“Price is what you pay. Cost is what you spend”
The sales price of an item usually has the biggest influence on the purchasing decisions we make. In business it is usually budgetary constraints that come first. However, buying something because it is ‘competitively priced’ but then proves to be unreliable and/or needs replacing after an unacceptably short period can be a very costly mistake.
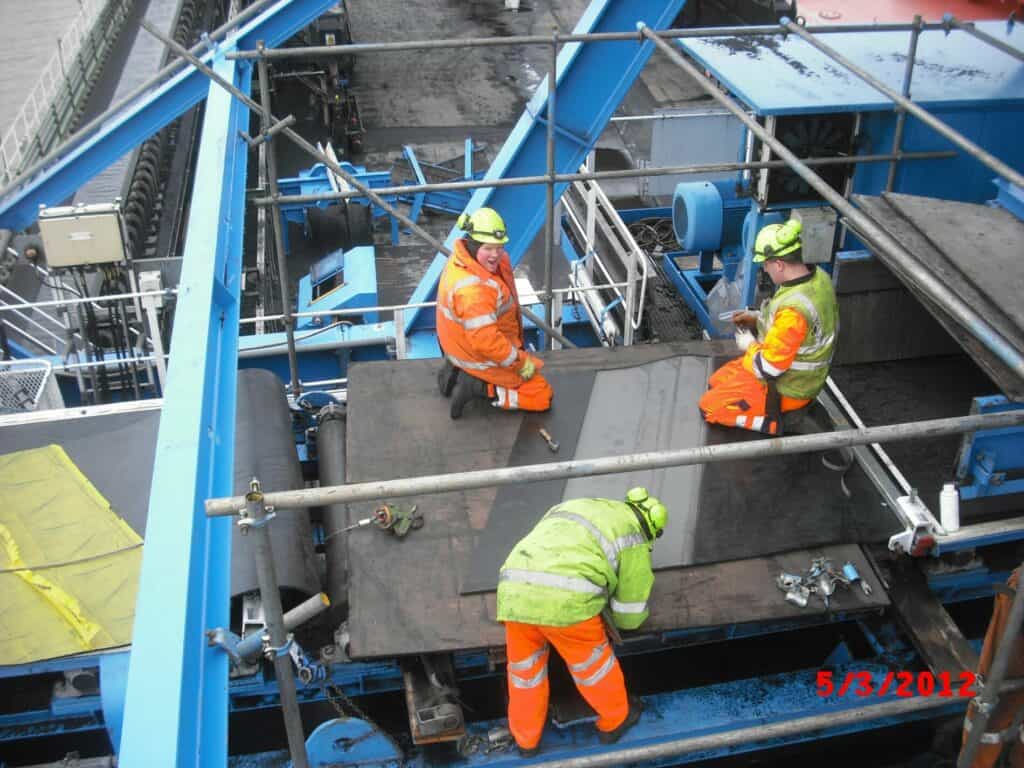
To calculate the true cost to your business when buying a complex and vitally important component such as a conveyer belt, it is necessary to include as many other directly connected costs as possible. The ‘above the line’ price that you pay is one thing but the less obvious ‘below the line’ costs are what your company will actually spend. For example, people who are directly responsible for conveyors will probably know how much has been lost in terms of volume when there is a stoppage. However, the question that needs to be asked is whether or not the cost of that lost output is being measured and recorded and then used to help make buying decisions?
Not all conveyor belts are created equal.
Although they may outwardly look the same, there often huge differences between the performance of one conveyor belt and another, even when they both claim to meet a certain specification and international quality standards. There are numerous, well-documented reasons for these huge differences in performance and longevity but they are not necessarily easy to identify at the buying stage.
