Increasing the service life and prolonging the service life of screen cloths can therefore result in significant savings, both directly by reducing the cost of constantly procuring new screen cloths and indirectly by reducing plant downtime and maintenance work. There is therefore a strong demand for wear-resistant screen cloths. Allgaier supplies new types of wear-resistant screen cloths that offer a service life several times longer than that of previous standard cloths.
For obvious reasons, operators of screening machines are interested in ensuring that the screens, screen decks, or screen cloths in the machines have the longest possible service life. After all, if the meshes fail, the production process has to be interrupted, there is a loss of production, the machines have to be dismantled or opened, and the broken screens have to be replaced. So, in addition to the simple cost of procuring new fabrics, there are costs associated with production downtime and assembly work, as well as possibly the resulting after-treatment of the defectively manufactured product quantities. The price of a screen with twice the service life compared to two screens with a single service life can therefore already bring significant advantages for operators of screening machines.
There are various ways to extend the service life of screen cloths. For example, instead of standard 1.4301 (304) wire, screen cloth can be made from spring-hard 1.4310 AISI 301) steel wire or also from duplex 1.4462 (AISI 318 LN) steel, both of which have higher material hardnesses than pure austenitic stainless steels. The problem is that meshes made of such harder steel grades are not available in the full variability of mesh sizes and wire thicknesses. They are therefore not in stock and have to be specially produced as required, in as large a batch as possible, otherwise high manufacturing and delivery costs are incurred, also because of the higher material price. In addition, the processability of duplex steel wire is limited for very fine mesh sizes and wire thicknesses.
Consequently, the respective meshes made of wear-resistant steels are not available for all needs for screening abrasive products or can be supplied quickly and in small quantities and at the same time are inexpensive.
Other methods of increasing wear protection, such as coatings, have not proved successful in industrial practice because of the risk of detachment of the coating material and the resulting product contamination. Plastic fabrics, on the other hand, are only used in special applications.
In order to enable fast availability as well as low-cost deliveries, screen cloths for the market are produced “in stock” in large quantities with a wide variability of mesh sizes. Depending on the mesh sizes, graded wire gauges are used to produce the meshes, the diameters of which have become established for each mesh size and vary only slightly. In order to meet the requirements for availability, price and delivery times, sieve meshes made of stainless steel 1.4301 (AISI 304) are mainly offered for sieve applications. Fabrics made of this stainless steel exhibit sufficiently good corrosion resistance for frequently dry applications. However, they are only moderately wear-resistant.
Consequently, screens made of 1.4301 usually have a shorter service life, especially in applications for screening highly abrasive products. Examples of such abrasive products are abrasives, quartz sands, slag granules, volcanic sands, waste glass granules, fireclay, zircon, perlite and many others. The service life of screen cloths for such applications can vary from several weeks or months to, in extreme cases, only a few days. Coarse and freshly crushed products often wear more than rather fine products, while the screen cloths in vibrating screening
machines are often more abrasively loaded than, for example, cloths in planar screening machines or tumbler screening machines.
The above-mentioned problems are solved in many cases by the new wear-resistant screen cloths from Allgaier Process Technology. Allgaier supplies corrosion-resistant screen cloths made of almost all austenitic stainless steel grades with a service life increased by a factor of 2 to 3.
