Dairy Processing
Experts for Dairy Processing

Peter Raeven Ing.
Dinnissen Process TechnologyMore than 35 years' experience in development and realisation projects as a project manager for feed, aqua feed and petfood. Working at Dinnissen for 25 years as account manager in feed, aqua feed and petfood division. Specialist in developing major projects with added value focussing on pneumatic conveying, mixing, drying, grinding and coating with liquid and powder systems.

Sylvain Bellamy
Tetra Pak Powder Process & TechnologySylvain Bellamy is currently the Commercial Director for Powder Process and Technology at Tetra Pak, based in France. With over 25 years of specialized experience in powder processing, handling, and packing, Sylvain has held various roles across the Americas and Europe, providing him with a comprehensive understanding of the global market. Sylvain's robust background in the food processing industry has sharpened his powder expertise during his years at Tetra Pak, where he contributed to developing innovative powder processing solutions. He leverages his extensive experience to drive strategic growth and operational excellence, always ensuring the delivery of cutting-edge technology and solutions that bring innovations to the market. Contact: Sylvain.Bellamy@tetrapak.com

Tim Porco
Erie Technical Systems Inc.Tim Porco is the the President of Erie Technical Systems Inc. He oversees the company's day-to-day operations, ensuring top-notch solutions for customer needs. He holds a Chemical Engineering degree from Case Western Reserve University and is an active member of the Flexible Intermediate Bulk Filling Association (FIBCA). With an extensive background in technical sales, product management, and sales management within the powder solids handling industry, Tim applies his diverse skills to develop economical solutions for clients. Tim is committed to listening carefully to customer requirements and translating them into effective applications of Erie Technical Systems equipment.

Tim Llewellyn
Flexicon CorporationTim Llewellyn is the Global Projects & Applications Engineering Manager at Flexicon Corporation, a world leader in the design and manufacture of bulk handling equipment and custom-engineered systems. He has over 20 years of experience managing and delivering complex global projects within the bulk material handling industry, including expertise across multiple sectors, including food, chemical, pharmaceutical, nutraceutical, and plastics. Tim has a proven track record of building and managing teams focused on helping clients solve their powder handling challenges. Tim holds a Bachelor of Science degree in Mechanical Engineering from Lehigh University.

Gerard van Schoten
HethonGerard van Schoten is Managing Director at HETHON, a globally active specialist in powder dosing systems. With a strong technical background and hands-on experience throughout the company, Gerard combines strategic leadership with deep process knowledge in dry bulk handling. He is widely regarded for his expertise in handling and dosing poorly flowing powders, particularly in industries requiring high precision and reliability under challenging conditions such as ATEX environments. Gerard works closely with international customers, engineers, and agents to translate complex process challenges into custom-engineered, long-term solutions. Having grown within the company from a technical role into leadership, Gerard brings a unique combination of technical credibility and commercial insight. He remains actively involved in advising on system configurations, control integration, and customer-specific adaptations—ensuring that every solution HETHON delivers is both technically sound and practically applicable. Gerard regularly supports agents and customers worldwide and is a trusted point of contact for clients seeking high-performance dosing technology for demanding industrial applications.

David Hyer
Thayer ScaleSince 2016, David Hyer has served as the President and General Manager of Thayer Scale and is responsible for daily operations. In 2013, he rejoined the company after serving as the division manager of the circuit-board test and inspection business at Teradyne. His professional experience includes senior management positions in sales and business development at Teradyne and two venture capital-backed startups. His first position was with Thayer Scale in 1985 as a college student writing machine-level code for the PI-164 instrument. David has expertise in the design and manufacture of market-leading conveyor belt scales and gravimetric feeders. With an unyielding focus on product line specialization and quality, the company's portfolio of products and customized solutions are tailored to the unique requirements of its three key segments; Food, Energy & Building Products, and Chemical & Industrial. David holds a Bachelor of Science in Electrical Engineering from Tufts University. He is married with three children and enjoys tennis, golf, and spending time on his boat.

Emre Ergun
IEP TechnologiesEmre Ergun is the Head of Sales of IEP Technologies Europe. He brings over 24 years of experience in the industrial explosion protection and prevention field, specializing in explosion suppression & isolation systems, venting (including flameless venting), and spark detection & extinguishment solutions. He is also experienced on dust explosibility testing methods, applications and relevant standards. He holds BS Chemical Engineering from Middle East Technical University, Ankara, MS Engineering Management from Northeastern University Graduate School of Engineering, Boston MA and MBA from Babson College, F.W. Olin Graduate School of Business, Wellesley MA USA. Mr. Ergun is a certified safety auditor (CSA) by the National Association of Safety Professionals, NASP.

