Filtermist manufactures dust control equipment that utilises either media-based filtration or liquid separation under the Dustcheck brand – one of very few UK manufacturers that can offer both solutions. This means we are not restricted by a limited product range and are able to specify the optimal solution for any application.
Choosing the right dust control equipment requires expertise, knowledge and experience due to the multiple design considerations for each individual application and varying characteristics of dusts that needs to be captured. Dustcheck has been providing dust control and air filtration equipment for more than 40 years and as such is perfectly positioned to specify the most appropriate solution to the dust control requirements of its clients.
Application considerations for dry and wet filter systems; when and how to apply them
Of the many types of solid particulate filtration systems available to industry in general, there are two main categories which encompass the vast majority of equipment supplied for this purpose; ‘dry’ filter units and ‘wet’ filter units.
We are going to examine the defining characteristics, limitations and application of each type of technology to offer an insight into the main considerations required when making a selection.
Fundamentals of dry filter unit separation
These types of units typically utilise elements made from permeable filter media in various degrees of efficiency and finish to separate solid particulates from a gas stream utilising the four main components of membrane filtration mechanics; impaction, interception, diffusion and electrostatic attraction. Usually, dry filter units used in industrial applications utilise some method of automatic cleaning to dislodge filtered particulate from the media (dynamic filters) however this is not always the case, some units are designed to be simple barriers without the need for media re-generation (static filters).
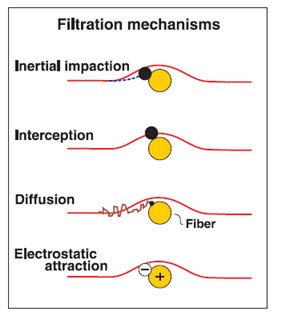
- Inertial impaction is where the gas stream passes around the filter fibre but inertia causes a dust particle to come into contact with the fibre itself
- Interception is where a dust particle follows the path of the gas and comes into contact with a filter fibre
- Diffusion is characterised by the random motion of a dust particle coming into contact with a filter fibre
- Electrostatic attraction causes a particle to be drawn into contact with a filter fibre
As particulates accumulate on the filter elements there is an increase in differential pressure (the static pressure measured each side of the filter media) and depending on the type of application this will either need to be periodically cleaned (usually high dust load applications with automatic cleaning systems) or the filter element(s) changed completely (low dust load applications without a cleaning system such as secondary HEPA filters)
Membrane type filtration offers very high levels of efficiency which can be over 99.99% at 0.3 microns (E10 rated) with primary automatically cleaned media, and up to and even past H14 efficiency on static filters. Dry filter systems are suited to a myriad of different applications in multiple industries and offer a reliable, low maintenance and high efficiency solution.
Limitations of dry filter units
Dry filter units that utilise membrane type medias usually contain filter elements in one of the following formats; pleated cartridges, pleated cassettes, tubular bags or flat bags.
Common constraints across all of these formats are that they are all essentially using a permeable media which requires filtration to occur on the surface and through the depth of the material in some cases. As such these types of filters are challenged if there are high moisture levels (in liquid form) in the extracted air which can saturate the filter media or the particulates being filtered are very adhesive in nature and difficult to remove with an automatic cleaning system.
For particulate in liquid form there are other extraction solutions available on the market, not covered within this paper but details of which can be found at www.filtermist.com.
High moisture levels that exist in a gaseous state i.e., the relative humidity of the air passing through the filter, is not necessarily an issue as long as any temperature differences between the extract air and the filter unit are considered in terms of not letting the air cool to ‘dew point’ which is where condensation into a liquid will occur. This is usually addressed by the addition of trace heating and / or lagging to minimise dew point issues.
Other considerations for the application of dry filters are where potential ignition sources are introduced into the system by the process itself e.g., metal grinding producing sparks, and limitations of protection when handling highly explosive and volatile dusts.
Most dry filter medias are flammable and introduction of ignition sources can pose a risk of fire unless some means of protection is implemented such as spark extinguishing or similar. If the dust being extracted is explosive then the risks are even greater if ignition sources are known to be present as there is a potential mix of fuel and an ignition source co-existing. Even with adequate explosion protection in line with ATEX Regulations, this type of application may pose a high enough risk to move away from a dry filter solution.
A limiting factor with dry dust filters is also the maximum level of explosion protection available. In terms of explosibility the vast majority of particulates handled in industry are well within the capabilities of a dry filter system however care should be taken when handling ST3 rated dusts with a KST value >300 bar m/s (as per BS EN 14034 – Determination of explosion characteristics of dust clouds). These high explosibility levels are usually found when handling reactive white metals such as aluminium, magnesium etc. and can reach
levels of 1,000 bar m/s or more. In this instance it is unlikely that a dry filter unit could be made strong enough and with enough explosion vent area to handle the application and the customer is also likely to deem the potential risk and significant repercussions of such a violent explosion, should it occur, too great and to seek an alternative.