Production of wear-resistant screen fabrics
The novel meshes are treated by a special gas-based process for which, depending on the application, the reactive atmosphere in the process of treatment is varied in terms of pressure, temperature control, gas composition and concentration, and treatment duration. This leads to a very significant increase in the wear resistance of the wires of the screen cloth. Due to the application of gases in the process, there is a complete influence on the entire wire surfaces of the already woven screen fabric, even the surfaces touching at the crossing points of the wires. The intensity of the treatment by means of the above-mentioned process parameters is carried out as a function of the wire thickness of the fabrics, so that the ductility of the individual wires does not suffer due to possible material embrittlement and the fabrics can continue to withstand the heavy loads in vibrating screening machines. There is no negative influence on the dimensions of the meshes or wire thicknesses, and thus no negative effect on the accuracy of the meshes and the screening quality that can be achieved as a result. The corrosion resistance of the stainless steel mesh is not negatively affected by the methods used.The new method offers the unique advantage that for common austenitic stainless steels a significant service life extension against abrasive wear is achieved. The treatment is not comparable to coating the surfaces of the wires or meshes, which would always be associated with risks of spalling
The new method makes it possible to treat meshes of any mesh size and wire gauge, such as those made of austenitic stainless steels, which are available on the market in great variety quickly and inexpensively, and to make them available as wear-resistant meshes. It is no longer necessary for wire weaving mills to purchase wear-resistant spring steel wire in order to produce woven wire cloth from it. Instead, the standard austenitic steel meshes already woven are cut to the sizes required for the individual machine or screen sizes prior to treatment. Wear-resistant meshes therefore no longer have to be purchased or stockpiled in large quantities for reasons of cost and availability. This significantly increases the flexibility of production and availability for customer applications. Wear-resistant meshes with mesh sizes or wire gauges that are not normally available are a thing of the past.
Fabrics of wear-resistant quality can be produced or supplied from wire gauges of around 80 mm. The additional costs incurred by the process are compensated for by the significantly extended service life of the patented meshes and the benefits and savings for the user described above.
Laboratory and pilot plant trials
Intensive laboratory and pilot plant trials were carried out for the development and testing of the new screens. These were carried out both with MSizer vibratory screening machines in a continuous mode of operation with screening in the material circuit and on Allgaier tumbler screening machines TSM and TSI as well as vibratory rotary screening machines of the VRS type. Model conditions were selected for the tests on the machines in the Allgaier pilot plant. As an exemplary highly abrasive test material, freshly crushed glass granules were produced in a grain fraction suitable for the respective fabric tested, but in a grain size larger than the respective mesh size, so that batch
tests without continuous material circulation were possible. The material discharge of the test machines was closed, and the product was moved on the respective screen deck during the entire test period, but not screened. Rather, only its abrasive effect on the screen cloths was investigated.
The test setup was chosen so that untreated fabrics and the new wear-resistant fabrics were subjected to exactly the same conditions. During the tests, the wear conditions were evaluated and compared at regular intervals. For this purpose, the machines were stopped after 63 hours in each case, the screen frames were removed and carefully cleaned and freed from any plugged grain. This made it possible to accurately weigh the screen frames and thus determine the mass reduction of the fabric due to wear over time. After each measurement and before continuing the test, fresh, sharp-edged glass granules were placed on each sieve. A microscope camera was used to document the wear conditions. Figure 3 shows an example of how the wear patterns of the untreated mesh (top) and the treated mesh (bottom) differ in the respective time intervals until the untreated mesh breaks after 399 hours. The treated fabric shows only minimal signs of wear at the time of the screen break of the untreated fabric.
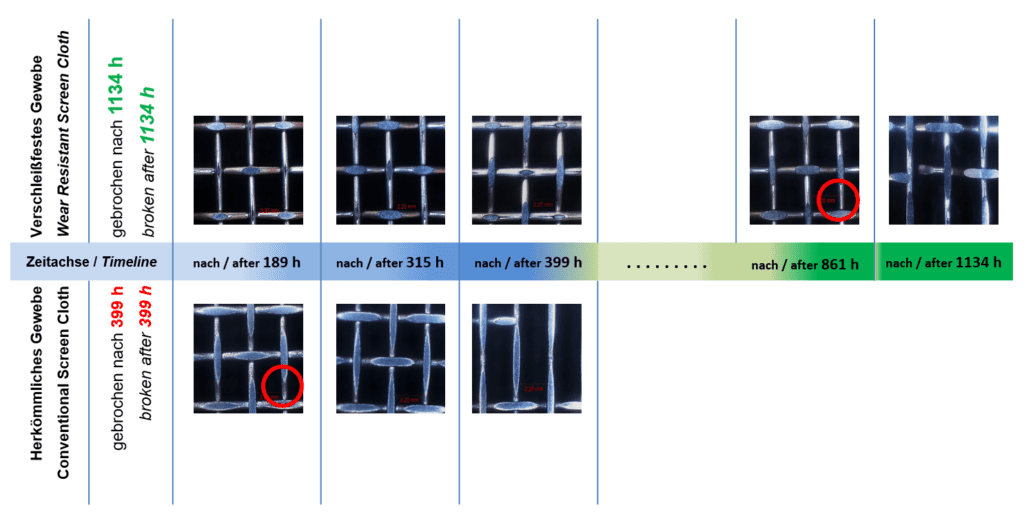
The test was also continued with the new type of wear-resistant fabric still intact until it broke, while the fabric continued to be photographed and weighed at equal time intervals. Fig. 4 shows the wear-resistant fabric at the time of rupture after 1134, i.e. another 735 hours, which corresponds to a factor on the service life of 2.84. The comparatively small abrasions at the upper bends of the warp and weft threads of the fabric can be seen, which lead to fabric breakage after a correspondingly long time.
