Common Bulk Materials Handling Challenges
Bulk materials flow properties are frequently overlooked within the engineering fraternity, however, the consequences become significant when the engineered equipment or systems encounter failure or fail to operate correctly from the start.
The effectiveness of a dry bulk materials handling operation is significantly influenced by the material’s flowability through a piece of equipment, any obstruction occurrence leads to time, financial, and resource losses, along with potential hazards for operators. While challenges are inevitable in any industry, understanding the root causes and available solutions helps with establishing proper prevention measures because prevention is usually the best safeguard for breakdowns. Some of these challenges include the following:
Material Flowability
One of the prevalent challenges in dry bulk solids handling systems revolves around the flow properties of bulk materials. Most equipment designs, silo or hopper designs, are done with little to no regard for the flow properties of the handled bulk solid, and consequently, numerous material flow problems in storage vessels arise.
In cases of improper designs, materials may create bridges or form ratholes inside the storage vessels necessitating interventions to induce flow. More often than not, these interventions (typically hammering the tapered bottom of the silo or hopper) are manually performed and result in plant downtime, equipment structure deformation, as well as impact product consistency.
Bridging: a prevalent occurrence seen in cohesive bulk materials that tend to clump together or interlock. In this phenomenon, the bulk material creates a stable bridge or arch above the outlet of storage vessels, impeding material flow. The effectiveness of the bridge is typically determined by the cohesive strength and internal friction of the individual particles.
Rathole: this is simply the creation of a material flow channel directly above the outlet of a storage vessel. In contrast to a uniform discharge of the bulk material, the material accumulates along the sidewalls of the storage vessel, creating an empty space or void in the centre. Ratholing commonly occurs in flow patterns known as funnel flow, lacking a first-in, first-out (FIFO) sequence.
Segregation
Another common challenge in the industrial sector is the issue of material separation in storage vessels such as silos, hoppers, etc. This material separation is commonly referred to as segregation. Bulk material segregation occurs when particles separate primarily due to variations in their physical and/or chemical properties, such as size, density, and shape. Consequently, during handling processes, materials with these differences may undergo segregation. In the course of handling, lighter or smaller particles tend to rise to the top, while denser or larger particles settle at the bottom. The blending of bulk materials often results in segregation, leading to an uneven discharge and impacting product quality due to non-uniformity.
The cost incurred for these obstructions and the damage caused to equipment while trying to manually induce material flow leads to minimised efficiency and ultimately avoidable expenses for the business. These expenses manifest as plant downtime and the need for equipment repairs. Fortunately, the bulk solids handling industry is now tackling these issues with contemporary solutions such as incorporating the use of bin activators or other suitable material flow aids.
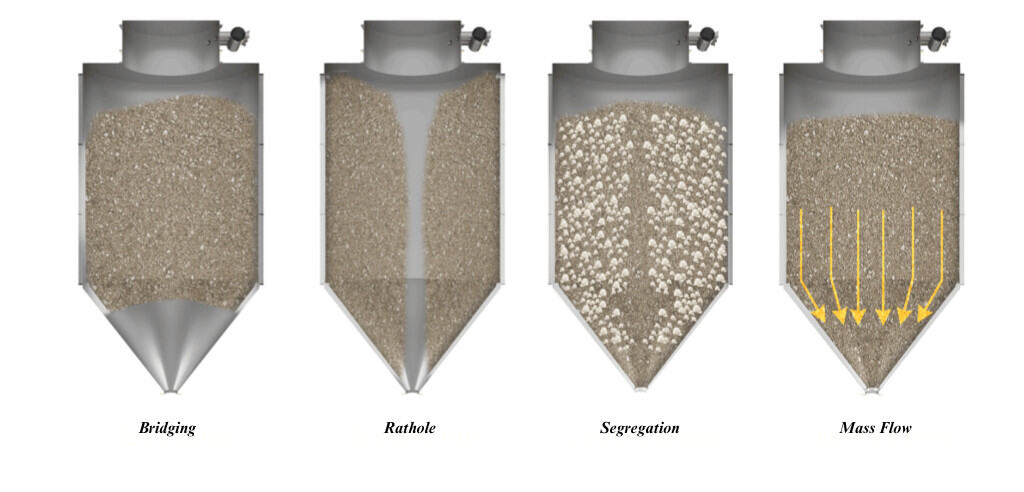
Bin Activators
Bin activators, also known as vibrating bin activators, are tapered conical-shaped equipment that facilitate easy and on-demand bulk solids take off from silos or hoppers. They are typically used in process applications with the purpose of promoting bulk solids mass flow due to their principle of operation, thus reducing bridging, ratholing, and segregation. Bulk material mass flow promotion ensures seamless and efficient discharge of materials from upstream equipment.
