In order to minimise the risk of explosion when handing flammable solids and dusts, the requirements for an explosion and the respective dust characteristics are assessed in advance.
As a rule, the fire triangle or even the explosion pentagon is considered here:
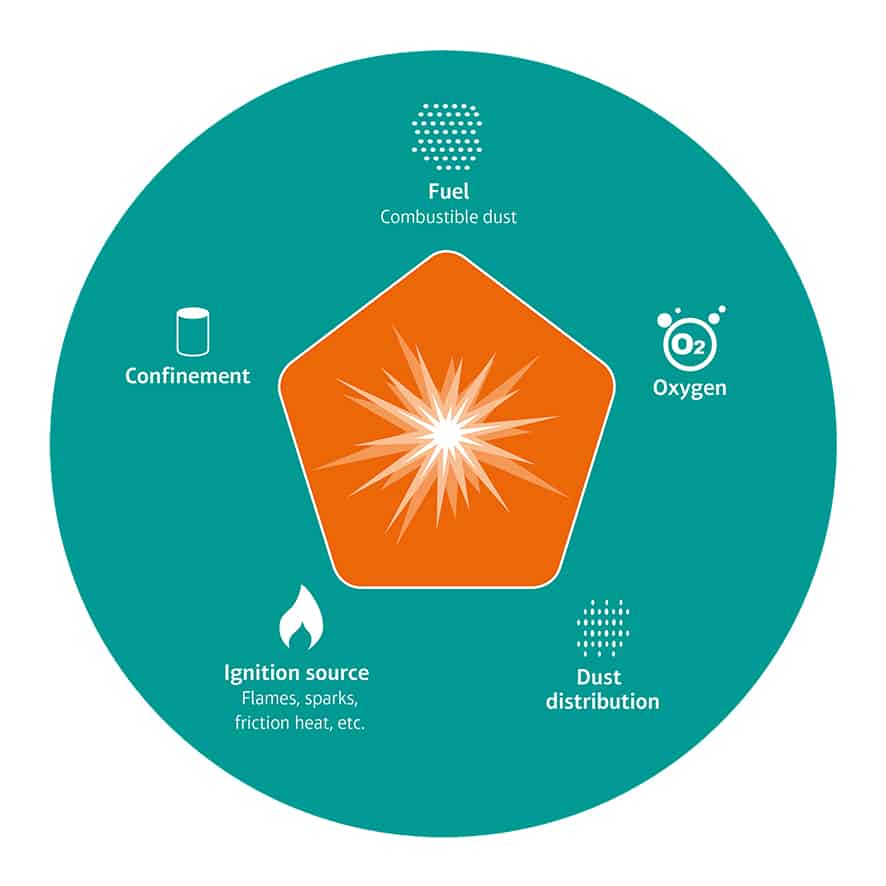
Thus, in order to create an explosion inside a production facility or machine, the following parameters must be fulfilled
- Fuel (dust)
- Sufficient oxygen
- Suitable mixing ratio (dust cloud)
- Source of ignition which has the minimum ignition energy of the dust
- Confined Space
If one of the above conditions are eliminated, explosion safety has already been practiced. If, however, it was not possible during operation, the risk of explosion remains, which requires the endangered area to be declared (Zone 20, 21 or 22) and based on that other preventative or protective measures to be implemented.
Typically the first approach would be to just apply explosion protection such as venting and explosion isolation in order to protect the equipment from each other to save lives and limit the damage. In principle, this thought is not incorrect: Compared with the use of motor vehicles, where accident could not be 100% ruled out, it is mandatory to wear seatbelts and apply safety measures such as airbags to reduce the effects of the accident.
However, if we take a step back and stay in the example, we can see that accidents are much more likely to be avoided with the help of driver-assistance systems such as braking assistants and lane keeping assist. As a result, it is no longer the accident but instead a hazardous situation that is recognised and averted in advance.
It was the idea of REMBE´s engineers to allow such hazardous situations to also be identified in the bulk solids industry and to be prevented by smart assistance and preventative systems.
Ignition Hazard – Electrostatic Charge:
Spark discharges, propagating brush discharges, cone discharges, and lightning bolt-like discharges are capable of igniting dust/air mixtures. To prevent these, sufficient grounding of the various vessels, plants and machines must always be ensured.
When pneumatically unloading tankers, high electrostatic potential that is able to ignite explosive dust atmospheres can also occur due to the high speeds. This risk can be eliminated by grounding the silo, intake station and vehicle. As a constant grounding connection is not possible on the vehicle, smart-ground monitoring systems are used as assistance and preventative systems.
Those systems make it possible to ensure that the connection to ground is sufficiently conductive during the unloading or filling of a vehicle. The grounding clamp on the monitoring unit is connected to the vehicle and then the line resistance is measured. If this is below 10 ohms, the grounding system issues a release and the grounding process begins. Release signals can be transmitted using integrated relays.
FARADO II takes things a step further here. The intelligent manipulation monitoring system ensures that a pre-set object size must be connected to the grounding clamp. Object sizes are determined based on electrical capacity (measured in PF) in this case. This prevents grounding clamps from being connected to steel girders that are already earthed or small objects such as screwdrivers.
