These systems are essential for capturing and adsorbing hazardous pollutants such as mercury, dioxins, and furans from flue gases emitted during high-temperature combustion processes.
Key applications of ACI include:
1. Power Generation
- Coal-Fired Power Plants: ACI systems significantly reduce mercury emissions from coal combustion, helping power plants meet environmental standards.
2. Waste Incineration
- Municipal Waste Incinerators: ACI systems capture pollutants like dioxins, furans, and mercury during the incineration of municipal solid waste, reducing environmental impact.
3. Chemical Plants
- Chemical Manufacturing: ACI systems control emissions of hazardous air pollutants (HAPs) during chemical production processes, ensuring air quality and regulatory compliance.
4. Steel Mills
- Steel Production: These systems capture mercury and other pollutants released during high-temperature steel manufacturing operations.
5. Casting Plants
- Foundries and Casting Operations: ACI systems reduce emissions of mercury and volatile organic compounds (VOCs) from furnaces, promoting cleaner air and safer working conditions.
Polimak’s Customized ACI Solutions
How ACI systems work?
During high-temperature combustion, various gases are released into the atmosphere that are toxic and harmful to human health. Powdered activated carbon (PAC) is a high-performance adsorbent designed to eliminate these toxic gases, including dioxins, furans, and mercury.
Besides flue gas treatment, PAC is also used to remove micropollutants in wastewater and drinking water treatment. Activated carbon addresses environmental issues impacting both air and water.
Under normal conditions, baghouse filters cannot effectively prevent the spread of flue gases generated by incineration. Introducing PAC into the pipeline at the baghouse filter inlet allows it to adsorb these gases. The PAC, along with captured flue gases such as dioxins and furans, is then trapped by the filter bags, preventing their release into the atmosphere.
Implementing PAC in industries faces challenges related to storing raw materials (sacks, big bags, silos), conveying them to dosing systems, and then dosing them into the desired process. These steps can be costly and require significant plant space. Inefficient methods increase operational time, labor, and energy costs. The Polimak activated carbon injection (ACI) system offers a high-efficiency solution for controlling gas emissions. This long-term solution features a compact, easy-to-install, and easy-to-operate packaged system designed for PAC delivered in bulk bags. The system includes a hoist, big bag discharging platform, storage silo, weighing unit, dosing unit, and pneumatic conveying system for PAC injection. It can also be integrated with lime dosing systems for enhanced functionality.
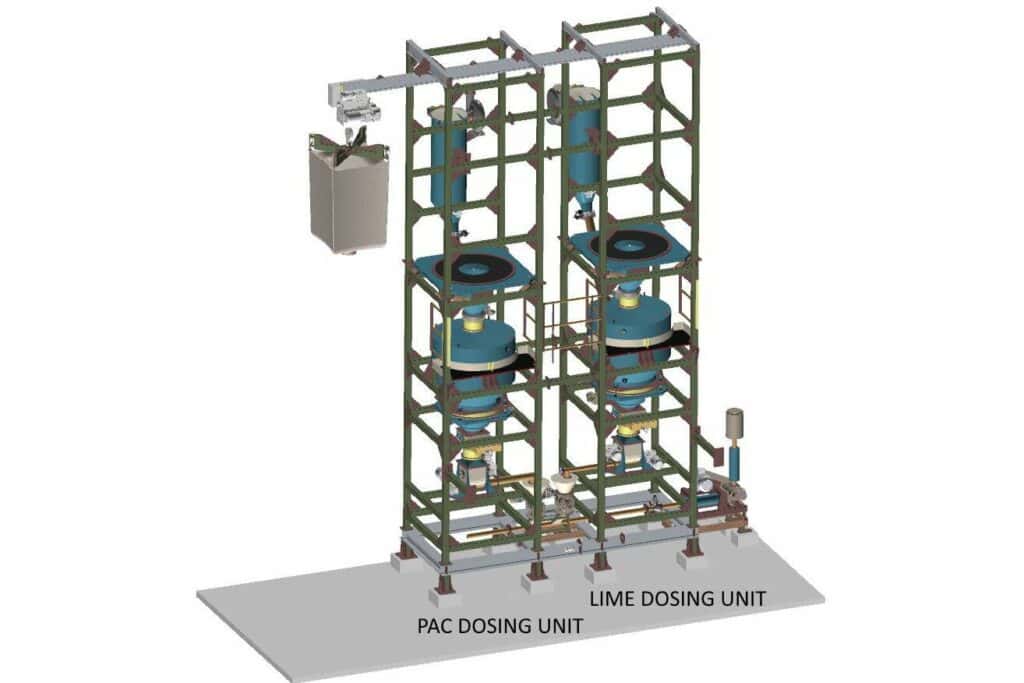
The PAC is delivered in bulk bags and is placed onto a carrier platform using a forklift or hoist. The bag’s outlet is released, allowing the carbon to feed into a powder hopper and then discharged into a storage silo. From the silo, the PAC is automatically fed into the pneumatic conveying pipeline by a feeder located under a weighing device. This feeder controls the precise amount of PAC injected into the process line, typically within the dust collection pipeline, by regulating the material transfer capacity, speed, and timing through a PLC-controlled automation system. This ensures efficient and controlled pollutant adsorption, preventing their release into the atmosphere.
