Areas of application for LeadingEcoSolutions
Thermal drying processes can be challenging. On the one hand, the process and plant technology must meet the respective product requirements, which primarily concerns the process and mechanical engineering design. On the other hand, these highly energy-intensive processes are in the focus of attention due to the currently critical security of supply and price explosion of the required fossil raw materials.
Thermal drying processes can involve the use of drum dryers (rotary dryers), fluidised bed dryers, fluidised bed dryers, contact dryers or spray drying variants. Up to now, these technologies have been operated primarily via hot gas systems based on fossil fuels. Driven by the current supply and price circumstances, the most efficient possible design of these processes is becoming increasingly relevant. Many years of process engineering expertise with corresponding process experience and sound manufacturing knowledge are particularly helpful here.
Experts provide individual advice
The experts at Allgaier Process Technology aim to work out the best technical/economic solution together with the plant operators. In this way, the general conditions can be agreed in an initial preliminary discussion. In an on-site measurement, the actual process parameters can then be determined and compared with the original dryer design point. The analysis of the process parameters then also serves to evaluate the individual optimisation measures and potential savings.
A question of price/performance
The adaptation of a thermal drying process can be done in many different ways. The solutions are often influenced by the structural conditions, but also by the technical process parameters. Individual consultation and case-by-case examination are therefore indispensable. In particular, various options for heat recovery can be considered. Either this heat recovery can take place within the drying process (e.g. by using the warm process exhaust air) or by integrating external heat sources from other processes. If an appropriate high-temperature heat pump is used, the available heat can even be raised to a higher temperature level so that it can be used even more effectively as dryer supply air. The dryer itself can also be modified, e.g. by changing the drum internals or converting/modernising the burner units. In combined drying and cooling units, energy can also be saved by using the effect of evaporative cooling. For example, the waste heat from the already dried, hot product is used to dry moist goods, or the heat generated by evaporation of a residual moisture content present in the solids in the area of the cooling zone (post-evaporation).
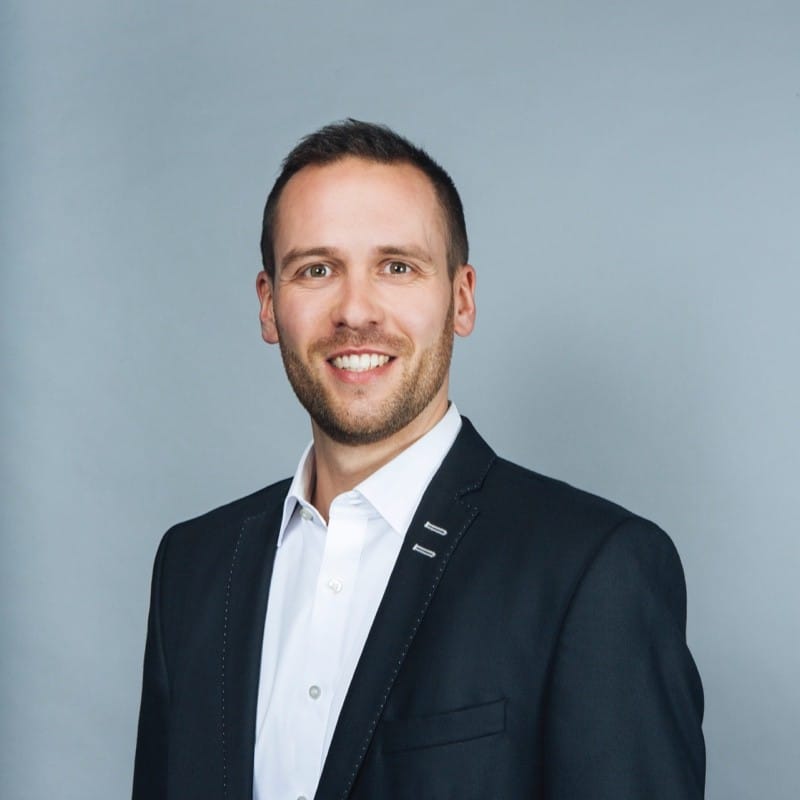
If it makes sense to replace an existing system or if a new dryer line is planned, then the possibilities of heat recovery or evaporative cooling can be taken into account from the outset in the system design. An interesting system solution is the use of the TK-D Duo drum dryer/cooler system.
Optimum conditions for low operating costs
The drum dryers/coolers from Allgaier are known as high-quality, high-performance and efficient drying and cooling systems. They are used in particular for processing free-flowing bulk materials, but are also used for sticky, clumping or highly abrasive materials. Since the drums are always individually designed and manufactured to suit the task at hand, they can be used in an exceptionally wide range of applications. Supplemented by special designs, throughput rates of 1 t/h to over 350 t/h are achieved, whereby process steps combined with drying can be integrated.
The TK-D drum dryer/cooler represents a further development of the already extremely successful Allgaier dryers/coolers of the TK and TK+ (TKplus) series. With these systems, cooling of the dried product to approx. 50 to 60 °C can already be achieved. The TK-D model takes into account the fact that in some applications, such as foundry sands or the production of ready-mix products, such as building adhesives, and also in the preparation of materials for further treatment stages in recycling processes, particularly low temperatures of the discharged dry materials are increasingly required. These are around 30 to 45° C or close to the ambient or cooling air temperature.