Pneumatic conveying manufacturers excel at moving powders and bulk solids, while blender manufacturers specialize in homogenizing them. Direct charge blender loading systems merge these technologies, automating and streamlining the process.
1. What is “Direct Charge Blender Loading”?
Direct charge blender loading is an innovative adaptation of vacuum transfer technology that uses a vacuum-tolerant process vessel, such as a tumble blender, as the primary receiver for powdered materials. In this system, materials are automatically vacuum conveyed into and out of the process vessel, streamlining the loading and unloading of pre- and post-blend bulk materials. This approach eliminates the conventional loading and discharge cycle associated with vacuum receivers, transferring materials directly into the blending process without spills or fugitive dust, which minimizes housekeeping requirements.
The automated nature of direct charge blender loading removes the need for manual material handling, eliminates operator exposure to dust or harmful materials, prevents ingredient loss and waste, and avoids product contamination. Materials can be drawn from various sources, including floor-level wands, bulk bags, or mezzanine-level feed points. The system also features timing controls and automatic pulse filter cleaning, ensuring a seamless, efficient, and safe operation.
2. What are the loading and unloading options?
Direct charge loading technology enables the vacuum conveying of powders and bulk solids from various sources, such as drums or bulk bags, to a designated location, typically the blending vessel. Materials can be efficiently conveyed from floor level to mezzanines or to upstream equipment like screeners or sieves. Once the blending is complete, the material is vacuum conveyed out of the tumble blender and transferred to the desired post-blend container. This process is fast, secure, and straightforward, significantly reducing the risk of batch contamination, material waste, extended loading times, and operator exposure to fugitive dust.
3. What types of materials can be vacuum transferred to a tumble blender?
Vacuum transfer technology is a proven, efficient method for moving a wide range of powders and bulk materials, eliminating the need for manual handling and enhancing process efficiency. While factors such as material consistency, moisture content, and particle size may influence the process, direct charge blender loading technology is capable of conveying virtually any dry powder or granular material that can be transported through a hose or tube.
4. How are powders moved into and out of containers or into a process vessel?
The tumble vessel is the center of the mixing project, acting as the vacuum discharge receiver. Powders can be conveyed from any ingredient container such as a drum or tote box, using a hand-held vacuum wand, or a bulk material device like a bulk bag unloader or bag dump station, with material transferred through vacuum hose lines and discharged into the blender vessel. In reverse, the same material transfer vacuum lines can empty post-mix ingredients from the vessel and discharge them directly into the container(s) of choice. Inline filters on the direct charge blender loading system guarantee zero loss of material transfer between drum and vessel and prevent powder from collecting on the pump.
5. Are there any industry standards applied to direct charge blender loading technology?
Process vessel sizes and shapes should be designed and manufactured per USDA-sanitary design standards suitable for the food, beverage, pharmaceutical, nutraceutical and chemical industries. Blenders should be Mill-Certified, inspected, and American Society of Mechanical Engineers (ASME)-certified. Vacuum conveyors should be designed for cleaning and sanitation requirements for the industry being served.
All documentation and testing is consistent with standard cGMP (Current Good Manufacturing Practices) quality controls. Calibration and Material Certification(s) are also available.
Safety standards for combustible dusts (NFPA 652) and control of static electricity (NFPA 77) are also applied.
6. What seal options are available on vacuum tumble dryers?
There are two (2) seal options available, standard packing and/or a mechanical seal design.
The standard packing options are easy to install, with a lapped tolerance of less than one micron (0.00039 inches). Vacuum dryer systems have extremely low RPMs, making them better for packing.
The mechanical seal design is sensitive to installation errors – measurements must be precise. Any vibration or shaft deflection can cause catastrophic results. When cleaning and servicing the units, fluid can solidify, crystallize, become viscous, etc. when the mixer/dryer is not running.
The mechanical seal design does not generate much heat and seldom requires cooling. Newer face materials and the latest elastomers are chemically compatible with a wide cross-section of chemicals and cleaners. Mechanical seals are better than packing when designing a high-speed shaft application.
Packing is best for slow-speed or high-temperature applications. Packing seals and mechanical seals will hold the same vacuum and maintain the same transfer leakage rate.
7. What do I need to know about vacuum tumble drying?
Vacuum tumble drying is approximately three times faster than a tray dryer. This approach provides low temperature drying for heat sensitive materials and allows for inert atmospheres without oxygen contact. Vacuum tumble-drying systems allow product mobility without segregation or classification of fines. Depending on the application, it can also provide low final moisture content, produce predictable, repeatable, and scalable results, and limit any potential for contamination. Additionally, the vacuum pump can be located in separate mechanical room, up to 500ft (15m) away from the blender, saving floor space and noise in the blending suite.
8. What is the best blender vessel shape for drying: double-cone, slant-cone or V-shape?
The critical element in determining vessel shape for drying is the ratio between heated surface area inside the vessel and the volume of material load inside the unit. The lower the load level, the better the ratio and the faster the drying.
