Hosokawa Alpine, the manufacturer of shredding machines, has developed a shredder cutting mill that produces regrind of a defined size. This flexible solution was put to the test for the first time at the MG Plast GmbH company – with great success.
Faster, more flexible and more efficient production. These are the current requirements when it comes to recycling plastic waste. Intelligent system concepts can substantially increase the productivity, for example of the material feed or comminution.
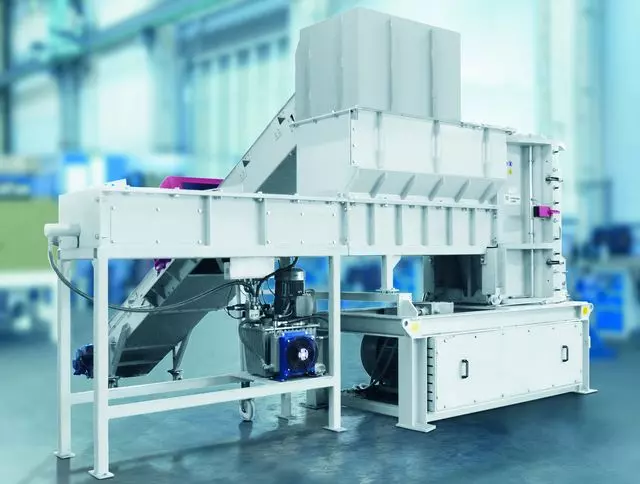
Hosokawa Alpine faced this challenge: “The requirements of our customers were clearly defined. They wanted an automated and cost-efficient solution which can be implemented flexibly and which takes account of the cramped working space”, says Jörg Krause, Head of Engineering at Hosokawa Alpine.
With the shredder-granulator Polyplex PPC 50/120, Hosokawa Alpine has developed a novel solution for the comminution of all kinds of plastic materials which is convincing due to the uncomplicated material feed, low space requirement and significantly reduced downtime.
Creating added value for the customer
The Hosokawa Alpine Polyplex PPC 50/120 is ideally suitable for demanding recycling applications and offers numerous advantages. The new machine concept combines a vertical shredder rotor with a granulator rotor. The innovation: end products with a fineness down to 5 millimeters can be produced in one single comminution step. The machine design allows the feed material to be non-uniform in shape. Small trimmings can be fed together with heavy machine purgings or large-volume blow moldings.
Another advantage of the vertical rotor shaft is the easier access to grinding chamber, rotor and knives. Subsequent to successful tests in our own application testing center, the next step is to validate the new development in real operation on a customer’s premises. Owing to the excellent industry knowledge as well as the optimum production conditions on site, the machine was integrated into the production process at MG Plast GmbH.
New ideas in demand for efficient recycling
At its headquarters in Bodenwöhr in Bavaria, the company processes production waste from the plastics processing industry and offers its customers a reliable recycling method for sprues, overproduction articles and rejects. As a medium-sized company, MG Plast is always on the lookout for future-oriented solutions in order to remain competitive on its own business sector.

“When Hosokawa Alpine asked us, we were very keen to find out to what extent the new shredder-granulator can boost day-to-day operations, and we agreed to be a part of this project”, says Michael Gleixner, Managing Director at MG Plast. Installation and commissioning on site were organized by staff from the technical departments of the recycling division.
Fully automatic process control
During the four-weeks validation phase, the Polyplex PPC 50/120 was integrated into the recycling process of plastic production waste at MG Plast. Plastic chunks and trimmings constituted the main feed materials in this process. “The challenge was in the self-dosing of the system as well as in the size reduction of large and heavy machine purgings to granulator fineness in one step”, says Krause.
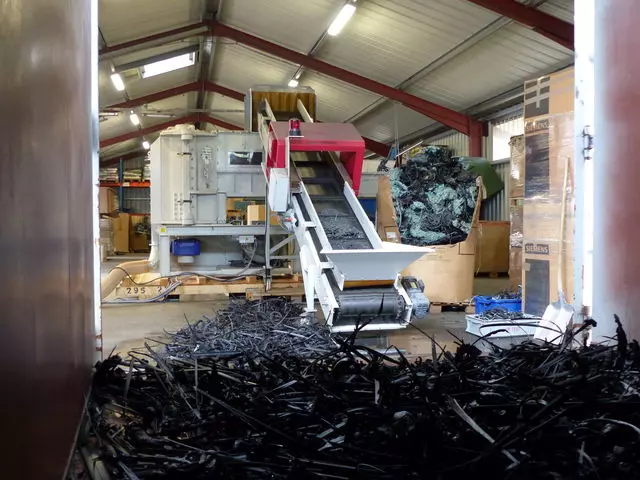
The principle of operation of the shredder-granulator is amazingly simple: the plastic purgings are charged to the machine with the aid of an intake unit. The feed material can be fed continuously or in batches A pusher then pushes the feed material towards the shredder which takes care of the preliminary size reduction. By means of gravity, the pre-comminuted material falls into the granulator zone located on the same shaft. The material is then comminuted to the desired end-product fineness and is then discharged pneumatically.
Expectations fully met
“The intelligent design guarantees significantly shorter downtime, for example during cleaning procedures”, explains Gleixner. Especially the fact that the one-stage solution from Hosokawa Alpine means that manual pre-sorting of the purgings is a thing of the past brings decisive advantages. “The personnel are on the one hand liberated from monotonous and physically strenuous tasks, and at the same time, the throughput is increased considerably”, says Gleixner.
Because only one drive is required with the combination of shredder and granulator, the energy efficiency also constitutes a significant added value compared with a two-stage solution. “For processors of machine purgings and above all mixed materials, the Hosokawa Alpine shredder-granulator is the ideal machine”, says Gleixner.