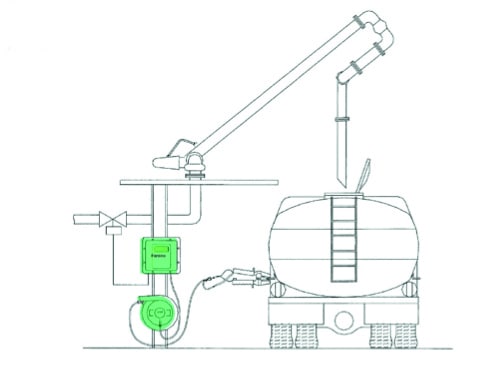
Ignition hazard – High temperatures, self-ignition and smouldering embers:
A further ignition hazard that should be identified at an early stage is a temperature increase in the conveyed or processed material/product.
Friction, for example, often causes a slow temperature increase, which may eventually ignite dust clouds or at least produce glowing embers of sedimented dust layers. Depending on how the material behaves, Maillard reactions can also occur, which continue through to self-ignition.
Such temperature increases in product layers cannot be reliably detected either by spark detectors or by PT100 temperature sensors. For smart preventative assistance the use of infrared cameras with a longer wavelength is commonly applied. REMBE´s HOTSPOT X20 measures surface temperatures using an intelligent evaluation system, which divides the field of view into detection zones. A separate temperature threshold value can be set for each individual zone in order to tailor the detection to the process as far as possible. The HOTSPOT X20 can even identify small temperature increases (1°C) and enables to warn the operator of a fire or glowing embers at extremely early stages. The HOTSPOT X20 can also be used in explosion atmosphere up to zone 20 and under high dust loads and monitors a temperature range in the standard version of 0-200°C (higher temperatures possible, but typically not required).
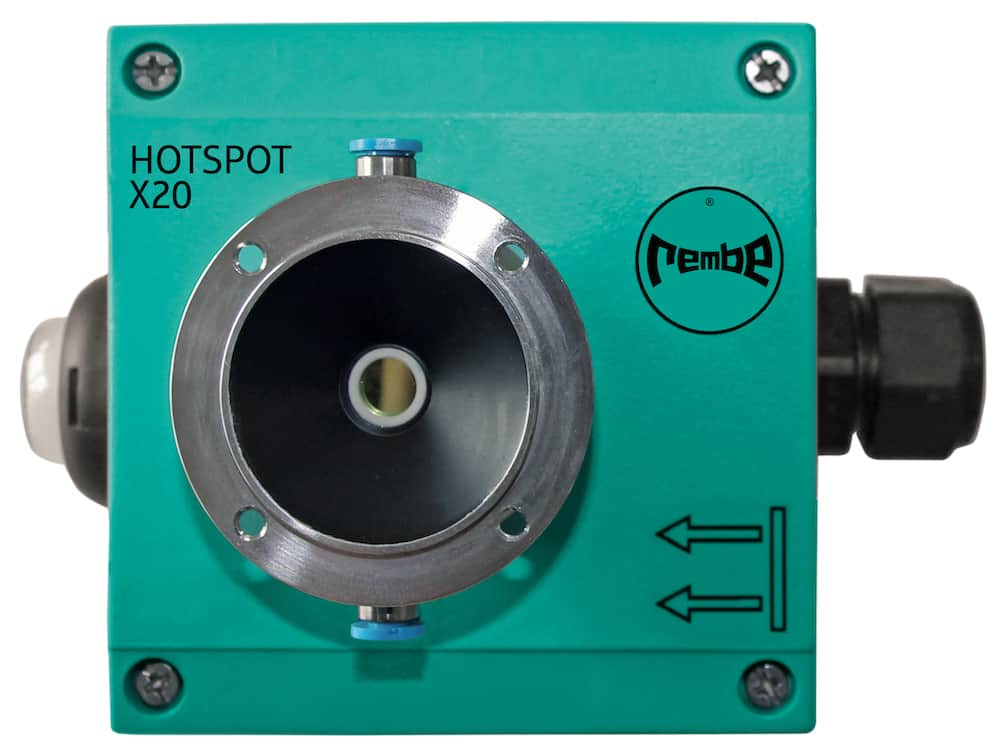
Before smoke develops or a fire occurs, the material usually experiences a “roasting process”, which releases various fire gases. The phase from warming through to roasting can be very lengthy and thus allows the REMBE Engineers to detect pyrolysis gases during this roasting process.
Mainly hydrocarbon compounds are released when many substances thermally decompose. If there is incomplete burning without a flame and a low oxygen supply, carbon monoxide is created as well. The GSME X20 pyrolysis gas detector, for instance, has been designed for detecting these gases, even as they develop. Alongside carbon monoxide and hydrocarbon compounds, nitrogen oxide and hydrogen compounds (CO, HC, H2 and NOx) are also monitored. With the aid of an intelligent evaluation algorithm, a process behaviour can be ideally mapped and normal off-gasing be adopted. If a concentration increases above the usual level, the GSME X20 immediately triggers an alarm. The detector, is also suitable for explosion atmospheres up to zone 20, monitors concentration ranges from 0-100ppm.