The test procedure was carried out in the same way for a series of fabrics of different mesh sizes and wire thicknesses. The results presented above were confirmed by the large number of tests and allow a good estimate of the service life extension that can basically be achieved (service life factor).
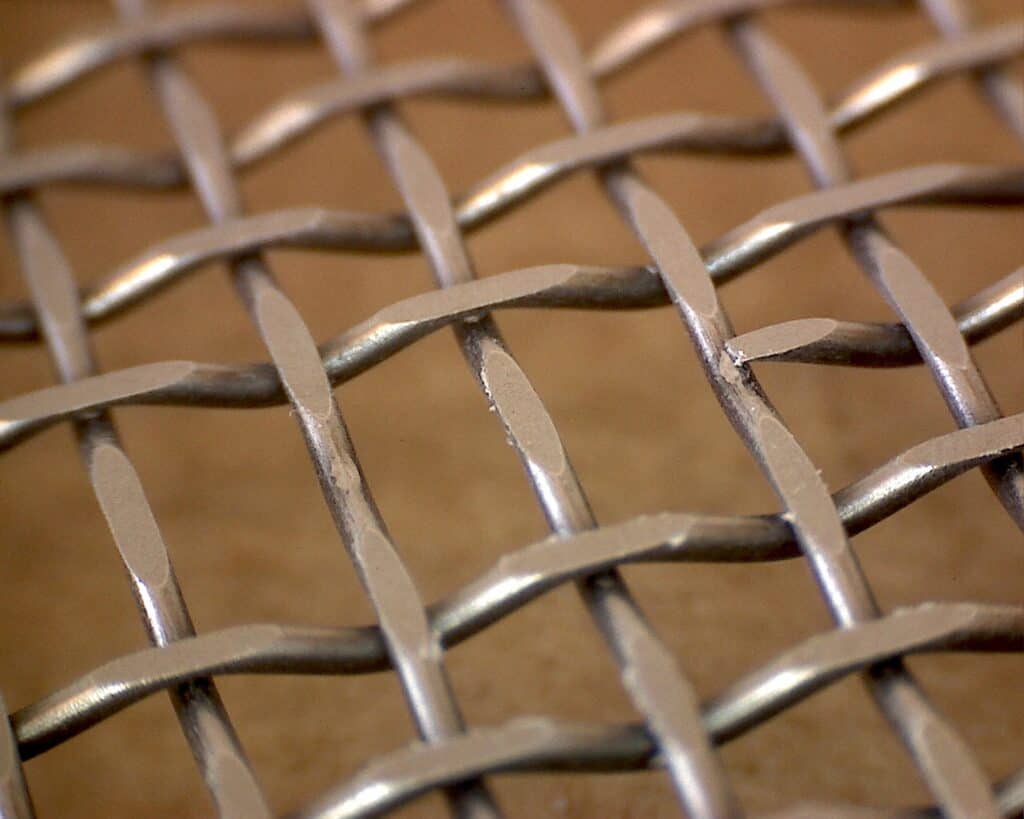
The figure below shows for the exemplary test the decrease in mass for both fabrics tested in parallel (untreated and treated) in % of the original weight over the operating time in hours. While the untreated fabric (yellow bars) shows a rapid mass loss down to 14.4 % of the original weight, the wear of the treated fabric proceeds much more slowly and only gradually gains speed until, after a mass loss of 5.4 %, it breaks only after 1134 hours. The lower mass loss to fracture compared to the mass loss of the treated fabric shows that the treated fabric is generally still intact significantly longer than the untreated fabric. However, the test was stopped at the first small defect detected. The high mass loss of the untreated fabric until breakage illustrates a generally higher risk of breakage over the entire screen area.
