In connection with air, fine sugar dust is considered an explosive mixture. Depending on the grain size of the material, explosions can occur even with a very low ignition energy of 5mJ. Sugar dust is one of the most explosive dusts in industrial processes and can therefore be ignited by a variety of ignition sources, such as mechanical or electrical sparks.
Around 27% of all explosions in the food and feed industry occur in and around conveyor systems and elevators. Due to the high explosiveness of sugar, many plants and operating areas in the processing industry are defined as explosion protection zones. Big bag filling/ emptying and the (un)loading of silo vehicles and tankers are therefore carried out almost exclusively in explosion protection zones 21 and 22. In these zones, the main focus lies on minimizing possible ignition sources. Especially electrostatic charges have to be considered as a possible ignition source during loading processes with sugar.
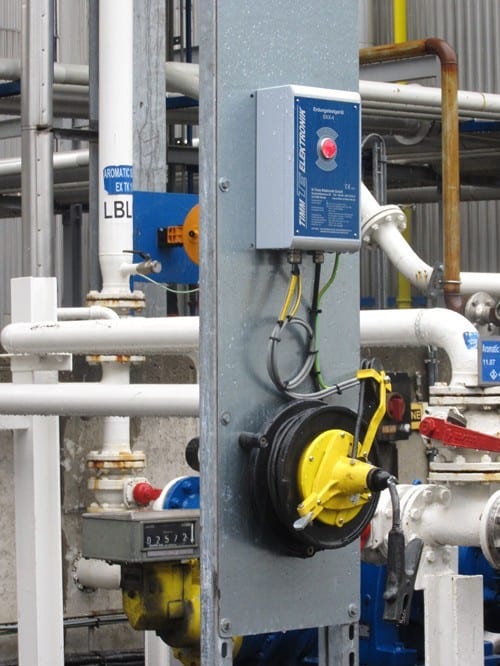
Electrostatic charge occurs when two substances rub against each other at high speed, such as when sugar is conveyed in pipes or when it is blown into tanks. If one of the two substances is isolated from earth potential or has very poor conductivity, the resulting electrostatic charge cannot be dissipated and will accumulate on the material. If this happens and a grounded object is approached or the field breakdown strength of the surrounding atmosphere is exceeded, a sudden and high-energy spark discharge can occur. The ignition energy released depends on the electrical capacity of the object on which the charges have accumulated. Typically, with small to medium-sized metal containers, ignition energies between 3 and 60 mJ can be assumed. Silo trucks, on the other hand, can even have ignition energies of well over 60mJ due to their container size. The potential ignition energies are therefore more than sufficient to ignite explosive sugar-air mixtures.
For this reason, the international standard IEC 60079-32-1 provides information about which measures must be taken to prevent the dangers of electrostatic charge as best as possible. A main statement of the standard is “Grounding helps!”. A conductive earth connection prevents electrostatic charging by dissipating the charges directly to earth potential. This means that no charges can accumulate on the material. For tankers, measures should be taken that the resistance in the grounding connection does not exceed a value of 1 MΩ. In order to ensure this limit value, a grounding system for monitored grounding should be used, which signals the danger in the event of insufficient conductivity and, if necessary, is able to automatically stop the loading processes. The standard also points out that the grounding system should be able to distinguish between a truck and other conductive objects and structures in order to avoid incorrect use of the device.
Modern grounding control devices such as the TIMM EKX-4 are therefore equipped with various electrical and mechanical interfaces in order to transmit start and stop signals to the process control system. In combination with the integrated object detection, the device also ensures that the grounding system is used correctly by checking whether a truck is connected before signaling safe state.
The requirements are very similar when processing sugar in big bags. Typically, big bag loading systems for sugar are classified in Ex zone 21 In these zones, conductive big bags, the so-called FIBC type C, are prescribed depending on the minimum ignition energy of the processed material. According to IEC 60079-32-1, this type of big bag must be conductively connected to the earth potential in the presence of combustible dusts, gases and vapors during filling and emptying. The use of such big bags without a dedicated grounding connection does not sufficiently proper grounded.
