How do electrostatic charges develop?
Electrostatic charges and the associated discharges are considered as one of the 13 possible ignition source types to be considered in a plant-related risk assessment. A distinction is made between the most varied types of discharge which, depending on the type, can be responsible for igniting gases or dusts (Table 1).
Electrostatic discharges and their ignition potential
Energy Ascending | Discharge type | Hydrogen / Acetylene MIE ≤ 0.025 mJ | Solvent vapours MIE > 0.025 mJ | Dust > 1 mJ MIE > 1mJ |
+++ | Propagating brush discharges | + | + | + |
+++ | Conical pile discharge | + | + | + |
++ | Sparks | + | + | + |
+ | Brush discharge | + | + | – |
Fig. 1: Electrostatic discharges and their ignition potential. Source: www.bgrci.de
Selection of the suitable Big Bag
Big Bags, also referred to as FIBC´s, are divided into the types A, B, C, D, which can be categorized according to their protective characteristics as follows:
Avoid brush discharges: Type C and D
Avoid propagating brush discharges: Type B, C and D
Avoid spark discharges: Type B, C and D
Type C Big Bag has conductive filaments, which makes it necessary to ground type C Big Bag. Such grounding can be carried out by means of a cable and clamp. Another option is the grounding by means of a grounding monitoring system such as FARADO II FIBC. An approval function enables the Big Bag Type C to only be filled if the grounding is correctly established.
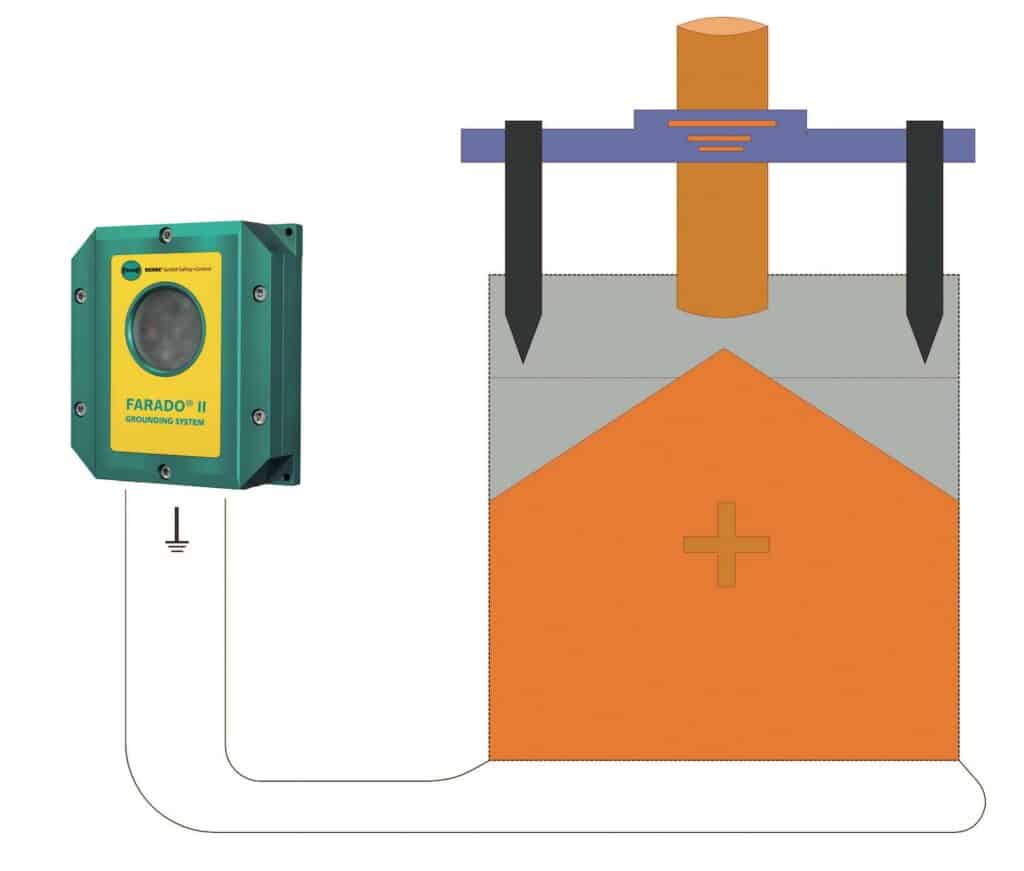
Type D FIBC transfers the resulting charges to the environment via dissipation. However, this requires grounding of all conductive equipment and objects located within reach of the type D Big Bag. Likewise, persons must wear conductive footwear, otherwise these persons will be charged up as well and act as an ignition source themselves.
