Furthermore, the significance, application, and benefits of integrating sensors on these pivotal components are elaborated upon, emphasizing their role in real-time data acquisition and analysis. Central to this discourse is the integration and utility of IoT platforms and artificial intelligence. Their capabilities not only reshape operational paradigms but also offer unparalleled advantages, which are comprehensively discussed, laying the foundation for a new era of intelligent and efficient pneumatic conveying systems.
Introduction
Pneumatic conveying, an integral component in a myriad of industries, from food processing to pharmaceuticals, and from mining to chemical engineering, has stood the test of time due to its efficiency in transporting bulk materials across varying distances. Critical to its operation is the consumption of power, predominantly due to the extensive use of air, which often represents a significant portion of operational costs. With the dawn of Industry 4.0 and the burgeoning integration of industrial IoT technologies, cloud systems, and smart analytics, the landscape of traditional pneumatic conveying is poised for transformative changes. Central to this transformation is the concept of ‘digital twinning’. Digital twinning is more than just a technological trend, it’s a transformative approach that melds the physical and digital worlds. Essentially, it’s about crafting a dynamic, virtual representation of a real-world system or entity. This digital counterpart, continuously fed with real-time data from sensors and other sources, mirrors the state and performance of its tangible twin. The resultant synergy allows for richer insights, predictive analytics, and a holistic understanding of complex systems, from their current operational status to potential future scenarios. In the context of pneumatic conveying, such digital replicas become invaluable tools for enhancing system efficiency, monitoring wear and tear, and ensuring optimal energy utilization.
The Role of Digital Twinning in Pneumatic Conveying
Process Monitoring
The first and perhaps most significant role of digital twinning in pneumatic conveying is the capability for comprehensive process monitoring. By mirroring the physical system, a digital twin provides an in-depth look at every aspect of the conveying operation, capturing essential parameters such as air pressure, flow rate, and energy consumption. Furthermore, digital twins can monitor external factors like ambient temperature or humidity, which might influence system performance. But the potential of a digital twin doesn’t end with just mirroring these parameters. It actively gathers and analyzes this data, offering insights that can be harnessed for performance optimization. For instance, patterns discerned from air pressure or flow rate fluctuations can lead to adjustments that maximize throughput while minimizing energy use. Additionally, digital twins have the foresight to account for external influences such as ambient temperature or humidity, factors often overlooked but which can significantly impact system performance. By understanding these external parameters and their effects, the system can be calibrated to work optimally under varying conditions. In summation, the digital twin isn’t merely a passive observer. It’s an active participant that, through rigorous monitoring and data analysis, paves the way for continual refinement and optimization of pneumatic conveying operations.
For pneumatic conveying, even minor inefficiencies can lead to significant costs over time, both in terms of energy and wear on equipment. The digital twin’s constant vigilance means that operators no longer need to rely on intermittent manual checks or wait for a problem to become glaringly evident. Instead, they have access to a continuous stream of data insights that can guide them in fine-tuning the system. Consider, for example, a scenario where the digital twin detects a sharp drop in air pressure at specific point in the conveying line. This data, when analyzed, might indicate a potential blockage in the pipeline. Addressing such an issue promptly could mean the difference between a minor maintenance task and a significant system breakdown. Moreover, by analyzing trends over time – such as energy spikes during certain operational hours or decreased efficiency due to seasonal temperature fluctuations – organizations can forecast potential issues and make proactive adjustments. This predictive approach not only ensures uninterrupted system operation but also optimizes energy consumption, leading to cost savings.
Additionally, data-driven insights can shed light on the optimal operating conditions for different materials being conveyed. For instance, some materials might be transported more efficiently at a different airflow rate or pressure. With the digital twin’s data at their disposal, operators can adjust parameters on- the-fly, ensuring that the system always operates at its peak efficiency regardless of the material being conveyed.
In essence, the holistic view provided by the digital twin, coupled with its analytical capabilities, empowers organizations to shift from reactive to proactive management. The result? A pneumatic conveying system that is not only more reliable but also operates at its highest possible efficiency, driven by data-informed decisions.
Condition Monitoring
One of the paramount applications of digital twinning in pneumatic conveying is in the domain of condition monitoring. Instead of simply observing the performance metrics of the conveying process, condition monitoring focuses specifically on the health and performance of the equipment involved. Every piece of equipment, from blowers and rotary valves to the pipelines themselves, has a lifecycle. Over time, wear and tear, exposure to harsh materials, or even simple operational stresses can deteriorate their performance. The beauty of digital twinning lies in its ability to capture these subtle changes in equipment behavior before they manifest as significant issues.