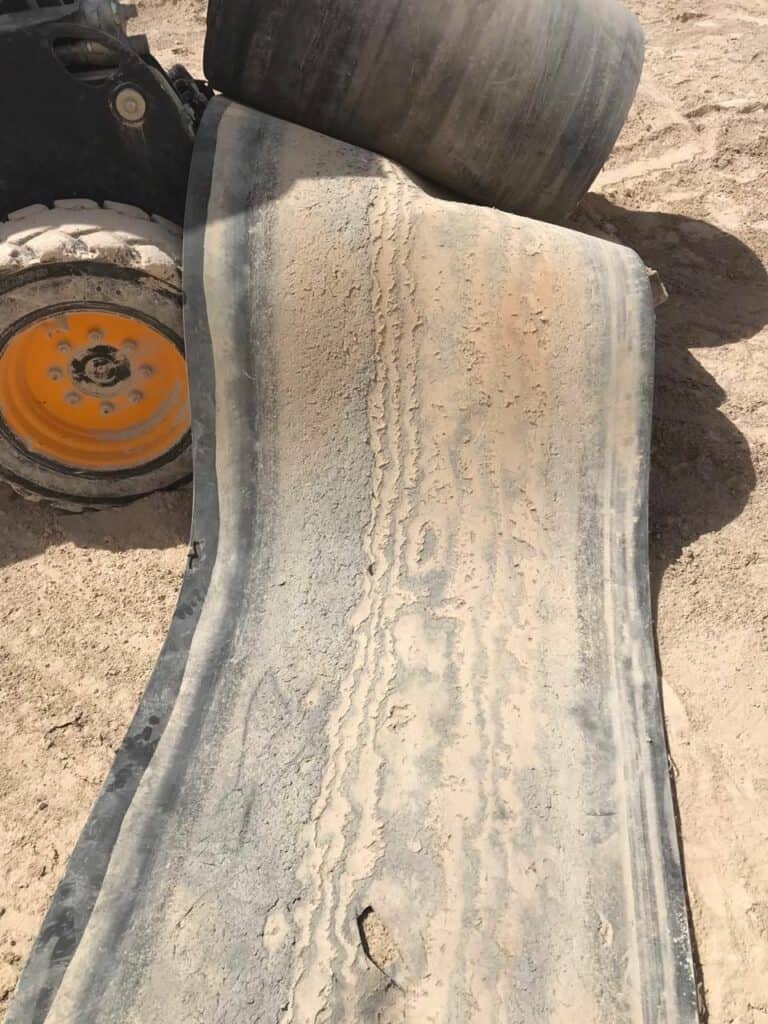
Ironically, one of the best warning signs are the prices being offered. The majority of rubber belting imported into Europe is from China. It is not uncommon to see belts being offered by European traders, suppliers and sourcing companies that have been manufactured in Southeast Asia that are half the price of those being offered by quality-led European manufacturers such as Netherlands-based Dunlop Conveyor Belting and Contitech in Germany.
To make matters worse, unlike the Dunlop’s and Contitech’s of this world, the traders of imported conveyor belts are making huge margins because in reality the difference in manufactured cost is even greater than it first appears. As with virtually any product, price ultimately determines its quality of performance, its need for frequent repairs and the length of its service lifetime. In the case of imported conveyor belts, all the evidence points to top quality European-made belts being able to provide up to four or five times longer operational life compared to their Asian counterparts and requiring considerably fewer repairs during that working life. Their ‘whole life cost’ is therefore appreciably less.
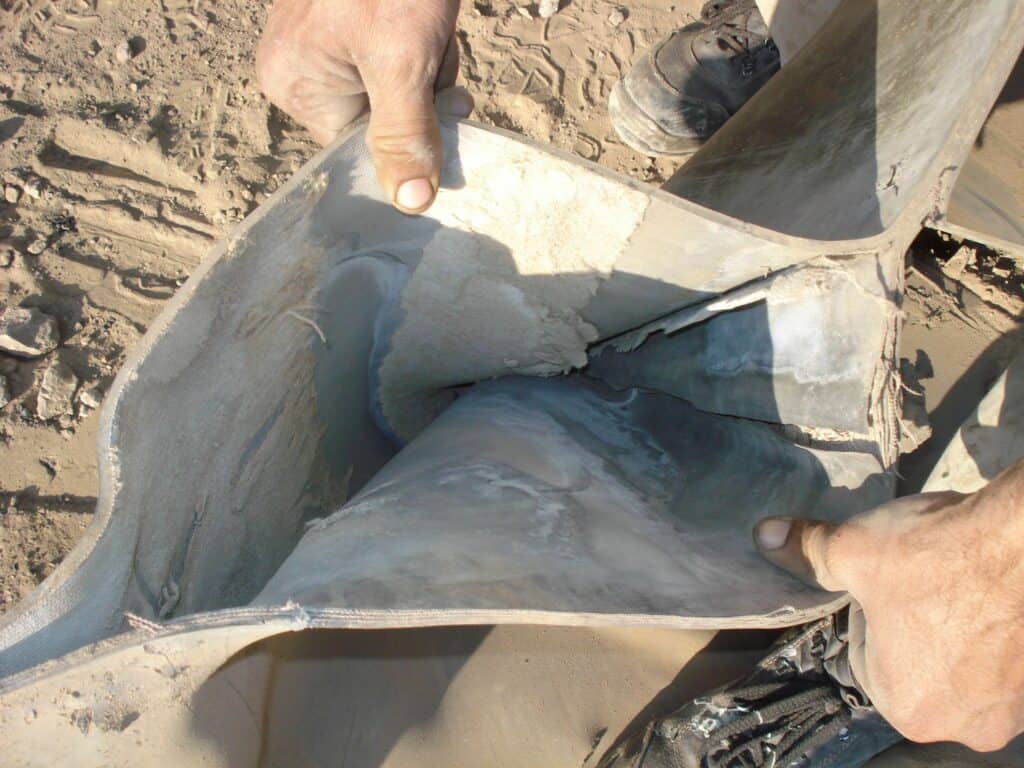
Unfortunately, for those responsible for the day to day running of conveyor systems, it is extremely rare for those who are responsible for purchasing and capital expenditure to understand the technical differences associated with the performance and longevity of a conveyor belt. Consequently, price is the number one buying criteria. To be fair, purchasing professionals cannot be an expert on every product they are required to source. Trying to convince them and the company accountants that you want to use more reliable but ‘higher priced’, premier quality belts can be very difficult. Fortunately, it becomes very much easier if you ‘speak their language’ by presenting an argument based on factual, ‘whole life’ cost calculations.
Calculating ‘whole life’ cost
