Part I of this series of articles How to Safely Store Combustible Dusts & Powders discussed how a hazardous area classification should be undertaken. This resulted in the assignment of a hazardous zone within or around items of processing equipment. The Part II article considered the ignitability characteristics of powders. The Part III article considered how this information should be used to ensure that fire and explosions from combustible dusts can be prevented.
At this point we have discussed the prevention of fires and explosions from combustible dusts by breaking the ‘fire triangle’ – preventing the formation of flammable dust clouds and preventing ignition sources by the installation of certified ‘special’ equipment (ATEX equipment).
However, although we have done our best to prevent these events, they can still occur. In safety language what we have done is reduced the risk of fire and explosion to a very low level. We therefore now have to deal with the ignited event. This is often known as the Basis of Safety – the whole gambit, including organisational aspects to ensure that if a fire or explosion actually occurs, we do not hurt anyone.
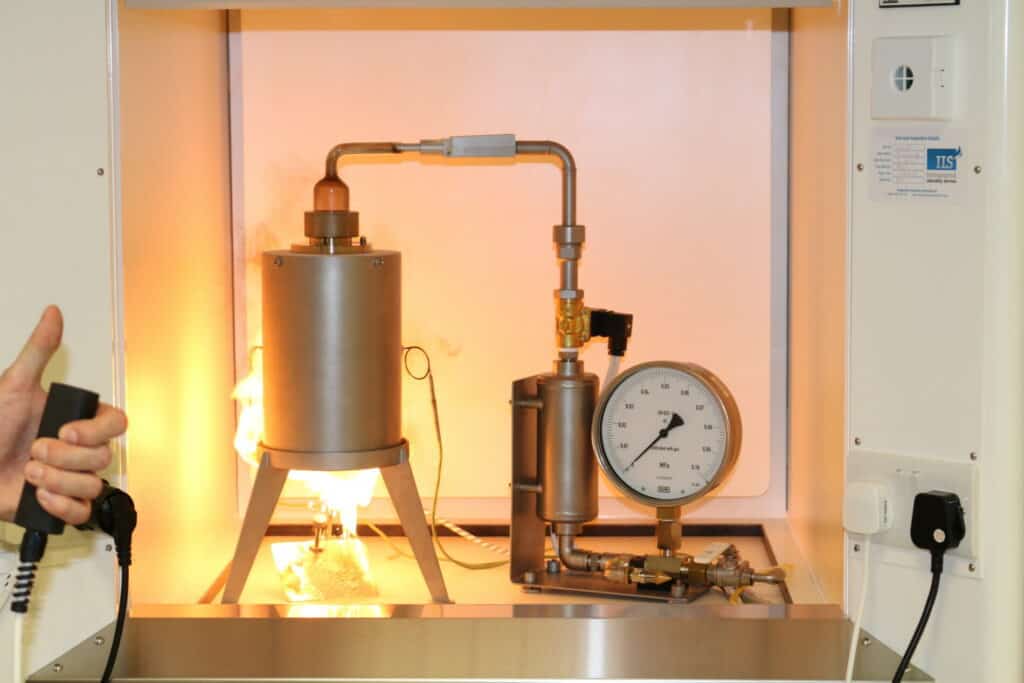
The Basis of Safety includes the Prevention of fires and explosions, and the Explosion Protection aspects, which is the subject of this article.
Explosion protection is generally achieved by one of three means:
- Containment – the effects of an explosion are contained within the equipment item. There are no external impacts of the explosion.
- Explosion Venting – the effects of the explosion (flame and pressure) are vented to a safe location.
- Explosion Suppression – the initial effects of the explosion are detected rapidly and extinguished.
With knowledge from explosion testing (the 20litre sphere test) the maximum pressure developed during the dust explosion (Pmax) and the rate of pressure rise (KSt value) are determined. Equipment can then be constructed to withstand this pressure. The containment can be constructed in two ways – the first is explosion resistant plant (the explosion effects are fully contained, and the containment system suffers no damage. Therefore, it could be cleaned out and re-used. The second type is explosion resistant. Again, the explosion is contained but the equipment may suffer some damage. The containment system may be bulged or distorted. Obviously, in such cases, the strength of the containment system will be different than the original design, and is likely to require replacement.
