The opportunities offered to operators here are both diverse and economically interesting. With non-invasive signalling that can be integrated into the rupture disc, even processes with critical pressures and demanding media can be reliably monitored.
Processes involving high temperatures and highly corrosive media are widespread throughout the chemical industry. In the past, conventional signalling was not always compatible with such extreme conditions, which is why it is now often overlooked as an additional process monitoring system.
The use of modern signalling equipment not only helps to improve productivity and safety but is also helpful in terms of addressing environmental concerns. The German manufacturer REMBE is a European leader in the production of pressure relief devices, explosion protection systems and the associated signalling devices. The company’s product range includes some of the most robust rupture discs and signalling systems available on the market. These solutions create significant operational added value in the chemical industry by reliably monitoring safety systems and critical pressure relief devices.
In processes involving potentially harmful media, the risk of leakage can be reduced via a quick and safe shutdown. REMBE’s well-designed signalling systems comply with both industry-relevant standards for explosive atmospheres and the intrinsic safety standards. By providing rapid notification of a burst rupture disc, they help to safely control the process while minimising downtime. High-quality signal transmitters can be easily integrated into the existing control systems in order to transmit a visual or acoustic signal when the rupture disc bursts and to shut down the system if necessary.
Avoiding unnecessary downtime through non-invasive signalling
The NIMU (non-invasive rupture disc monitoring) signal transmitter is suitable for systems exposed to harsh operating conditions. This reusable monitoring system is explicitly designed to provide rapid notification of a burst rupture disc. The REMBE NIMU sensor does not come into contact with the process itself, so it is not affected by harsh process conditions or corrosive media and ensures maximum tightness even for systems containing extremely corrosive chemicals.
The NIMU is mounted in a blind tap in the outlet on the rupture disc holder. Thus, the signal transmitter is completely isolated from the process. Potential leakage after the rupture disc has burst is also prevented – this is essential for customers in the chemical industry where leaks cannot be tolerated.
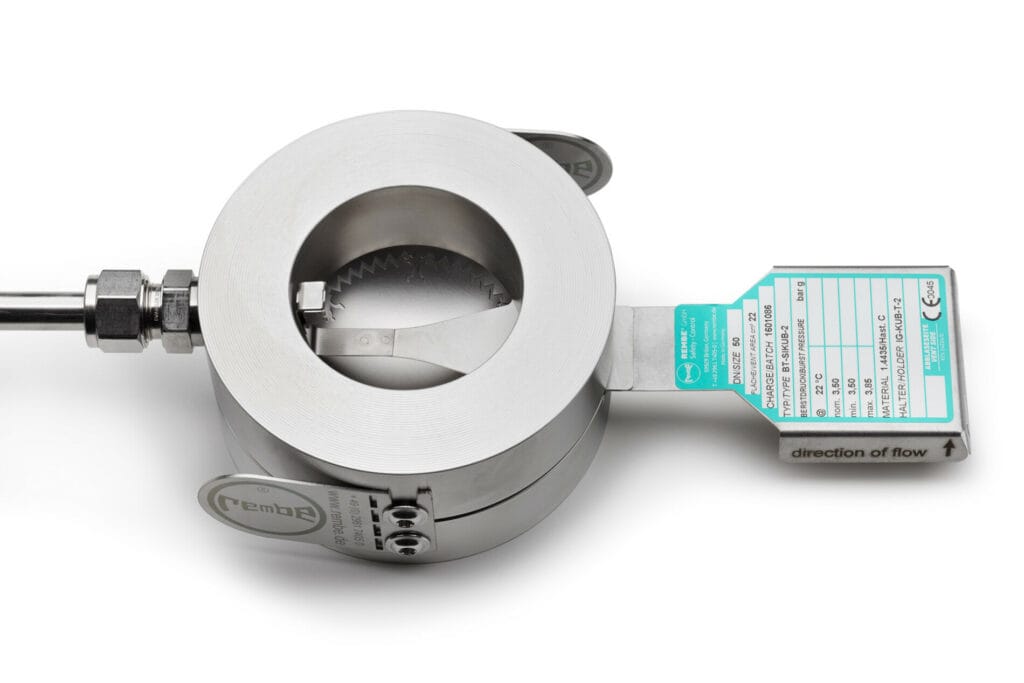
The signal transmitter is fully reusable not only after the rupture disc has burst, but also after scheduled maintenance work. During such maintenance work, the closed circuit of the rupture signalling system makes it easy to perform a function test – the rupture disc can then be reinserted into its holder. Furthermore, the operator can do this without external assistance, which simplifies and speeds up the maintenance process. This is simply a must in the chemical industry due to the demanding productivity requirements.
