The simple act of transferring a large quantity of powders in a relatively short amount of time results in a lot of displaced air. This naturally creates process dust that, if not properly managed, can leak out of the bag connection and into the plant.
In any manufacturing plant dust leaking into the environment is a serious concern around combustible dust explosion risks, and the health hazard this dust represents for operators.
It’s important, therefore, that there is a form of dust collection or venting system incorporated into any filling process. The displaced air will need to have an outlet to allow rapid product flow to continue without dust leaking into the environment.
Although dust collection/venting systems certainly help, dust leakage can still be a serious problem for bulk bag loading systems as the seal around the neck of the bag when it is connected to the filling head is rarely airtight.
Old-style clamp systems
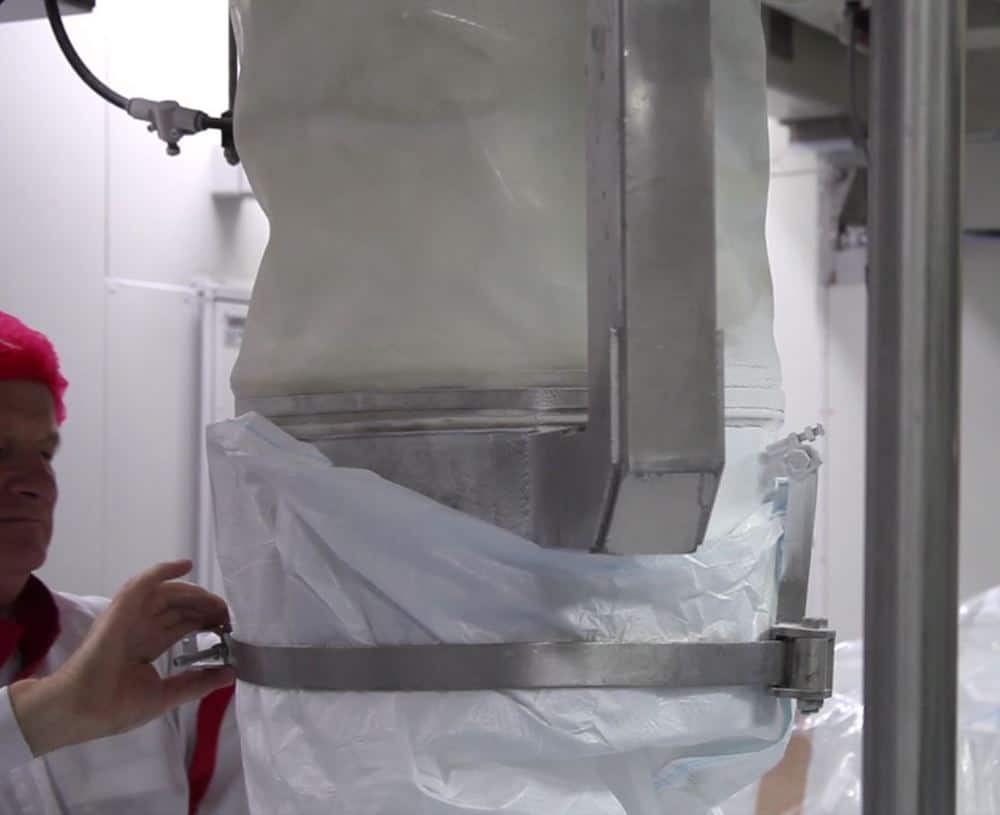
Many of the traditional bulk bag loading systems in factories feature a clamp-style system to hold the neck of the bag against the filling head. Whilst this method does have the advantage of allowing multiple-sized bags to be used, clamps simply cannot seal the neck fully for all bag sizes.
Where a neck is considerably larger than the feeding head, when fitting larger bags, the folds of the material create even more opportunities for dust to escape into the atmosphere. Another safety risk from clamped systems is the potential danger to operators’ hands. There are multiple opportunities for damage to fingers when positioning the neck of the bag in the correct position and holding it in place while trying to get the clamps fastened correctly on all sides of the filling head.
Inflatable filling heads
To improve the seal and reduce dust escaping, inflatable filling-head systems are being used more and more today. The inflatable ‘bladder’ on the outside of the filling head expands against the inside of the neck of the bag, holding it open and taught and sealing off any gaps for potential dust leakage.
