After years of working closely with companies that value their material yields, Elcan has developed and engineered the most advanced sieving technology in the industry by many standards. The Hi-Sifter sieving technology allows Elcan to sieve materials down to as fine as 5um on an industrial scale, which no other screening technology can achieve continuously while maintaining high throughput rates, efficiencies, and no screen mesh blinding.
As the demand for finer particles with tighter specifications continues to grow, companies are forced to develop 21st-century products using 20th-century technologies. While air classifiers have somewhat helped service the market of fine separations, there is no denying that a sieving machine allows for much higher efficiency separations. Elcan Industries’ superior line of sieving equipment does this, coupled with over 30 years of experience running the equipment while helping companies achieve yields of over 95%.
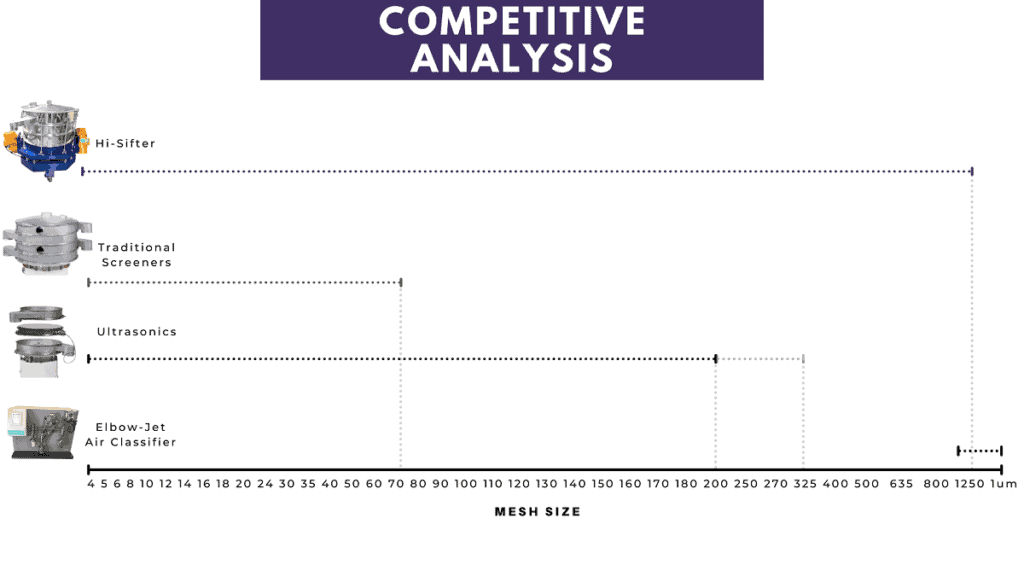
Ultrasonic Sieve VS Hi-Sifter Sieving Technology
Sieving technologies, like ultrasonics, traditionally stimulate each wire within the mesh to vibrate independently from the machine. Where ultrasonics falls short is that it will not work with coarse or ultra-fine mesh. Ultrasonic sieving machines are unlike the Hi-Sifter because they require external hardware, and damaged screen mesh is highly costly to repair (not to mention lengthy lead times). The Hi-Sifter, however, allows the user to stock their screen cloth in-house, and if it needs to be replaced, the user can change the mesh by themselves in less than 15 minutes.
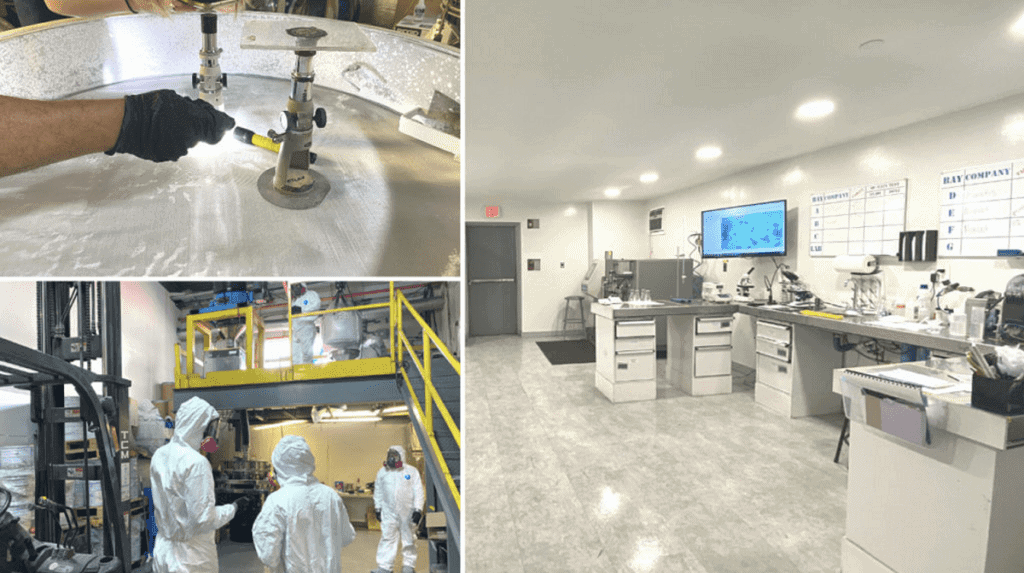
Testing Material at Elcan Industries VS Other Facilities
The most notable difference between testing at Elcan and other facilities is that when companies come to test material at Elcan, hundreds of pounds, if not thousands of pounds, are tested on the various sieving technologies. Other companies typically run 60-second testing (yes, that’s right, 60 seconds) on their equipment and conclude right then and there that this is how the material will perform over an entire production day year in and year out. This is not an efficient way of benchmarking performance by any usual production standard, and what sets Elcan apart is that Elcan conducts extensive testing to prove the entire process with the highest efficiencies and yields possible. Other companies want to sell machines based on their 60-second testing, and when their output does not meet the same rates as the “60-second test”, they tell the customer to “buy more machines.” That is why the saying around Elcan is that we offer companies RESULTS, not promises and for potential customers: never fall for 60-second testing.