“We’re diverse in what we manufacture and package,” says Jim Longo, DCP President. “We either develop technology and private-label it for large dental and medical distributors, or we manufacture product according to customer specifications under the customer’s label.
“We make powder blends for specialty functions within the dental industry,” he explains. “These include cement removers, powders that remove impression material from moulds, products for fabrication of dental prostheses and for cleaning of dental instruments, in addition to other custom powders for dental laboratories.”
Other products range from cleaners used by jewellers to high-level enzymatic cleaners used on printed circuit boards.
Playing a central role in DCP’s growth is a Munson 1.13 m3 (40 cu ft) HD-36-SS Ribbon Blender that has been producing the company’s powder blends since 2003. It now processes some 45 formulations totalling about 340,194 kg (750,000 lb) annually––a leap from 13,607-18,144 kg (30,000 to 40,000 lb) blended by the mixer when new.
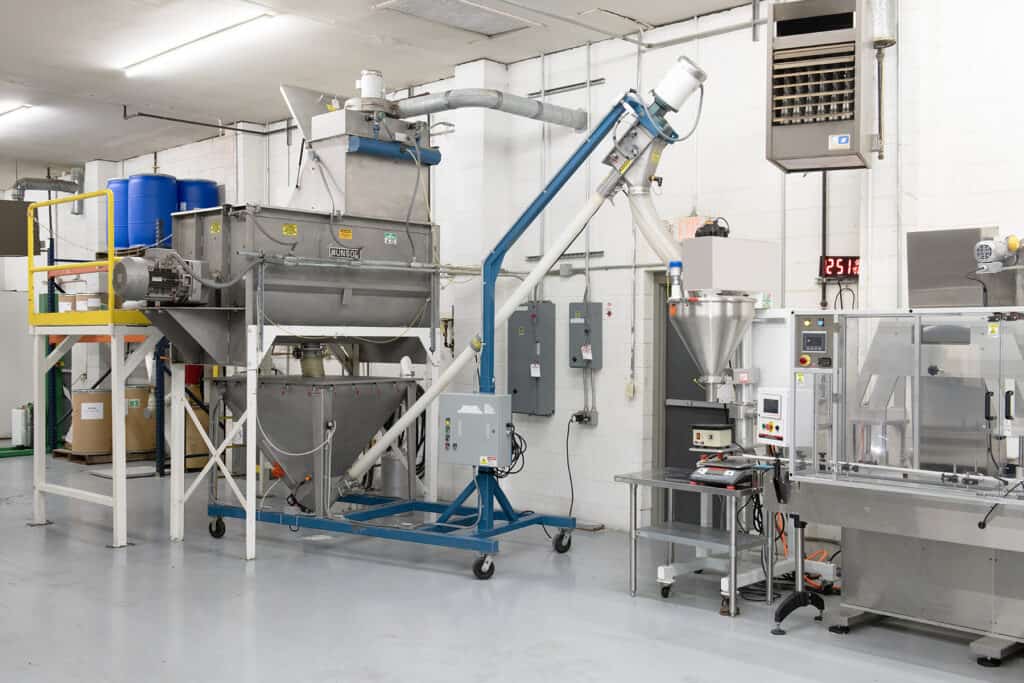
The FDA-compliant, all stainless steel machine is configured with a bag dump station at its intake, and a receiving hopper and screw conveyor at its discharge to transfer materials to a surge hopper feeding a filling and packaging line.
Powder blending a mainstay at DCP
“Our blender is adaptable and flexible,” says Longo, “and has been our most consistent piece of equipment. Numerous machines here have been replaced or upgraded, but the ribbon blender has been a mainstay for 50 percent of our business, which is powder blending.”
“The machine has never required an overhaul and has enabled us to take on projects that we previously could not handle,” Longo continues. “We fill everything from 208 l (55 gal) drums all the way down to small individual unit-dose packets. If you consider the range of products processed, and that we are moving three quarters of a million pounds of powder per year, our ribbon blender is constantly running.”
