An often-cited example is a painted metal drum which stands on an insulating wooden pallet and is filled with either flammable bulk or liquids. In the moment the filled material hits the inside of the metal drum, a charge exchange takes place between the two materials which cannot be reversed if the filling speed is too high. During the filling process, the charges accumulate and discharge in a spark when a grounded object (e.g., a wrench or a person) approaches or if the breakdown voltage of the surrounding air is exceeded. The same effect applies to filling processes of various other containers such as IBC, buckets, canisters and also ungrounded parts of the plant.
Favoured by high filling speeds (> 1 m/s) and very low conductive materials, potential differences of up to several thousand volts can occur, which can in turn lead to spark discharges with ignition energies in clearly double digit mJ range within the explosion hazardous area. To prevent this danger and according to international IEC-standards, all conductive materials, process equipment and objects need to be grounded or connected with ground potential.
In practice, this often means simple grounding cables and clamps which are directly connected to the potential equalisation rail. The grounding clamp is than connected to the object to be grounded, e.g., the metal drum, and the electrostatic charges are discharged via the grounding cable to the rail.
A much safer, but often more expensive option are monitored grounding control devices, which actively monitor the grounding connection and can interrupt filling processes in case of an unsafe situation. These explosion-proof devices like the TIMM EKX-products are often used during the filling of large objects, such as trucks, railcars or FIBC and have several advantages:
- No uncertainty by continuous monitoring and displaying the grounding quality
- Tamper-proof and failsafe due to integrated object detection and diagnosis
- Automatic interruption of filling processes via integrated control outputs
But despite all these safety critical advantages, monitored grounding control devices are only rarely used in filling processes with smaller containers. There are several reasons for this, but mostly it’s a matter of costs or a subjective (under)estimation of the explosion risks of the filling operation.
However, one should be aware, that a grounding connection is only as good as the quality of its weakest link. For unmonitored cables and clamps, this means on the one hand that the grounding cables are subject to wear, which can significantly limit or even completely eliminate the conductivity. Common examples are torn off cable cores at the clamps, crushed cables, (partially) broken ring terminals at the rails or broken copper cable cores. On the other hand, incorrect use of the grounding cables, such as clamping it to a painted or dirty surface, can significantly reduce the conductivity, even without the operator noticing it.
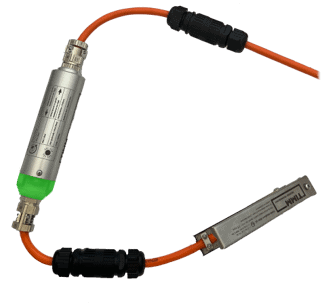
To close the gap between the unmonitored grounding clamps and cables and the safer, but only rarely used monitored grounding devices, we developed the TIMM SMART BITE LED ground indicator. This battery-powered device plugs into any two-pole cable and signals the quality of the grounding connection via three leds. This allows the operator to instantly see whether the grounding connection meets the standards and the electrostatic charges are safely dissipated. The SMART LED is built completely intrinsically safe and the integrated battery can be exchanged by the operator on site
The device can be used for all metal connection points and objects as well as mobile or stationary in a variety of combinations (clamp – clamp, clamp – ring terminal, ring terminal – ring terminal). Typical areas of use are the monitoring of connections between objects, such as IBC, drums, or canisters and earth rails, the connection between two objects and the connection of individual plant parts with the earth rail.
Besides the advantage of improving existing, unmonitored grounding cables it can also reduce the effort for the regular checking of the grounding cables as the SMART LED always signals whether the cable meets the quality requirements – without someone actively measuring by hand.
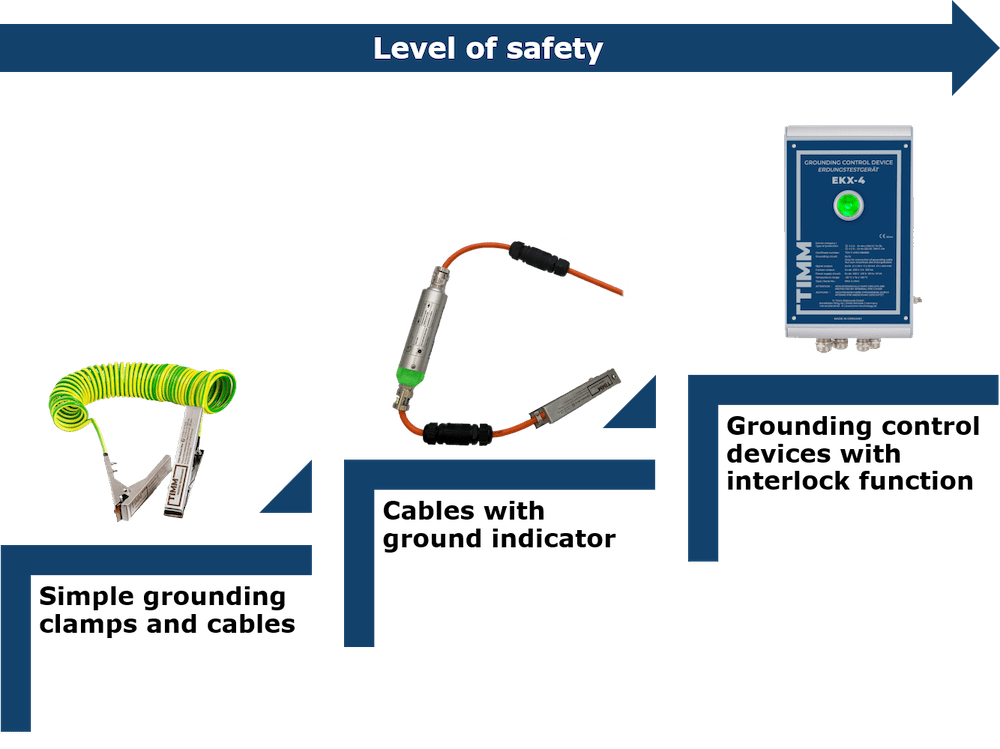
It can therefore be stated that there are three different levels of grounding in hazardous areas, which differ significantly in terms of the level of safety achieved. And especially with unmonitored grounding cables, the step to the next higher safety level should be considered, since grounding indicators, such as the TIMM SMART LED, can be used to safely and cost-effectively avoid typical grounding problems.