For instance, a slight change in vibration patterns of a blower or a minuscule drop in efficiency of a rotary valve could be early indicators of impending equipment failure. By continually comparing the real- time performance data against the optimal operational benchmark set in the digital twin, the system can instantly detect these anomalies. Integrating this with predictive maintenance, the digital twin not only identifies potential issues but also forecasts when these anomalies could lead to equipment failure. Instead of waiting for a breakdown, maintenance teams can be alerted in advance, allowing them to take preemptive action. This proactive approach drastically reduces downtime, ensures consistent system performance, and extends the lifespan of equipment components. Thus, by merging condition monitoring with predictive maintenance capabilities, digital twinning becomes an indispensable tool. It not only ensures the robustness of pneumatic conveying systems in terms of material transportation efficiency but also safeguards the longevity and health of the integral equipment components.
Implementing Digital Twins in Pneumatic Conveying Systems
Sensor Integration: The first step involves integrating various sensors – like pressure, temperature, and flow rate sensors – into the pneumatic conveying system. These sensors capture vital data in real-time.
Digital Model Creation: Using specialized software, a digital twin of the conveying system is created. This model will continuously sync with the sensor data, ensuring it always mirrors the physical system’s current state.
Data Collection: It begins with embedding sensors at strategic locations in the pneumatic conveying system. These sensors collect real-time data on various parameters such as pressure, temperature, flow rate, and more.
Continuous Monitoring and Analysis: Operators can now keep an eye on the digital twin, analyze data, run simulations, and even use machine learning tools to predict future scenarios or potential issues.
Continuous Evolution: As the pneumatic conveying system evolves – due to changes in materials, upgrades, or expansions – the digital twin must also be updated to reflect these changes.
Example Application
For a clearer understanding, we’ll illustrate a pneumatic conveying system example. This setup includes key components like a roots blower, rotary valve, conveying pipeline, storage silo, and a top- mounted silo filter (dust collector). The system operates on a positive pressure dilute phase principle. Here’s how it works:
Material Input: Powdered materials are introduced into the system via a bulk bag discharging mechanism. Material Feed: A rotary valve manages the entry of the material into the conveying pipeline.
Air Supply: The roots blower supplies the necessary conveying air, propelling the material through the pipeline.
Material Storage: Upon reaching the storage silo, the material separates from the conveying air.
Air Evacuation: The separated air exits through the top-mounted silo filter which employs a reverse pulse jet mechanism, allowing for automatic self-cleaning capabilities.
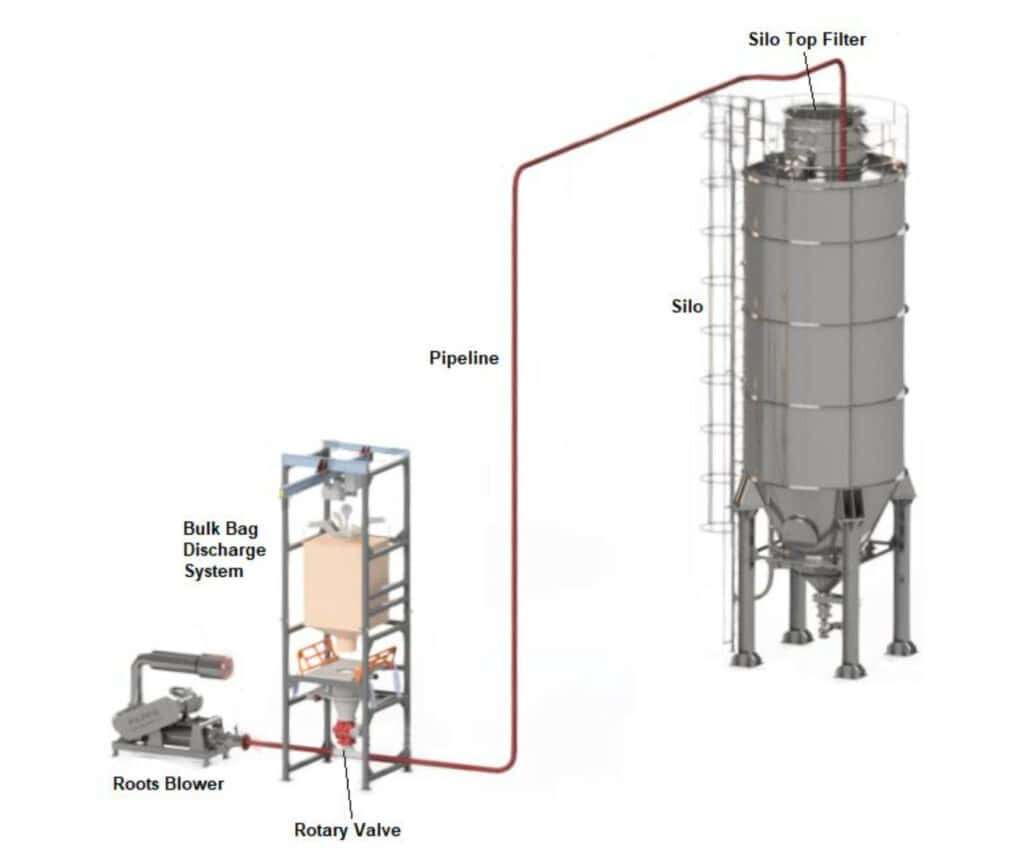
The system incorporates a variety of sensors, each meticulously detailed in the accompanying tables in terms of their locations and functions. For each sensor, potential triggers and circumstances are systematically documented. While pneumatic conveying systems might appear straightforward, issues can arise from incorrect sizing, inadequate engineering, improper installation, or lapses in maintenance practices. Moreover, even after extended periods of optimal performance, shifts in the provided raw materials can introduce challenges. Given the extensive array of potential issues in pneumatic conveying systems, we’ve catalogued the most prevalent ones and linked them to their respective sensors for easy reference.
