If you work in the baking industry and are curious about how you can further improve the quality and purity of your product, as well as reduce risks of metal-related recalls, then you are in the right place – this can be done with magnetic separators.
In bakeries, there are 5 primary locations where the presence of magnetic separators is crucial for food safety. These include:
- Incoming flour blowlines
- Minor dry ingredients and mixing
- Minor liquid ingredients and mixing
- Finished liquid/batter ingredients
- Sprinkling & topping
Different locations have their own risks and levels of contamination, so a suitable magnetic separation design is a must! Luckily, we have a range of Magnattack® magnetic separators suitable to these locations which will effectively increase your metal fragment controls.
Let’s have a look at each location and the magnetic separators suited.
Magnetic Separators for Incoming Flour Blowlines in Bakeries
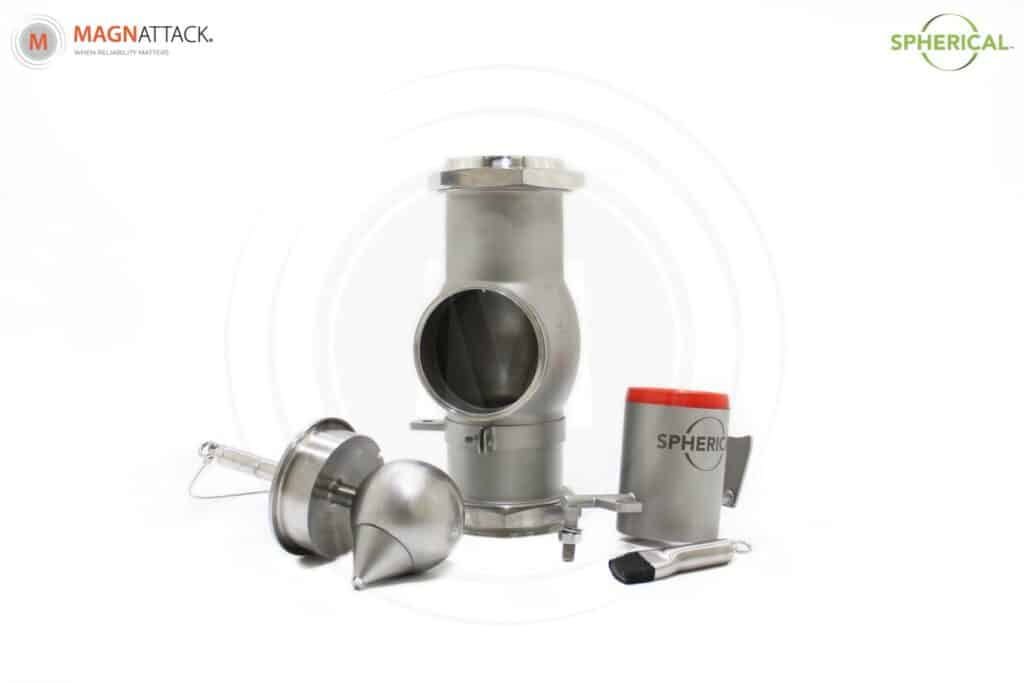
The Magnattack® Spherical Pneumatic Transfer Magnet effectively collects and retains contaminants such as magnetic stone particles, work hardened stainless steel and magnetic dust, from high-velocity, dry product lines, without experiencing bulk density changes and pressure loss.
The Spherical Magnet is suitable for high velocity and large volume vertical installations in blow, vacuum, gravity, & pneumatic transfer lines. It is a more effective, sanitary, and aerodynamic alternative to outdated Bullet Magnet-type designs. The aerodynamic design of this magnetic separator prevents blockage of product and minimizes product particle breakdown.
The Spherical Pneumatic Line Magnet suitable for products such as sugar, flour, salt & semolina.