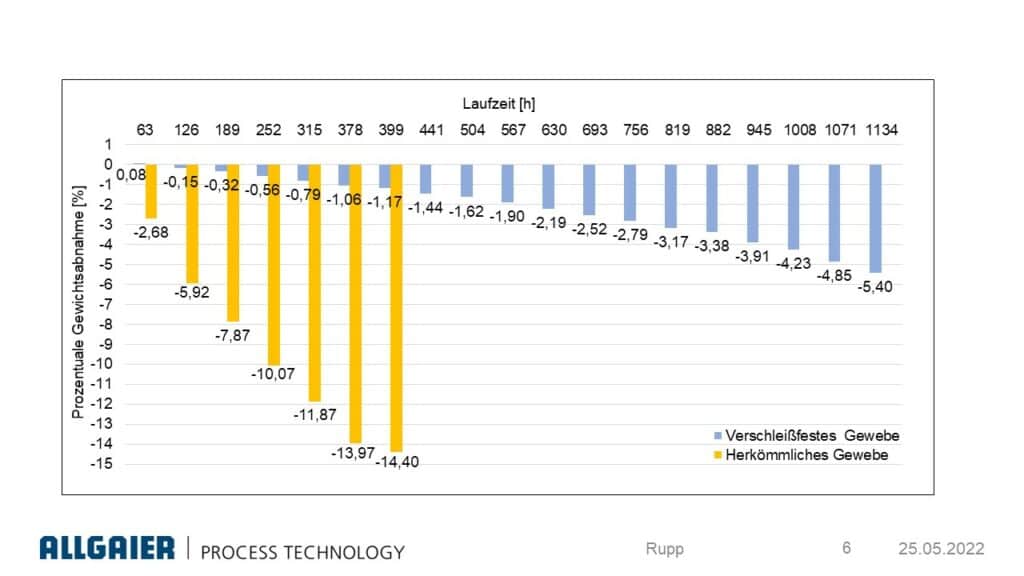
The test procedure was carried out in the same way for a series of fabrics of different mesh sizes and wire thicknesses. The results presented above were confirmed by the large number of tests and allow a good estimate of the service life extension that can basically be achieved (service life factor).
As a statement in principle, a service life factor of 2 to 3 can be predicted for the new wear-resistant meshes compared with the untreated meshes made of 1.4301 (304). Some meshes had a service life significantly exceeding these values again.
Field trials in practical industrial applications
In order to validate the results of the laboratory and pilot plant trials, initial field trials were carried out at interested customers’ plants during normal production operations. Applications with particularly abrasive materials were selected, e.g. abrasives, quartz sand, blast furnace slag, and volcanic sand.
The new wear-resistant fabrics were tested both on Allgaier tumbler screening machines and on an MSizer from Mogensen GmbH & Co. KG, as well as on a flat screening machine from a third-party manufacturer. The following mesh sizes were tested:
6.3 mm; 4.5 mm; 2.5 mm; 2.0 mm; 1.5 mm; 0.71 mm; 0.63 mm
Even though not all the results of the field tests are yet available, since many of the mentioned meshes are still intact and running, it can nevertheless already be concluded that the results from the laboratory and pilot plant tests have been impressively confirmed by the field tests and that the tendencies of a clear service life extension are clearly recognizable.