The principal of ‘whole life cost’ is simply the sum total cost (excluding VAT) of the conveyor belt itself plus the cost of its installation including splicing. Added to that should be the time spent removing and replacing the old belt before normal service can be resumed, which should be included as part of the ‘lost output’ calculations. The final part of the cost calculations are the labour and material costs incurred in repairing the belt (including the splice repairs) during its lifetime plus the estimated costs of the production lost while those running repairs are carried out. These calculations are easier to make if conveyor maintenance and repair is contracted out to a vulcanizing company. However, if these functions are performed ‘in house’ then it is important that accurate maintenance records are kept.
Time or tonnage?
Having added together the various elements of cost, the final step is simply to divide the total. This can either be done by either the period of time that the belt has been operational or, if known, the total weight of material conveyed during its operational life. On conveyors that are usually running non-stop during the day then time is usually the best measure. However, if the conveyor only operates intermittently then using tonnage as the basis for the calculation may prove more accurate. You can, of course, calculate on the basis of both time and tonnage.
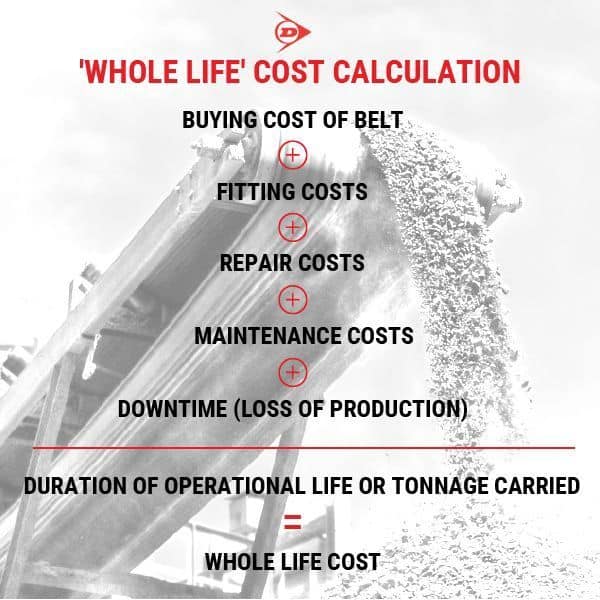
Having calculated the cost of a belt you are using or have finished using, the question then becomes one of comparison. There is little or no point in making the calculation unless you have something to compare it against. This, of course, means trialing a higher grade of belt or a different type of belt entirely, perhaps both.
Predicting the lifespan
The most challenging aspect of selecting conveyor belts based on whole life cost is that it can be difficult to accurately predict the lifespan of a new type of belt or one that is made by a manufacturer that you have never have used before. Understandably, manufacturers of conveyor belts, regardless of their reputation for quality, can never guarantee how long a belt will last before needing to be replaced because there are simply too many influencing factors. Do not let this put you off. There is inevitably some degree of risk in any business decision but if you choose a tried and trusted manufacturer, especially one that is well-known for its quality and which actually manufactures in Europe, then the rewards can be considerable. As the old saying goes, “If you never try something different then you will always get what you already have”.