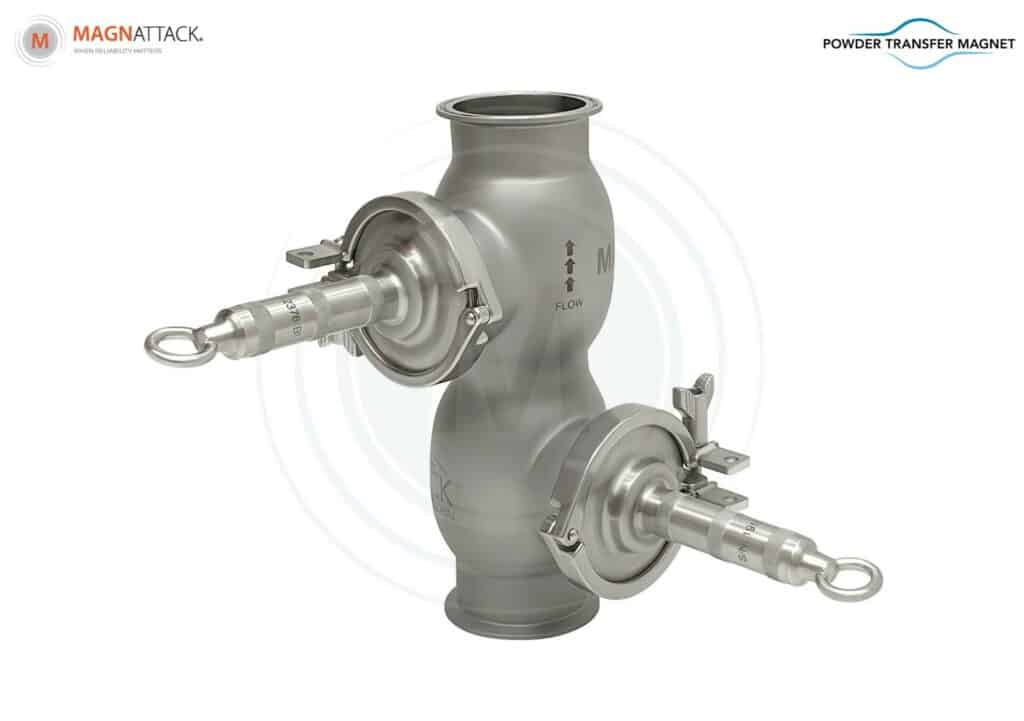
The Powder Transfer Magnet also provides highly efficient separation of metal fragment contamination without experiencing bulk density or blockage problems.
This magnetic separator features high-intensity, +11,000 gauss Acutex® Probe Magnets, configured to remove weakly magnetic contamination and work-hardened stainless steel fragments and stone from horizontal pneumatic transfer lines, thus greatly increasing food safety control and product purity.
Magnetic Separators for Minor Dry Ingredients & Mixing
Minor dry ingredients are often overlooked when the mixing process is undertaken, however, it is a common source of magnetic contamination in baking products.
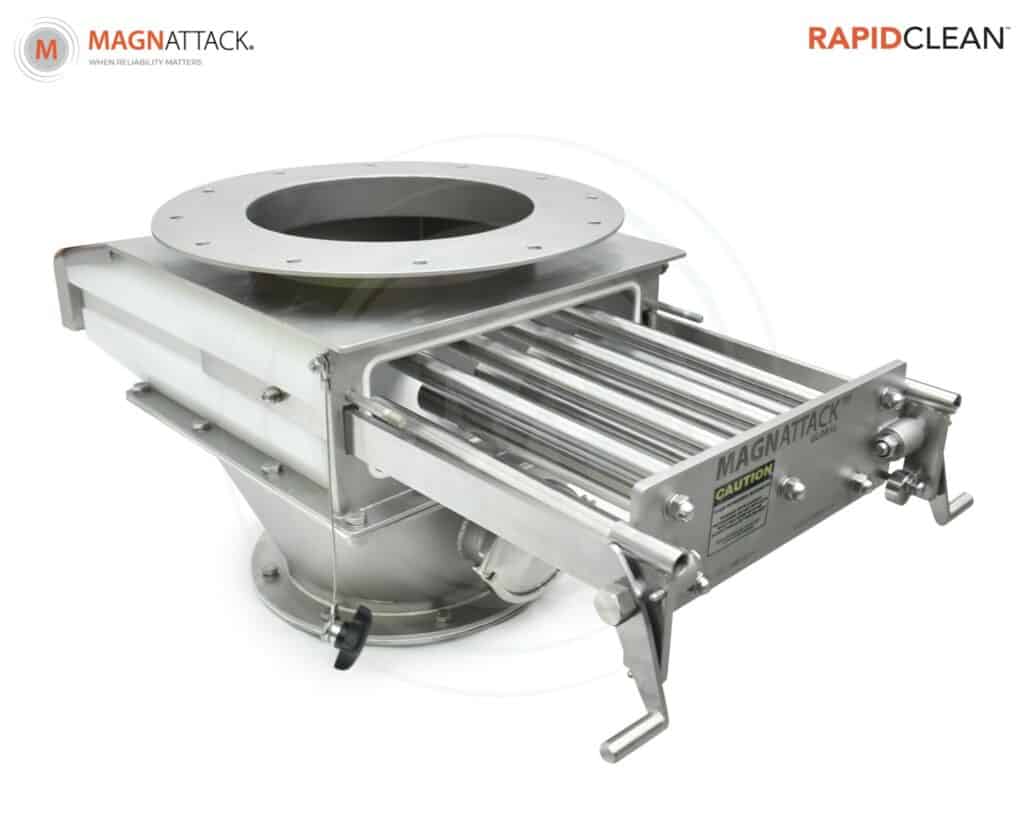
The Rapidclean® Grate Magnet can be installed at bag tipping locations to extract foreign metal fragments before they enter the mixing process.