The comparison will be illustrated by an example where on a Mogensen MSizer SL2068 the top deck on one half was fitted with an untreated screen cloth and the other half with a new wear-resistant screen. Care was taken to ensure that the screenings (volcanic sand) were fed evenly over the entire width of the screener and consequently to ensure even loading of both sides of the screen and thus of the two fabrics to be compared. The feed rate was approx. 60 t/h (2x 30 t/h) in 24-hour continuous operation.
It should be mentioned in particular that the untreated wire cloth was made of spring steel hard wire 1.4310 (MW=6.3 mm; DS=1.6 mm), while the wear-resistant Allgaier wire cloth was made of austenitic stainless steel 1.4301 (304). The comparison therefore poses a particular challenge for the new wear-resistant mesh.
The figure below shows the wire cloth made of spring steel hard wire after an operating time of 1250 h, the time of failure on the left at an averagely loaded point of the screen deck and on the right at the point of screen breakage.
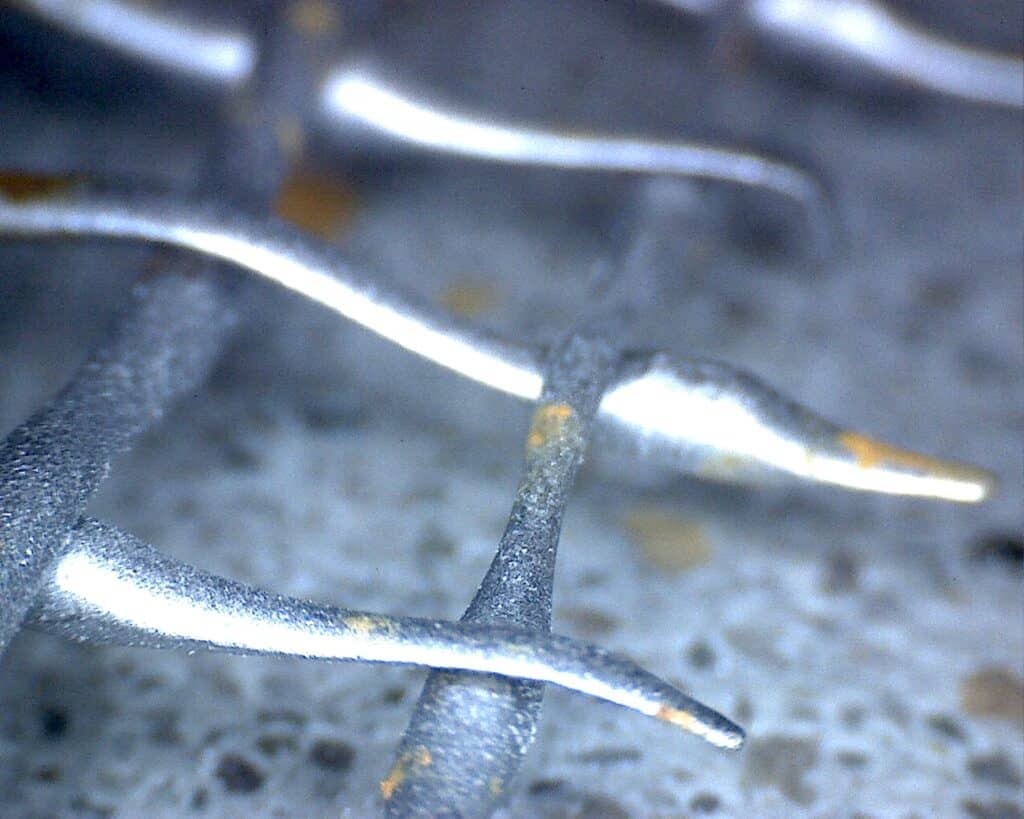
The wear pattern can be clearly seen. The wires of the fabric are initially abraded quite uniformly by the abrasive action of the screenings, preferentially at those points where the wires are not “protected” by the covering wire and thus directly exposed to the abrasive material. Wear progresses until the wire thickness is too low and can no longer withstand the stresses. Then individual wires break (Fig. right).
