A critical part of the pelletising process is drying the pellets without altering their size, shape or properties. To provide effective drying with maximum design flexibility, Mars Mineral specifies a Kason 750 mm diameter Vibro-Bed™ circular fluid bed dryer for its pilot-scale pelletising line used for process development. The circular fluid bed dryer is gentle enough to handle the most delicate pellets, and offers advantages over a horizontal fluid bed dryer, including footprint and cost, says Craig Vaughan, General Manager at Mars Mineral, adding that the company specifies circular fluid bed dryers for a number of its customer sites depending on throughput requirements.
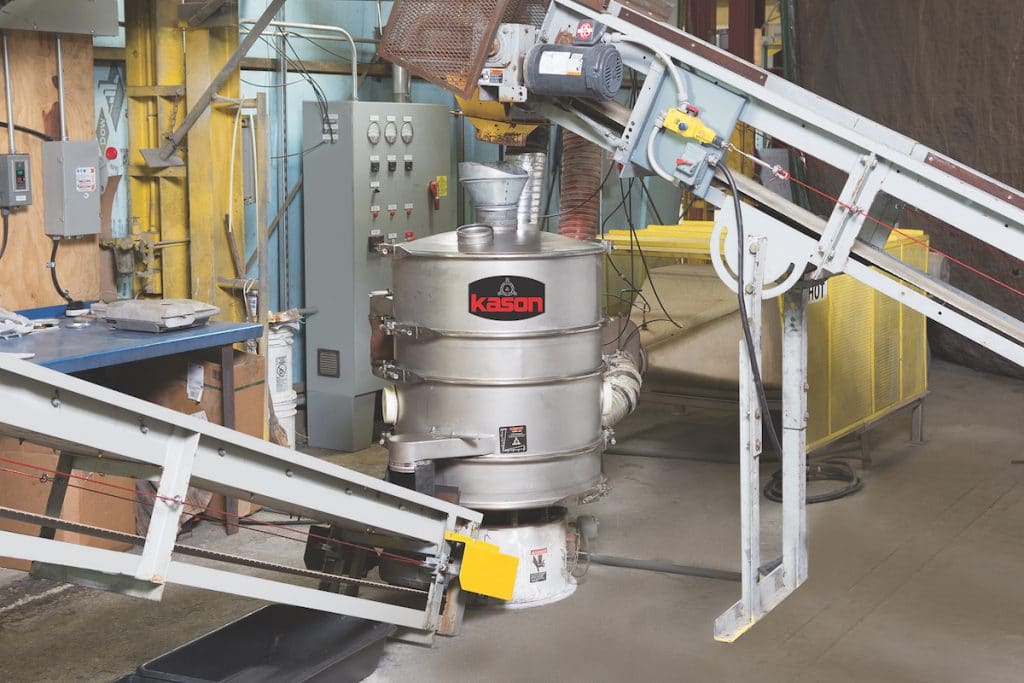
Mars Mineral’s pilot-scale pelletising line
On the pilot line, a Mars Mineral pin mixer combines the feed material with the binding fluid and forms the pellets. The pellets are then dried in the 750 mm, two-stage circular fluid bed dryer. From there, the pellets are conveyed to a circular screener where they are separated by size, typically 0.5 to 5 mm in diameter for products such as fertilisers and carbon black, Vaughan says. Finally, the finished, sorted pellets are packaged.
How a circular fluid bed dryer works
A two-stage circular fluid bed dryer has a circular housing fitted with two horizontal screens, one above the other. Two gyratory motors vibrate the vessel to keep the pellets in motion. A centrifugal fan takes in ambient air and blows it through a heater section. The dryer in the Mars Mineral pilot line uses electric heating. Others use oil, natural gas, or steam as a heat source.
The heated air enters the housing at the bottom, passes up through the screens, and exhausts into a duct connected to the top of the unit. Meanwhile, wet, newly formed “green” pellets are fed onto the top screen of the dryer. The hot air flowing upward surrounds and dries the pellets as the vibration agitates them. The pellets are partially dried on the top screen and, as vibration moves them to the periphery, pass to the lower screen where drying is completed. The pellets exit the dryer through a discharge chute on the circumference. On the screens they follow a path determined by the unit’s geometry and vibratory motion so that processing is first-in, first-out and continuous.
Green pellets contain as much as 40 percent water. Pellets of different materials have different requirements for final moisture content, which may be less than 1 percent or as high as 15 percent. As an example, Mr. Vaughan says, to inhibit mould growth in chicken manure fertiliser, the pellets must contain no more than 10 percent water.