(PS: The functions outlined in the table offer a general overview and may not be applicable to all scenarios. They also don’t encompass every possible condition. For a comprehensive analysis or troubleshooting of your system, it’s recommended to consult an expert.)
Roots Blower
Location | Sensor | Function |
Roots Blower Air Outlet | Outlet Temperature | -Used to verify if the supplied air temperature is appropriate for the material being handled. -Used to monitor the temperature rise across the blower. An abnormal temperature increase could suggest that the blower is operating at lower speeds with elevated pressure. Alternatively, it might indicate increased clearance between the blower lobes and the housing, pointing to potential damage or wear on the lobes. |
Outlet Pressure | Used to monitor the pressure within the pneumatic conveying system, a critical parameter reflecting process conditions. For example: -A notably high pressure can suggest miscalibrated airflow rates or excessive feeding by the rotary valve. -A consistent, gradual increase in pressure could be indicative of early- stage pipeline blockages or filter clogs. -Significant pressure fluctuations may denote irregular product intake from the rotary valve or temporary blockages that eventually clear. | |
Outlet Flowrate | Roots blowers typically maintain relatively stable airflow rates despite fluctuations in air pressures. Any significant drop in flow rate could suggest issues such as v-belt slippage, reduced motor speed, blockage in the blower’s inlet filter, or air leakage immediately post-blower. | |
Roots Blower Body | Temperature and Vibration | Elevated temperatures in the blower could suggest it’s running at reduced speeds under higher pressure. Another possibility is an enlarged gap between the blower lobes and housing, which could hint at wear or damage to the lobes. Similarly, excessive vibrations could signal potential damage to components like the blower’s bearings, pulleys, or rotors. |
Electrical Motor | Temperature and Vibration | An increase in temperature on the motor body might result from overloading the conveying system beyond its designed capacity. Meanwhile, excessive vibrations could indicate potential harm to components, such as the bearings and pulleys. |
Power Consumption | The power consumption of an electric motor reflects system performance. Comparing power consumption with conveying capacity gauges system efficiency. Elevated consumption might suggest system overloading or additional mechanical strains like ungreased bearings, over-tightened v- belts, or blower rotor contact with housing. | |
Blower Air Inlet | Inlet Filter Vacuum Level | Inlet filter vacuum level indicates the cleanness of inlet filter |
Ambient Temperature | Ambient temperature is crucial when handling sensitive materials like food or chemicals. Excessive temperatures could damage these materials or pose an explosion risk. |
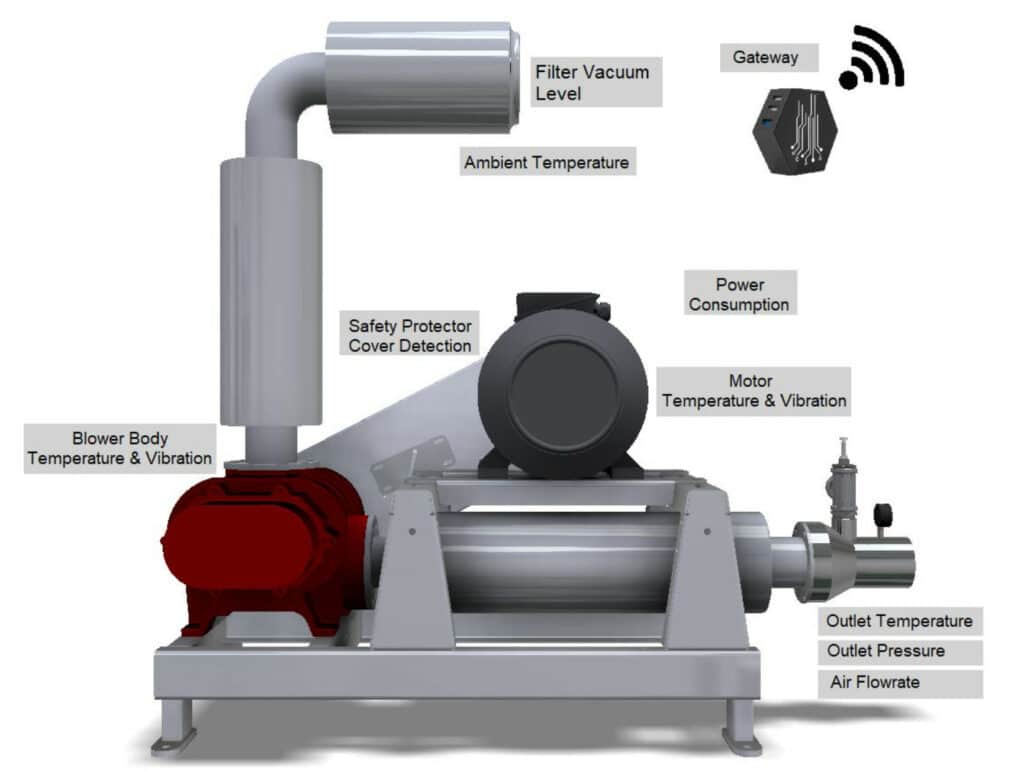
Rotary Valve
Location | Sensor | Function |