This means in practice, that these big bags must be connected to earth with a grounding connection with a maximum resistance value of 10 MΩ before each filling and emptying process, for example by means of grounding clamps with cables. However, with this very simple solution there is still the risk that the cable connection is not conductive enough, for example because of a broken cable or insufficient conductive grounding tabs at the big bag. In this case, despite the grounding cable, electrostatic charges can accumulate on the big bag and cause the explosive atmosphere to ignite.
In order to counteract this problem, a monitored grounding with a grounding control device including object detection, such as the TIMM EKX-FIBC, should also be implemented for big bags. This is an easy way for the user to be sure that the big bag is grounded in accordance with the relevant standards at all times, as the discharge connection is automatically and permanently checked. For the supervisor, on the other hand, the object detection provides the additional certainty that the grounding is not forgotten and the grounding cable is actually connected to the big bag. Thereby operating errors are effectively avoided. In addition, the process control as well as lamps or horns can be activated via the control outputs in order to signal safe or unsafe state.
All in all it can be said that sugar, due to its low minimum ignition energy, is one of the dusts with the highest risk of explosion and therefore requires special attention. Since electrostatic charges can be sufficient to ignite such a sugar-air mixture, the requirements stated in IEC 60079-32-1 should be observed. This international standard prescribes a grounding connection for tankers with a maximum resistance value of 1 MΩ, which must be attached before filling or emptying. Monitoring the connection is seen as best-practice. FIBC type C must be equipped with a conductive grounding connection before each filling and emptying, which must not exceed a resistance value of 10 MΩ.
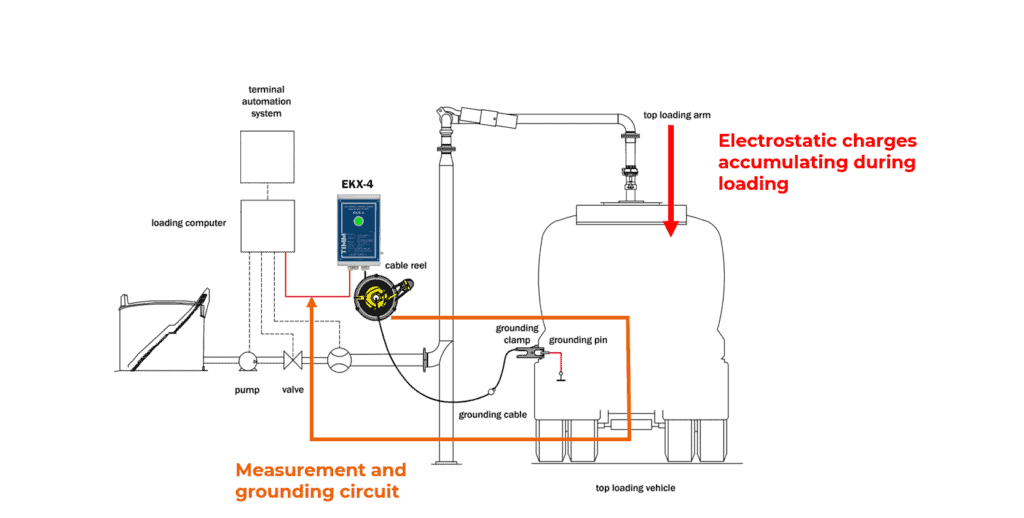
For both types of grounding, it is very senseful to use a grounding control device for monitored grounding. On the one hand, object detection can ensure that the grounding control device is used correctly and, on the other hand, the quality of the grounding connection can be monitored at all times. With the help of the signals from the control outputs, it is possible to react as quickly as possible in the event of danger, thus effectively preventing the risk of ignition of electrostatic charges.