Karen Van Aelst
Stuvex International NVKaren Van Aelst, ing., is a seasoned professional with a rich background in sales and engineering, particularly within the dry bulk handling and process industry. Over the course of 12 years, she honed her expertise in selling installations tailored for these sectors. In 2010, Karen transitioned to StuvEx, where she embarked on a decade-long journey as a sales engineer specializing in explosion protection. Her role encompassed managing sales activities in both BeLux and Germany, showcasing her proficiency in navigating diverse markets and establishing strong client relationships. Since 2019, Karen has assumed the position of Product Manager at StuvEx, where she is entrusted with the vital responsibilities of overseeing the development and market realization of explosion protection products. Her extensive experience in sales, coupled with her engineering background, positions her as a valuable asset in driving innovation and ensuring the safety of industrial environments. Karen's dedication and expertise continue to play a pivotal role in the success of StuvEx in the field of explosion protection.

Robert Meirick
Material TransferRobert brings over 25 years of experience for bulk material handling and material processing equipment to Material Transfer. At MTS, he is responsible to fostering new business opportunities while nurturing account relationships. His depth of experience and industry knowledge allows our Team to meet the growing needs of our customers as we continue to provide the highest quality systems to the marketplace.

Chuck Johnson
National Bulk Equipment, Inc.Chuck Johnson is the director of sales at National Bulk Equipment, located in Holland, Michigan. His professional experience includes over 25 years in the design, engineering, & sales of bulk material handling equipment & systems. Johnson holds a BS in mechanical engineering from Michigan State University.

Pablo Balan
Boss Products, LLCDesign Engineer, Project Manager, Territory and Sales Manager with 40+ years of experience in capture at source designs, sales and installation projects for high and low vacuum and dust collection and filtration systems and explosion and fire mitigation in dust collection systems.

Chris Brennan
Spiroflow LtdChris has been working at Spiroflow for over 10 years and is currently in the role of technical sales manager. He handles all the technical drawings and specifications during the sale and aides our drawing office while the equipment is designed, he also assists the manufacturing department with the build. His vast knowledge of powder handling and mechanical design is why he is involved in every aspect of designing our powder handling solutions.

Alex McCans
HammerTek CorporationAlex McCans is National Sales Manager for HammerTek Corporation, manufacturer of the innovative Smart Elbow Deflection Elbow. With over 10 years of experience in mechanical and pneumatic conveying of bulk solids, Alex leads the HammerTek sales team to solve conveying challenges for customers around the world. His expertise and dedication have helped establish HammerTek as a trusted leader in the industry.

Travis Young
Vortex Global LimitedTravis has over 20 years of experience in the dry bulk solids industry and is the President at Vortex, an engineering and manufacturing company that specialises in process valves and loading solutions specifically for solids handling. Travis has worked on solution-driven installations across six continents and has a strong knowledge of market-specific regulations and requirements within the industry.

John Lovatt
Marion Process SolutionsJohn has been working as a Mechanical Engineer in Mixing & Sieving Technology for over 47 years, the last 6 at Kason and is currently in the role of Technical Sales Engineer. He handles all the technical aspects of providing the Regional Sales Managers with the quotations they require to sell the AMP/AHS range of equipment globally. He also assists the RSM’S with customer queries and final deal negotiations as well as liaising with the Engineering team to ensure a smooth transition between sales and GA approval. His vast knowledge means that he also offers and provides training where required on the AMP product range of equipment across the European Sales group.

Nathan Grube
BinMaster Level ControlsNathan Grube is Regional Vice President of Sales for BinMaster covering the central United States including a ten-state area stretching from North Dakota to Texas. He joined BinMaster in 2001, already equipped with five years of experience in agricultural equipment. Grube has worked with end users, distributors, and OEMs across the US. His vast expertise covers many industries including agriculture, aggregates, cement, plastics, and mining, among others.

George Bougioukas
Acmon SystemsGeorge Bougioukas, Plant Manager of Acmon systems has over a 20 years of experience in plant process design for both mechanical and automation engineering in a wide range of industrial sectors. He has gained a unique knowhow of cross-cutting technologies and applications bringing the organization to reach a new industrial value chain era. George’s expertise includes applications ranging from reception and storage of raw materials, pneumatic and mechanical conveying, sieving, weighing and dosing, mixing, up to bagging and final product dispatch. Behind George there is a dedicated team of engineers who like him are constantly striving to improve design and performance of all plants Acmon systems has been delivering all around the globe for the last 30years on a turnkey basis.

