The pressure shock-resistant design of the complete grinding system up to an explosion overpressure of 10 bar(g) is the most frequently used version, which, however, is associated with a high level of equipment and corresponding space requirements.
Thanks to the ATEX-compliant Condux® Compact plant concept, the installation of a high-performance grinding plant for numerous products is now much easier, since explosion protection valves or explosion suppression devices, explosion isolators, fans, and even conventional dust filter systems are no longer required with the newly developed plant concept.
The idea of a compact grinding system is not new but existing solutions show significant disadvantages when it comes to cleaning efforts and hygienic design. NETZSCH has therefore improved the decisive points of its Condux® Compact plant concept once again: The footprint or space requirement of the compact plant is 80 % less than that of comparable standard grinding plants with the same throughput capacities. This also has an effect on investment costs, which are approximately 30 % lower. By using the newly developed CycloFil cyclone filter in the Condux® Compact system, the integrated pre-separation of the grinding stock and the recirculation of the process gas allows a filter area that is over 90 % smaller than that of comparable mill sizes. With CycloFil, the degree of separation can be adapted to the operator’s requirements by means of exchangeable immersion tubes. These features of the new system result in various advantages. For example, the grinding system can be easily integrated into existing production systems thanks to the minimal space requirement, and the necessary cleaning when changing products is extremely quick thanks to easy access to the parts in contact with the product.
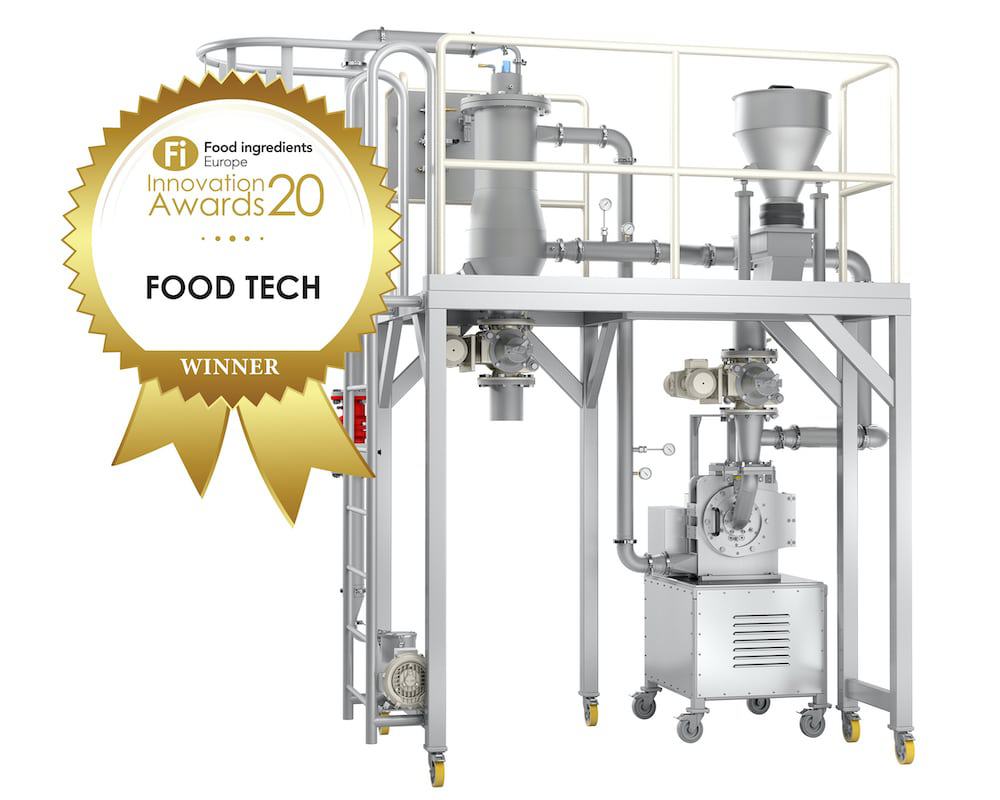
The well-proven Impact Mill Condux® is the basis machine of this grinding system. The products are ground within this mill mainly by impact and shearing action. For use with a wide variety of products and final finenesses, this machine is available in various executions, as either a blast mill, pin-disc mill, or wing-beater mill.
In contrast to conventional grinding plants, the processing gas in the Impact Mill Condux® Compact streams in a circular motion. The product is fed directly to the mill via a pressure-shock-resistant rotary valve and discharged after the grinding process via a separator with an airlock. Parallel to this, the additional rinsing air fed through the valves and mill bearing is continuously discharged through the CycloFil to prevent a build-up of pressure. A subsequent aspiration system generates the vacuum needed to stabilize the system pressure.
Thanks to the innovative CycloFil cyclone filter, the supplied energy is dissipated via the product and the system surface, so that no additional cooling is required. The warmth produced by the grinding process is mainly compensated along with the product when it leaves the machine and to a smaller extent by the system surface and is, therefore, throughput dependent.
The expected temperature increase, for e.g. of ground powdered sugar (d90 = 100 μm) is normally in the range of ∆T = 10-25°C. For a large range of products, the warming has no influence on the quality or the downstream process. For the grinding of particularly temperature-sensitive products, the system can be additionally cooled with liquid nitrogen.
Especially the degree of innovation of the System was confirmed recently by the Fi Europe Innovation Award jury, who awarded the fine impact mill Condux® Compact as the winner of the Food Tech Innovation Award for the most innovative technical processing solution for food ingredients.