Rotary Valve Inlet | Inlet Pressure / vacuum | When a rotary valve is positioned beneath a cyclone, filter receiver, or a similar vessel, the pressure or vacuum level above the valve is crucial since it impacts its feeding efficiency. Deviations from the expected pressure, either too high or too low, might suggest significant air leakage through the valve. |
Rotary Valve Outlet | Outlet Pressure / vacuum | The outlet pressure/vacuum level reflects the internal pressure or vacuum of the pneumatic conveying system’s pipeline, serving as a primary indicator of system performance. Overpressure might suggest potential pipeline clogging or that the rotary valve’s feed rate exceeds its design value. A significant pressure disparity between the rotary valve outlet and the blower outlet can hint at issues within the pipeline or valves connecting them. |
Rotary Valve Body | Temperature and Vibration | A rise in body temperature may result from overheating in the conveying air, stemming from overloading, clogging, or a faulty blower. It could also be due to elevated material temperatures entering the rotary valve or friction between the valve’s rotors and housing. Vibrations on the rotary valve body usually indicate rotor contact with the housing, entry of particles between deteriorated rotor tips and housing, or oversized particles causing forceful contact between the rotors and housing at the valve’s inlet. Additionally, clogging at the rotary valve’s outlet can be a contributing factor. For smaller rotary valves, vibrations can also signal issues related to the bearings. |
Rotary Valve Side Flanges | Temperature and Vibration | Temperature and vibration on side flanges may suggest issues with bearings and rotor shafts. While some temperature and vibration can arise from other factors mentioned earlier, it’s crucial for larger rotary valves to be equipped with separate sensors on side flanges to detect bearing- related problems. |
Electrical Motor | Temperature and Vibration | A temperature rise on the motor body may be due to the intrusion of particles between worn rotor tips and housing, resulting in additional friction. Concurrently, excessive vibrations could signify potential damage to components, including the bearings and gearboxes. |
Power Consumption | Evaluating power consumption against conveying capacity provides a measure of system efficiency. An uptick in power use could point to system overloads, increased friction on rotor tips, or other mechanical stresses such as under-lubricated bearings or gearboxes. | |
Purge Air Pipeline | Purge Air Pipeline | To enhance sealing on side flanges, purge air is employed. Maintaining the appropriate pressure level of the purge air is vital to shield bearings from wear due to inadequate sealing. |
Side Flange | Rotor Speed | Rotor speed or zero-speed sensors are utilized to track rotor rotation, monitoring for potential clogging and halts in its movement. |
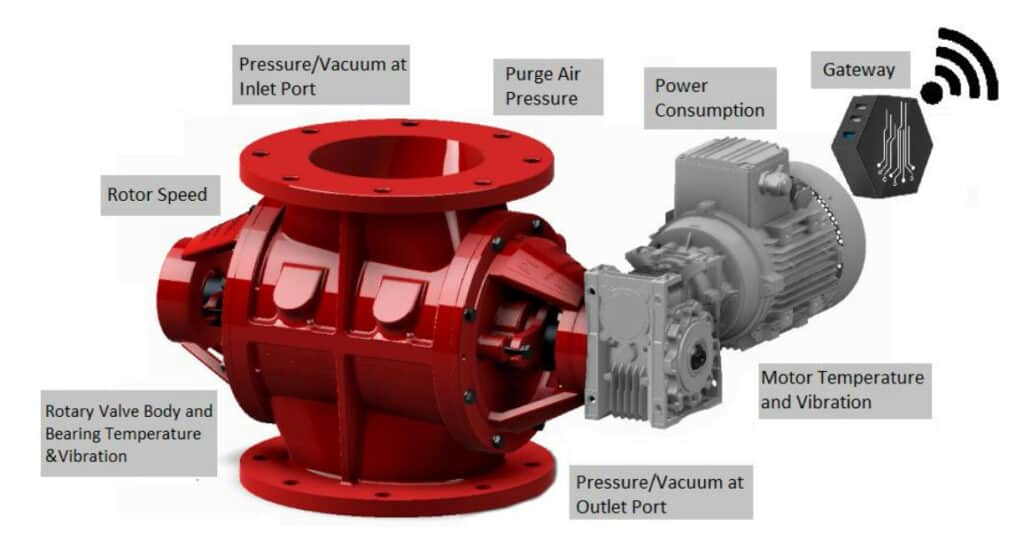
Silo Top Filter
Location | Sensor | Function |
Dirty Side of Silo Filter | Inlet Pressure | The pressure level beneath the filter reflects the internal pressure of the silo, which is vital for process safety. Overpressure can signal clogged filters or air vents, posing explosion risks to the silo. |
