, such that no electric breakdown can take place. The IEC/TS mentions a layer thickness of 10 mm. However, set aside the technical difficulties to apply a uniform coating of this thickness, there is no guarantee that this layer will not reduce in time due to wear. Therefore, this approach is less favourable.
Another approach is to prove that this coating material can only charge to such a degree, that the resulting discharge does not give rise to (a highly energetic) propagating brush discharge. This depends on a specific product property, called the dielectric strength (kV/mm), and the resulting breakdown voltage (kV). When the breakdown voltage is proven to be less then 4 kV, propagating brush discharges can be excluded. Guidance on how to measure this breakdown voltage, can be found in EN 60243-1. The same approach (limiting break-down voltage) is also applied with FIBC’s (bigbags) type B, to exclude the propagating brush discharges.
A final resort can be found in the ATEX directives. When an ignition source can not be excluded with sufficient certainty, and dust clouds may be present, measures must be taken to control the consequences of an explosion. Therefore, it is a good practice to equip silos with explosion venting. Due to the potentially disastrous effects of a silo explosion, the protection of a silo is a good practice for storing combustible products or products that form a dust explosion hazard anyway.
Special thanks
The author wishes to thank Dr. Martin Glor for sharing his in-depth knowledge regarding this matter.
About ISMA
ISMA specializes in process explosion safety consulting. Activities include risk assessment of dust and gas explosive atmospheres, predicting explosion effects and post-incident analysis in a wide variety of industries. ISMA also shares its expertise in various expert groups.
Over 5000 installations in various industries have been assessed by ISMA since the start of its activities in 1984.