The patented Intell-I-Mag monitors ferrous contamination of incoming ingredients, detects equipment malfunctions before scheduled cleanings, ensures fully saturated magnets are cleaned before metal events occur, reduces shutdowns for premature magnet cleaning, and confirms the separator is always working at peak performance, capturing weakly magnetic materials such as work-hardened stainless.
Real Time Monitoring for Peak Magnetic Performance
- Internal sensors monitor tramp metal saturation levels and alert staff before an incident can occur – once a magnet reaches the designated level, it notifies plant personnel of required cleaning or can activate the automated self-cleaning system
- Oversee vendors during unloading for earlier metal detection to reduce damage in the production process
- Avoid challenges caused by equipment failures, inadequate magnet cleaning intervals, or inaccessible equipment
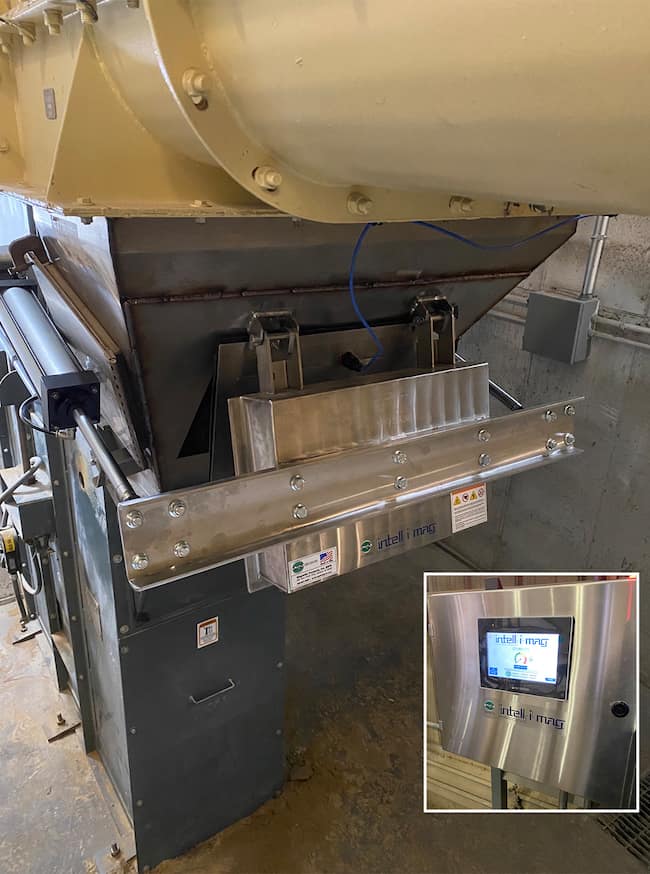
Customized Reporting for Quality Compliance Initiatives
- Data collection improves analysis of magnetic separator performance, including magnet saturation, cleaning alerts, temperature monitoring, cleaning cycles, and position location
Saturation Level Indicators
- As captured metal increases and magnetic performance decreases, LED signal indicators signal separator saturation – green, red, and yellow
Industry 4.0 and IoT Ready – Magnet Metrics Controller
- Industry 4.0 compliant PLC controller allows for communication between controller and network for remote magnet monitoring and control
Built for the Harshest Environments
- Controllers are rated for appropriate installation environments
Intell-I-Mag will revolutionize the way you use magnetic separators in your facility and reduce the risk of product recall saving millions of dollars.