Clean Side of Silo Filter | Outlet Pressure | A differential pressure between the clean and dirty sides suggests the cleanliness or condition of filter bags or cartridges, which is crucial for system efficiency. |
Pulse Air Manifold | Process Air Pressure | The pressure level in the pulse air manifold indicates the adequacy of the process air supply. The pressure variation graph helps assess the sufficiency of airflow and detects potential leaks. It’s also instrumental in identifying non-functional or leaking pulse valves. Given the significant energy consumption of process air, monitoring manifold pressure can lead to substantial savings. |
Filter Outlet | Dust Emission | Dust emission monitoring reveals the condition of filter bags or cartridges. It can also highlight leaks stemming from incorrect filter bag installation or structural issues within the filter system. Additionally, alterations in the conveyed material, such as an increased presence of finer particles, can be identified through this monitoring. |
Vacuum Fan | Temperature and Vibration | An elevated temperature on the fan body could stem from obstructed filters. Meanwhile, vibrations may point to problems with the bearings, fan impellers, or accumulated dust on the impeller surfaces. |
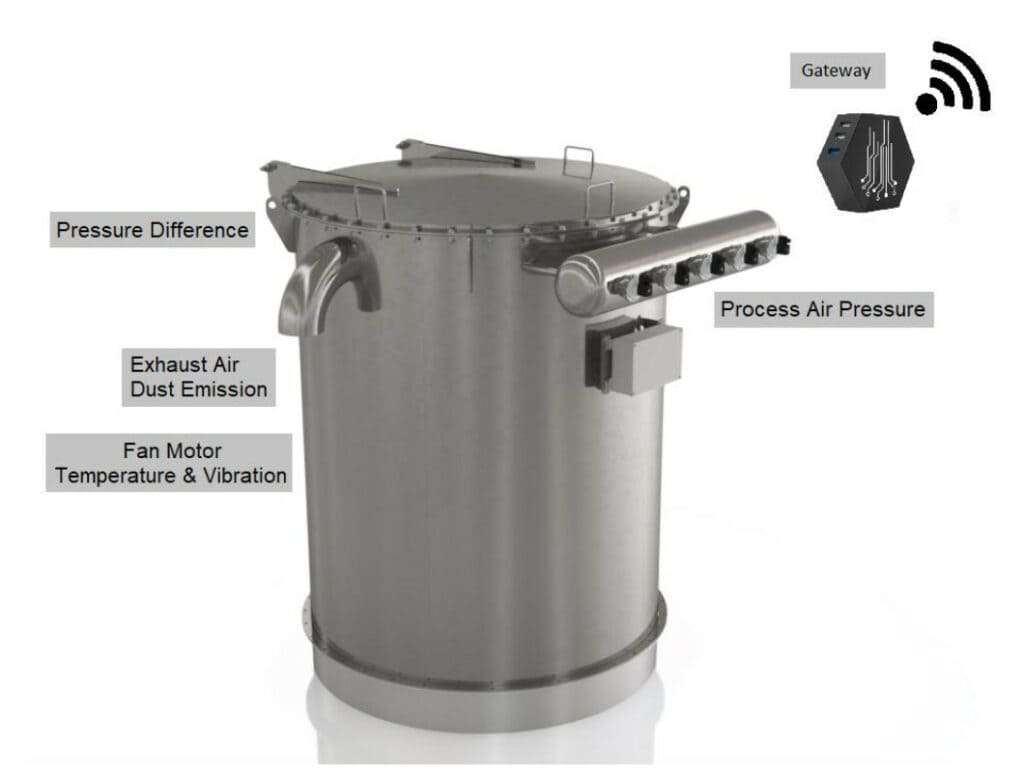
Other Locations
Location | Sensor | Function |
Pipeline | Conveying Air Pressure | Monitoring conveying air pressure from various points along the pipeline offers a proactive approach to detecting blockages. Furthermore, this data can aid in enhancing system efficiency, particularly in extensive conveying lines. |
Silo | Silo level sensors / loadcells | While silo level sensors provide volumetric measurements, load cells are tasked with weighing the material in the silo. Analyzing variations in the material volume within the silo serves as a valuable tool to assess the performance of the pneumatic conveying system and ensures a consistent raw material supply to downstream processes. |
Bulk Bag Discharger | Dust Emission | Dust emission monitoring near the bulk bag discharger provides insights into the operator’s efficiency and adherence to clean operations. It reveals their ability to prevent dust accumulation and their commitment to regular cleaning. Additionally, this feature can detect any sudden dust leaks resulting from overpressure or air leakages above the rotary valve. |
Electrical Panel | Power Consumption | Total power consumption of the system can be measured to monitor total efficiency of the system. |
Sensor Measurement, Data Collection, Transfer, Visualization and Analysis
Every piece of sensor data delineated in this section is garnered through a cloud gateway, subsequently conveyed to an industrial IOT platform. In the present application, the industrial IOT portal, Politrace, stands out as the chosen tool for data aggregation, preservation, and analysis. The preferential selection of Politrace springs from its dedicated emphasis on process technologies and the standardized monitoring modules it offers for handling bulk solids equipment. This encompasses machinery like rotary valves, root blowers, and dust collectors, to name a few. Outlined below are the principal elements integral to the current monitoring structure:
