As a result, there was excessive dust leakage throughout the filler room and there was significant product build-up in the joins – a major hygiene issue for a dairy plant. They turned to BFM® fitting to help find a solution.
Problem:
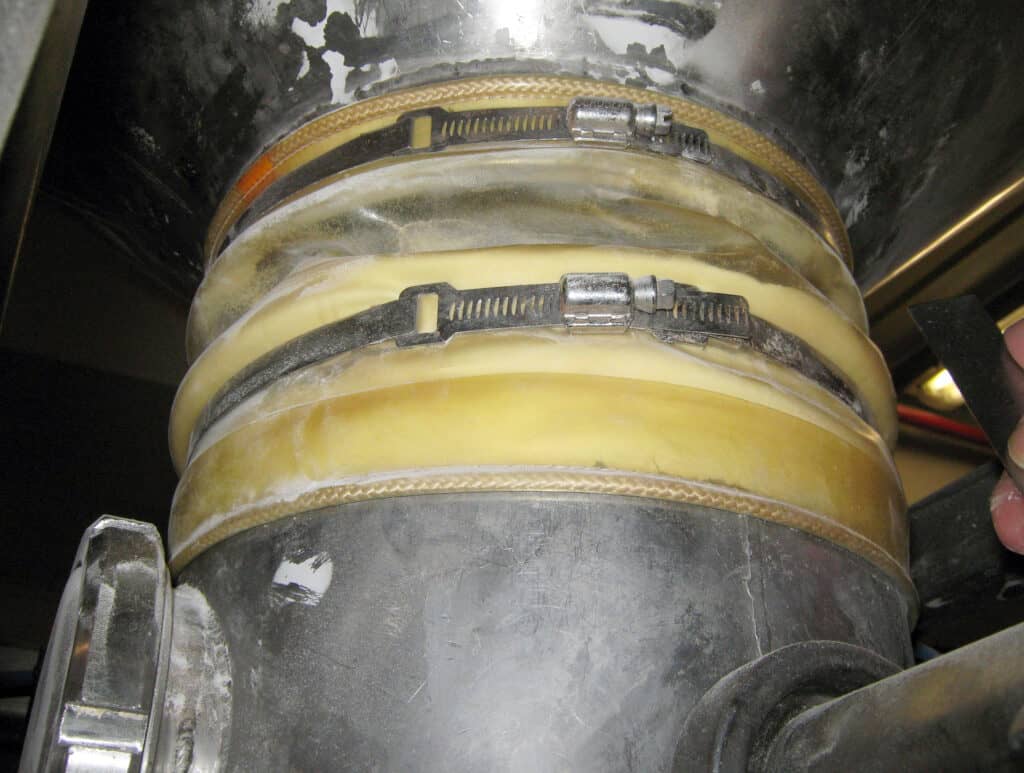
The problem location was where a vibratory discharging cone was connected to the hopper via a traditional connecting sleeve and hose-clamps. Regular operational gas purging at high pressure meant the old-style flexible connections simply couldn’t contain the powder. This caused an unhygienic environment and hours of down-time for regular cleaning.
There was also concern about the contamination point created by significant product build up between the externally fitted sleeve and hopper.
Staff found the steel strapping hose clamps were very time consuming to remove and re-fit during sleeve cleaning & replacement, and this only added to the amount of downtime being experienced daily.
Solution
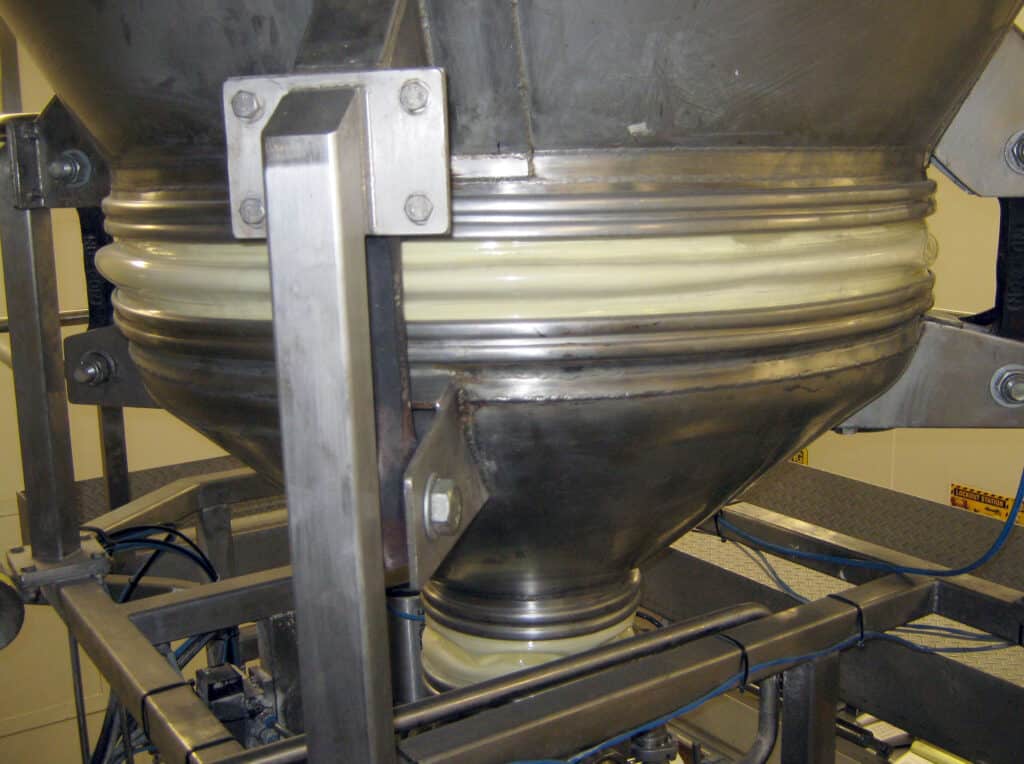
A BFM® fitting Seeflex 040E flexible connector system was installed in place of both the upper and lower connections which has created a fully sealed system. Because the BFM® fitting connectors are sealed from the inside, the pressure from the gas purging actually improves the seal, pushing them out wards and powder cannot escape.
The other key benefit of the BFM® fitting design where the connector sits inside the pipe (via the specially shaped spigot) is there is no risk of product build-up or contamination at the connector joins.
When the fittings do need replacing or removing for any reason, it’s now a quick and easy snap-fit process that can be completed within a few minutes.
Result
Since installing the BFM® fitting system, the filling room is clean and there has been a significant reduction in both downtime and replacement costs.
The contamination point has been resolved and with no more product leakage, overall plant hygiene has dramatically improved. Thousands of dollars a year are being saved by eliminating downtime for constant cleaning and complex sleeve and clamp replacement.
The filling room operators are ecstatic about how their work environment is now dust-free and a “pleasure to work in”. They no longer spend hours cleaning powder off the surfaces in the filling room or regularly removing the messy wire-clamps from the machinery to clear the product build-up between the connectors.