Group Depre operates in four distinct sectors of the animal feed industry. The focus within the first three branches is on production and trade. Group Depre specializes in mixed feed for intensive livestock farming, pet food for birds and rodents, pet food for dogs and cats, and the trade in plant resources. The fourth branch concerns the trading and transshipment of vegetable raw materials. Holland Diervoeders, a division of Group Depre, specializes in producing pet food for rodents and birds.
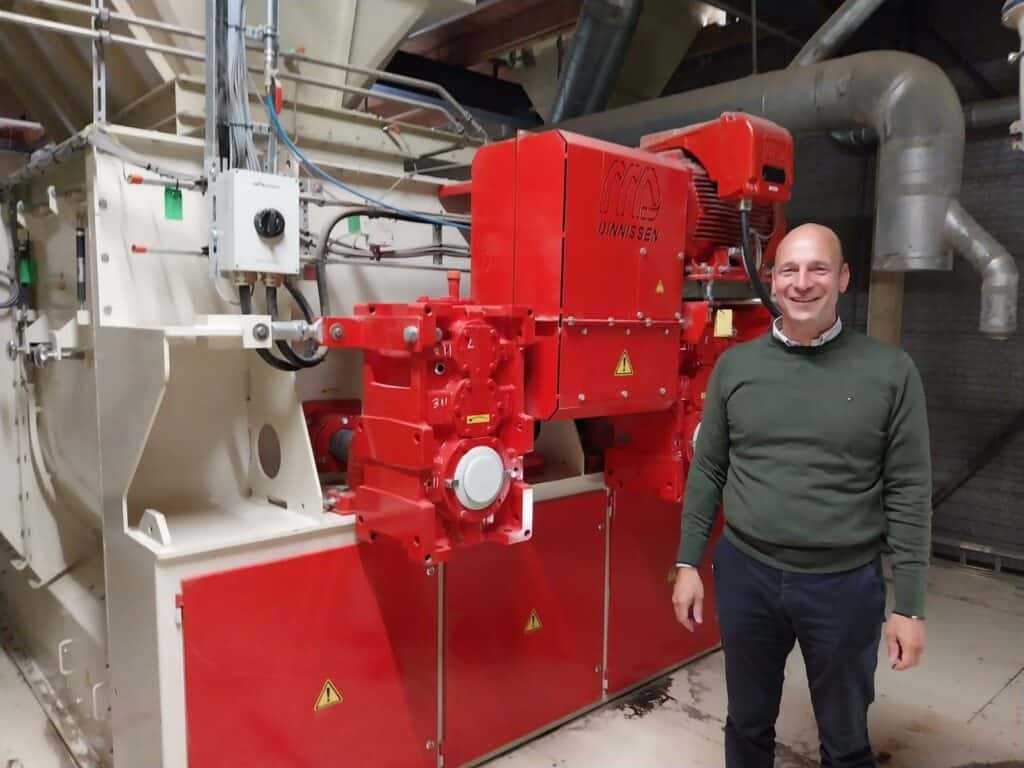
A new production process with the help of LDL Bulkhandling
LDL Bulkhandling assisted Holland Diervoeders in establishing a more efficient and sustainable production process at their Dordrecht facility. Together, they designed a system that replaced the 18 mixers, that were scattered throughout the facility, with a single mixer. This became a Pegasus® Batch Mixer from Dinnissen. This one mixer can supply all bagging lines, which were previously supplied by 18 mixers.
“DINNISSEN’S MIXERS HAVE A SHORT MIXING TIME AND ENSURE THAT NO RESIDUES REMAIN IN THE MACHINE AFTER THE MIXING PROCESS. AS A RESULT, THE MIXER DOES NOT NEED TO BE CLEANED AFTER EACH BATCH”
– EDWARD DEPRE, PROJECT MANAGER AT GROUP DEPRE
Why a Dinnissen mixer was chosen
Holland Diervoeders chose Dinnissen based on the concept and the way Dinnissen builds. “The gentle way of mixing is very important for our products, as it prevents product breakage,” states Edward Depre the project manager of Group Depre. “Dinnissen’s mixers have a short mixing time and ensure that no residues remain in the machine after the mixing process. This means the mixer does not have to be cleaned after each batch.”
Holland Diervoeders needed a mixer that could handle various batch sizes, as not every customer of Holland Diervoeders requires the same quantity of final product. Edward Depre explains: “We used Dinnissen’s test center. This allowed us to test whether the mixer was suitable for both the maximum and the minimum amount of product to be processed. The tests showed great mixing results in a very short time. All batches are mixed within seconds, even the more challenging recipes.”
“THE AMAZING PART IS THAT WE MANAGED TO INCREASE THE CAPACITY, DESPITE USING 17 FEWER MIXERS”
– EDWARD DEPRE, PROJECT MANAGER AT GROUP DEPRE
The advantages of the new mixing situation
Edward emphasizes the benefits brought about by the new mixing setup. “The replacement of 18 mixers with one mixer has been a significant sustainability improvement in terms of energy consumption. In addition, a single mixer requires less maintenance and takes up less space than all separate mixing installations. The amazing part is that we managed to increase the capacity, despite using 17 fewer mixers.”
“WE USED DINNISSEN’S TEST CENTER. THE TESTS SHOWED GREAT MIXING RESULTS IN A VERY SHORT TIME. ALL BATCHES ARE MIXED WITHIN 40 SECONDS, EVEN THE MORE CHALLENGING RECIPES.”
– EDWARD DEPRE, PROJECT MANAGER AT GROUP DEPRE
A powerful collaboration
It was a challenge to fit the Pegasus mixer exactly into the existing silo building. Holland Diervoeders, LDL Bulkhandling, and Dinnissen took on this challenge together. The project required detailed preplanning and precise measurements. Edward is satisfied with the way the implementation went: “The installation of the mixer in the existing situation has been successful. It was a new type of mixer for the operators, but the commissioning also went very smoothly.” All three parties can look back on a smooth process that resulted in a successful outcome.