Reduce environmental risks
Environmental concerns such as emissions control have become increasingly important for chemical manufacturers. The ability to quickly detect a leak within the process without external support brings significant benefits.
On the one hand, the SBK signal transmitter ensures fast and reliable fault signalling via the bursting of rupture discs and, on the other hand, has the unique ability to monitor leaks from upstream rupture discs. REMBE has specially developed this signal transmitter for processes with high temperatures where alternative signalling systems may no longer be suitable. The combination of leak detection and signalling in one product is a cost-effective solution. The materials used remain stable even at extreme temperatures and ensure high reliability in the long term without the risk of premature failure.
Integrated signalling – reduce installation points, ensure reliable monitoring
Whereas with other signalling systems the rupture disc and signalling devices must be installed and maintained separately, the SGK versions allow the signalling to be integrated directly into the rupture disc. Thanks to their unique design, it is not necessary to run a cable out of the rupture disc holder, thereby eliminating the need to drill a hole for the signal cable. Especially for processes with a low set pressure, where (for example) the non-invasive NIMU signalling may not be suitable, the SGK signalling systems allow continuous monitoring. The SGK versions are available with the KUB and IKB reverse acting rupture discs and the ODV triple-section rupture disc.
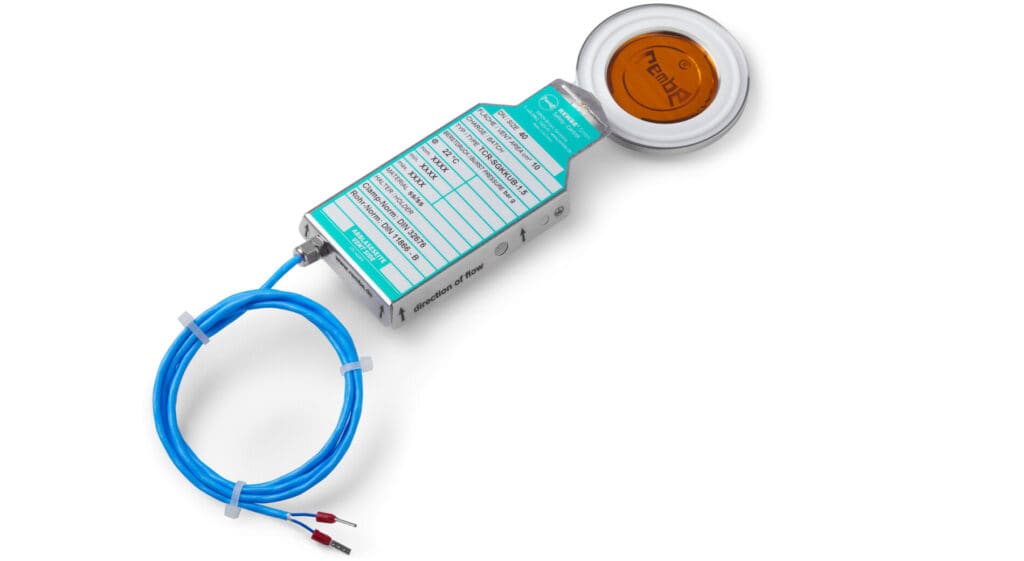
About REMBE – the REMBE Alliance introduces itself
Most people associate REMBE with REMBE GmbH Safety + Control, the specialist for explosion safety and pressure relief worldwide. The company offers customers cross-industry safety concepts for plants and equipment. All products are manufactured in Germany and meet the requirements of national and international regulations. REMBE customers include market leaders in various industries, including the food, timber, chemical and pharmaceutical industries.