The Big Bag must be selected strictly in accordance with the requirements of IEC TS 60079-32-1 “Explosive Atmospheres – Electrostatic hazards, Guidance”, and depends on the minimum ignition energy (MIE) and the zone classification. However, the division also depends on the zone defined on the outside. If a gas zone is present at the same time, special measures must be considered.
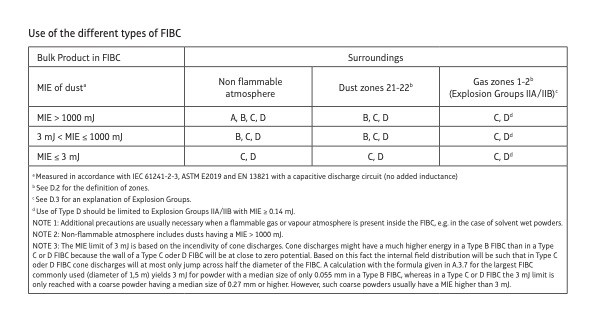
Electrostatic charges during the filling of silos with a pneumatic filling
Another source of electrostatic charges is in places where a pneumatic transport or pneumatic filling of silos by trucks is carried out. If an explosive atmosphere develops outside the truck, and the truck charges up electrostatically due to the conveyance, there will be an acute risk of explosion. For this purpose, always ensure that the truck is properly grounded. Here, there are also systems on the market that are able to monitor the proper grounding of the truck and, via relays, provide an approval system that can be used to control valves or other equipment (Figure 2). In addition to grounding the truck, care must also be taken to ensure that the conveying line is properly executed. Adequate means that this must be electrically conductive/conductive dissipating and grounded.
Insulating intermediate pieces such as sight glasses or similar should be avoided, as these may lead to propagating brush discharging.
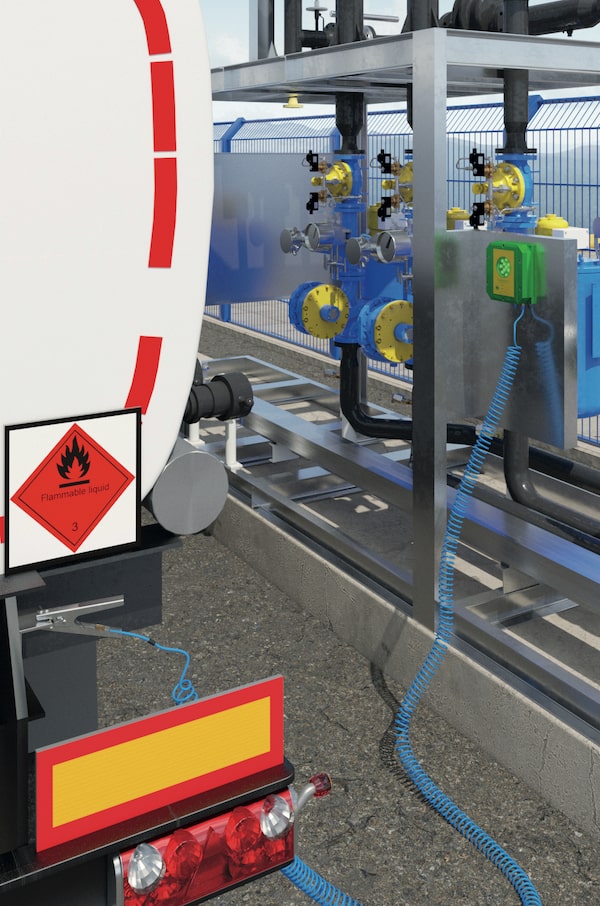
Conical pile discharge in silos
An often not considered circumstance is the possibility of so-called conical pile discharges in silos. Bulk solids are generally not to be regarded as conductive and are dangerously charged during the pneumatic conveying. If the silo is correspondingly large and the median of the bulk material is also larger in median, there is a risk that the cloud of dust above the bulk material will ignite due to a conical pile discharge. If the conical pile discharge cannot be excluded as an effective ignition source, a protection through protective systems must be established in case of doubt. Flameless explosion venting by means of a Q-Box or explosion suppression by means of the Q-Bic offer numerous options for the indoor installation. The protection of adjoining plant components must also be taken into account during the protection design. Thus the supply line must be isolated against the pressure and flame of a possible explosion. This prevents the explosion from striking back, e.g. into the conveying truck or into the Big Bag loading station. In addition, the silo discharge must be equipped with an appropriately certified rotary valve, e.g. Ex II (1) 2 D, to prevent the explosion propagation in this direction.