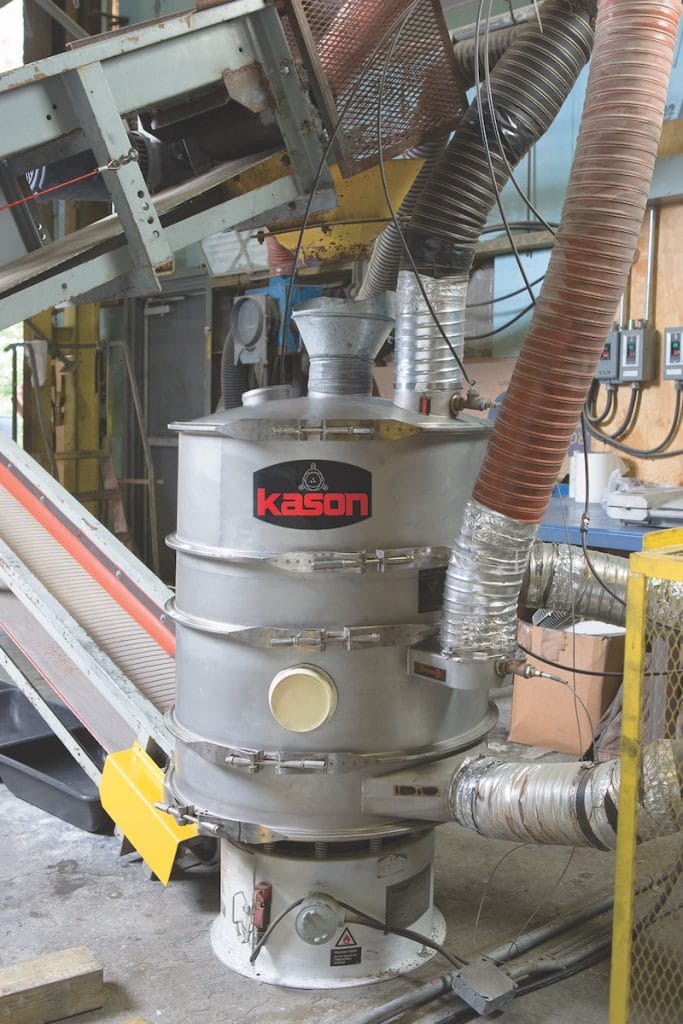
Selection criteria for dryers
Mr. Vaughan says Mars Mineral specifies circular fluid bed dryers for the pilot line and certain customers’ pelletising systems based on the following criteria.
Space: The circular design saves floor space, as much as 50 percent over rectangular units with similar capacity. To gain additional capacity, the pilot line dryer has two screens – two stages – permitting higher capacity in the same footprint. “It’s like building a two-story house instead of one,” Mr. Vaughan says. “If you go vertical, the cost for incremental capacity is lower.”
Energy source: Most dryers use natural gas to heat the air. The Mars Mineral fluid bed dryer uses electric heat. For different customers, Mars Mineral specifies the customer’s preferred energy source: natural gas, oil, steam, or electric.
Ease of Cleaning: For a dedicated pelletizing line, this is less important, but since the pilot line runs many different materials, thorough cleaning between runs is critical to prevent cross-contamination. A circular fluid bed dryer cleans much more easily and quickly than a large rectangular dryer, Mr. Vaughan says.
Preserving delicate pellets: Pellets of some materials can withstand rough handling. “Cement or metals or coal make pellets like bullets,” Vaughan says, which can withstand rough treatment. But some pellets, such as kitty litter, organic fertilizer, or carbon black, need to be handled gently to prevent their falling apart during drying. Some types of dryers, such as drum dryers, may damage the pellets. The circular fluid bed dryer, however, is more suitable for handling fragile pellets, as it agitates, moves, and dries the pellets with only vibration and air flow. The pilot line dryer has to be gentle enough to handle the most delicate pellets.
Cost: Mars Mineral found the circular fluid bed dryer a cost-effective choice for the pilot line. Mr. Vaughan gives an example, filling the above criteria, of a company that makes organic pelletised fertiliser from fresh chicken manure. Because the manure is fresh and not composted, it needs to be pasteurized to destroy harmful microbes to make it safe for consumers to handle. Mars Mineral developed a drying process with a circular fluid bed dryer that keeps the manure pellets in the dryer long enough and at a high enough temperature to pasteurize them, eliminating the additional costs, energy use and space requirements of a separate pasteurization process.
