Manufacturers of adhesives, sunscreens, and wall paints have a common problem: these products are usually characterized by having a high viscosity, which can make the production of the products very complicated and costly. The goal is a homogeneous distribution of all liquid and solid components without any lumps. At the same time, economical production with the shortest possible production times and efficient use of the infrastructure is crucial for manufacturers’ competitiveness. In order to find a solution for these requirements, IKA Werke GmbH & Co. KG have developed the compact and extremely powerful XPP mixing and dispensing system. The plant is suitable for all basic operations of mixing and dispersing in the food, chemical, pharmaceutical, electronics, and cosmetics industries. The XPP is available in 7 sizes from 50 to 4000 liters capacity.
The main components of the powerhouse plant
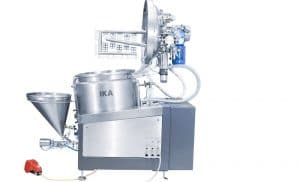
The XPP has been specially designed to achieve maximum performance in the smallest footprint. Minimal maintenance was also taken into account. The low overall height, the removable cover panels, and the very compact design of this powerhouse speak for themself. The direct connection of the integrated CMX inline mixing machine underneath the mixing vessel ensures an immediate additive supply. The ideally short pipelines also ensure the lowest possible pressure losses on the liquid side and thus reliable operation even with increasing viscosity and minimal residual quantities. Thus, the XPP can be operated over a very wide viscosity range without the need for an additional pump. A clear design and the use of proven machine components allow for easy operation, shortest process times, and very good and constant mixing quality. Another decisive component of the XPP is the anchor agitator with its special function for product discharge. Together with its mounted movable scrapers, it ensures optimum mixing, ideal heat transfer between the product and the double jacket, and prevents deposits from gathering on the container wall.
The multifunctional dispersion miracle CMX
The functional heart of the XPP plant is the integrated CMX inline mixing machine. It ensures highly turbulent solid-liquid mixing. Designed in a two-stage version with a pumping and a dispersing stage, the CMX guarantees fast, homogeneous incorporation of additives into liquids with avoidance of agglomerates. The CMX is operated in a recirculation process. By circulating the contents of the vessel at a high flow rate, a negative pressure is created in the mixing chamber, which is used to suck in the additives. Thanks to the closed system, dust and solvent emissions are avoided. The CMX can be adapted to the product and the process objective by changing to different tools in the two dispersion stages. The speed of the machine is a further process parameter. Stable functionality and delivery rate is guaranteed by the multi-stage design, even with increasing viscosity without the use of pumps. The high circulation capacity of the CMX even serves as an integrated conveying device for the CIP cleaning liquid, as well as for the discharge or transfer of the container contents.
Helpful accessories
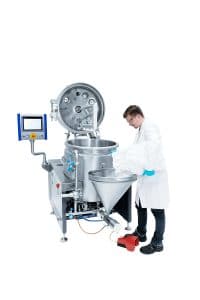
Different industries have more diverse requirements for the periphery of their production plant. Thanks to a range of optional accessories and the possibility of connecting various feed systems, the XPP mixing and dispersing plant is universally applicable. From big-bag stations for the automated feeding of large quantities of solids to bag chutes, simple hoppers, and suction lances for manual operation, anything is possible. The lid of the plant is tiltable to allow easy access to the inside of the vessel and the stirrer. Safe handling of the plant is ensured by a 2-hand operation and an acoustic signal. All connections necessary for the process and the safety devices are located on the lid itself, as well as sight glass and lamp for process observation. An intuitively operated control panel with a touch display and CIP spray nozzles located in the lid for highly efficient cleaning of the inside of the container is further helpful equipment features. Customer-specific special solutions are our expertise: an ATEX version is just as feasible as are special stirrers, for example. Furthermore, the XPP plant can be supplemented by several tanks for additives and for filling, which is installed upstream and downstream of the mixing process.
Scale-up from laboratory to production
The use of the same procedures and process parameters for laboratory and production is the basis for a safe scale-up. The technology on which the XPP mixing and dispersing plant is based is identical to the magic PLANT inline pilot plant of IKA Werke GmbH & Co. KG. It is the ultimate simulation of a process plant and can be used just like the XPP for the production of e.g. emulsions, suspensions, and solutions. The recipes, which are created and further developed in small batches with the pilot plant, can be produced in the same process by scale-up thanks to a uniform plant concept. During the scale-down from production plant XPP to magic PLANT, in turn, the effects of changes in process parameters or ingredients can be easily determined with little material input and effort.