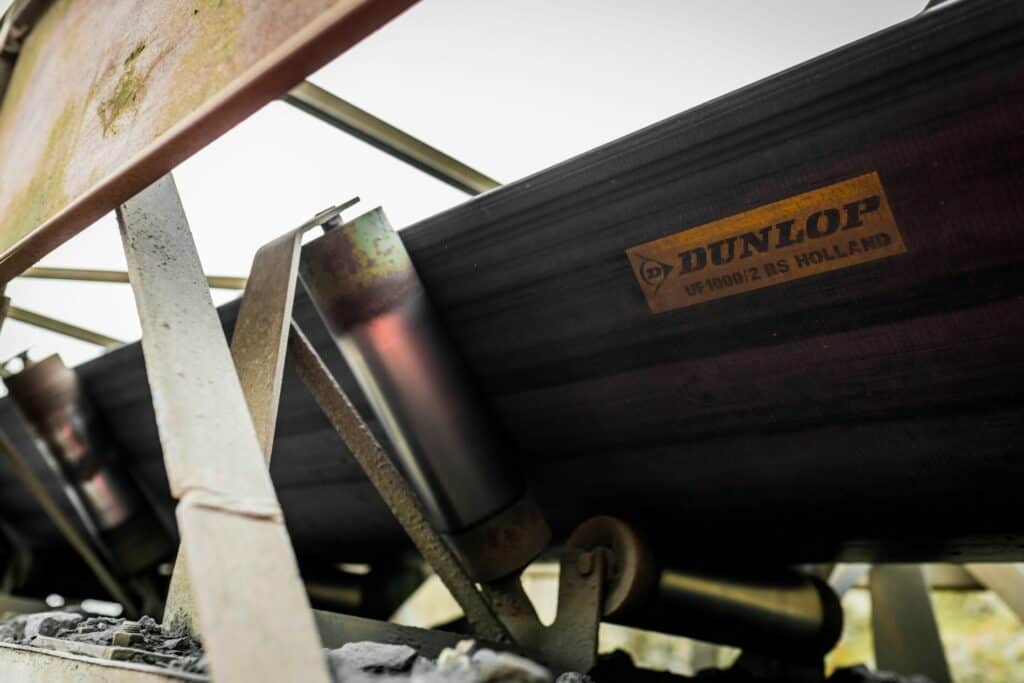
In my experience, the best approach is to select a conveyor that has the highest frequency of belt repairs and replacements. The next step is then to discuss the application and your requirements with an experienced representative or application engineer representing each potential new supplier. If the conveyor you have chosen is particularly problematic then it is often a good idea to make absolutely sure that the specification of the belt is correct for that particular conveyor by using a belt calculation program. If necessary, have the process overseen by a professional conveyor belt engineer.
For conveyors where damage caused by trapped foreign objects can be a problem, the most cost-effective solution is to fit a belt that has been specifically engineered to resist such damage. Specialist belts such as Dunlop UsFlex and Dunlop Ultra X will provide much longer lifetimes because that is exactly what they have been designed to do.
Standing the test of time
Never accept that it is not possible for a belt to last many times longer than is currently being achieved. Thanks to huge technological advances, the cost-effectiveness of modern-day conveyor belts should be measured over several years rather than just a year or two. Worryingly, in bulk handling we are seeing more and more examples of belts that only last a few months and, in some cases, only a matter of weeks before needing to be replaced. It is no coincidence that this decrease in average belt life mirrors the increased use of imported belting.