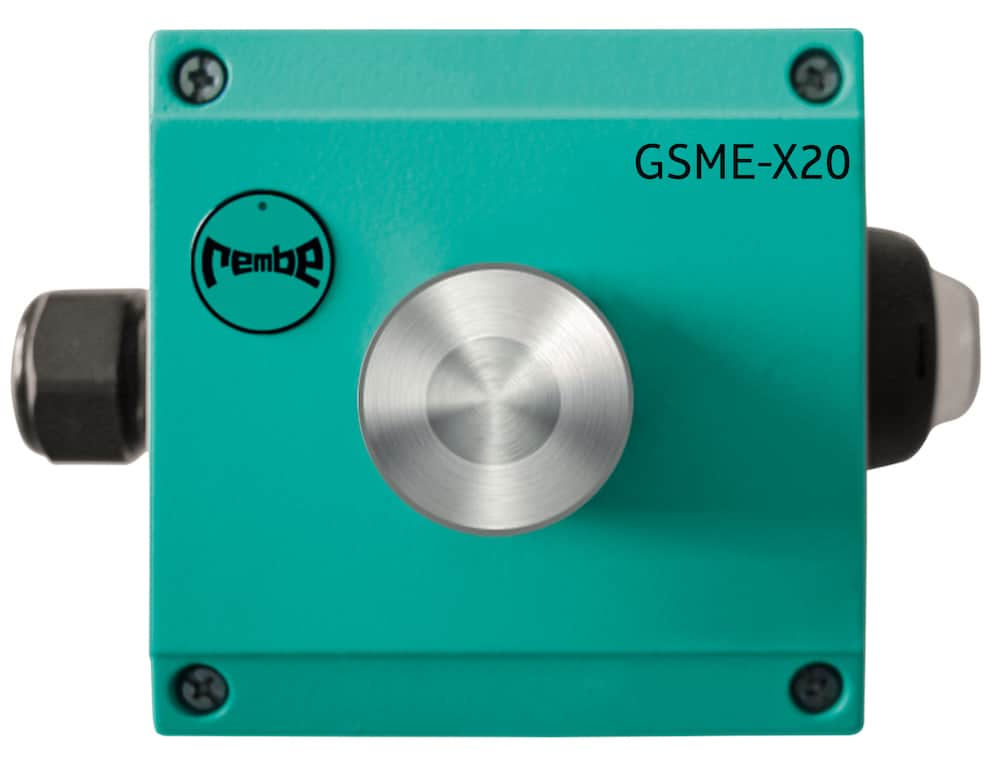
What happens next after detection?
Each of the above mentioned situation requires a tailored solution of the assistance system. When the location and mounting position are ideally designed in an explosion protection concept, HOTSPOT X20 and GSME X20 allow explosions and fires to be prevented through early detection.
However, if a hazardous situation has been identified and operations stopped, this presents a further challenge. How can a safe environment now be restored for safe operation?
Process guidelines are a way to provide employees with fast possible actions in emergency situations. However, these must be transparent and easy to access. The REMBE iQ Safety Cockpit can help to visualise the fire and explosion protection components in an easy-to-understand way and connect various types of detectable risks with process flows and guidelines. Similar to the brain of smart cars as per the above-mentioned example, the REMBE iQ Safety cockpit acts a assistance system and navigates the operator to a safe situation.
If all of the components are connected to the network, signals can be received and resulting messages distributed automatically to various recipients (SMS, e-mail, pagers, etc.). In order to not only identify the devices but also the dangerous areas, the REMBE iQ Safety Cockpit can also display plant and building plans.
About REMBE – the REMBE Alliance introduces itself
Most people associate REMBE with REMBE GmbH Safety + Control, the specialist for explosion safety and explosion venting worldwide. The company offers customers cross-industry safety concepts for plants and equipment. All products are manufactured in Germany and meet the requirements of national and international regulations. REMBE customers include market leaders in various industries, including the food, timber, chemical and pharmaceutical industries.
The company’s engineering expertise is based on more than 45 years of application and project experience. As an independent, owner-managed family business, REMBE combines expertise with the highest quality standards and is involved in various specialist committees worldwide. Short coordination paths allow for quick reactions and customer-specific solutions for all applications, from standard products to high-tech special designs.
In addition to REMBE GmbH Safety + Control (www.rembe.de) with approx. 280 employees worldwide, headquartered in Brilon (Hochsauerland, Germany), and numerous subsidiaries worldwide (Italy, Finland, Brazil, USA, China, Dubai, Singapore, South Africa, Japan), four other companies operate under the REMBE umbrella brand:
- REMBE Research & Technology Center GmbH (www.rembe-rtc.de)
- REMBE Advanced Services + Solutions GmbH (www.rembe-services.de)
- REMBE Kersting GmbH (www.rembe-kersting.de)
- REMBE FibreForce GmbH (www.argusline.de)