Albeit slight, double cone units have consistently larger surface areas versus V-shapes for the same working volume, however, the V-shape has a somewhat more significant advantage over double cones.
Slant cone units have slightly more surface area than similar double cone units. Accurate scale-up of tumble dryers is possible using this ratio. As the ratio goes down with larger units (more material, less surface area), the time required to dry will increase.
9. What is a dummy hose station?
A dummy hose station is for operator safety. A direct charge loading system may be equipped with optional dummy hose stations. These devices are wired to the blender control panel and integrated into the loading sequence programming. When blender loading is completed, operators must connect both the vacuum hose and convey hose to the respective dummy hose station.
Each hose station is designated for a different sized hose to prevent a mismatch. If both vacuum hoses are connected correctly, the blender can begin tumbling. If one or both vacuum hoses are not connected, or connected incorrectly, the operator will be prompted to correct the hose connections before the tumbling will be permitted.
A dummy hose station also provides a sanitary benefit by closing off the end of the hose when not in use, discouraging dropping the hose couplers on the floor which may damage the coupler or ferrule.
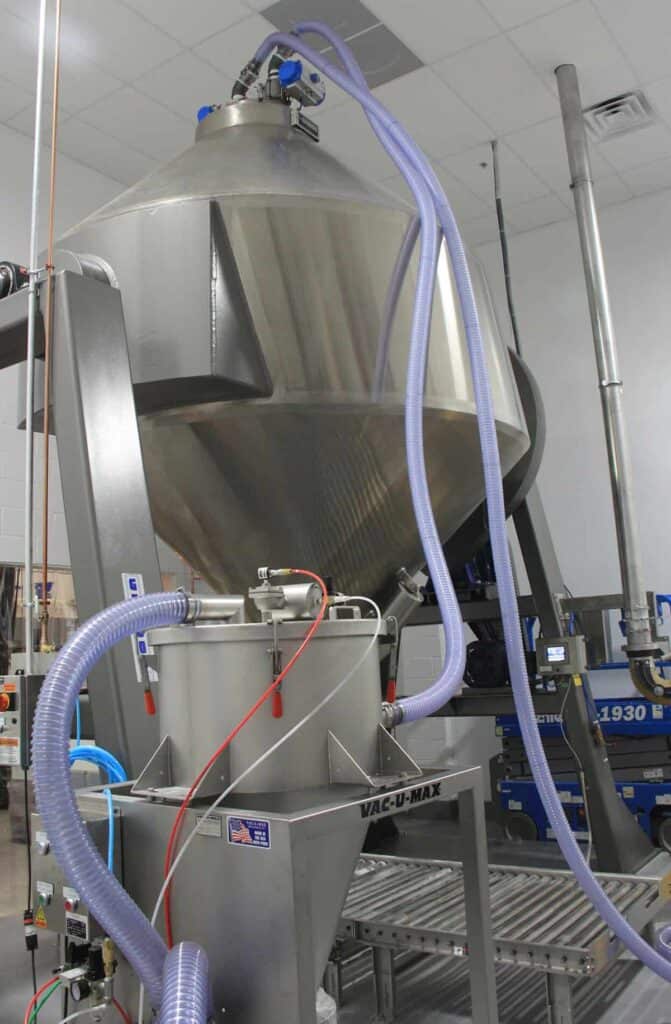
10. Does direct charge blender loading require any routine maintenance?
Direct charge blender loading technology automates blender loading by eliminating manual lifting and dumping. It is important to inspect convey hoses after each use and check for leaks of powder due to internal or external abrasion or excessive bending. Since this technology incorporates dilute phase vacuum conveying (not pressure conveying), any leaks are inward. Other routine maintenance includes inspection of dust filter(s) on the blender loader filter separator, and inlet adaptor on the front of the blender loader filter separator. Clean the interior of the blender loader filter separator in accordance with your sanitation and quality control procedures. This may be as frequent as following each usage, or simply when the ingredients in the blend are changed. On a quarterly basis, inspect the polytube compressed air tubing for leaks or any loose connections, as well as the ports on the vacuum vent valve.
One System with Homogenized Results
Direct charge tumble blender loading eliminates the vacuum receiver’s conventional loading and discharge cycle. The system transfers all material in and out of the tumble blending vessel without spills and fugitive dust, keeping everyone safe, clean, and housekeeping at a minimum. Material transfer, and precise blending and drying are all completely automatic, with no manual handling of the material, no operator trying to figure out blending times or recipes, no operator exposure to dust or harmful materials, no ingredient loss or waste, and no contamination. Material can be drawn from floor level via hose or tubing, from bulk bags, or mezzanines and discharged into the tumble mixer or dryer. The system is packaged with timing controls and automatic pulse filter cleaning. Controls for mixing and drying, and controls for the vacuum pump can all be remotely located and monitored. For more information about vacuum conveying and direct charge tumble blender loading visit www.vac-u-max.com or www.okgemco.com.