Matthew Bailey – Technical Lead
BFM® Global Ltd.Matthew is a mechanical engineer holding an honours degree from the Auckland University of Technology and has been responsible for BFM® Global’s product development, testing and compliance programme for almost 5 years. Matt’s experience is centered on the powder handling industry with a specific focus on flexible connectors, and all the compliance requirements around them. From food to pharmaceutical and all industries in between, Matt works with our Distributor partners, end users and OEMs from Europe, Asia and the Americas to solve application challenges. He regularly attends industry tradeshows around the world and understands the complex requirements of each different market.

Gareth Meese
EriezGareth Meese works as Regional Sales Director – EMEA (Europe, the Middle East, India, and Northern Africa) for Eriez-Europe, a global leader in several key technology areas, including magnetic separation, metal detection, and material handling equipment. With nearly 20 years of experience in continuously-evolving positions, Gareth is well versed in bulk material handling applications. When Gareth joined Eriez as an Export Sales Engineer, he led several Eriez teams tasked with expanding business throughout Scandinavia, the Baltic States, and the Czech Republic. Later, as Export Sales Manager, he concentrated on growing Eriez-Europe in Russia, Europe and Northern Africa. His recent promotion expands his geographic responsibilities further with the addition of the Middle East and India. Gareth has been instrumental in pursuing Eriez’ vision and holds a Bachelor of Science in Physics from Cardiff University. Gareth is more than prepared to discuss and recommend a tailored solution for any unique bulk material handling application.

Carrie Hartford
Jenike & JohansonCarrie Hartford is the Director of Business Development and Senior Project Engineer in Jenike & Johanson’s office in California. For nearly 2 decades, she has been solving challenging bulk material flow related problems around the world. Typical projects include the analysis and design of bins, hoppers, feeders, and transfer chutes. Previously, she opened and established an engineering office and laboratory facilities in Perth, Western Australia. Internationally she publishes and presents technical papers, participates in conferences, and presents numerous short courses in the field of bulk solids flow. Carrie has a Mechanical Engineering degree from the University of California, Santa Barbara and an MBA from Azusa Pacific University in California. She is a licensed Professional Mechanical Engineer in the State of California.
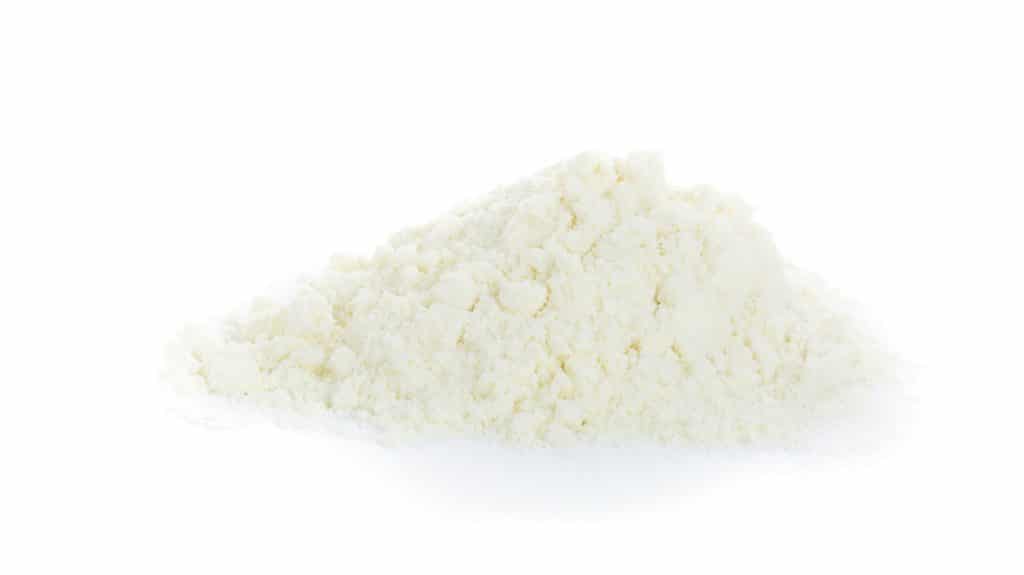
Dairy processing is the transformation of raw milk into processed milk and products. Dairy processing can benefit entire communities by generating employment opportunities in milk collection, transportation, and marketing.