This grate magnet was originally designed to overcome disadvantages experienced with conventional grate magnets in the food industry, including stainless steel magnet sleeves, safety issues, and cleaning difficulties. It stands out from other grate magnet designs with its sanitary, dust-tight housing and a cleaning operation that is performed wholly outside of the product stream, reducing recontamination risks. The Rapidclean® can be supplied with the Rapidclean® Cleaning Tool, which allows for effective cleaning of each individual magnetic bar.
The Rapidclean® system uses a combination of various bar diameters, door designs, and sizes to suit many variables. Units can be custom-made to suit your individual applications.
In minor dry ingredients and mixing applications, for blowlines above 2 inches, we recommend installing the above-mentioned Spherical Magnetic Separator.

For smaller line applications, we recommend a custom Magnattack® Round Pipe Separator. This magnetic separator is specially designed with extra high strength at the base of the magnet – this is the point at which metal contamination typically passes through the pipe in these types of applications. This extra strength and positioning ensures that magnetic fragments are less likely to pass through.
Magnetic Separators for Minor Liquid Ingredients & Mixing
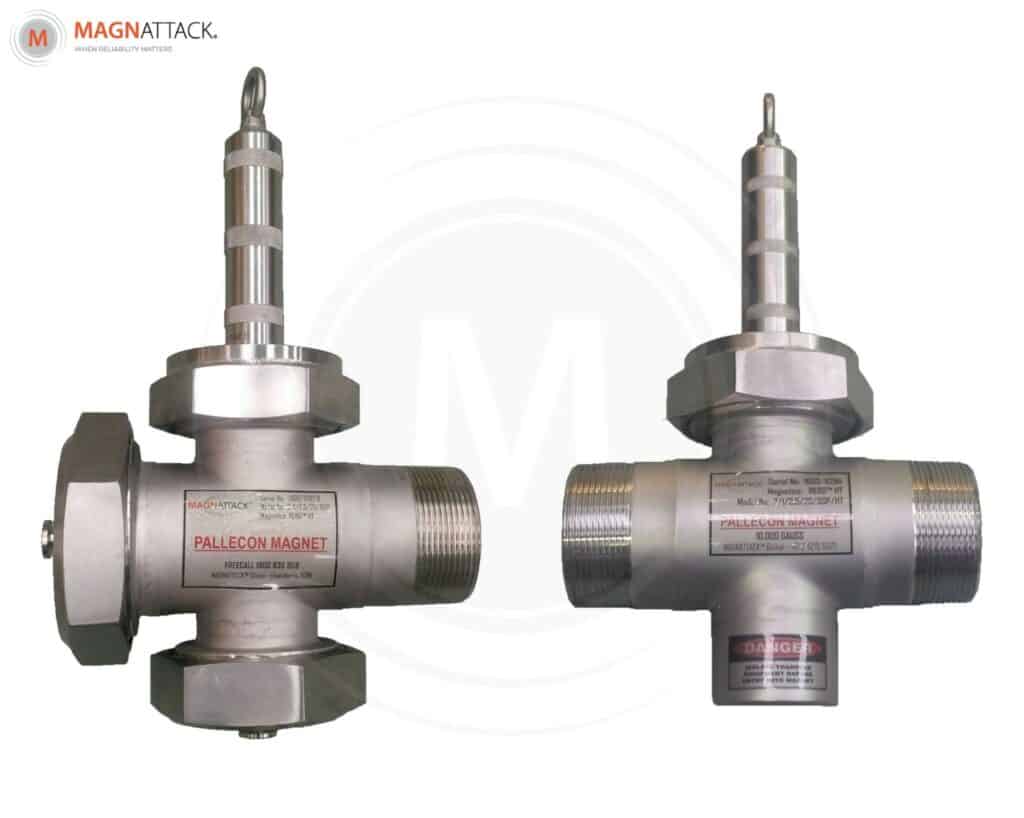
Minor liquid ingredients are frequently used in the baking industry and are often a source of metal fragment contamination. Magnattack® have developed a simple but very effective ‘bolt on’ magnetic separation solution for removing fragments from minor liquid ingredients. The Magnattack® Pallecon Outlet/Tote Magnet is the ideal solution for extracting metal contamination from this application.
