The Angle of Repose Feeder (ARF) is a variable speed feeder that works in harmony with the natural flow of the material being fed, causing minimal degradation at significantly lower energy consumption than other type feeders. The ARF controls the flow of material based on the material’s inherent angle of repose. The feeder works in conjunction with articulate able plates (“gates”) mounted to the bottom of a receiving hopper/ bin. The articulate able plates control the material on the rotating member as the material feeds itself.
The gate is positioned to allow for the maximum product size using the angle of repose of the material as it contacts the rotary member. This, in relationship with the rotary member, sets up the cross-sectional area within the hopper to feed the material without retardant action. The material flow can be completely shut off by stopping the rotary member or by closing/controlling the gate opening manually or automatically. The ARF and Belt scales linked through PLC control can deliver an accurately controlled flow rate for consistent meter feeding regardless of material characteristic change.
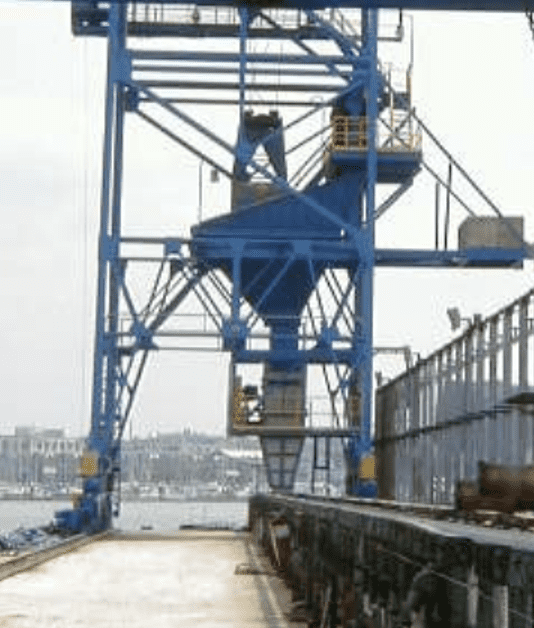
The material characteristics of unprocessed raw sugar change from a free-flowing powder to a non-flowable wet and sticky molasses. The ability to retard the flow of material is easily adjusted by closing down the throat area/opening to reduce the active drum surface. Since the flow control of the material comes from using the inherent angle of repose, bridging and plugging are non-issues. The desired feed rate is determined by the rotational speed, length of the drum, and opening gate height. The positioned gate height from the rotational drum must be at least 2.5 times the maximum lump product size. The ARF units can run either perpendicular or parallel with the collecting belt, allowing for a wide range of possibilities. This maximizes the effective live storage area of the bin.
Applications:
The Angle of Repose Feeder handles a wide range of particulate material with varying flowability and angle of repose characteristics. Materials that bridge, stick or are abrasive are easily managed by the ARF.
Attributes:
The strength of the ARF stems from its simplistic design. A minimal number of moving parts provides flexibility and increased uptime, no product degradation, and significant energy conservation which equates to increased throughput and a lower overall operating cost. The ARF’s reliability and consistency in material flow eliminate material jamming.
There’s a Reason Things are Round:
The ARF uses the natural forces of gravity to feed material onto the rotating member, similar to a water wheel design with no paddles or pockets. The consistent volume is maintained regardless of moisture content and the ARF’s wheel-feeding design eliminates the possibility of conditions that would promote excessive wear.
Flexibility:
The ARF provides the flexibility of operating at a fixed speed with variable gate opening, or at a variable speed with a fixed gate, opening to maintain material flow consistency to adapt to the various material size, moisture content, and flow characteristics. The ARF can be manually or automatically controlled to increase RPM and gate opening to achieve the precise flow rate required.
Comparisons:
Unlike belt feeders, vibratory feeders, or screw feeders, the ARF delivers consistently reliable performance that sets it apart, because the ARF works with the material and the natural forces of gravity.