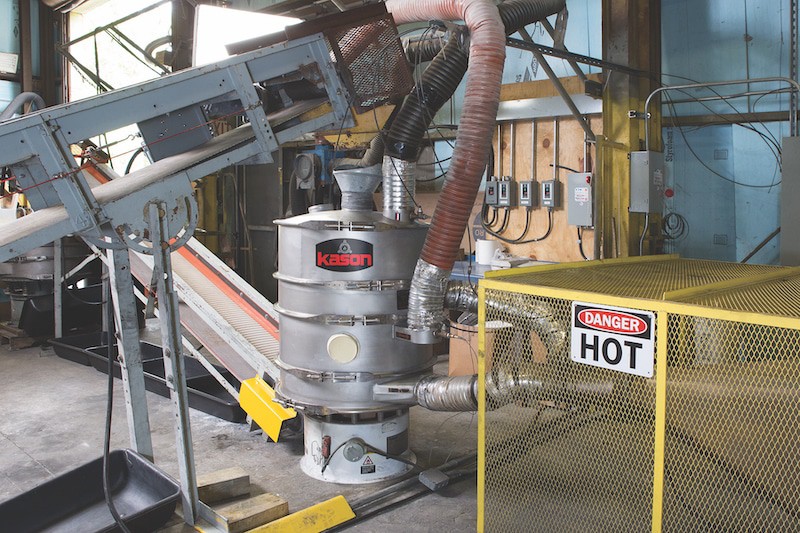
Drying capacity and throughput determine dryer selection
Some or all of the water contained in the green pellets may be present as “free water” and some water may be chemically bound to the material, Mr. Vaughan explains. Therefore, part of the drying-rate equation is theoretical and part needs to be determined through testing. Removing a pound of free water requires 1850 BTU (4303 kJ for 1 kg). Bound water takes more energy to remove. Through experiment, Mars Mineral’s laboratory and the pilot pelletising line fine tune the overall drying requirement and process.
For any pelletising system, the dryer is specified according to the desired throughput and amount of water to remove from the green pellets. The pilot line’s 750 mm two-deck circular fluid bed dryer is equipped with a 500,000 BTU/hr (147 kW) heater. Vaughan offers an example of green pellets of a special chemical product entering the dryer at 40 percent water and exiting at 15 percent. This product runs on the pilot line at the rate of about 273 kg/hr.
The pilot line processes about 1.1 to 2.7 tonnes /day, depending on the amount of moisture to be removed, Mr. Vaughan says. Mars Mineral pelletising systems at customer sites typically produce 1.1 tonne/day to 11 tonnes/hr of pellets – capacities that usually require a larger dryer.
“We provide the enabling technology to convert waste powders into value-added products,” says Vaughan. “As part of that process we supply customers with the entire suite of processing equipment needed to complete that conversion. Depending on capacity, we include circular fluid bed dryers as an integral part of that process because of the advantages of space and cost.”
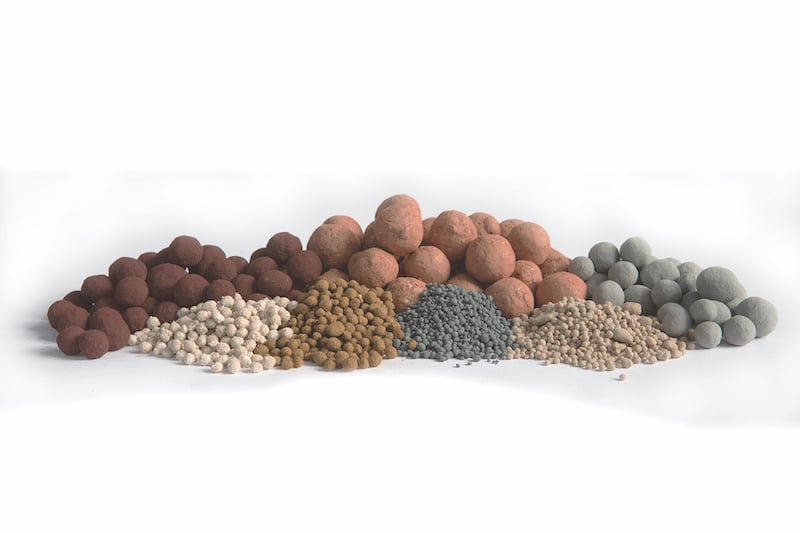