Fundamentals of wet filter unit separation
A wet filter unit typically separates solid particulate from a gas stream by passing it through an atomized liquid whereby particles get encapsulated by droplets and subsequently submerged into a tank where sedimentation occurs. As the method of separation is provided by a liquid which is recovered and re-used within the unit, there is no requirement for replaceable filter elements such as those in a dry unit
Scrubbing Stages
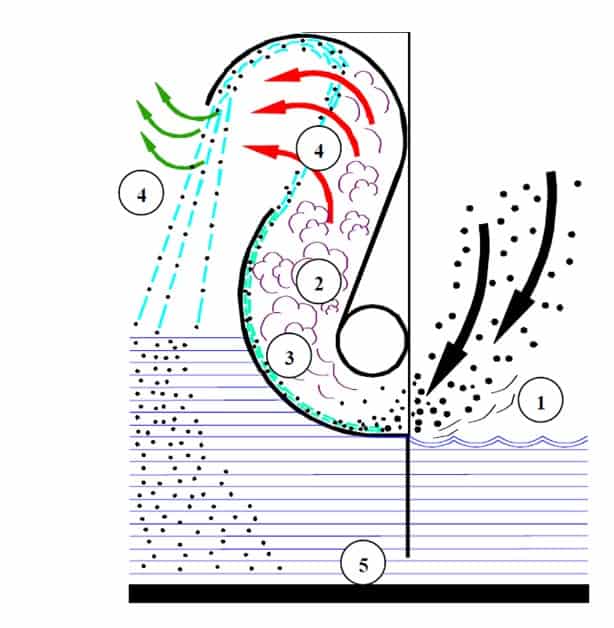
Primary inertial separation onto water surface of sump
Spray generation zone – fine droplets/mist
Irrigated baffle surfaces
Final water curtains
Collected dust settles in bottom of tank
Wet dust collectors, or wet dust scrubbers, are mass separators. The efficiency of wet dust collection is determined by the mass of the dust particle present in the extracted dust cloud relative to the size of the water droplets generated.
Wet collectors are more suited to particles with heavier mass and they function by generating very fine droplets or aerosols in the ‘spray generation zone’. These droplets will impinge on, and encapsulate dust particles of similar momentum.
Wet units usually require dusts of relatively high specific gravity (>2500kg/m3) and with particle sizes >10 microns to achieve acceptable filtration efficiencies of >99%.
Wet collectors are recommended when machining reactive white metals such as aluminium, titanium and magnesium etc. due to their highly volatile nature and are also ideal for handling sticky particulates or dusts extracted with liquid moisture.
Limitations of wet filter units
Unlike a dry system where filtered dust is discharged from the unit, then collected and disposed of, wet units effectively create a liquid waste stream as the means of filtration and is also the medium in which the particulate accumulates. This requires regular manual cleaning and therefore some limitation of operation during maintenance down-time.
Treatment is also required to be added to the water in a wet unit to minimise corrosion, and this requires regular checks to maintain correct levels. In addition, the scrubbing liquor will collect water soluble salts, liquids and gases and will therefore require periodic drainage. Hydrophobic (water repellent) particulate will not be contacted by the droplets and therefore not filtered out in the unit.
A proportion of water is consumed and given off as a vapour and a visible discharge plume from the unit so a permanent water supply is required to be connected to it to allow operating levels to be maintained. Consideration must be given to the unit discharge position because of the vapour plume and it is also worth noting that the plume can sometimes be misinterpreted as excessive carry-over and require validation by the supplier to the end user.
Due to the mechanics of atomized liquid filtration, the efficiency of wet units is linked to the specific gravity of the extracted dust as well as particle size distribution. A SG of 2,500kg/m3 and typical particle sizes >10 micron are usually required to achieve acceptable efficiencies as stated above, and this can rule out wet collector application in some industries.
Filtration efficiency based solely on particle size is limited when compared to dry units. Typically, the mean particle sizes in a wet unit need to be >25 microns to achieve the same levels of efficiency as dry units handling dusts at 5 microns and less therefore careful consideration of required filtration efficiency and particle size distribution should be applied before selecting a wet unit. The main applications for wet filtration are based around mechanically generated dusts such as polishing, linishing, grinding, crushing and fettling – typically in the metals and stone masonry sectors as the particle sizes and specific gravity of dusts generated from these processes generally fall within the capabilities of the equipment
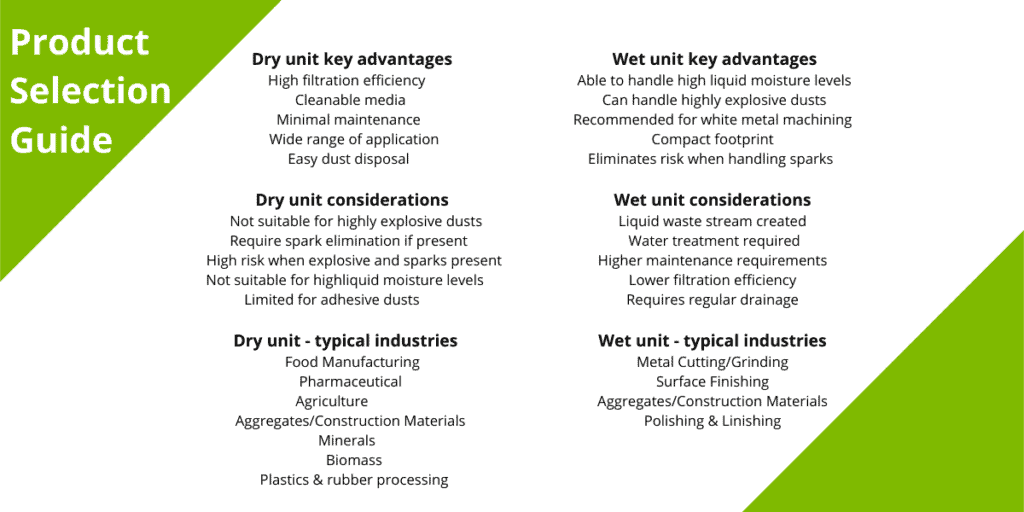
Industrial filtration is extremely varied with many factors influencing product selection; as such we recommend that advice is obtained from Dustcheck in terms of application before product selection is made. Our extensive knowledge and portfolio of both wet and dry products allows us to tailor the correct solution to each individual application.