Mounted on a mobile frame with locking castors and fold-down step, the dust-free system features a bag disposal chute through the sidewall of the hopper hood, allowing the operator to pass empty bags directly into the bag compactor. Dust generated from bag dumping, empty bag pass-through, and bag compaction is drawn away from the operator, onto the system’s two cartridge filters. Automatic reverse-pulse air nozzles release short blasts of compressed air inside the filters at timed intervals causing dust build-up on the outer surfaces to fall into the hopper, conserving useable product. Filters are readily accessed by removing the interior baffle and replaced using quick-disconnect fittings.
The compactor employs a pneumatic air cylinder capable of compressing up to 80 bags into a removable bin. The compactor’s main door and flapper door within the bag disposal chute is equipped with safety interlocks that prevent operation of the compactor unless both doors are closed.
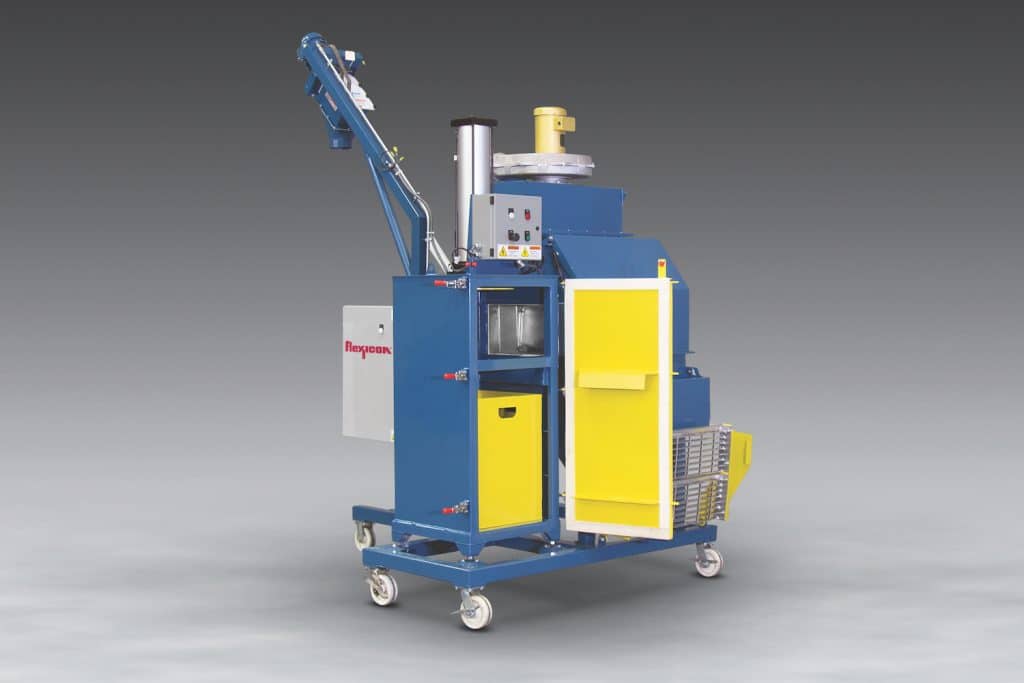
The hopper discharges into an enclosed flexible screw conveyor, capable of moving free- and non-free-flowing bulk materials from large pellets to sub-micron powders, including products that pack, cake, seize, smear, fluidize, break apart, or separate, with no separation of blended products.
Ready to plug-in-and-run, the mobile system is equipped with an IP-66 control panel and user-friendly HMI interface, allowing the operator to vary operation of the dust collection system and conveyor to serve varied processes, and then roll the system to a cleaning station or storage area between uses.
The unit is constructed of carbon steel with a durable industrial finish, and available with stainless steel contact surfaces or in all-stainless models finished to industrial, food, dairy, or pharmaceutical standards.