Normally containment as a Basis of Safety is little used in the powder handling sector – such systems are expensive to construct, but they are very effective (if designed correctly). Equipment that is routinely robustly manufactured, such as hammer mills etc often provide containment from explosion as well as containment of missiles etc.
Explosion venting is perhaps the most common protection seen in the powder handling industries. Many dust collectors have explosion venting as the explosion protection. It relies on an engineered passive system – a deliberately weak section of plant, with low inertia, which opens at very low pressures (known as PStat) very quickly and vents the flame and pressure effects to a safe area – often outdoors at high level to ensure people are not impacted during the venting. If correctly designed, the original equipment is essentially undamaged because it only ‘sees’ a much reduced pressure (known as PReduced). The PReduced and PStat are important aspects, but the area of the vent needs to be correct as well. These factors can be designed into the system to ensure effectiveness. Obviously during the venting process there may be some development of back pressure on the system, especially if the relief is ducted along tortuous ductwork runs. This has the effect of increasing the vent area required. Ideally relief ductwork should be straight and short (less than 3 metres).
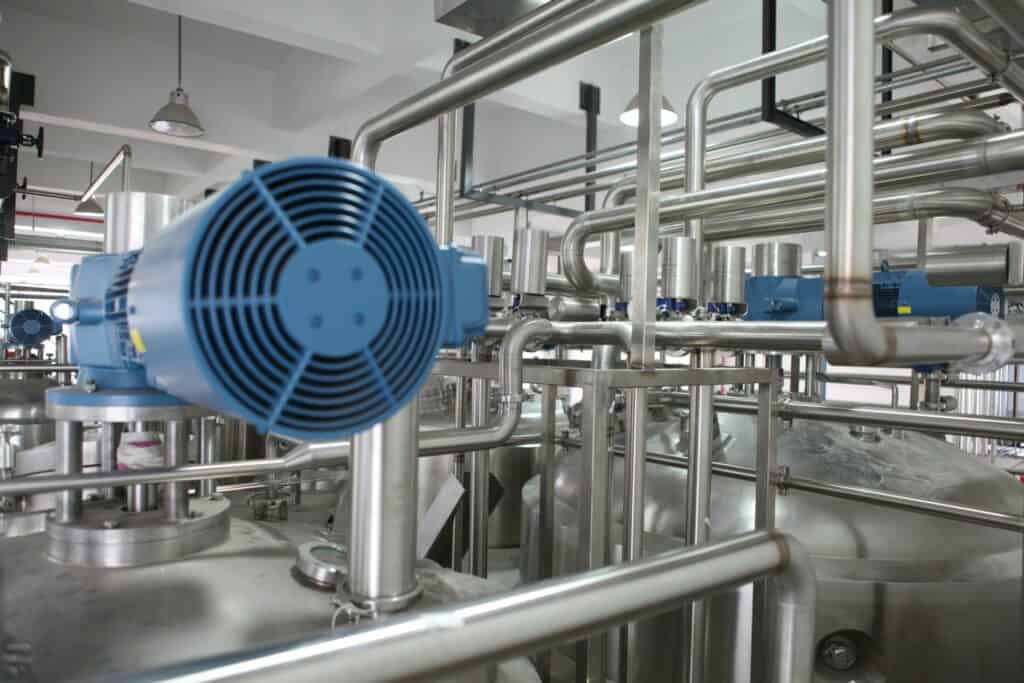
Sometimes because of the restraints described above, the explosion vent is located indoors. When an explosion is vented a large flame, combustion products and pressure emanate from the opening which can cause serious harm to people. The combustion products (and indeed any entrained combustible dust) may be toxic causing potential additional hazards. Traditionally, the area where the vent is became a cordon santitaire, with interlocked fencing preventing personnel access during operation. Now, special vents have been developed which prevent the passage of flame from the vent – so-called flameless venting. Although these prevent the flame from causing injury, the combustion gases and pressure still remain a potential hazard.
The third method, explosion suppression is becoming increasingly common. It relies on detector systems to detect the initial stages of an explosion (either pressure or temperature etc) which on activation cause the rapid injection of an extinguishant into the system. Appropriate design by specialist providers is important especially with regards to the siting of the detectors in relation to the extinguishing point.