At Polimak, we engineer bin activators that serve as a solution to material handling flow challenges. We avoid adopting the “one size fits all” approach, understanding the risks it poses in the engineering fraternity. We take the necessary time to assess every potential solution best suited for our client’s application by considering one of the most notable contributing factors in equipment design, the properties of the handled material. Failure to engineer bulk solids handling equipment from the beginning to handle the distinctive properties of the processed materials can lead to substantial delays in process start-up.
Operation Principle
During operation, the bin activator serves as a partial replacement for the tapered section of a storage vessel. It is typically mounted to the storage vessel at the cross-section where bridging (also referred to as arching) is likely to occur – the cross-section is known as the bridging crosssection. The vibrator, sometimes called a gyrator, applies high-frequency low-amplitude gyratory vibrations to the unit thereby promoting steady material flow through the outlet port. An internal baffle plate (deflector) is in place to prevent material packing at the outlet port as well as transmit vibrations to the material, thus, eliminating bridging hiccups. Additionally, gyrating vibrations from the deflector surface effectively transfer forces into the stored material, extending all the way to the vertical walls, inducing gentle agitations that diminish segregation and prevent the formation of ratholes. Ultimately, the vibrating bin activator aids with the firstin, first-out (FIFO) sequence and promotes uniform and even discharge of bulk materials.
Bin Activator Features
Polimak bin activators come in different sizes having different innovative features. Some of the significant standard features are shown in the image below.
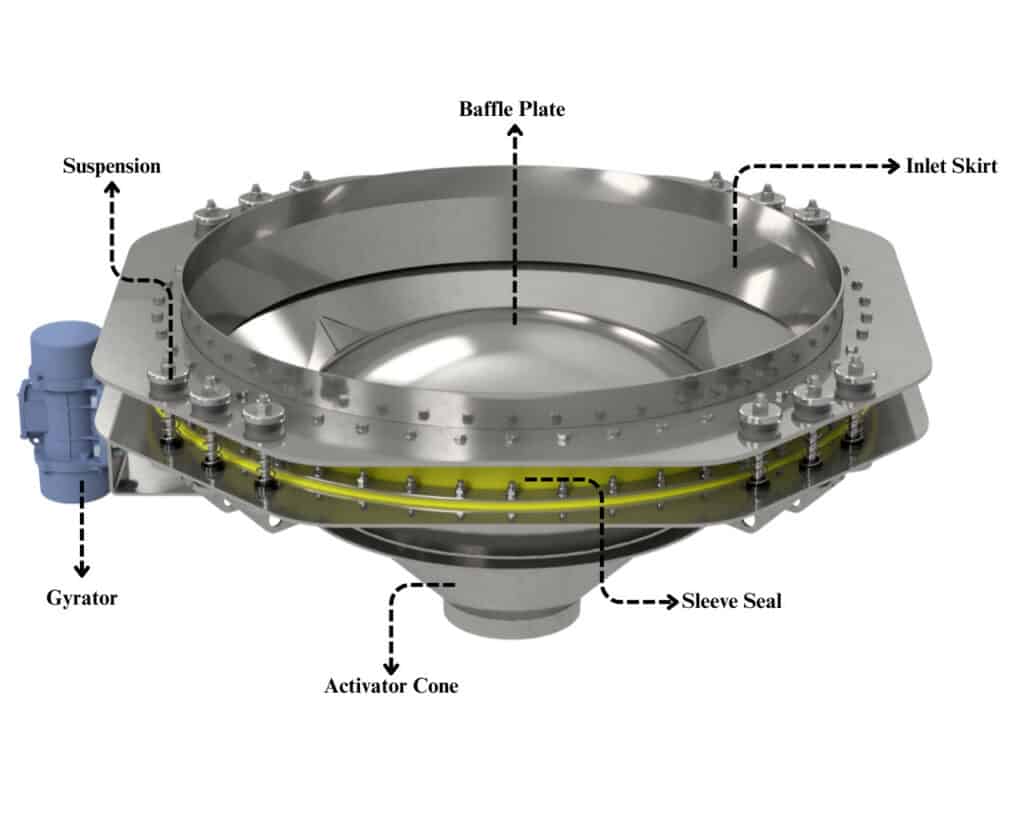
Bin activators have been established as effective bulk materials discharge aids from storage vessels as they ensure dependable plant performance and alleviate bulk materials handling flow challenges. These devices enhance efficiency, minimize downtime, and contribute to a seamless and reliable discharge of bulk solids from silos and hoppers. In addition, bulk materials can be accurately metered from bin activators at modulated rates with optional downstream equipment such as screw feeders or rotary feeders.