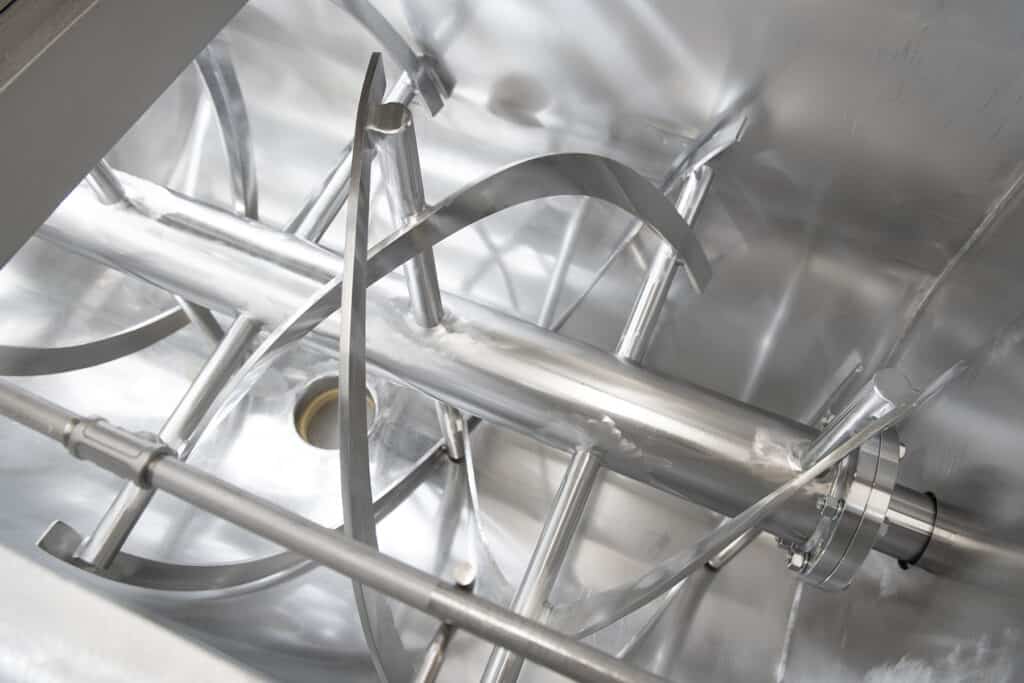
Longo says batch sizes range from 227 to 1,134 kg (500 to 2,500 lb), and the blender yields an accurate mix that passes quality control specs. A typical batch when engineering a product for a customer falls between 816 and 953 kg (1,800 and 2,100 lb).
He adds that the blender’s simple design helps when transitioning between products, allowing for cleaning and sanitising with relatively little downtime. “We change seals regularly, depending on which product we’re going into, to eliminate cross-contamination. The unit has air purge for the seals, which keeps out most of the powder. But after a day when we have finished five different blends, everything is broken down, cleaned, stripped, scrubbed, sometimes seals changed, and then it’s set up in for the next blend, which takes place a day or two later.”
Dust containment is vital for DCP. “To manage the dust created by the materials we process, we fit the bag dump station with pleated, one-micron filters for some applications and submicron filters for others, which we can easily swap in and out.”
Agitator design achieves uniform blends, sanitises rapidly
Given the uniform dispersion needed for materials having varying densities and particle sizes, the ribbon blender remains optimum for DCP, compared to a plow- or paddle-style machine. “Some ingredients might only weigh 10 or 15 pounds (4.5 or 6.8 kg) on a 2,000-pound (907 kg) batch,” explains Longo. “Some might be a fraction of a percent.
The blender’s semi-helical arrangement and counter-flow agitation uniformly disperse the ingredients throughout the mix; the outer blades extending to the vessel wall are pitched to move material in one direction, while inboard blades are pitched to move material in the opposite direction.
“You have the two outer bands moving in a direction counter to the inner flow, and the two edges mixing together,” Longo explains. “We have a number of powders containing enzymes that have to be accurately dispersed and verified through QC analysis. We achieve accurate dispersion consistently.”