The figure below, on the other hand, shows the wear pattern of the new wear-resistant screen cloth at a location comparable to the figure above. The first small traces of wear can be seen, which occur preferentially on the side facing the material flow (from above in the picture). However, it can be assumed from the visual comparison that the screen will tolerate many more hours of continuous operation and will also achieve a service life factor of 2 to 3 compared to the spring steel screen shown here. We would like to take this opportunity to thank our very cooperative customer, who will continue to monitor the still intact wear-resistant Allgaier fabric and inform us at the time of the screen breakage
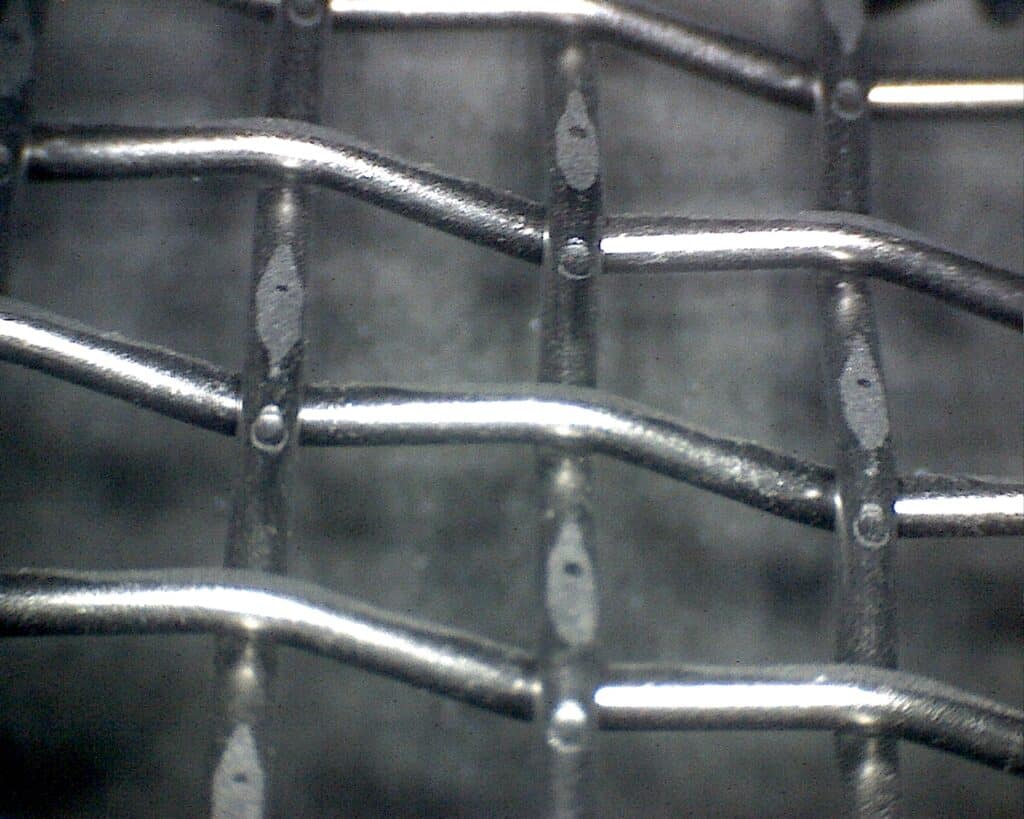
Summary and conclusions
Allgaier supplies wear-resistant sieve cloth made of austenitic stainless steels with a service life several times longer than that of conventional sieve cloth. The meshes are used in particular in applications for screening highly abrasive products and can be produced in wire thicknesses of 80 m and above.
Due to their long service life, the new wear-resistant fabrics lead to a reduction in downtimes of machines and plants as well as to a reduction in expenses for rebuilding and repair measures and reworking. They solve the problems of possible lack of availability, long delivery times or high prices of screen cloths of certain mesh sizes made of, for example, spring steel materials. Due to the new process, the wire thicknesses and mesh sizes remain unaffected in their dimensions and thus the separation quality.
The new meshes can be supplied together with new machines from Allgaier as well as spare parts for older screening machines that have been in operation for some time. It is also possible to equip screens from other manufacturers. An extended service life of a factor of 2-3 can be expected.