This magnetic separator provides effective indication and retention of metal fragments from liquids as they exit/discharge from tote bins, large containers, and pallecons.
As metal fragments are often present in a wide variety of liquids such as oils, chocolate, egg whites, and syrups, these magnets enable thorough inspection and control of incoming/outgoing materials and early detection.
Magnetic Separators for Finished Liquid/Batter Ingredients in Bakeries
For final protection of finished liquid or emulsion ingredients in the baking industry, such as batter mixes, chocolate, oil, and pie fillings, we have two magnetic separators which excel in these applications.

The Emulsion & Slurry Pipeline Separator is designed for thick, viscous slurry products, and includes powerful above-mentioned Magnattack® Acutex® Probes.
These probes have a distinctive lachrymiform (or teardrop) shape, allowing for very smooth transition of viscous products to move around the magnet with minimum resistance to flow. Maximum product to magnet coverage is achieved without causing leaks, blockages, and pressure problems.
The peak (or V-section) of the probe is faced towards the oncoming product stream, ensuring that collected magnetic fragments are washed to the back of the probe and safely retained until cleaning operations are underway. This feature greatly reduces the risk of recontamination caused by the impact of the product flow dislodging the collected fragments and reintroducing them back into the product stream.
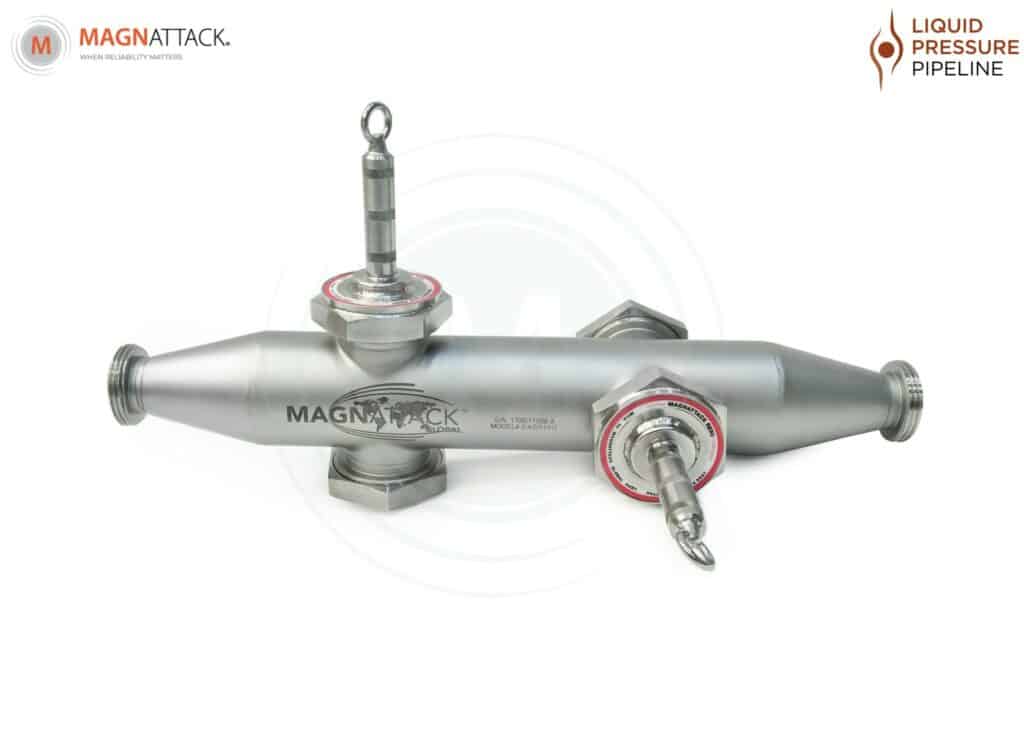
Another magnetic separator which is designed for liquid applications in the baking industry is the Magnattack® Pressure Pipeline Separator.