Although these inflatable filling heads provide an excellent solution for dust control, many often have a bar or cage that the inflated necks are pushed out against to hold the neck open and create the seal. This is still a potential risk to operators’ hands when holding the bag neck in place as it is inflated.
With both clamped loaders and inflatable systems that use hose clips to secure their rubber bladders, there is also a real risk of components from these fastening systems falling into the product, causing contamination.
A faster, cleaner, and safer option
The leading brand in flexible connection technology, BFM®, have used their patented snap-fit connector system to develop a fully sealed, inflatable Bulk Bag Loading head that makes hygienic loading fast and easy, as well as safer for operators.
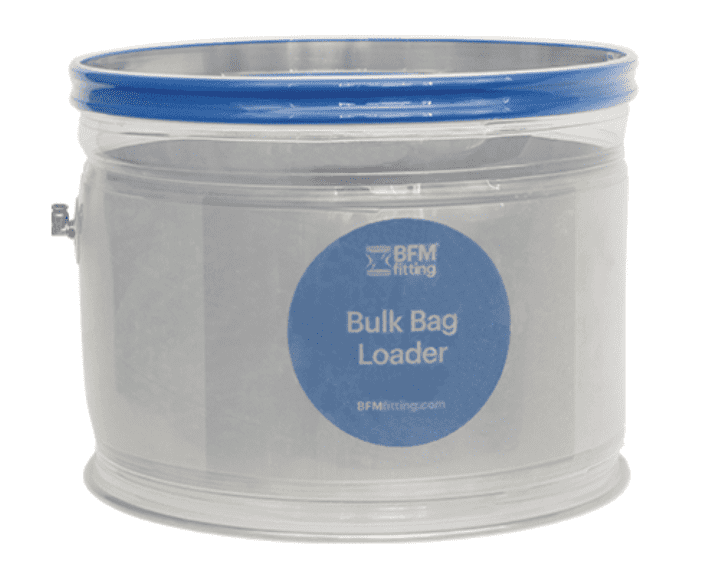
The BFM® Bulk Bag Loader is a three-layered inflatable filling head that snaps easily into a BFM® spigot welded to the outlet chute. It features a stainless-steel central core, fully encased in BFM®’s extremely strong, flexible Seeflex urethane.
An external air fitting is simply plugged into a standard 8mm pneumatic airline to inflate the super strong and flexible outer layer.
When inflated, the outer Seeflex layer will securely hold the bag neck up and open for clean, efficient filling. It doesn’t need clamps, bars or cages which means there are no pinch points to endanger operators’ hands when fitting the bag, making it a much safer option for staff.
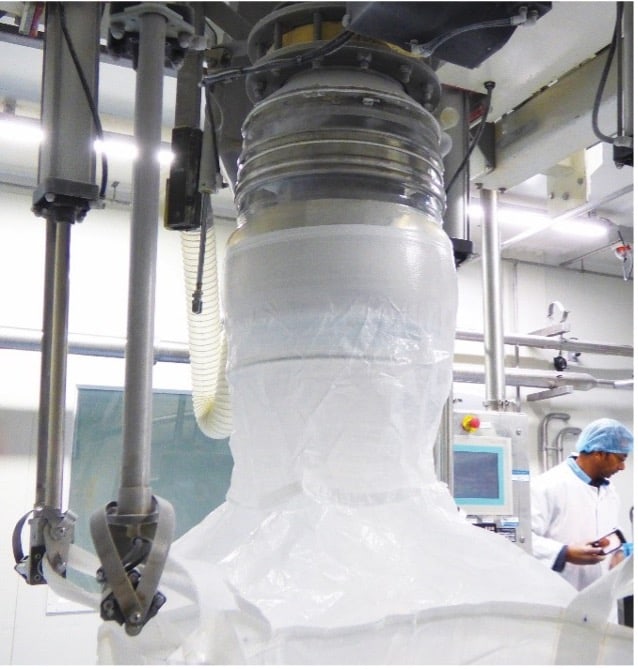
The superior seal of the BFM® fitting system means that the neck of the bulk bag will be securely held open and there will be no leaks during loading. Once loading is complete, the outer sleeve can be instantly deflated for easy bag removal.
The BFM® Seeflex urethane is much stronger, more flexible, and durable than silicone/rubber-based products that degrade if inflated multiple times.
The patented snap-fit connection of the BFM® fitting also makes it faster and easier to take out, clean and replace than any other connector/filling head.