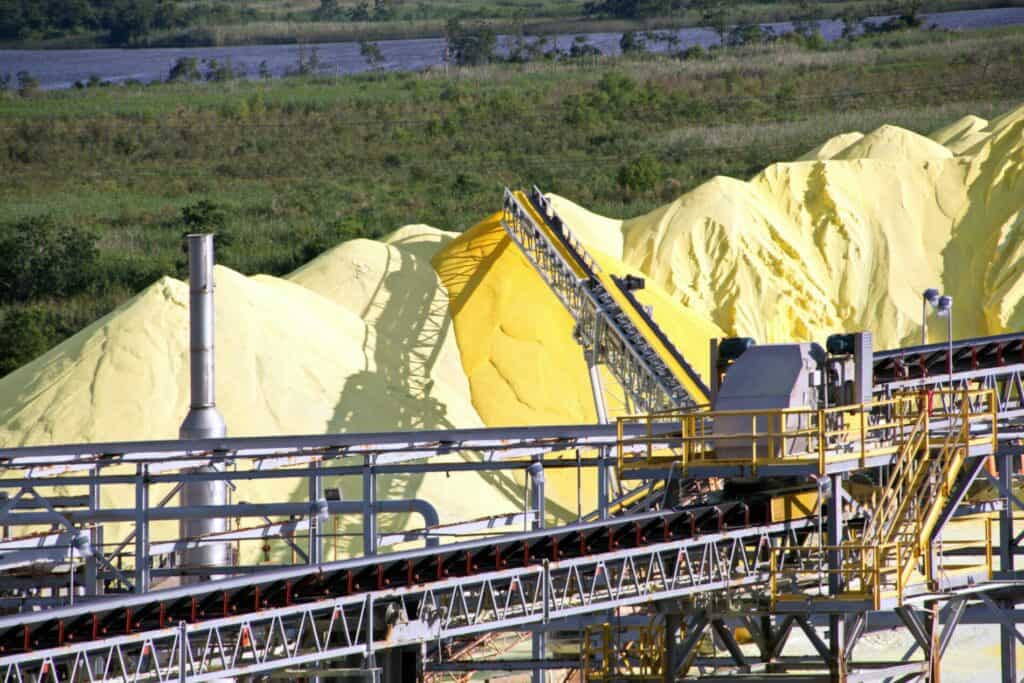
This actually strengthens the case for selecting belts based on ‘whole life’ calculations rather than simply the buying price. Naturally, there will always be a desire to reduce expenditure but conveyor belts that provide a longer operational life will invariably prove much cheaper in the long run.
Leslie David
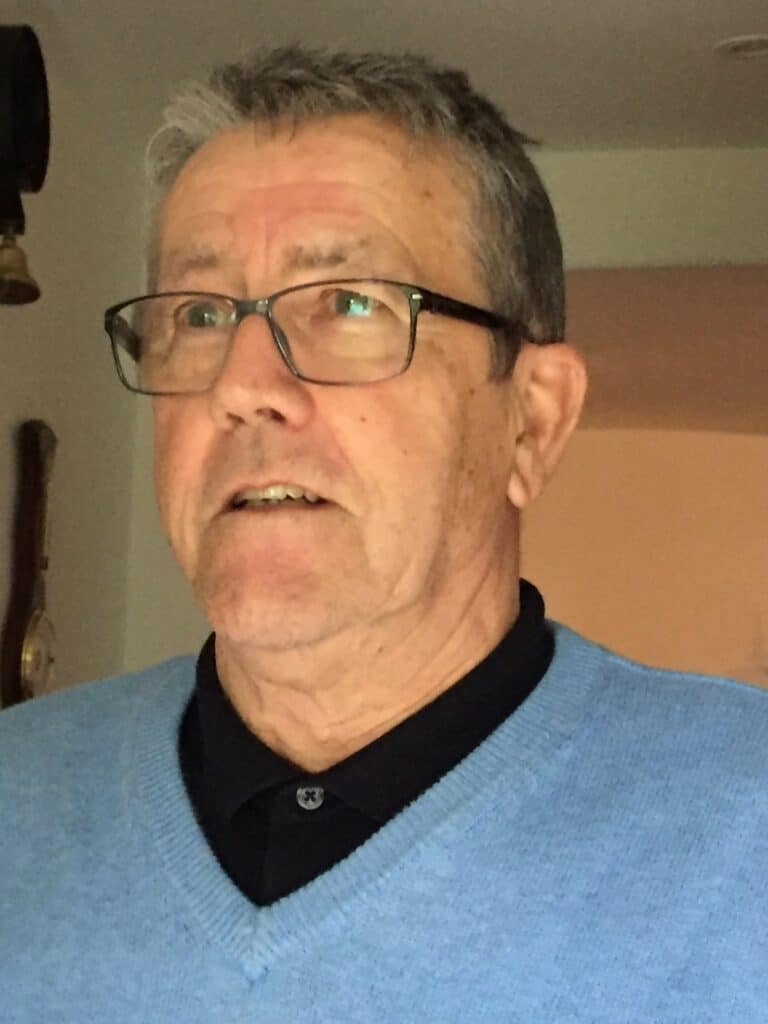
About the author
After spending 23 years in logistics management, Leslie David has specialised in conveyor belting for over 17 years. During that time, he has become one of the most published authors on conveyor belt technology in the world.