The most challenging materials the blender handles include “fluffy” low bulk density powders, many which require large liquid additions through the blender’s internal spray lines. Longo says, “Out of the 45 powders blended at DCP, at least 40 include some form of liquid injection into the mix, whether customers require fragrances, dyes or colours added, or formulas requiring liquid ingredients.”
According to Longo, cleaning proceeds quickly and easily, without needing to remove the ribbon blade agitator element. “After many years of performing regular maintenance, my team has cleaning down to a science.”
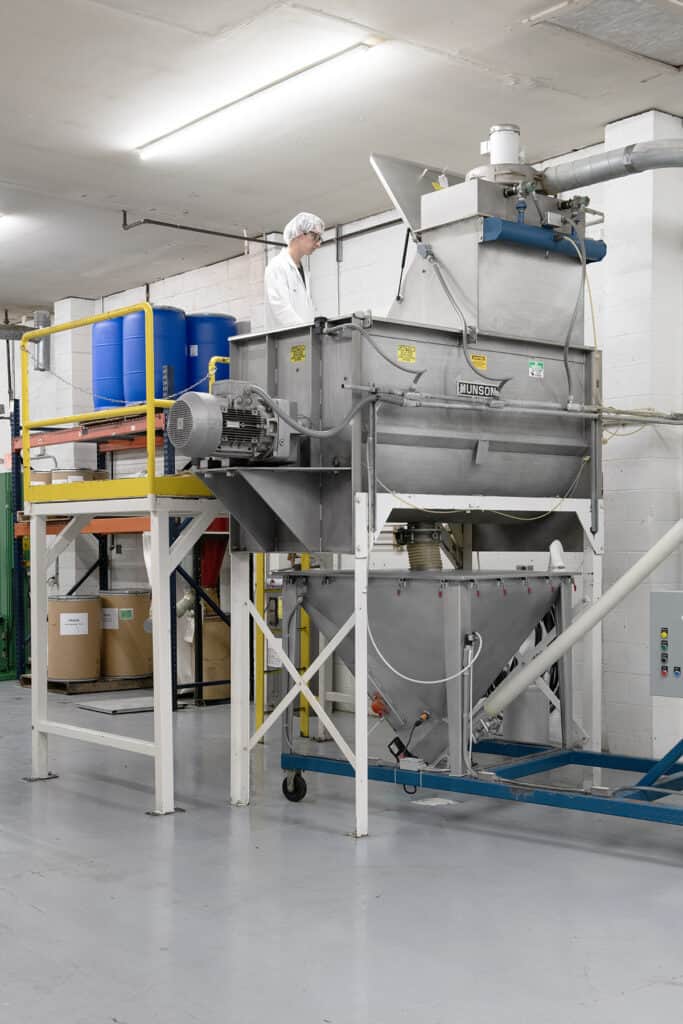
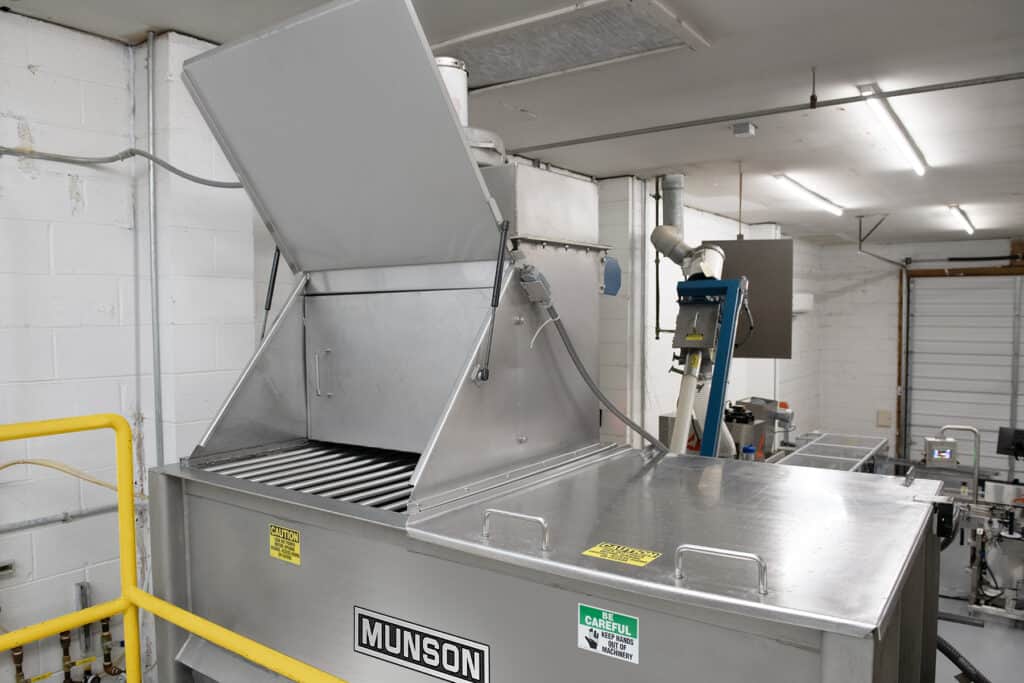
Growth plans include larger and smaller blenders