Polimak’s ACI systems, such as the PAC bulk bag discharge storage weighing dosing and injection system, are designed for high-efficiency control of gas emissions. These systems are compact, requiring less space in the plant, and are simple to install and operate. They offer a long-term solution with features like easy big bag handling, integrated lime dosing, and streamlined operations to reduce space requirements, labor, and energy costs.
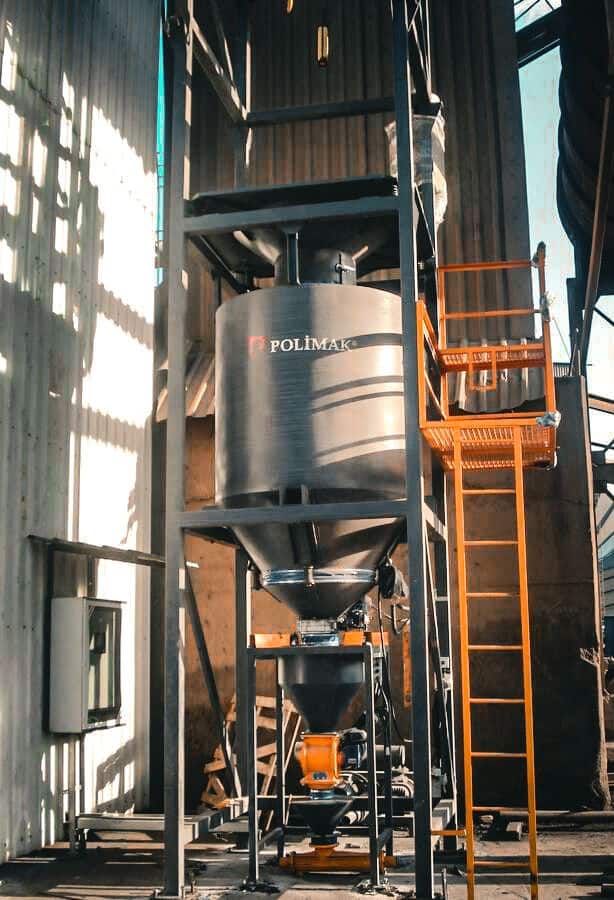
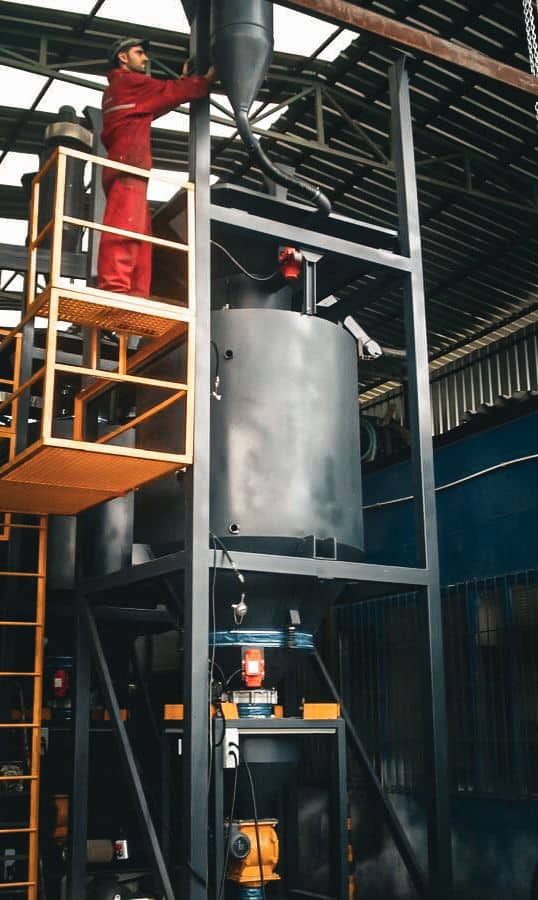
Benefits of ACI Systems in Industrial Applications
- High Removal Efficiency: ACI systems are capable of achieving high removal efficiencies for a variety of pollutants, making them effective in diverse industrial applications.