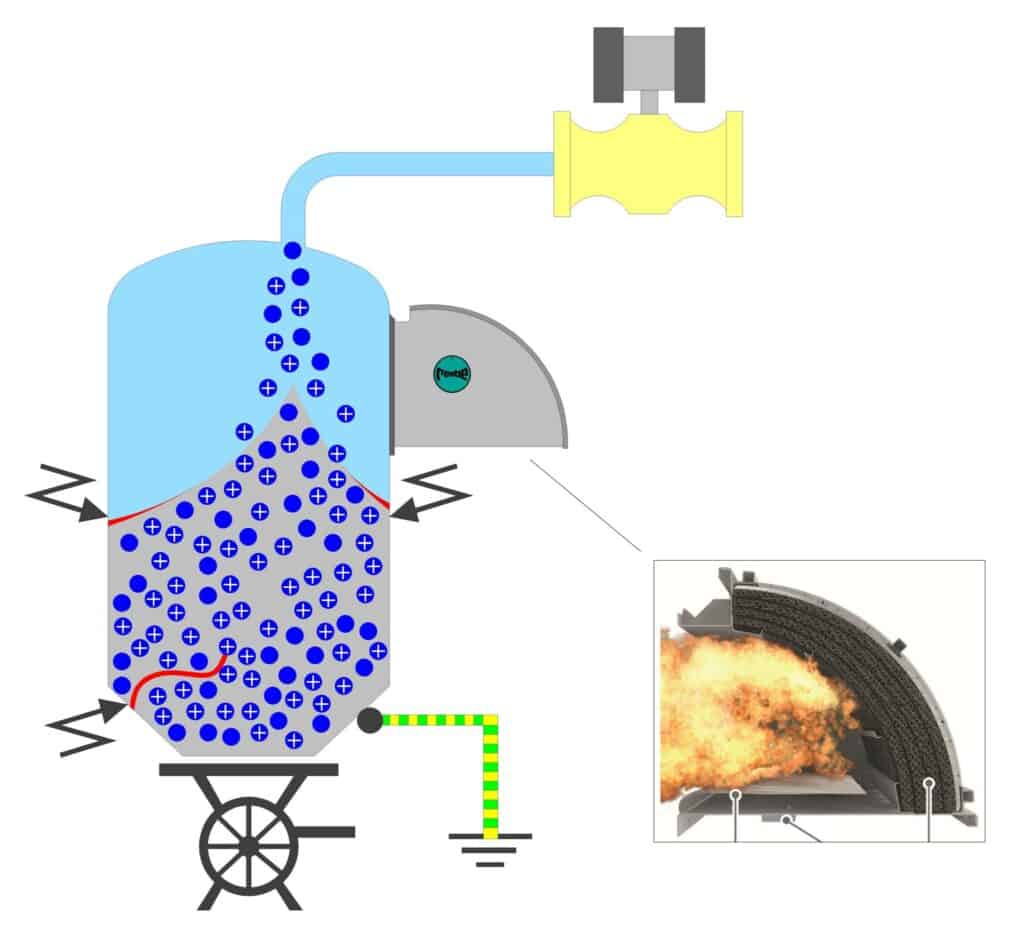