DCP is looking to move to a larger facility to increase capacity. “We’ve maxed out this facility as far as square footage. If we had more space we would install a larger blender, which would take up the downtime and run concurrently with the existing unit.”
In the meantime, DCP is contemplating adding a smaller Crossley Economy™ Ribbon Blender, also offered by Munson, to handle some sophisticated minor blends.
“These minor blends might have three or four minor ingredients that are added to the larger batch,” explains Longo. “It could be a colour batch, a fragrance batch, or a blend of enzymes. We prepare these in a small planetary blender that can only handle about 35 gal (132 liters) at a time. We are looking to get a machine that can handle batches around 10 to 20 cu ft (0.3 to 0.6 m3).”
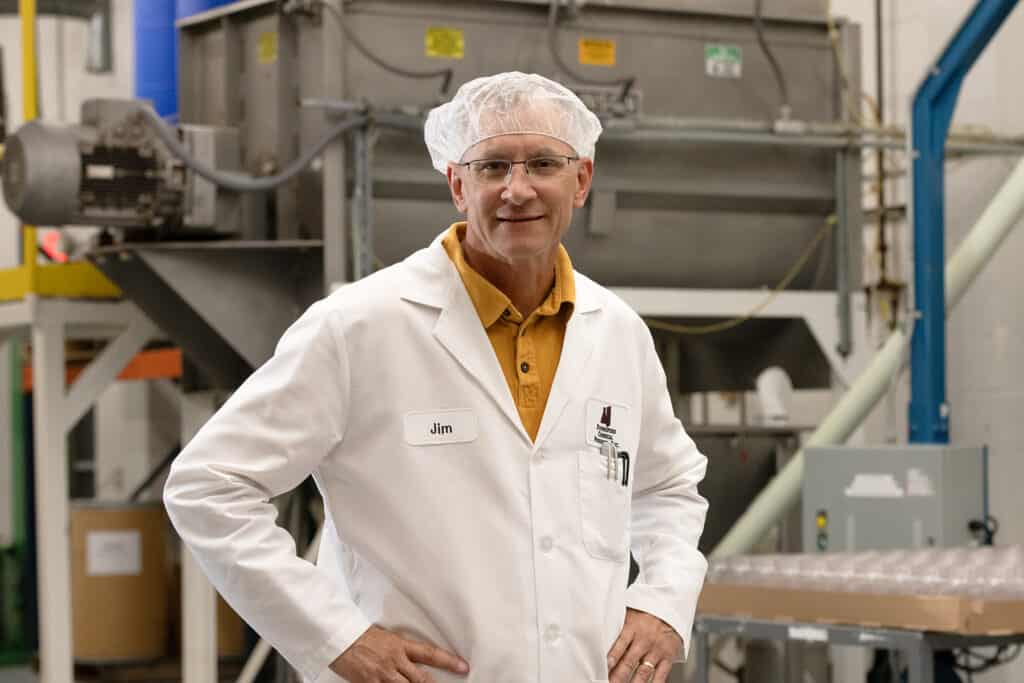