Asset: Within the system monitoring universe, an ‘asset’ refers to any machinery, apparatus, or instrumentality that possesses a pivotal operational role. Instruments like rotary valves, blowers, and silos epitomize system assets. The immediate process values and the holistic health of the asset emerge as crucial indicators warranting measurement and subsequent analysis.

Sensor: Deployed to instantaneously measure specific physical or chemical process parameters, sensors capture variances in aspects such as pressure, vibration, temperature, velocity, and more.
Sensor Output: A sensor’s output can be depicted digitally (e.g., an ON or OFF status) or through an analog format that mirrors the actual measurement after applying a scaling factor, typically represented by metrics like 0-10V or 4-20mA. To elucidate, an air pressure reading of 12 bars might be symbolized as 8mA, while 14 bars could correspond to 9mA. The flexibility extends to the adoption of various communication protocols like Modbus or IO-Link.
Sampling Rate: This refers to the frequency of data recordings within a specific duration. For instance, ten readings every hour implies a 6-minute interval between measurements. While amplifying the sampling rate offers granularity, it simultaneously places demands on the communication structure, increases cloud storage consumption, and requires augmented CPU processing power. On the contrary, a diminished rate might render an incomplete picture of system dynamics. Thus, calibrating an optimal sampling rate tailored to each system is pivotal.
Sensors equipped with their own processors can analyze data and relay only pertinent information to the IOT cloud server, thereby minimizing communication, storage, and CPU demands. This principle is termed “Edge Computing.” A prime illustration is the vibration sensor, typically affixed to machinery that operates at high velocities, usually within the 1500 to 3000 rpm range. For perspective, a machine operating at 3000 rpm completes 50 revolutions every second. Given such machines often incorporate ball bearings on their shafts, rapid measurement intervals become essential to identify potential issues. While 1000 measurements per second might yield comprehensive data, it also poses a strain on communication, storage, and processing capacities. An onboard signal processor on the sensor facilitates localized data processing, transmitting only the final results to cloud servers. For vibration detection, metrics like peak or average velocity, acceleration, kurtosis values, and more are invaluable for immediate asset condition assessment. Hence, in some scenarios, a single measurement every minute might suffice for machinery diagnostics. However, it’s crucial to possess a profound understanding of the asset type to discern if either processed data (that’s lighter on communication) or real-time data (with a high sampling rate) is more apt for analysis.