The company’s engineering expertise is based on 50 years of application and project experience. As an independent, owner-managed family business, REMBE combines expertise with the highest quality standards and is involved in various specialist committees worldwide. Short coordination paths allow for quick reactions and customer-specific solutions for all applications, from standard products to high-tech special designs.
In addition to REMBE GmbH Safety+Control (www.rembe.de) with approx. 340 employees worldwide, headquartered in Brilon (Hochsauerland, Germany), and numerous subsidiaries worldwide (Italy, Finland, Brazil, USA, China, Dubai, Singapore, South Africa, Japan), four other companies operate under the REMBE umbrella brand:
- REMBE Research+Technology Center GmbH (www.rembe-rtc.de)
- REMBE Advanced Services+Solutions GmbH (www.rembe-services.de)
- REMBE Kersting GmbH (www.rembe-kersting.de)
- REMBE FibreForce GmbH (www.argusline.de)
Author: Nils Lange
(Process Engineer Dept. Team Leader Product Design Solutions).
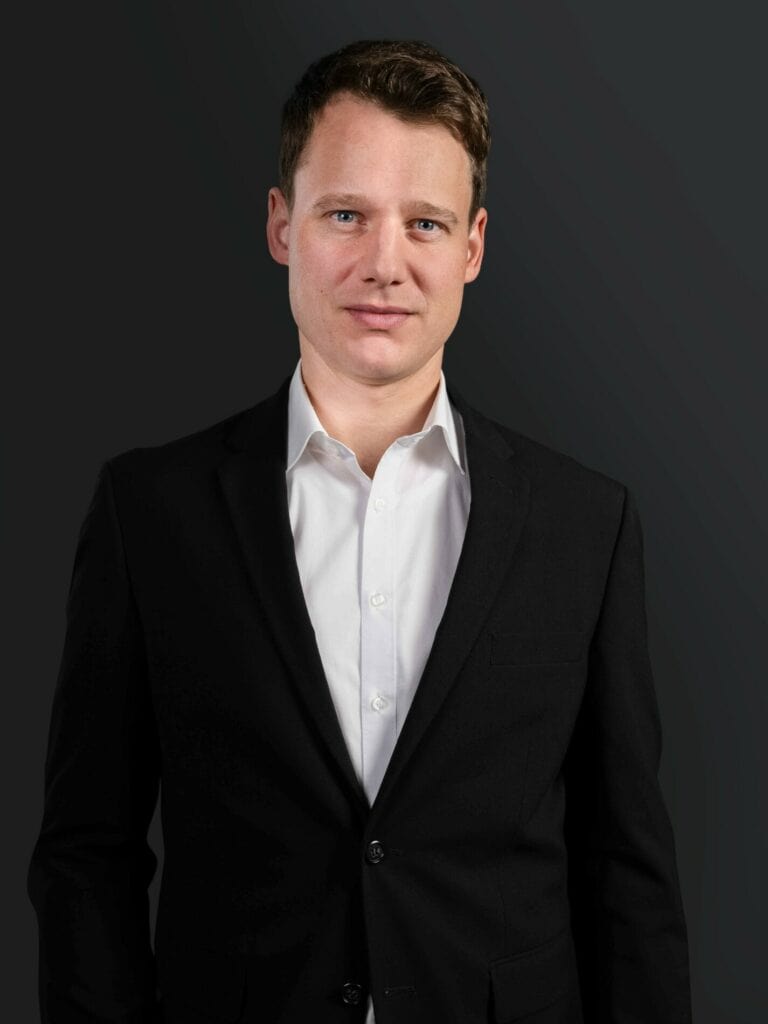