This magnetic separator is engineered to efficiently extract magnetic fragments (including work-hardened stainless-steel) from liquid food lines.
The system features a single or double set of powerful +11,000 Gauss magnet elements which intercept the flow of product and securely retain foreign metal contaminants. This magnetic separator achieves efficient separation without leaks, blockage, or distortion, with minimal resistance to product flow.
Magnetic Separators for Sprinkling & Topping Baking Industry Applications
There are two types of magnetic separators we recommend for the sprinkling & topping applications in the baking industry.
The above-mentioned Magnattack® Round Pipe Separator is a great choice for toppings that are vacuum transferred, or scooped into a hopper to sprinkle.
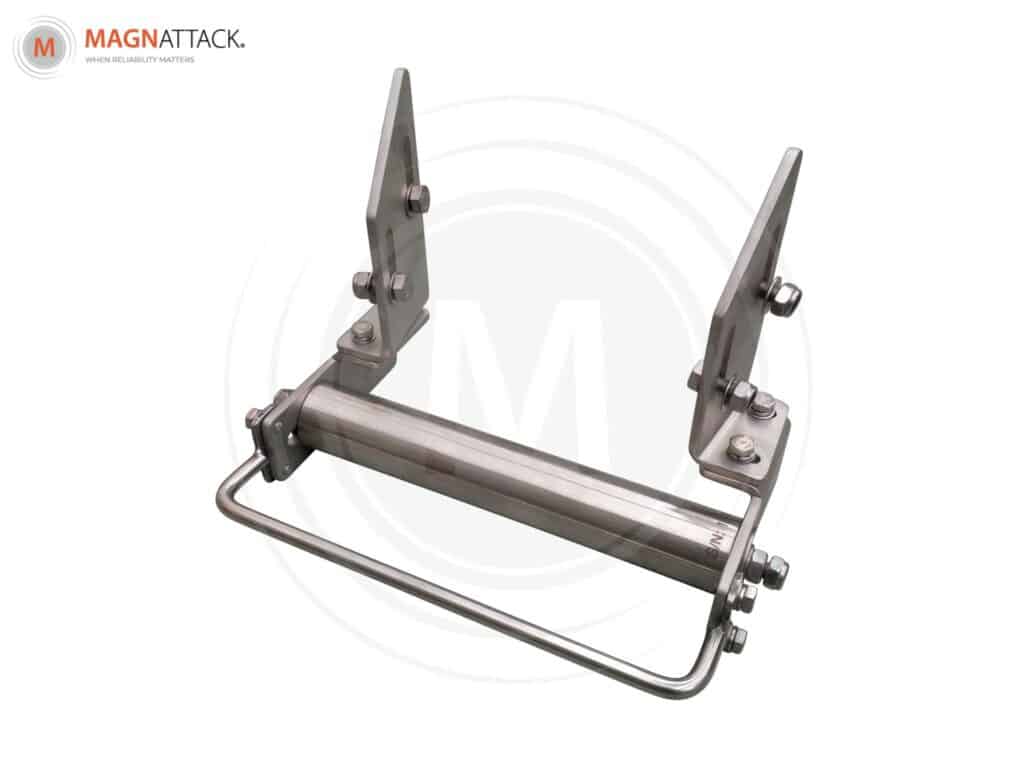
For applications where toppings are simply sprinkled, we recommend installing a Roller Bar Separator. This magnetic separator is designed to split the flow of the product and maximize product-to-magnet contact. It effectively extracts splinters of stainless steel, magnetic stone fragments, and >98% of tramp iron and ferrous fines from dry products.
The Rollers/Bars can be rotated 180° to view collected contaminants when mounted on a bearing and are available in 35mm, 51mm, and 63mm diameters.
These magnets are perfect for installing at the point of discharge at the end of conveyors, and have optional complete bracketry systems for easy handling. This allows operators to lift out and away from the process flow for cleaning, reducing risk of decontamination.
For further information on magnetic separators suited to the baking industry, or for your specific application, contact the friendly Magnattack® team today.
Magnattack® Global – When Reliability Matters