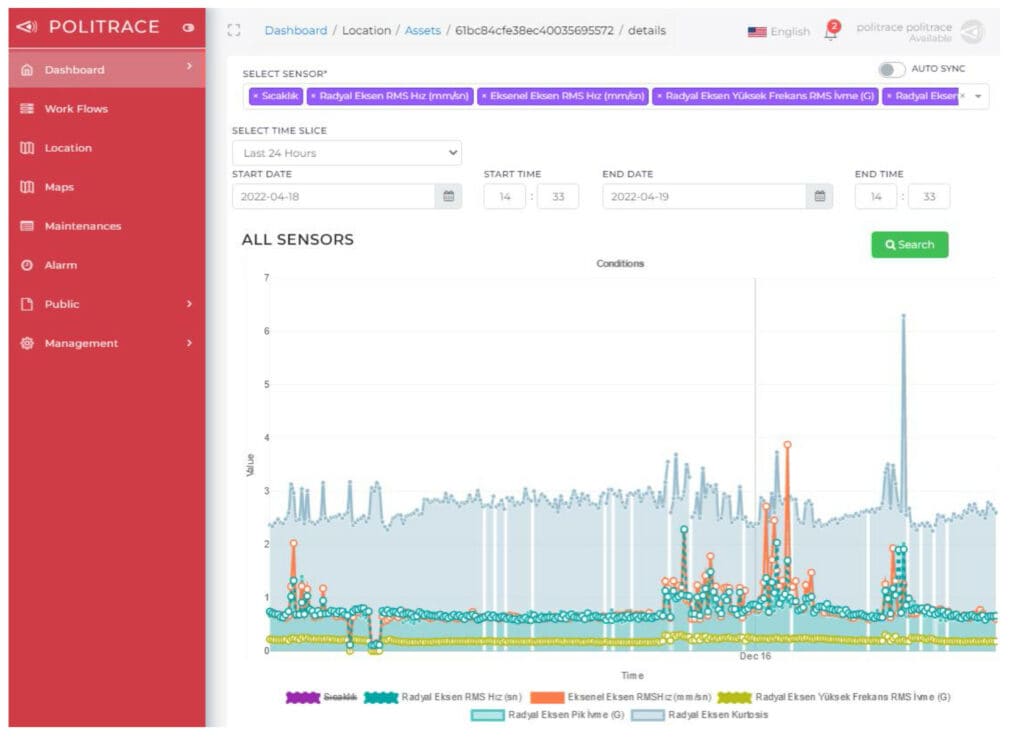
Gateways: Gateways serve as intermediaries, collecting data from sensors and transmitting them to cloud servers. The market offers an extensive array of gateways capable of capturing diverse signal types, including digital, analog, modbus, and IO-Link, among others. Factors such as the quantity of sensors, signal types, and the physical distance between sensors and gateways play pivotal roles in determining a robust system architecture. Additionally, the communication protocols between the gateway and cloud platform can vary, often set by the preferences of cloud server providers and gateway manufacturers. A paramount consideration in this setup is ensuring the secure transfer of information. Given the sensitivity and critical nature of the data, implementing stringent security measures is absolutely vital to prevent unauthorized access or breaches.
IOT Platform: Internet of Things (IOT) platforms primarily operate on cloud infrastructure, offering global accessibility and services. These platforms are designed to store, process, and analyze the vast amounts of data collected from various sensors and gateways. Their architecture is tailored to transform raw data into insightful, actionable information for end-users. Beyond mere data storage, they integrate advanced analytics and machine learning capabilities, ensuring that the data is not just gathered but also provides value to users, aiding in decision-making processes and predictive analytics. The choice of an IOT platform is pivotal, as it forms the backbone of the entire digital ecosystem, ensuring seamless data flow, comprehensive analysis, and robust security.
User Interface: Usually accessible via web-based portals, this interface presents the curated data to users. It grants users the autonomy to configure, visualize, analyze, and extrapolate insights, enhancing their understanding of the system’s real-time status and equipping them with predictive capabilities.
Data Analytics: Data analytics offers critical insights to plant operators, enhancing their decision- making processes. The choice of analytical technique varies based on the machine, sensor type, and the specific measurement in focus — ranging from simple alerts, like low or high-value alarms, to complex trend measurements and statistical models. Further amplifying the capabilities of IoT systems is the integration of artificial intelligence. Through AI models trained on historical data, potential future issues can be forecasted, and targeted areas for enhancement can be pinpointed with heightened accuracy.
Specifically, within the realm of pneumatic conveying systems, AI’s integration becomes a game- changer. It aids in preemptively identifying potential challenges – be it pipeline blockages, material inconsistencies, rotary valve rotor wear, or issues with dust collectors.