- Regulatory Compliance: Helps industries meet strict environmental standards, avoiding legal and financial penalties.
- Adaptability: Can be integrated into existing infrastructure with minimal modifications, providing a cost-effective pollution control solution.
- Versatility: Activated carbon can be tailored to target specific pollutants, enhancing the overall effectiveness of the system.
Polimak emerges as one of the leaders in providing customized ACI solutions tailored to meet specific industrial needs. Their offerings encompass a wide range of systems, including:
Big Bag Discharge and Activated Carbon Injection System:
Dry bulk solids are transferred and delivered with different ways. FIBC (Flexible Intermediate Bulk Container) also know as big bags are one of the the most preferred way of handling bulk materials in granular and powder form. Well designed big bag handling systems are needed to be able to fully benefit from big bags.
The integration of Big Bag Discharge Systems with Activated Carbon Injection Systems represents a significant advancement and operational benefits in terms of;
Efficiency:
- Streamlined material handling reduces downtime and improves overall process efficiency.
- Automated systems can further enhance the precision and consistency of PAC injection.
Safety:
- Dust control elements protect workers from exposure to fine particles.
Flexibility:
- Suitable for various types of dry bulk solids, not just PAC.
- Can be integrated into different industrial processes where bulk material handling is required.
Environmental Compliance:
- Effective handling and injection of PAC contribute to reduced emissions of harmful pollutants.
- Helps industries meet stringent environmental regulations and standards.
PAC Bulk Bag Discharge Storage Weighing Dosing and Injection System:
An integrated system ensuring precise control over the dosing and injection of powdered activated carbon, optimizing its consumption and effectiveness, primarily used in large-scale industrial operations.
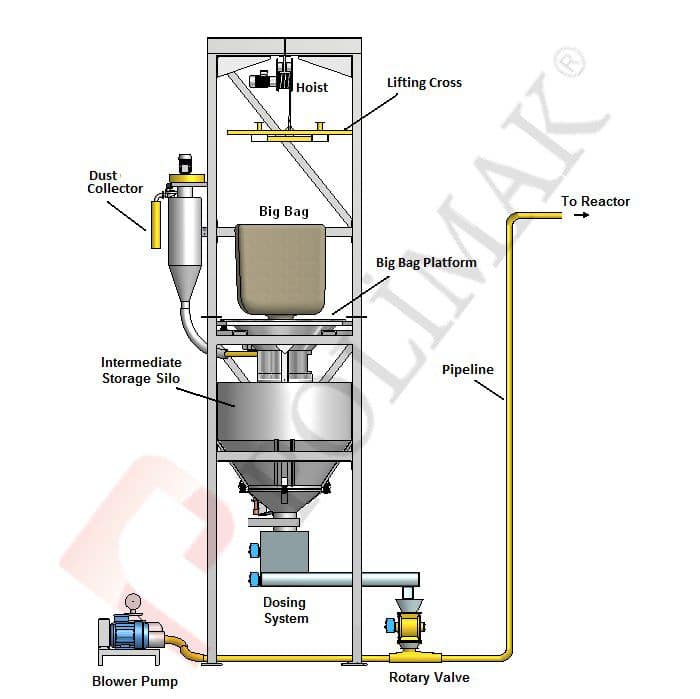
PAC Storage Silo and Dosing Unit:
Pneumatic transfer systems used for silo loading utilize blower pumps or compressors. Motor power, pipeline diameter, equipment selection depends on type of bulk material, transfer distance, silo height and transfer capacity. Level sensors, jet filters and other equipment are installed on storage silos to properly run silo filling system offers bulk storage and automated dosing for continuous and efficient pollutant control, essential for large manufacturing plants and power generation facilities.
PAC Big Bag Discharge and Dosing Unit:
Big bag discharge systems can deliver dry bulk solids in powder and granular form to weighing and batching systems. Loading hopper of weighing system should be kept full during dosing and batching. Big bag discharge systems can monitor the product level in loading hopper and maintain constant level automatically. Depending on dosing speed and conveying distance, mechanical conveying systems or pneumatic loading systems may be used. Dust collectors can be used to prevent dust emission during hopper loading for materials with high dust content.
Polimak’s solutions illustrate its commitment to innovation and environmental responsibility, providing industries with effective tools to address pollution and achieve sustainability goals.