It is one of the biggest peat moss companies with 5 facilities in Europe and 2 facilities in Canada. ASB Greenworld exports to 72 countries worldwide. While in 1996-1997 the first production was 26,000 m3, today it reaches 450,000 m3, so that is the development that was made in the last 20 years.
“In our range, we have 12 different grades of peat that we use,” says Jüri Tiidermann, the Production Director. “Firstly, at the screening station we divide all raw peat into different grades and then we mix those grades in different proportions back again. Then we add the fertilizer, lime, clay perlite, all depends on our own custom-made recipe according to the customer specification. Then those materials are mixed together, add the wetting agent, and later on, the mix is forwarded for packaging.”
All the mixing lines were built by ASB Greenworld themselves and lasted for more than 20 years. However, due to the fact that quality requirements and dosage precision in the industry were increasing, they were forced to make a major investment into new equipment in order to keep their share in the market. Consequently, the company had to completely rebuild the whole factory. After thorough research of equipment vendors, their choice fell on Premier Tech Systems and Automation.

Premier Tech Systems and Automation installed a complete mixing line for ASB Greenworld, which holds 8 dosing hoppers for raw materials, which in their case was peat moss. Additionally, 5 dosing hoppers for fertilizers and lines and 2 dosing hoppers for clay and perlite were installed as well.
There was a very short timeframe given in order to finalize the whole project. All the infrastructure and machinery were changes in just two and a half months.
“Volume-wise the project of Premier Tech was the biggest one but they surprisingly succeeded and were one of the best groups that were present here on the site,” added Mr. Tiidermann. “During the project development, they knew what they were talking about and gave us many pieces of advice. Which means that the group was professional enough to run this project.”
Due to the cold weather conditions, ASB Greenworld was losing 1 month of production every year. The reason for this was the mixing line not getting heated enough and the hoppers working at negative temperatures. With the new complete heating system installed throughout the whole factory of 6,000 m2, the problem has been solved. The company was planning to build winter storage for all the materials used on a daily basis independent of the temperature. So Premier Tech Systems and Automation provided the company with a box loading system to create internal storage.
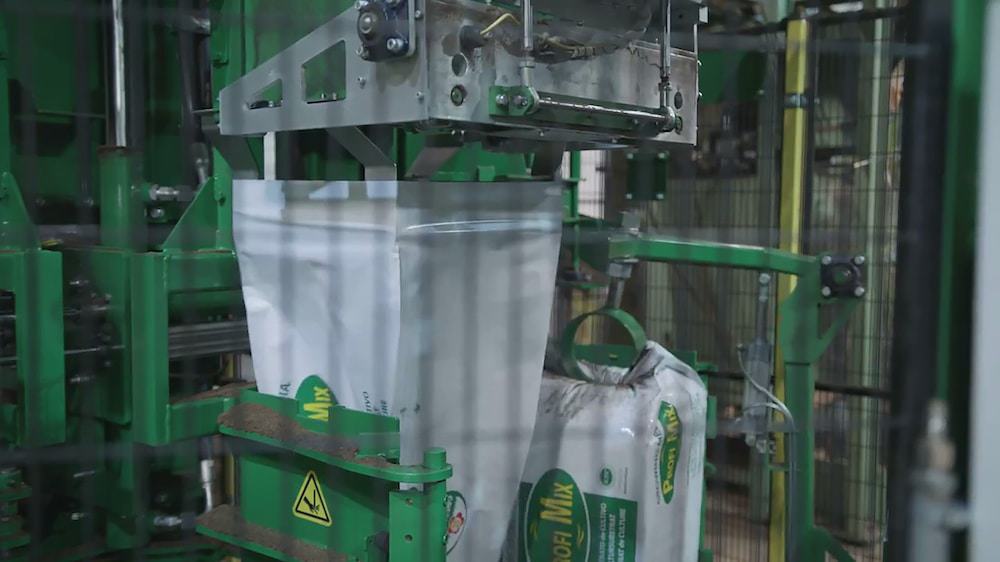
The company had to choose equipment that would answer the needs of the present day to minimize the labor cost and to bring them to the next level of automatization. So they bought the VP-410 baler from Premier Tech.
“From my point of view, there is no alternative for the present day that is comparable to that baler,” says Mr. Tiidermann. “It’s very easy to handle, very easy to change products, to change packaging bags. It takes only 10-15 minutes and we are back live again.”
Nowadays more and more customers require private labels, or the companies are getting merged, they are going bigger and they want to represent their brands in the market. The baler VP-410 gives you a very simple possibility to change from product to product just within 10-15 minutes. Furthermore, the cleanup of the machine is very simple as well. In ASB Greenworld’s case, they have many fill-and-form machines for other purposes (for loose bags and half compressed bags) but the Production Director explained that change for those machines takes way longer than for the 4 stations baler from Premier Tech.
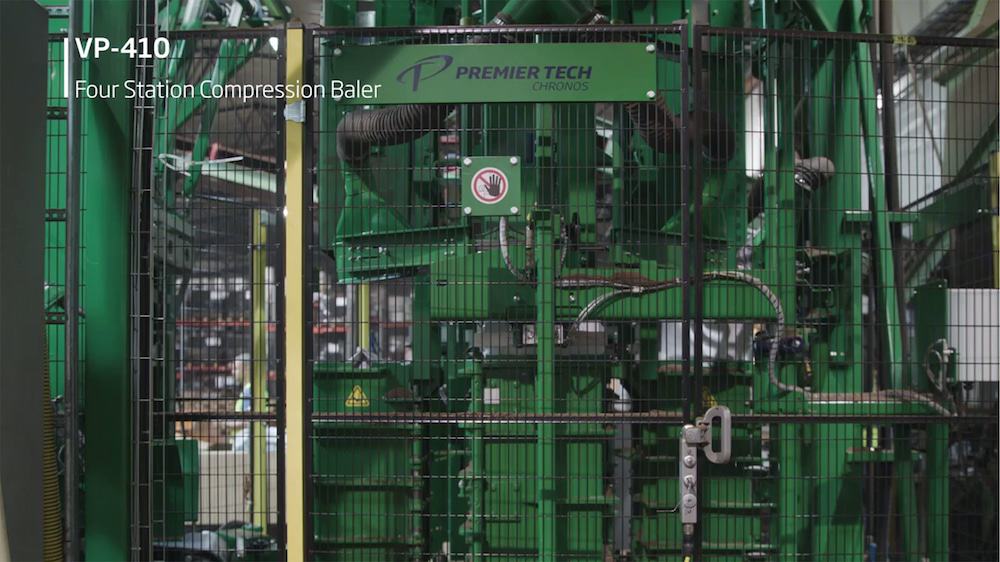
One of the problems the company has is that customers do not always order in advance and ahead of time, but usually they order at the last moment and want to have the product immediately. This requires the company to react in the next few hours. With the new solution from Premier Tech, they have the possibility to react much quicker on the market requirement, logistical requirements, etc. This complete installation has increased ASB Greenworld’s production capacity by around 30%.
“The first piece of equipment we purchased from Premier Tech was Vacuum Harvester back in 1996, so I know this company for more than 20 years,” says Mr. Tiidermann. “The experience of the company is there, they know what they are doing and that gives an advantage when we choose equipment even for future projects. We have big plans for expansion.”