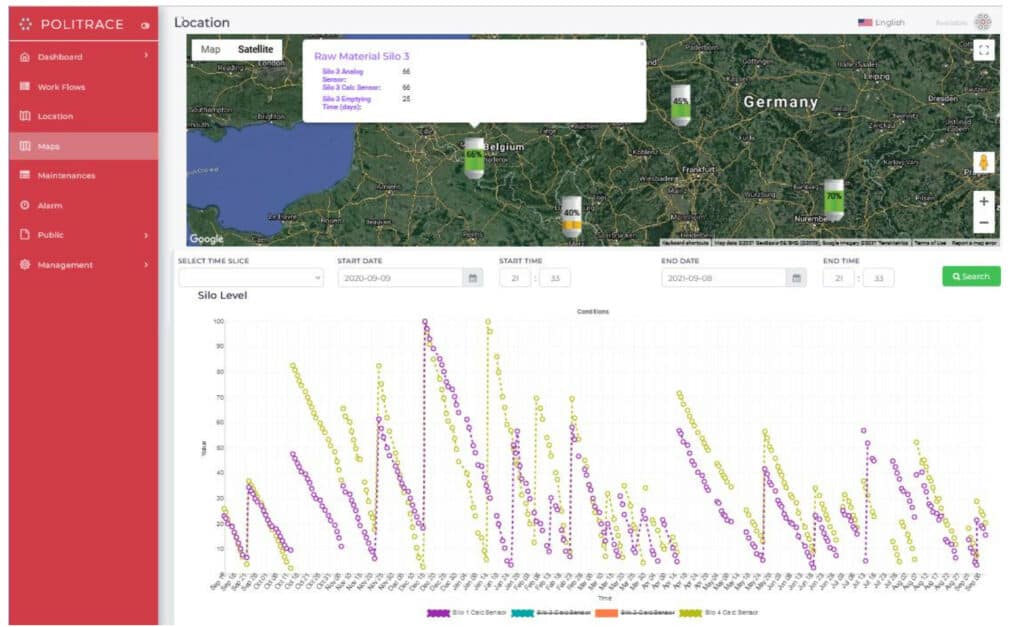
Conclusion
In the rapidly advancing world of industrial automation, recent developments in pneumatic conveying systems have been particularly transformative. With global emphasis on sustainability and green technologies, the need to establish energy-efficient systems has never been greater. The role of digital twinning in these systems is central to this transition, offering unparalleled insight and optimization opportunities. Data analytics and AI, as explored in this paper, form the backbone of this digital evolution, paving the way for predictive maintenance and enhanced operational efficiency. Yet, the successful integration of digital twinning into pneumatic conveying isn’t solely a function of technology. It hinges profoundly on a deep-rooted understanding of pneumatic conveying systems. Only with a comprehensive grasp of these systems can one craft and implement effective digital twinning solutions. As industries progress and green technologies become the standard, the interplay of expertise in conveying systems and advancements in digital tools will be crucial for a sustainable, efficient future.
References
1. Klinzing, G.E.; Rizk, F.; Marcus, R.; Leung, L. Pneumatic Conveying of Solids: A Theoretical and Practical Approach; Springer Science & Business Media: Berlin/Heidelberg, Germany, 2011; Volume 8.
2. Mills, D. Pneumatic Conveying Design Guide; Elsevier: Amsterdam, The Netherlands, 2003.
3. McGlinchey, D. Characterisation of Bulk Solids; John Wiley & Sons: Hoboken, NJ, USA, 2009.
4. A. Fuchs, P. Wypych, D. Hastie, I. Frew & H. Zangl (2007) Nonintrusive Monitoring of Slug Sequence and Flow Stability in Dense-Phase Pneumatic Conveying, Particulate Science and Technology, 26:1, 2-14, DOI: 10.1080/02726350701758961
5. Adriano Gomes de Freitas, Ricardo Borges dos Santos, Luis Alberto Martinez Riascos, Jose Eduardo Munive- Hernandez, Shibo Kuang, Ruiping Zou, Aibing Yu; Experimental design and optimization of a novel solids feeder device in energy efficient pneumatic conveying systems, Energy Reports, Volume 9, Supplement 9, 2023, Pages 387- 400, ISSN 2352-4847, https://doi.org/10.1016/j.egyr.2023.05.270.
6. Mohd Javaid, Abid Haleem, Rajiv Suman. Digital Twin applications toward Industry 4.0: A Review, Cognitive Robotics, Volume 3, 2023, Pages 71-92, ISSN 2667-2413, https://doi.org/10.1016/j.cogr.2023.04.003.