Whichever explosion protection method adopted also has to have means of preventing the propagation of the flame and pressure effects into upstream or downstream connected equipment. Flame and pressure is like water flow – it takes the route of least resistance. If such means of preventing propagation are not installed then a series of explosions within connected equipment items may occur.
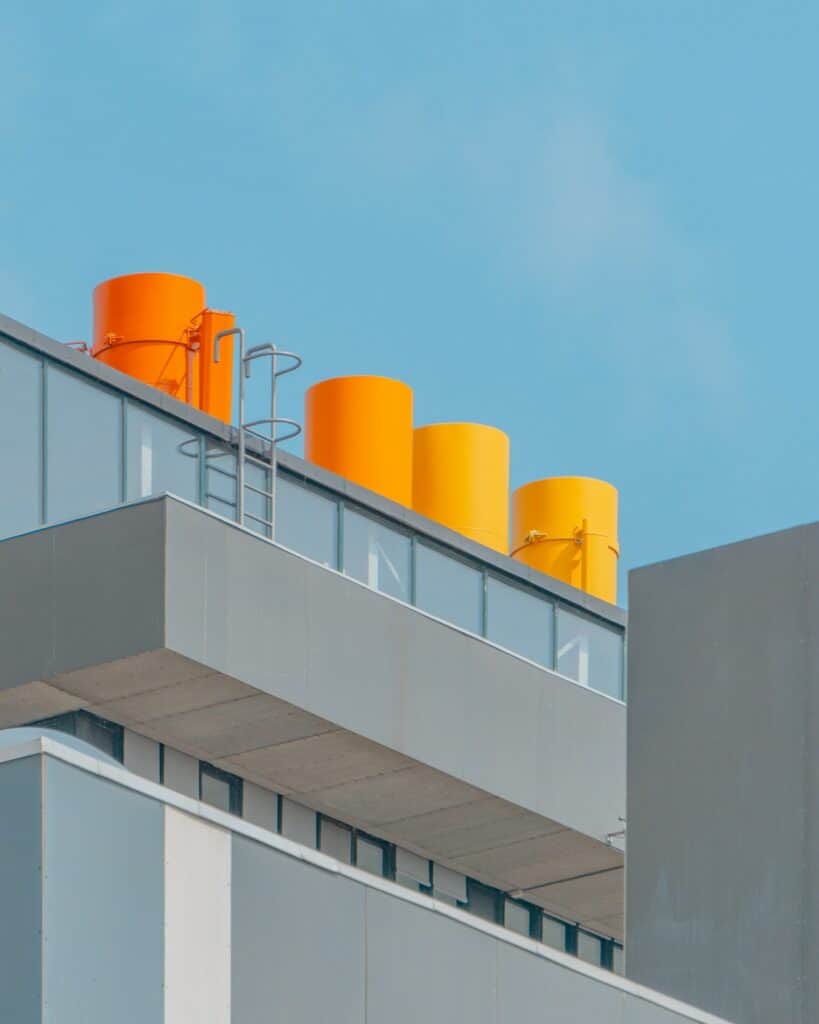
Sometimes these isolation means can be fairly simple, for example, a choke in a screw conveyor or a rotary valve. Such systems allow a plug of powder to prevent the passage of flame etc. Prevention of flame flow in ductwork can simply be achieved by a flap valve – the valve is normally held open by the extracted airflow, but reverse flow will close the valve. In other cases, it can be more complex, similar to the explosion suppression systems discussed above. Detection of the flame or pressure activates the operation of a quick acting valve to isolate sections of the plant.
Sigma-HSE is an internationally recognised process safety company with ISO/IEC 17025 accredited testing laboratories. We provide fire and explosion data: 20L, MEC, MIE, LIT, LOC, electrostatics and thermal screening. Our safety engineers are experienced in DSEAR, ATEX and DHA across many process industries.
Read: “How to Safely Store Combustible Dusts & Powders: Part I“
Read: “How to Safely Store Combustible Dusts & Powders: Part II“
Read: “How to Safely Store Combustible Dusts & Powders: Part III“