The project also included several extraction screws for unloading silos and big-bags, and conveyor screws for transport with throughputs ranging from 9 to 36 tons per hour. Some of these screw conveyors would be mounted under inclinations of up to 35º. The design of the screws therefore had to take into account the function of each conveyor. The pitch, power and speed of the drives were calculated specifically for each screw.
Since the sugar was very fine, a mechanical air sealing system was chosen to close and seal the conveyors. In addition, hygienic production criteria were considered in the design to reduce or eliminate the risk of the screw conveyor being a source of contamination for this product, both directly and indirectly. This was achieved through a design that facilitates cleaning, inspection and maintenance and avoids the generation of dirt.
All materials in contact with the sugar must be stable and inert according to FDA requirements while complying with the ATEX protocol that we manage at LOMS. The equipment was manufactured in stainless steel INOX 304L.
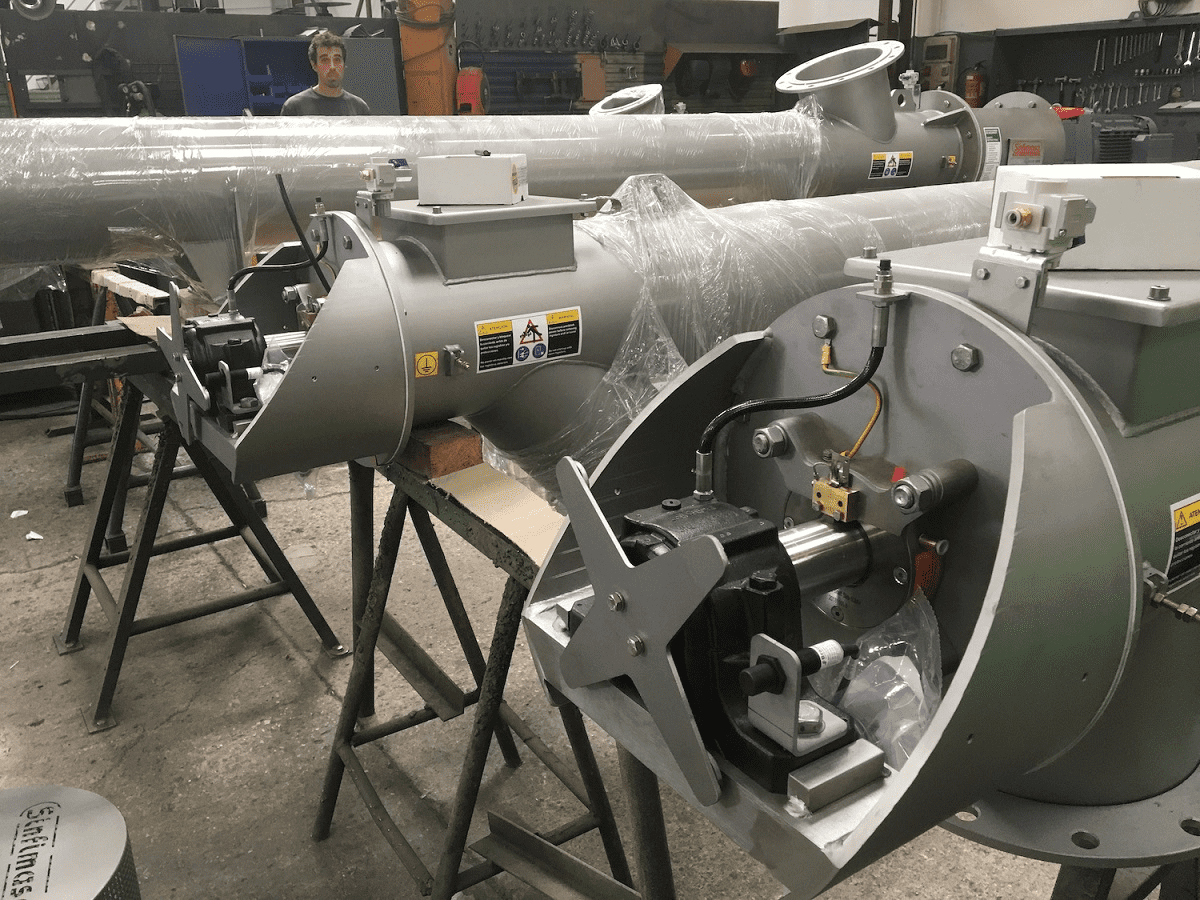
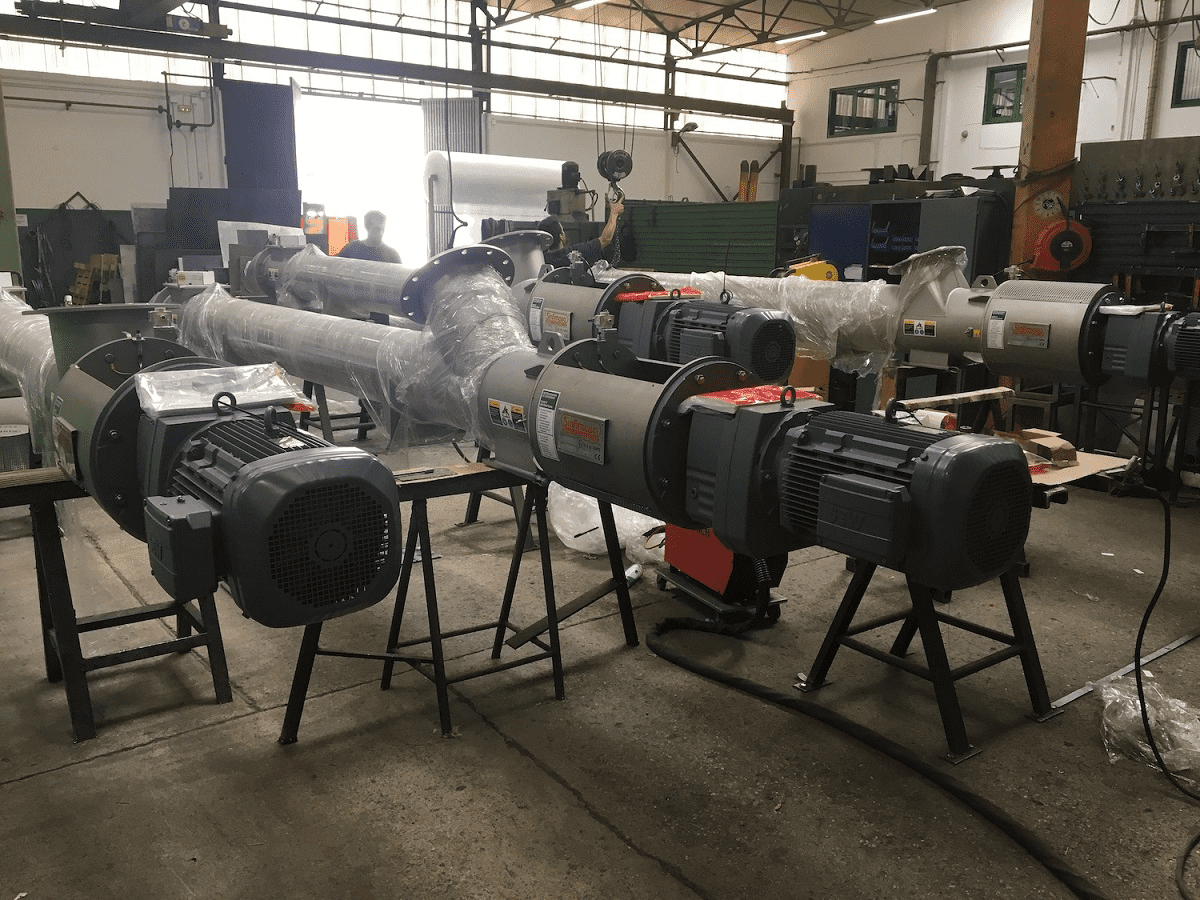
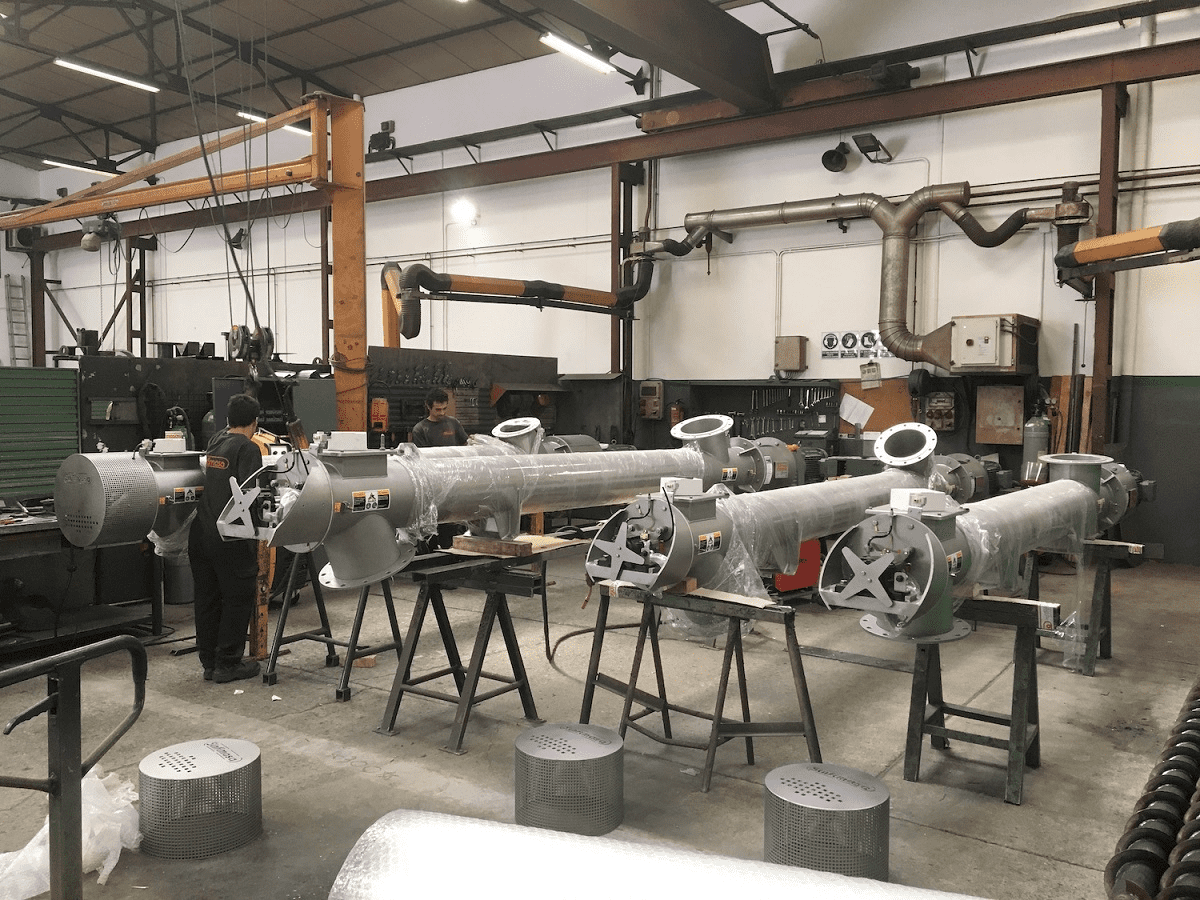
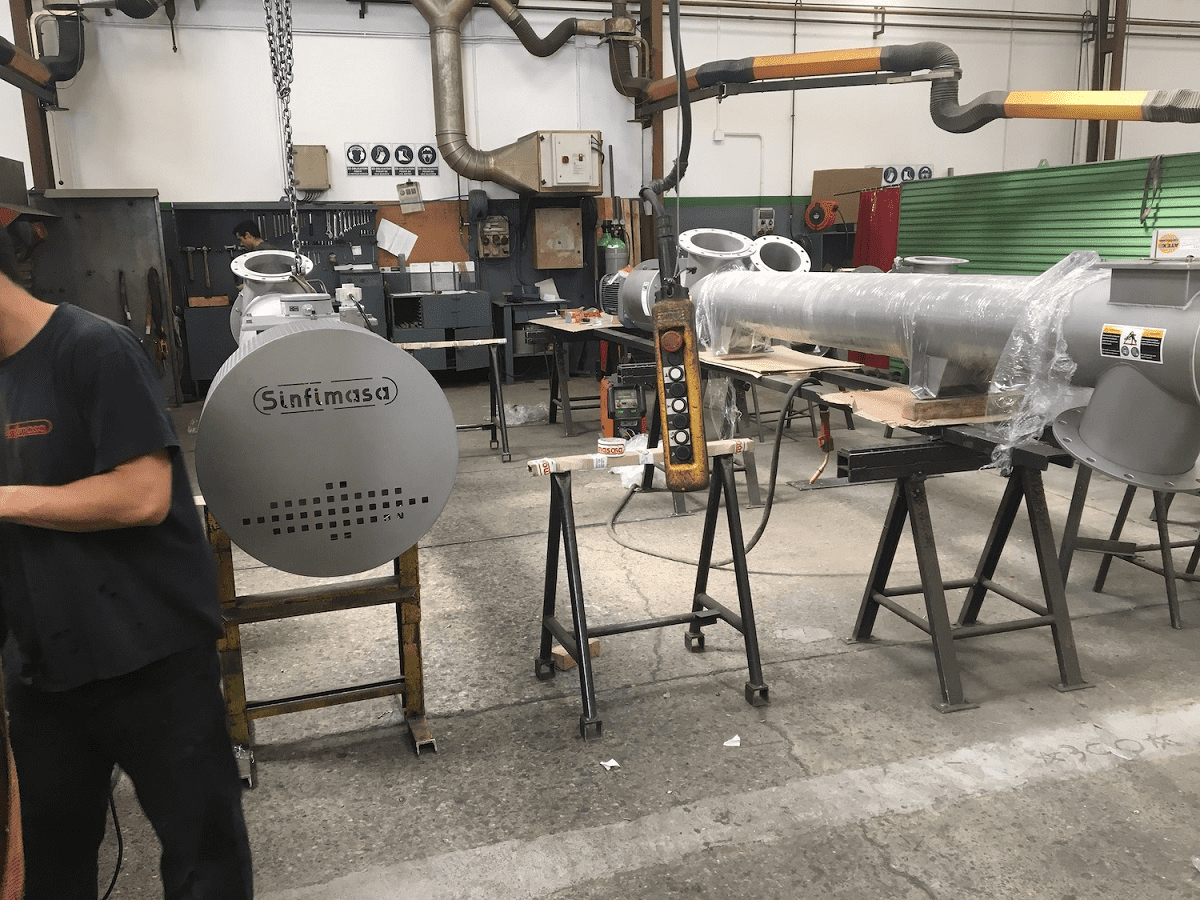